What is a DC Chopper?
A DC chopper is a power electronic device that converts fixed DC input voltage to a variable DC output voltage. It is essentially a high-speed switch that rapidly connects and disconnects the load from the power source, effectively “chopping” the DC voltage into discrete pulses. By varying the duty cycle (the ratio of on-time to total switching period) of the switch, the average output voltage can be precisely controlled.
DC choppers are widely used in various applications, such as:
– DC Motor Speed Control
– Battery charging systems
– Switchmode power supplies
– Traction control in electric vehicles
Types of DC Choppers
There are four main types of DC choppers, classified based on their quadrant of operation in the voltage-current plane:
Chopper Type | Quadrant | Voltage Polarity | Current Polarity |
---|---|---|---|
Class A | First | Positive | Positive |
Class B | Second | Negative | Positive |
Class C | First and Second | Positive and Negative | Positive |
Class D | First and Fourth | Positive | Positive and Negative |
Class E | First, Second, and Fourth | Positive and Negative | Positive and Negative |
Class A Chopper (First Quadrant)
A Class A chopper operates in the first quadrant, where both the voltage and current are positive. It is used for applications that require unidirectional power flow, such as DC motor speed control in the forward direction.
The basic circuit diagram of a Class A chopper is shown below:
+--------------+
| |
| +--+--+
| | |
+---+ | +----+ | | +---+
| |---+--| |---+ +---| |
| V | | | | R |
| |---+--| |---+ +---| |
+---+ | +----+ | | +---+
| | |
| +--+--+
| |
+--------------+
The chopper consists of a power semiconductor switch (usually an IGBT or MOSFET) connected in series with the load. When the switch is turned on, the full input voltage is applied to the load. When the switch is turned off, the current through the load is interrupted, and the voltage across the load drops to zero.
By controlling the duty cycle (D) of the switch, the average output voltage (V_o) can be varied according to the following equation:
V_o = D × V_in
where V_in is the input voltage.
Class B Chopper (Second Quadrant)
A Class B chopper operates in the second quadrant, where the voltage is negative, and the current is positive. It is used for applications that require power flow from the load back to the source, such as regenerative braking in electric vehicles.
The basic circuit diagram of a Class B chopper is similar to that of a Class A chopper, with the addition of a freewheeling diode connected across the load:
+--------------+
| |
| +--+--+
| | |
+---+ | +----+ | | +---+
| |---+--| |---+ +---| |
| V | | | | R |
| |---+--| |---+ +---| |
+---+ | +----+ | | +---+
| | |
| +--+ +--+
| | |
+--------+------------+
| |
+------------+
When the switch is turned on, the input voltage is applied to the load, and the current flows through the switch. When the switch is turned off, the current through the load continues to flow due to the inductive nature of the load, but it now flows through the freewheeling diode. This allows the energy stored in the load to be returned to the source.
Class C Chopper (First and Second Quadrant)
A Class C chopper operates in both the first and second quadrants, allowing power flow in both directions between the source and the load. It is used for applications that require bidirectional power flow, such as speed control of DC motors in both forward and reverse directions.
The basic circuit diagram of a Class C chopper consists of two switches and two freewheeling diodes connected in an H-bridge configuration:
+--------------+
| |
| +----+ +--+--+
| | | | |
+---+ | | | | | +---+
| |---+--| |---+ +---| |
| V | | | | R |
| |---+--| |---+ +---| |
+---+ | | | | | +---+
| +----+ | |
| +--+--+
| +----+ +--+--+
| | | | |
| | | | |
| | |---+ +---+
| +----+ |
| |
+-----------------------+
By controlling the duty cycles of the two switches, the output voltage can be varied in both positive and negative directions, allowing the motor to be operated in both forward and reverse modes.
Class D Chopper (First and Fourth Quadrant)
A Class D chopper operates in the first and fourth quadrants, where the voltage is always positive, but the current can be either positive or negative. It is used for applications that require power flow from the source to the load and from the load to the source, such as battery charging and discharging systems.
The basic circuit diagram of a Class D chopper is similar to that of a Class C chopper, with the addition of a second freewheeling diode connected in parallel with the load:
+--------------+
| |
| +----+ +--+--+
| | | | |
+---+ | | | | | +---+
| |---+--| |---+ +---| |
| V | | | | R |
| |---+--| |---+ +---| |
+---+ | | | | | +---+
| +----+ | |
| +--+--+
| |
| +----+ +--+--+
| | | | |
| | | | |
| | |---+ +---+
| +----+ |
| |
+-----------------------+
By controlling the duty cycles of the two switches, the chopper can operate in both the first and fourth quadrants, allowing power to flow in both directions between the source and the load.
Class E Chopper (First, Second, and Fourth Quadrant)
A Class E chopper operates in the first, second, and fourth quadrants, allowing power flow in both directions between the source and the load, with the capability to handle both positive and negative voltages. It is used for applications that require full four-quadrant operation, such as servo motor drives and active power filters.
The basic circuit diagram of a Class E chopper consists of four switches and four freewheeling diodes connected in an H-bridge configuration:
+--------------+
| +----+ +--+--+
| | | | |
+---+ | | | | | +---+
| |---+--| |---+ +---| |
| V | | | | R |
| |---+--| |---+ +---| |
+---+ | | | | | +---+
| +----+ | |
| +--+--+
| +----+ +--+--+
| | | | |
| | | | |
| | |---+ +---+
| +----+ |
| +----+ +--+--+ |
| | | | | |
| | | | | |
| | |---+ +---+ |
| +----+ |
+-----------------------+
By controlling the duty cycles of the four switches, the chopper can operate in all four quadrants, allowing full control over the voltage and current in both directions.
Chopper Control Techniques
There are several control techniques used to regulate the output voltage of a DC chopper:
Pulse Width Modulation (PWM)
PWM is the most common control technique used in DC choppers. It involves varying the duty cycle of the switch to control the average output voltage. The switching frequency is kept constant, while the on-time and off-time of the switch are varied to achieve the desired output voltage.
The duty cycle (D) is defined as the ratio of the on-time (t_on) to the total switching period (T):
D = t_on / T
The average output voltage (V_o) is related to the input voltage (V_in) by the duty cycle:
V_o = D × V_in
By varying the duty cycle between 0 and 1, the output voltage can be smoothly controlled from 0 to the input voltage.
Pulse Frequency Modulation (PFM)
PFM is another control technique used in DC choppers, where the switching frequency is varied while keeping the on-time or off-time constant. This technique is less common than PWM but can be useful in certain applications.
In PFM, the average output voltage (V_o) is related to the input voltage (V_in) by the switching frequency (f) and the on-time (t_on) or off-time (t_off):
V_o = (t_on / (t_on + t_off)) × V_in = (f × t_on) × V_in
By varying the switching frequency, the output voltage can be controlled while maintaining a constant pulse width.
Current Limit Control
Current limit control is used to protect the chopper and the load from excessive current. It involves sensing the load current and comparing it with a preset current limit. If the load current exceeds the limit, the chopper is turned off to prevent damage.
Current limit control can be implemented in various ways, such as:
– Hysteretic current control: The switch is turned on when the current falls below a lower threshold and turned off when the current exceeds an upper threshold.
– Constant current control: The switch is turned on and off to maintain a constant average load current.
– Foldback current limiting: The current limit is reduced as the output voltage decreases, providing better protection against short-circuit conditions.
Soft-Switching Techniques
Soft-switching techniques are used to reduce the switching losses in DC choppers by ensuring that the voltage or current across the switch is zero during the switching transitions. This allows for higher switching frequencies and improved efficiency compared to hard-switching techniques.
Some common soft-switching techniques include:
– Zero-voltage switching (ZVS): The switch is turned on when the voltage across it is zero, eliminating the turn-on loss.
– Zero-current switching (ZCS): The switch is turned off when the current through it is zero, eliminating the turn-off loss.
– Resonant switching: An LC resonant circuit is used to shape the voltage and current waveforms, creating zero-voltage or zero-current conditions at the switching instants.
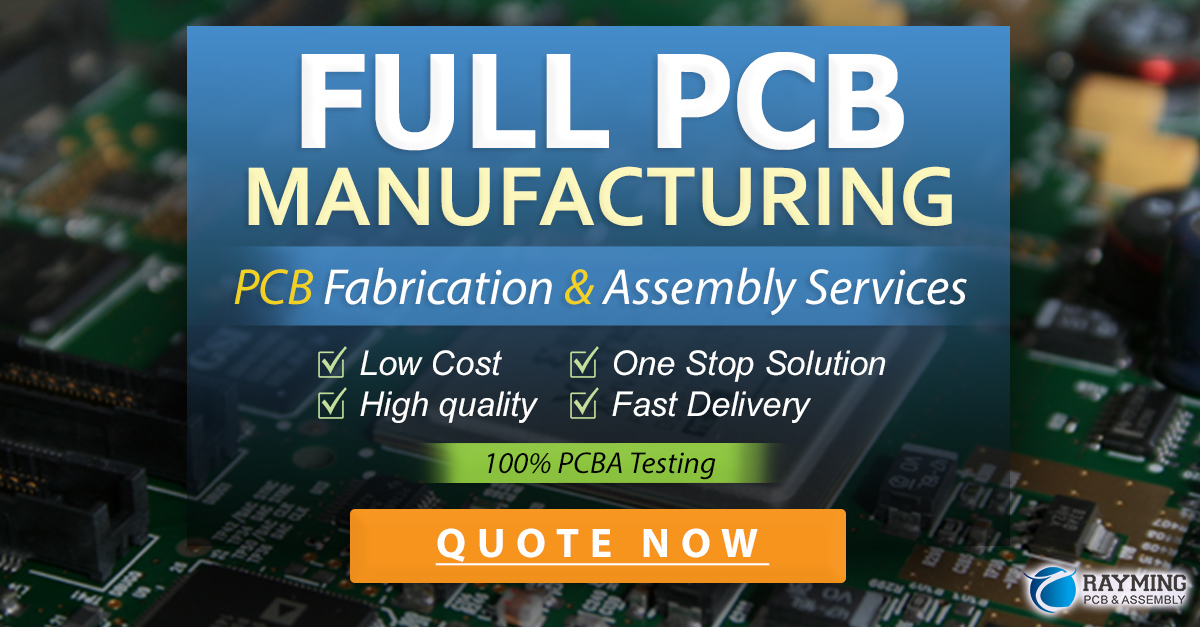
Applications of DC Choppers
DC choppers find extensive use in various industrial and consumer applications, some of which are discussed below:
DC Motor Speed Control
DC choppers are widely used for controlling the speed of DC motors. By varying the average voltage applied to the motor armature, the motor speed can be smoothly controlled over a wide range.
In a typical DC motor speed control system, the chopper is connected in series with the motor armature, and the duty cycle of the chopper is varied to control the motor speed. The chopper can be operated in either the first quadrant (Class A) for unidirectional speed control or in the first and second quadrants (Class C) for bidirectional speed control.
Battery Charging Systems
DC choppers are used in battery charging systems to control the charging current and voltage. By using a chopper to regulate the charging current, the battery can be charged efficiently and safely, prolonging its life.
In a typical battery charging system, the chopper is connected between the charging source (e.g., a solar panel or a rectified AC source) and the battery. The duty cycle of the chopper is varied to control the charging current, while the battery voltage is monitored to prevent overcharging.
Switchmode Power Supplies
DC choppers are used in switchmode power supplies (SMPS) to convert a DC input voltage to a regulated DC output voltage. SMPS are widely used in electronic devices, such as computers, smartphones, and televisions, to provide stable and efficient power supply.
In an SMPS, the DC chopper is used to generate a high-frequency pulse train, which is then transformed, rectified, and filtered to produce the desired DC output voltage. By using a high switching frequency, the size of the transformer and filter components can be reduced, resulting in a compact and efficient power supply.
Electric Vehicle Traction Control
DC choppers are used in electric vehicle traction control systems to regulate the power flow between the battery and the traction motor. By controlling the motor voltage and current, the vehicle speed and torque can be precisely controlled.
In a typical electric vehicle traction control system, the chopper is connected between the battery and the motor. The duty cycle of the chopper is varied to control the motor voltage and current, while the motor speed and torque are monitored using sensors. The chopper can be operated in the first and second quadrants (Class C) for forward and reverse motoring, and in the fourth quadrant (Class D) for regenerative braking.
Frequently Asked Questions (FAQ)
1. What is the difference between a DC chopper and a DC-DC converter?
A DC chopper is a type of DC-DC converter that uses a high-speed switch to convert a fixed DC input voltage to a variable DC output voltage. The term “DC chopper” is often used interchangeably with “DC-DC converter,” but not all DC-DC converters are choppers. For example, a linear voltage regulator is a type of DC-DC converter that does not use a switching element.
2. What are the advantages of using a DC chopper over a linear voltage regulator?
DC choppers offer several advantages over linear voltage regulators:
– Higher efficiency: Choppers can achieve efficiencies of over 90%, while linear regulators are limited to efficiencies of around 50% or less.
– Wider input voltage range: Choppers can operate with input voltages much higher than the desired output voltage, while linear regulators require the input voltage to be slightly higher than the output voltage.
– Smaller size and weight: Choppers use smaller transformers and filter components due to their high switching frequency, resulting in a more compact and lightweight design compared to linear regulators.
3. What is the purpose of the freewheeling diode in a DC chopper?
The freewheeling diode in a DC chopper provides a path for the load current to flow when the switch is turned off. This is necessary for inductive loads, such as DC motors, where the current cannot change instantaneously. Without the freewheeling diode, the sudden interruption of the load current would cause a high-voltage spike across the switch, potentially damaging it.
4. What is the difference between hard-switching and soft-switching in DC choppers?
Hard-switching refers to the conventional switching technique used in DC choppers, where the switch is turned on and off abruptly, causing voltage and current transients. This results in high switching losses and electromagnetic interference (EMI).
Soft-switching techniques, such as zero-voltage switching (ZVS) and zero-current switching (ZCS), aim to reduce the switching losses and EMI by ensuring that the voltage or current across the switch is zero during the switching transitions. This allows for higher switching frequencies and improved efficiency compared to hard-switching.
5. What are the factors to consider when selecting a DC chopper for a specific application?
When selecting a DC chopper for a specific application, several factors should be considered:
– Input voltage range: The chopper should be able to handle the expected range of input voltages.
– Output voltage and current requirements: The chopper should be capable of providing the desired output voltage and current levels.
– Load type: The chopper should be suitable for the type of load (e.g., resistive, inductive, or capacitive) and its electrical characteristics.
– Efficiency: The chopper should have high efficiency to minimize power losses and heat generation.
– Switching frequency: The switching frequency should be chosen based on the trade-off between efficiency
Leave a Reply