Understanding DC Motor Speed Control
To effectively control the speed of a DC motor, it is important to understand the fundamental principles behind its operation. A DC motor consists of a stator (stationary part) and a rotor (rotating part). When a DC voltage is applied to the motor, current flows through the armature windings, creating a magnetic field. This magnetic field interacts with the permanent magnets on the stator, generating a torque that causes the rotor to spin.
The speed of a DC motor is directly proportional to the voltage applied to its armature. By varying the voltage, we can control the motor’s speed. However, simply changing the voltage may not provide precise speed control, especially under varying load conditions. Therefore, more advanced speed control techniques are employed to achieve accurate and stable speed regulation.
Pulse Width Modulation (PWM) for DC Motor Speed Control
One of the most popular methods for controlling the speed of a DC motor is Pulse Width Modulation (PWM). PWM involves rapidly switching the motor’s power supply on and off at a high frequency. By varying the duty cycle (the percentage of time the power is on), the average voltage supplied to the motor can be controlled, effectively regulating its speed.
PWM offers several advantages over other speed control methods:
– Efficient power utilization
– Precise speed control
– Low heat generation
– Wide speed range
To implement PWM-based speed control, a microcontroller or a dedicated PWM controller IC can be used. The microcontroller generates PWM signals with the desired duty cycle, which is then amplified by a motor driver circuit to provide sufficient current to drive the DC motor.
PWM Speed Control Circuit
Here’s a basic PWM speed control circuit using a microcontroller:
+5V
|
|
|
+-+
| |
| | Microcontroller
| | (e.g., Arduino)
| |
+-+
|
|
| PWM Signal
+-----+
|
|
+-+-+
| |
| | Motor Driver
| | (e.g., L293D)
| |
+-+-+
|
|
+--+--+
| |
| | DC Motor
| |
+-----+
In this circuit, the microcontroller generates the PWM signal, which is fed into the motor driver. The motor driver amplifies the PWM signal and supplies the necessary current to drive the DC motor. By adjusting the duty cycle of the PWM signal, the speed of the motor can be precisely controlled.
Feedback-based Speed Control Techniques
While open-loop speed control methods like PWM provide a simple and effective way to regulate motor speed, they may not be sufficient in applications that require high precision and robustness against load variations. In such cases, feedback-based speed control techniques are employed.
Tachometer-based Speed Control
A tachometer is a sensor that measures the rotational speed of a motor. By incorporating a tachometer in the speed control system, closed-loop feedback can be established. The actual speed of the motor is compared with the desired speed, and the control system adjusts the motor’s input accordingly to minimize the error.
Here’s a typical tachometer-based speed control system:
+--------+
| |
| Speed |
| Ref |
| |
+----+---+
|
|
+-+-+
| |
| | Controller
| |
+-+-+
|
|
+-+-+
| |
| | Motor Driver
| |
+-+-+
|
|
+--+--+
| |
| | DC Motor
| |
+--+--+
|
|
+-+-+
| |
| | Tachometer
| |
+-+-+
|
|
+--------+
|
|
|
+-+-+
| |
| | Feedback
| |
+---+
In this system, the tachometer measures the actual speed of the motor and provides feedback to the controller. The controller compares the measured speed with the desired speed reference and generates an error signal. Based on this error, the controller adjusts the motor driver’s input to minimize the speed error and maintain the desired speed.
Encoder-based Speed Control
An encoder is another type of sensor commonly used for precise speed control. Encoders provide position information by generating pulses as the motor shaft rotates. By counting the pulses over a fixed time interval, the speed of the motor can be determined.
Encoder-based speed control systems work similarly to tachometer-based systems. The encoder provides feedback on the motor’s actual speed, which is compared with the desired speed reference. The controller then adjusts the motor driver’s input to minimize the speed error.
Here’s a block diagram of an encoder-based speed control system:
+--------+
| |
| Speed |
| Ref |
| |
+----+---+
|
|
+-+-+
| |
| | Controller
| |
+-+-+
|
|
+-+-+
| |
| | Motor Driver
| |
+-+-+
|
|
+--+--+
| |
| | DC Motor
| |
+--+--+
|
|
+-+-+
| |
| | Encoder
| |
+-+-+
|
|
+--------+
|
|
|
+-+-+
| |
| | Feedback
| |
+---+
Encoders offer high-resolution position feedback, enabling precise speed control even at low speeds. They are widely used in applications that require accurate speed regulation, such as CNC machines, robotics, and servo systems.
Advanced Speed Control Techniques
In addition to the basic speed control methods discussed above, there are more advanced techniques that can be employed for specific applications or to achieve higher performance. Some of these techniques include:
Field-Oriented Control (FOC)
Field-Oriented Control (FOC) is a advanced speed control technique commonly used in high-performance motor control applications. FOC involves controlling the stator currents of the motor in a coordinated manner to achieve precise torque and speed control.
In FOC, the stator currents are transformed into a rotating reference frame aligned with the rotor’s magnetic field. By controlling the direct and quadrature components of the stator currents independently, the torque and flux of the motor can be precisely regulated. This allows for smooth and efficient motor operation, especially at low speeds and under varying load conditions.
FOC requires complex mathematical calculations and fast control loops, typically implemented using powerful microcontrollers or digital signal processors (DSPs).
Sensorless Speed Control
Sensorless speed control techniques aim to eliminate the need for physical speed sensors like tachometers or encoders. These techniques rely on estimating the motor’s speed based on electrical measurements, such as stator currents and voltages.
Sensorless speed control algorithms use advanced mathematical models and observer-based approaches to estimate the motor’s speed and position. By analyzing the motor’s electrical characteristics, these algorithms can provide accurate speed estimates without the need for additional sensors.
Sensorless speed control offers several advantages, including reduced system complexity, lower cost, and improved reliability. However, the accuracy and performance of sensorless techniques may be limited compared to sensor-based methods, especially at low speeds or during transient conditions.
Adaptive Speed Control
Adaptive speed control techniques involve dynamically adjusting the control parameters based on the motor’s operating conditions. These techniques aim to optimize the speed control performance by adapting to changes in load, temperature, or other environmental factors.
Adaptive speed control algorithms use online parameter estimation and self-tuning methods to update the controller gains in real-time. By continuously monitoring the motor’s performance and adapting the control parameters accordingly, adaptive speed control can provide robust and efficient operation under varying conditions.
Adaptive speed control is particularly useful in applications where the motor’s load or operating conditions are subject to frequent changes, such as in robotics, automotive systems, or industrial automation.
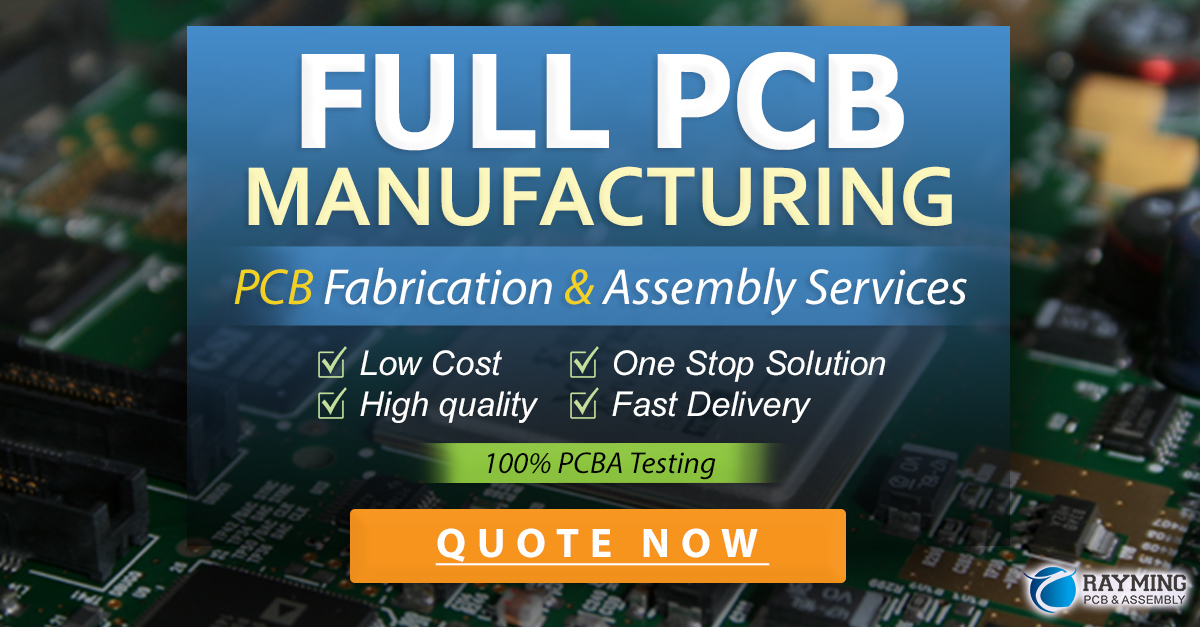
Choosing the Right Speed Control System
When selecting a suitable speed control system for your DC motor application, consider the following factors:
-
Speed Range: Determine the required speed range for your application. Some speed control methods may be more suitable for low-speed or high-speed operation.
-
Precision: Evaluate the level of speed precision required. Applications demanding high accuracy may benefit from feedback-based control techniques like tachometer or encoder-based systems.
-
Load Variations: Consider the expected load variations in your application. If the motor will be subjected to significant load changes, adaptive or robust control techniques may be necessary.
-
Cost: Assess the cost constraints of your project. Simple PWM-based speed control may be sufficient for low-cost applications, while advanced techniques like FOC or sensorless control may require higher investment.
-
Complexity: Evaluate the complexity of the speed control system in terms of implementation and maintenance. Advanced techniques may require specialized knowledge and expertise.
-
Reliability: Consider the reliability requirements of your application. Sensorless speed control techniques may offer improved reliability by eliminating the need for physical sensors.
By carefully considering these factors and understanding the advantages and limitations of different speed control methods, you can select the most suitable speed regulation system for your DC motor application.
Frequently Asked Questions
-
What is the difference between open-loop and closed-loop speed control?
Open-loop speed control methods, like PWM, control the motor’s speed without any feedback from the motor itself. Closed-loop speed control techniques, such as tachometer or encoder-based systems, use feedback from the motor to continuously adjust the control signals and maintain the desired speed. -
Can I use PWM speed control for high-precision applications?
PWM speed control can provide good speed regulation, but it may not be sufficient for applications requiring very high precision. For such cases, feedback-based control techniques like tachometer or encoder-based systems are recommended. -
What are the advantages of sensorless speed control?
Sensorless speed control techniques offer several advantages, including reduced system complexity, lower cost, and improved reliability. By eliminating the need for physical speed sensors, sensorless control simplifies the hardware design and reduces the potential points of failure. -
How do I select the appropriate motor driver for my speed control system?
When selecting a motor driver, consider factors such as the motor’s voltage and current requirements, the desired speed range, and the compatibility with your control method (e.g., PWM). Ensure that the motor driver can handle the peak currents and has sufficient heat dissipation capabilities. -
Can I implement speed control using a microcontroller?
Yes, microcontrollers are commonly used for implementing speed control systems. Most microcontrollers have built-in PWM modules and ADC (Analog-to-Digital Converter) inputs, which can be used for generating control signals and reading feedback from sensors. However, for advanced techniques like FOC or sensorless control, more powerful microcontrollers or DSPs may be required.
Conclusion
DC motor speed control is a crucial aspect of many applications, ranging from industrial automation to robotics and automotive systems. By understanding the principles behind DC motor operation and exploring different speed control techniques, you can select the most suitable speed regulation system for your specific requirements.
PWM-based speed control offers a simple and efficient method for regulating motor speed, while feedback-based techniques like tachometer or encoder-based systems provide higher precision and robustness against load variations. Advanced techniques such as Field-Oriented Control (FOC), sensorless speed control, and adaptive speed control offer additional benefits in terms of performance, reliability, and adaptability to varying operating conditions.
When choosing a speed control system, consider factors such as the required speed range, precision, load variations, cost, complexity, and reliability. By carefully evaluating these factors and selecting the appropriate control method, you can achieve optimal speed regulation and performance for your DC motor application.
Remember to properly size your motor driver, ensure compatible interfaces between the control system and the motor, and follow best practices for wiring and power supply design. With the right speed control system in place, you can unleash the full potential of your DC motor and achieve precise and efficient operation in your application.
Leave a Reply