Introduction to PCB Safety Distance
When designing and manufacturing printed circuit boards (PCBs), it is crucial to consider the safety distances between various components, traces, and layers to ensure proper functionality, reliability, and compliance with industry standards. PCB safety distance, also known as clearance or creepage distance, refers to the minimum spacing required between conductive elements to prevent electrical breakdown, short circuits, and other potential issues. In this article, we will delve into the details of PCB safety distance, exploring its importance, factors affecting it, and guidelines for maintaining appropriate clearances in PCB design.
Why is PCB Safety Distance Important?
PCB safety distance plays a vital role in the overall performance and longevity of electronic devices. Here are some key reasons why maintaining proper safety distances is essential:
-
Electrical Insulation: Adequate spacing between conductive elements prevents electrical current from jumping across unintended paths, which could lead to short circuits, arcing, or other electrical failures.
-
Voltage Breakdown Prevention: As the voltage level increases, the risk of electrical breakdown also rises. Maintaining sufficient safety distance helps prevent voltage breakdown between adjacent traces or components, ensuring the integrity of the PCB.
-
Environmental Factors: PCBs may be exposed to various environmental conditions such as humidity, dust, or contamination. Proper safety distances help mitigate the impact of these factors by providing a buffer zone that prevents conductive particles or moisture from causing short circuits.
-
Manufacturing Tolerances: During the PCB manufacturing process, slight variations in etching, drilling, or component placement can occur. Incorporating appropriate safety distances allows for these tolerances and reduces the chances of unintended connections or interference.
-
Compliance with Standards: Industry standards and regulations, such as IPC (Association Connecting Electronics Industries) and UL (Underwriters Laboratories), specify minimum safety distance requirements for different voltage levels and applications. Adhering to these standards ensures that the PCB meets the necessary safety and reliability criteria.
Factors Affecting PCB Safety Distance
Several factors influence the determination of appropriate safety distances in PCB design. Understanding these factors is crucial for making informed decisions and ensuring the optimal performance of the PCB.
Voltage Level
The voltage level is one of the primary factors that determine the required safety distance. As the voltage increases, the potential for electrical breakdown and arcing also rises. Therefore, higher voltage applications typically demand greater safety distances compared to low-voltage circuits. The following table provides a general guideline for minimum safety distances based on different voltage levels:
Voltage Level | Minimum Safety Distance |
---|---|
< 50V | 0.1 mm |
50V – 100V | 0.6 mm |
100V – 150V | 0.8 mm |
150V – 300V | 1.5 mm |
> 300V | 3.0 mm |
Note: These values are for reference only and may vary based on specific standards and applications.
Insulation Material
The choice of insulation material between conductive elements also affects the required safety distance. Different insulation materials have varying dielectric strengths, which indicate their ability to withstand electric fields without breaking down. Some commonly used insulation materials in PCBs include:
- FR-4 (Flame Retardant 4): A popular PCB substrate material with good insulation properties.
- Solder Mask: A thin layer of polymer applied over the copper traces to provide insulation and protection.
- Conformal Coating: An additional layer of insulating material applied to the PCB surface for added protection against environmental factors.
The dielectric strength of the insulation material directly influences the minimum safety distance required. Higher dielectric strength allows for smaller safety distances, while lower dielectric strength necessitates larger spacing.
Environmental Conditions
The environment in which the PCB will operate also plays a role in determining the appropriate safety distances. Factors such as temperature, humidity, altitude, and the presence of contaminants can impact the insulation properties and the risk of electrical breakdown.
For example, in high-humidity environments, the moisture in the air can lead to a phenomenon called “creepage,” where an electrical current can flow along the surface of the insulation material. In such cases, larger safety distances may be necessary to prevent creepage and maintain proper insulation.
Similarly, in high-altitude applications, the reduced air pressure can affect the dielectric strength of the insulation materials. Higher altitudes may require increased safety distances to compensate for the reduced insulation effectiveness.
PCB Manufacturing Processes
The manufacturing processes used in PCB fabrication can also influence the safety distance requirements. Different manufacturing techniques have varying tolerances and limitations that need to be considered when determining the appropriate spacing.
For instance, the etching process used to create the copper traces on the PCB has a certain level of accuracy. The minimum trace width and spacing achievable through etching depend on the capabilities of the manufacturing facility. The safety distance should account for these manufacturing tolerances to ensure that the final PCB meets the desired specifications.
Similarly, the drilling process used to create holes for through-hole components or vias has its own set of tolerances. The hole size, position, and accuracy can affect the spacing between adjacent holes or traces. Adequate safety distances should be maintained to prevent any unintended connections or short circuits due to drilling inaccuracies.
Guidelines for Maintaining PCB Safety Distance
To ensure proper safety distances in PCB design, designers should follow established guidelines and best practices. Here are some key considerations:
Clearance Between Traces
The clearance between adjacent traces on the same layer is critical to prevent short circuits and signal interference. The minimum clearance depends on factors such as the voltage level, trace width, and manufacturing capabilities. As a general rule of thumb, the clearance should be at least equal to the trace width. For example, if the trace width is 0.2 mm, the minimum clearance between traces should also be 0.2 mm.
However, for high-voltage applications or in cases where greater insulation is required, larger clearances may be necessary. Designers should refer to the applicable standards and guidelines specific to their industry and application to determine the appropriate clearance values.
Clearance Between Components
When placing components on the PCB, sufficient clearance should be maintained between the component pads and adjacent traces or components. The clearance requirement depends on the component package type, voltage level, and the presence of any heat-generating elements.
For surface-mount components, the clearance between the component pads and adjacent traces should be at least 0.2 mm to allow for proper soldering and to prevent solder bridges. For through-hole components, the clearance between the component leads and adjacent traces should be at least 0.5 mm to ensure proper insertion and to avoid any short circuits.
In cases where components generate significant heat, such as power transistors or Voltage Regulators, additional clearance may be necessary to prevent thermal damage to nearby components or traces. Designers should refer to the component datasheets and application notes for specific clearance recommendations.
Clearance Between Layers
In multi-layer PCBs, maintaining appropriate clearance between layers is crucial to prevent interlayer short circuits and to ensure proper insulation. The clearance between layers depends on the voltage level, the thickness of the insulation material, and the manufacturing process.
For standard PCB Stackups, a minimum clearance of 0.1 mm to 0.15 mm is typically recommended between adjacent layers. However, for high-voltage applications or in cases where enhanced insulation is required, larger clearances may be necessary. Designers should consult the PCB manufacturer’s guidelines and the relevant standards to determine the appropriate interlayer clearance for their specific design.
Creepage Distance
Creepage distance refers to the shortest path between two conductive elements along the surface of the insulation material. It is important to consider creepage distance in PCB design, especially in high-voltage applications or environments with high humidity or contamination.
The creepage distance requirement depends on factors such as the voltage level, the insulation material’s comparative tracking index (CTI), and the environmental conditions. Designers should refer to the applicable standards, such as IPC-2221 or IEC 60950, to determine the minimum creepage distance based on these factors.
To achieve the required creepage distance, designers can employ various techniques such as using slot cuts or trenches in the PCB, increasing the spacing between components, or applying conformal coating to improve the insulation properties.
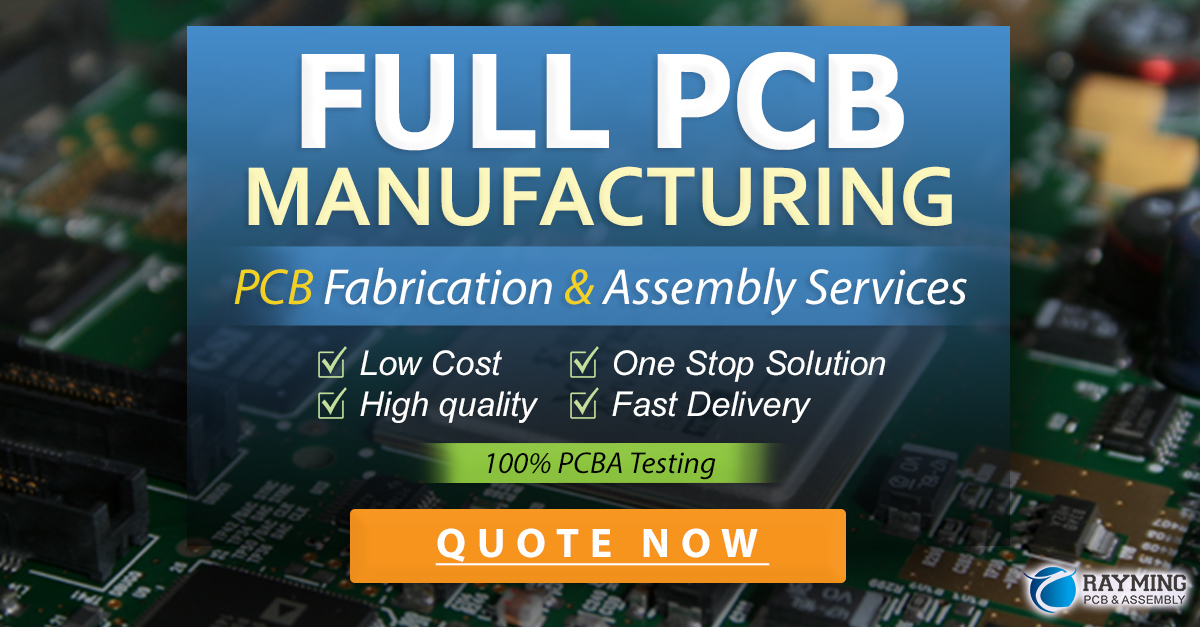
FAQ
-
What is the difference between clearance and creepage distance?
Clearance refers to the shortest distance between two conductive elements through air, while creepage distance is the shortest path between two conductive elements along the surface of the insulation material. -
How do I determine the appropriate safety distance for my PCB design?
To determine the appropriate safety distance, consider factors such as the voltage level, insulation material, environmental conditions, and applicable industry standards. Refer to guidelines provided by standards organizations like IPC or IEC, and consult with the PCB manufacturer for their recommendations. -
Can I use smaller safety distances to save space on my PCB?
While using smaller safety distances may help save space, it is important to prioritize safety and reliability. Always adhere to the minimum safety distance requirements based on the voltage level and other relevant factors. Compromising on safety distances can lead to potential electrical failures or non-compliance with industry standards. -
What happens if the safety distance is insufficient in a PCB?
Insufficient safety distance can result in various issues such as electrical breakdown, short circuits, arcing, or signal interference. These problems can lead to malfunctions, damage to components, or even safety hazards. Ensuring adequate safety distances is crucial for the proper functioning and reliability of the PCB. -
How can I increase the safety distance in a limited space?
If space is limited, designers can consider techniques such as using higher dielectric strength insulation materials, applying conformal coating, or employing slot cuts or trenches in the PCB to increase the creepage distance. Additionally, optimizing component placement and routing can help maximize the available space while maintaining the required safety distances.
Conclusion
Maintaining appropriate safety distances is a critical aspect of PCB design that ensures the proper functioning, reliability, and compliance of electronic devices. By understanding the factors that influence safety distances, such as voltage levels, insulation materials, environmental conditions, and manufacturing processes, designers can make informed decisions and adhere to industry standards.
Following guidelines for clearance between traces, components, and layers, as well as considering creepage distance requirements, helps prevent electrical failures, short circuits, and other potential issues. By prioritizing safety distances in PCB design, manufacturers can deliver high-quality, reliable products that meet the necessary safety and performance criteria.
As technology advances and PCB designs become more complex, it is essential to stay updated with the latest industry standards and best practices related to safety distances. Designers should collaborate closely with PCB manufacturers and refer to the relevant guidelines to ensure that their designs comply with the required safety distances.
By paying attention to PCB safety distances and following the appropriate guidelines, designers can create robust and reliable PCBs that perform optimally and meet the demands of various applications and environments.
Leave a Reply