Types of Solder Based on Composition
Lead-based Solder
Lead-based solder is an alloy that contains lead as its primary component, along with tin. The most common lead-based solder is 63/37, which consists of 63% tin and 37% lead. Lead-based solders have been widely used in the electronics industry due to their low melting point, excellent wetting properties, and good electrical conductivity. However, the use of lead in solder has been restricted in many countries due to environmental and health concerns.
Lead-free Solder
As an alternative to lead-based solder, lead-free solder alloys have been developed. These solders are typically composed of tin, silver, and copper, with varying proportions depending on the specific alloy. Some common lead-free solder alloys include:
- SAC305 (96.5% tin, 3% silver, 0.5% copper)
- SN100C (99.3% tin, 0.7% copper, 0.05% nickel)
- SN96C (96.5% tin, 3% copper, 0.5% silver)
Lead-free solders have higher melting points compared to lead-based solders, requiring higher soldering temperatures. They also have different wetting properties and may require adjustments to the soldering process.
Types of Solder Based on Form Factor
Wire Solder
Wire solder is the most common form of solder used in electronics assembly and repair. It consists of a thin wire of solder alloy, often with a flux core. The flux helps to remove oxides from the metal surfaces, promoting better solder wetting and adhesion. Wire solder is available in various diameters, allowing for precise control over the amount of solder applied to the joint.
Solder Paste
Solder paste is a mixture of powdered solder particles suspended in a flux medium. It is commonly used in surface mount technology (SMT) for assembling printed circuit boards (PCBs). Solder paste is applied to the PCB pads using a stencil or syringe, and the components are then placed on top. During the reflow soldering process, the solder paste melts, forming a permanent connection between the components and the PCB.
Solder Bar
Solder bars are solid blocks of solder alloy used in wave soldering machines. Wave soldering is a process used for soldering through-hole components on PCBs. The PCB is passed over a molten wave of solder, which wets the component leads and creates a solder joint. Solder bars are melted in the wave soldering machine to maintain the solder bath.
Solder Preforms
Solder preforms are precisely shaped pieces of solder designed for specific applications. They come in various shapes, such as rings, discs, washers, and custom designs. Solder preforms are often used in automated soldering processes, where consistent and repeatable solder volumes are required. They eliminate the need for measuring or dispensing solder, ensuring uniform solder joints.
Types of Solder Based on Flux Type
Rosin Core Solder
Rosin core solder contains a flux core made of rosin, a natural resin extracted from pine trees. Rosin flux is available in different activity levels, such as mildly activated (RMA), fully activated (RA), and no-clean (NC). Rosin flux is commonly used in electronics soldering due to its excellent wetting properties and compatibility with most electronic components.
Acid Core Solder
Acid core solder contains an acid-based flux, typically used for soldering non-electronic metals like copper, brass, and steel. The acid flux is more aggressive than rosin flux and can remove heavy oxidation from metal surfaces. However, acid flux is corrosive and must be thoroughly cleaned after soldering to prevent damage to the components and the PCB.
Water-soluble Flux Solder
Water-soluble flux solder contains a flux that is soluble in water, making it easy to clean after soldering. This type of flux is often used in applications where residue-free solder joints are required, such as in the food and medical industries. Water-soluble flux is more active than rosin flux and can provide better wetting on heavily oxidized surfaces.
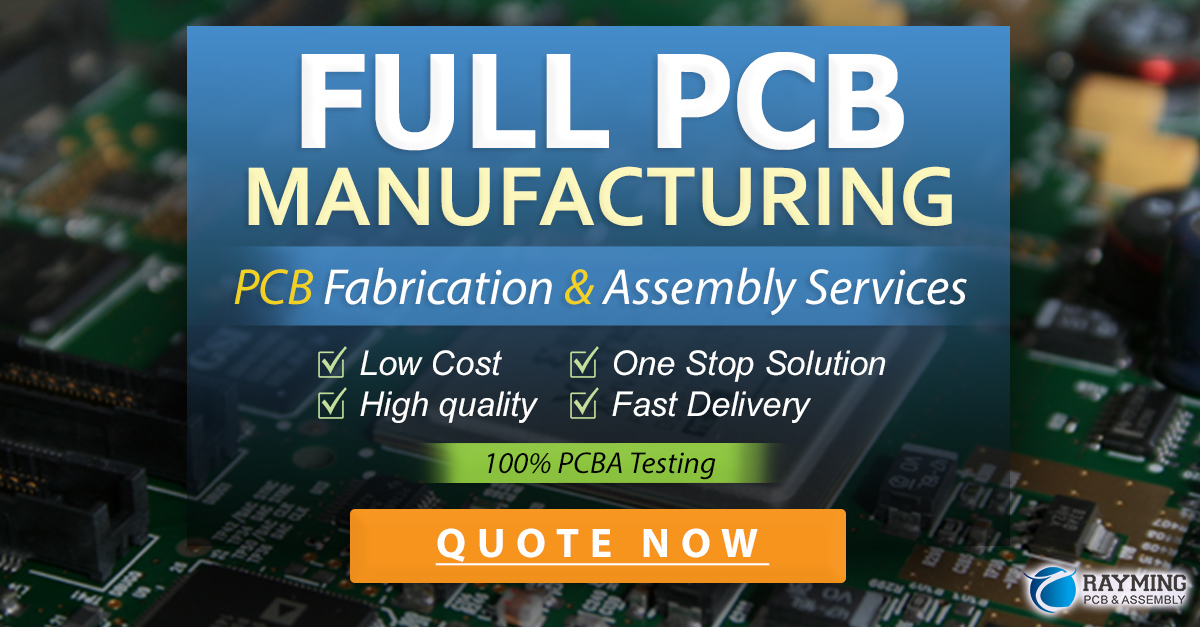
Choosing the Right Solder
When selecting the appropriate solder for a project, consider the following factors:
-
Composition: Choose between lead-based or lead-free solder based on environmental regulations, health concerns, and the specific requirements of your application.
-
Melting Point: Consider the melting point of the solder alloy and ensure that it is compatible with the components and the soldering process. Lead-free solders generally have higher melting points than lead-based solders.
-
Form Factor: Select the appropriate solder form factor based on the soldering process and application. Wire solder is versatile and widely used, while solder paste is essential for SMT assembly. Solder bars and preforms are used in specialized applications.
-
Flux Type: Choose the flux type based on the soldering requirements and the materials being soldered. Rosin flux is suitable for most electronics soldering, while acid flux is used for non-electronic metals. Water-soluble flux is ideal for applications requiring clean, residue-free solder joints.
-
Diameter (for wire solder): Select the appropriate wire solder diameter based on the size of the components and the soldering iron tip. Thinner diameters are suitable for precise work, while thicker diameters are used for larger components and connections.
Solder Types Comparison Table
Solder Type | Composition | Melting Point | Flux Type | Typical Applications |
---|---|---|---|---|
63/37 | 63% Sn, 37% Pb | 183°C (361°F) | Rosin | General electronics |
SAC305 | 96.5% Sn, 3% Ag, 0.5% Cu | 217-220°C (423-428°F) | Rosin | Lead-free electronics |
SN100C | 99.3% Sn, 0.7% Cu, 0.05% Ni | 227°C (441°F) | Rosin | Lead-free electronics |
Acid Core | Varies | Varies | Acid | Non-electronic metals |
Water-soluble | Varies | Varies | Water-soluble | Residue-free applications |
Frequently Asked Questions (FAQ)
1. What is the difference between lead-based and lead-free solder?
Lead-based solder contains lead as a primary component, typically in a 63/37 tin-lead ratio. Lead-free solder, on the other hand, is made from alloys that do not contain lead, such as tin-silver-copper (SAC) alloys. Lead-free solders have become more common due to environmental and health concerns associated with lead.
2. Can I use lead-free solder for all soldering applications?
Lead-free solder can be used for most soldering applications, especially in the electronics industry. However, some specialized applications may still require lead-based solder due to specific performance requirements or compatibility issues. It is essential to check the regulations and specifications for your particular application.
3. What is the purpose of flux in solder?
Flux is a chemical compound that helps to remove oxides and impurities from the metal surfaces during soldering. It promotes better wetting and adhesion of the solder to the metals being joined. Flux also protects the cleaned metal surfaces from re-oxidation during the soldering process.
4. How do I choose the right solder for my project?
When selecting solder for your project, consider factors such as the composition (lead-based or lead-free), melting point, form factor (wire, paste, bar, or preform), flux type (rosin, acid, or water-soluble), and diameter (for wire solder). Base your decision on the specific requirements of your application, including environmental regulations, component compatibility, and soldering process.
5. Can I mix different types of solder?
Mixing different types of solder is generally not recommended, as it can lead to inconsistent melting points, poor wetting, and reduced joint strength. It is best to use the same type of solder throughout a project to ensure optimal performance and reliability. If you need to switch solder types, thoroughly clean the soldering iron tip and the work area to avoid contamination.
In conclusion, understanding the various types of solder and their properties is crucial for achieving reliable and high-quality solder joints in electronics and metal joining applications. By selecting the appropriate solder composition, form factor, and flux type for your project, you can ensure optimal performance, compatibility, and longevity of the soldered connections.
Leave a Reply