What is a Custom Wire Harness?
A custom wire harness is a wiring assembly that is designed and built to a customer’s unique specifications rather than being an off-the-shelf product. The wire harness is custom-made based on the intended end application, performance requirements, operating environment, and other important criteria.
Custom wire harnesses offer several advantages compared to generic wiring solutions:
- Wires, connectors and components can be sized appropriately for the electrical loads and environmental conditions
- Conductors and jackets can be color-coded for easy identification and troubleshooting
- Harnesses can be pre-assembled to the correct lengths and with the right connectors for plug-and-play installation
- Protective sleeves, conduits and fasteners can be integrated to organize wires into a tidy, secure package
- Quality can be controlled from end-to-end, from material selection through to assembly and testing
Typical applications that utilize custom wire harnesses include:
Industry | Applications |
---|---|
Automotive | Engine wiring, chassis wiring, dashboard electronics, lighting, aftermarket stereos |
Aerospace | Avionics, in-flight entertainment, seat electronics, weapons systems |
Medical | Diagnostic equipment, patient monitoring, surgical robotics, imaging systems |
Industrial | Factory automation, robotics, motor controls, sensors, lighting |
Electronics | Computers, networking equipment, telecom, appliances, security systems |
Energy | Solar panels, wind turbines, battery storage, smart grid |
Transportation | Trucks, buses, trains, ships, agricultural equipment, construction equipment |
Military | Communications gear, surveillance, detection, mobility systems |
Wire Harness Design Process
Designing a custom wire harness is a multi-step process that involves close collaboration between the customer and the manufacturer’s engineering team. Key steps include:
1. Requirements Gathering
The first step is gaining a thorough understanding of the customer’s application and performance requirements. Key considerations include:
- Desired functionality
- Operating voltage and current
- Environmental exposure (temperature, moisture, chemicals, abrasion, etc.)
- Space constraints
- Regulatory standards
- Budget
2. Schematic Diagram
Based on the requirements, the manufacturer will develop a schematic wiring diagram as a blueprint for the harness. The schematic will specify components such as:
- Wire gauges
- Wire lengths
- Connectors
- Splices
- Fastening points
- Labelling
3. Materials Selection
With the schematic finalized, the manufacturer will select the appropriate materials and components to meet performance and cost targets. Considerations include:
- Conductor material (copper, aluminum, etc.)
- Insulation and jacket material (PVC, cross-linked polyethylene, Teflon, etc.)
- Insulation voltage rating, temperature rating and flammability
- Shielding (foil, braid) for EMI/RFI protection
- Connector types (crimp, solder, IDC, etc.)
- Connector gender, number of positions and pitches
- Accessories (tubing, clamps, grommets, cable ties, shrink wrap, etc.)
4. Prototype and Testing
Before moving into production, the manufacturer will typically assemble a prototype harness and perform testing and validation, including:
- Continuity testing to verify point-to-point connections
- HiPot testing to confirm insulation integrity under high voltage
- Accelerated lifecycle testing under extreme environmental conditions
- Connector retention force testing
- Real-world vibration, flex and abrasion testing
5. Manufacturing
Once the design is validated, the wire harness moves into production. Key steps include:
- Wire cutting to length
- Wire stripping, crimping and soldering
- Connector and contact insertion
- Harness tying and taping
- Labelling and marking
- Final testing and inspection
- Packaging and shipment
Choosing a Custom Wire Harness Manufacturer
With so much riding on the integrity of your product’s wiring, it’s important to choose a capable, experienced custom wire harness manufacturer. Important factors to consider include:
Technical Expertise
Look for a manufacturer with a knowledgeable engineering team that has experience with your type of application. They should be able to provide helpful design guidance while understanding the cost implications of different wiring approaches.
Manufacturing Capabilities
Tour the manufacturer’s facility to evaluate their production capabilities. Key considerations include:
- Automated wire processing equipment to cut, strip and terminate wires efficiently and consistently
- Injection molding for custom connectors and housings
- Ultrasonic welding for joining wires and insulation
- Potting and encapsulation for environmental sealing
- Laser wire marking for identification and traceability
- ESD-safe assembly areas for sensitive electronics
Quality Assurance
Understand the manufacturer’s quality management system and the certifications they hold. At a minimum, they should be ISO 9001 certified. For automotive, medical, aerospace and military applications, additional certifications may be required, such as:
- IATF 16949 for automotive
- ISO 13485 for medical devices
- AS9100D for aerospace
- IPC-WHMA-A-620 for cable and wire harness assemblies
Testing Capabilities
Evaluate the manufacturer’s in-house testing capabilities to verify the reliability and functionality of your harness. Valuable capabilities include:
- Automated electrical testers for continuity and HiPot testing
- Environmental test chambers for temperature, humidity and thermal shock
- Vibration and mechanical shock testers
- Salt spray chambers for corrosion testing
- Wire pull testers to measure connector retention strength
Supply Chain and Logistics
Make sure the manufacturer has a robust supply chain to secure the wire, connectors and components you need on time and at a fair price. Also consider their location and logistics capabilities relative to your manufacturing sites.
Industry Experience
Ideally, look for a manufacturer that has experience serving your particular industry. They will be familiar with common design requirements and standards. Some industries to consider include:
Industry | Relevant Standards |
---|---|
Automotive | USCAR, SAE J-1128, SAE J-1939 |
Aerospace | MIL-W-22759, NEMA WC 27500, SAE AS50881 |
Medical | IEC 60601-1, FDA 21 CFR |
Industrial | UL 1277, NFPA 79 |
Military | MIL-STD-202, MIL-STD-810, MIL-W-16878 |
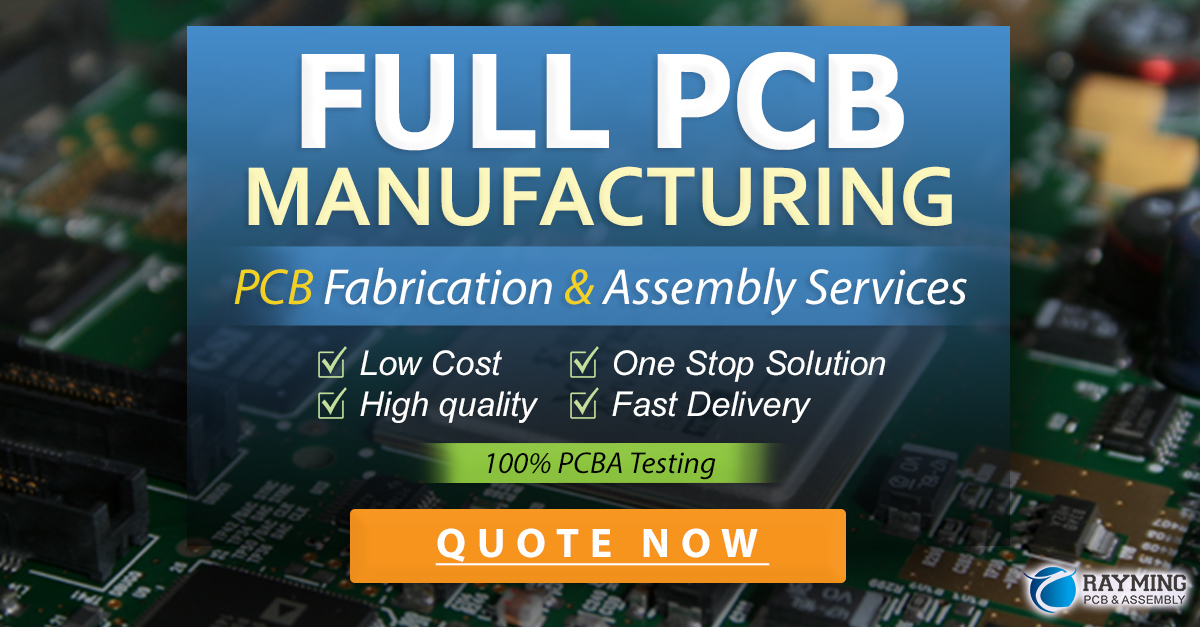
Common Wire Harness Failure Modes
Even a well-designed wire harness can experience failures under real-world use conditions. Common failure modes that a robust design and validation process will account for include:
Conductor Fatigue and Breakage
Repeated flexing and vibration can cause stranded conductors to break internally, leading to intermittent or open circuits. Specifying high-strand-count wire, minimizing bend radii, and using strain reliefs can mitigate this issue.
Insulation Damage
Abrasion, pinching, extreme temperatures and chemical exposure can breach the insulation, causing short circuits or ground faults. Insulation should be sized appropriately for the voltage and protected with abrasion-resistant sleeving in high-wear areas.
Connector Failures
Connectors can fail due to corrosion, contact fretting, contact misalignment, or improper crimping or soldering. Gold-plated contacts, dielectric grease, and positive locking mechanisms can improve connector reliability.
EMI/RFI Issues
Electromagnetic interference (EMI) and radio frequency interference (RFI) can cause signal degradation, especially in high-frequency applications. Proper grounding, shielding and twisted-pair wiring can reduce interference.
Poor Strain Relief
Cable flex and pulling forces can stress termination points, leading to conductor breakage or damaged connector housings. Clamps, cable glands, and service loops can provide proper strain relief.
FAQ
What’s the difference between a wire harness and a cable assembly?
The terms “wire harness” and “cable assembly” are often used interchangeably. Typically, a wire harness contains multiple insulated wires terminated to connectors, while a cable assembly may only contain one or a few conductors. However, the term wire harness is more common in applications like vehicles and industrial equipment.
How much does a custom wire harness cost?
The cost of a custom wire harness depends on several factors, including the number and type of wires, connectors, and accessories; the materials used; the level of environmental protection required; and the production volume. In general, expect to pay anywhere from a few dollars to a few hundred dollars per harness. The manufacturer can provide a more precise quote based on your specifications.
What’s the minimum order quantity for custom wire harnesses?
The minimum order quantity (MOQ) varies by manufacturer based on setup and tooling costs. Some manufacturers may produce orders as small as 50-100 pieces while others may require higher volumes to be cost-effective. If you need a very small quantity for prototyping, some manufacturers offer quick-turn services.
How long does it take to get custom wire harnesses?
Lead times depend on the complexity of the harness design, the availability of materials, and the manufacturer’s capacity. Expect at least 4-6 weeks from order placement to delivery, although some manufacturers can expedite orders if needed.
What information do I need to provide for a custom wire harness?
At a minimum, you’ll need to provide a schematic wiring diagram, a bill of materials specifying the wires and connectors, and any relevant drawings, 3D CAD models, or physical samples. The more complete and accurate information you can provide upfront, the smoother the design and manufacturing process will be.
In conclusion, a custom wire harness is a crucial component in many electrical applications, from automobiles to aerospace to industrial equipment. By partnering with an experienced, capable custom wire harness manufacturer, you can ensure your product is wired for reliable and safe performance in the field. Careful design, material selection, testing, and process control are key to the success of any custom wire harness project.
Leave a Reply