What is a Custom Cable Assembly?
A custom cable assembly is a specialized electrical cable designed and manufactured to meet specific requirements for a particular application or device. These assemblies are created by combining various components such as wires, connectors, terminals, and protective materials to form a complete cable solution tailored to the customer’s needs.
Custom cable assemblies are used in a wide range of industries, including:
- Aerospace and Defense
- Automotive
- Medical Devices
- Industrial Automation
- Telecommunications
- Consumer Electronics
The main advantage of using custom cable assemblies is that they provide a perfect fit for the intended application, ensuring optimal performance, reliability, and safety.
Components of a Custom Cable Assembly
A typical custom cable assembly consists of several key components:
Wires
The core of any cable assembly is the wire or wires used to transmit electrical signals or power. Wires can be made from various materials, such as copper, aluminum, or silver-plated copper, depending on the specific requirements for conductivity, flexibility, and durability.
Wires come in different gauges (thicknesses) and can be solid or stranded. Stranded wires are more flexible and resistant to fatigue, making them suitable for applications with frequent bending or movement.
Insulation
Insulation is the material that surrounds the wire conductor, providing electrical isolation and protection from environmental factors such as heat, moisture, and abrasion. Common insulation materials include:
- PVC (Polyvinyl Chloride)
- PE (Polyethylene)
- PP (Polypropylene)
- TPE (Thermoplastic Elastomer)
- PTFE (Polytetrafluoroethylene)
The choice of insulation material depends on the application’s requirements for temperature range, chemical resistance, and mechanical properties.
Shielding
In some cases, cable assemblies may require shielding to protect against electromagnetic interference (EMI) or radio frequency interference (RFI). Shielding is typically achieved by wrapping the insulated wires with a conductive material, such as copper braid, aluminum foil, or a combination of both.
Proper shielding ensures signal integrity and prevents interference from external sources or crosstalk between adjacent wires within the cable assembly.
Connectors
Connectors are the interface between the cable assembly and the devices or equipment it connects. They come in various types, sizes, and configurations, depending on the application requirements. Some common connector types include:
- USB (Universal Serial Bus)
- HDMI (High-Definition Multimedia Interface)
- D-Sub (D-Subminiature)
- RJ45 (Registered Jack 45)
- M8/M12 (Circular Connectors)
Connectors can be male or female, straight or right-angle, and may have different pin counts and arrangements. The choice of connector depends on factors such as signal type, data rate, power requirements, and the mating interface on the connected devices.
Overmolding
Overmolding is a process where a plastic material is injection-molded over a portion of the cable assembly, typically at the connector end. This process provides several benefits:
- Strain relief: Overmolding helps to distribute stress evenly and prevent damage to the wires or connectors caused by excessive bending or pulling.
- Environmental protection: Overmolded connectors can be sealed against moisture, dust, and other contaminants, making them suitable for harsh environments.
- Aesthetics: Overmolding allows for customization of the cable assembly’s appearance, including color, texture, and branding.
Custom Cable Assembly Design Process
The design process for a custom cable assembly involves several key steps:
1. Requirements Gathering
The first step in designing a custom cable assembly is to understand the customer’s specific requirements. This includes gathering information about the intended application, operating environment, performance expectations, and any applicable industry standards or regulations.
2. Electrical Design
Based on the requirements, the electrical design of the cable assembly is developed. This involves selecting the appropriate wire gauges, insulation materials, and shielding methods to ensure the assembly can handle the required voltage, current, and signal integrity.
3. Mechanical Design
The mechanical design focuses on the physical aspects of the cable assembly, such as the overall dimensions, bend radius, and connector placement. This step also involves selecting the appropriate connectors and determining the need for additional features like overmolding or strain relief.
4. Prototyping and Testing
Once the electrical and mechanical designs are complete, a prototype of the custom cable assembly is manufactured for testing and validation. This allows for the identification and correction of any issues before full-scale production begins.
5. Manufacturing
After the prototype is approved, the custom cable assembly enters the manufacturing phase. This involves sourcing the necessary components, setting up the production line, and implementing quality control measures to ensure consistent quality throughout the production run.
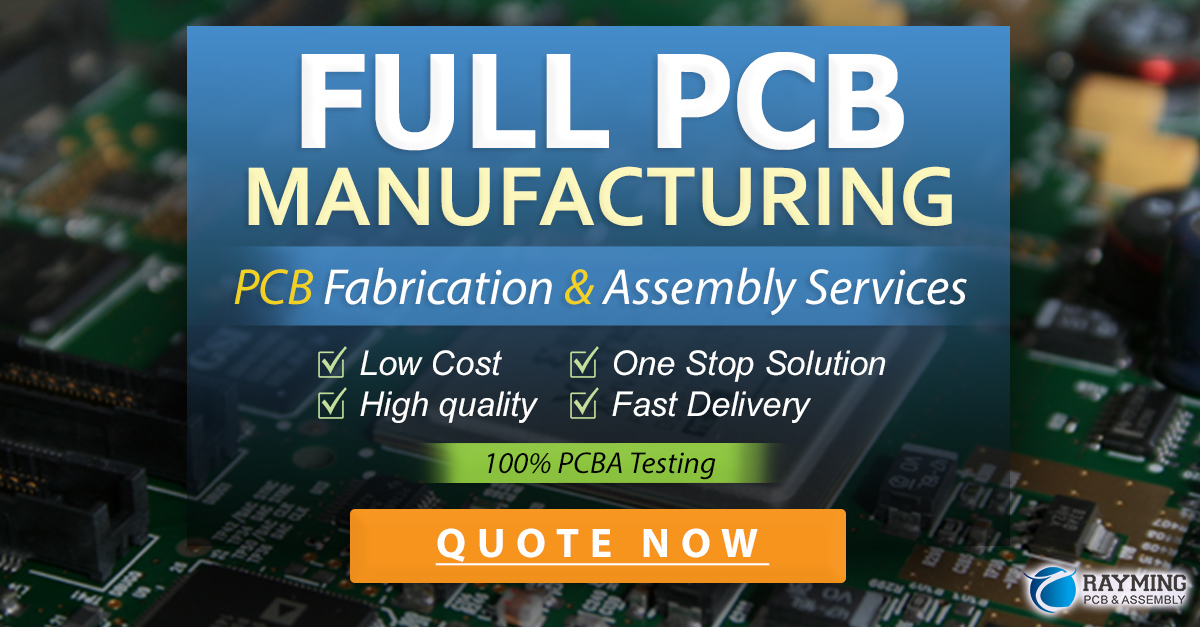
Benefits of Using Custom Cable Assemblies
Using custom cable assemblies offers several key benefits compared to off-the-shelf solutions:
-
Optimized Performance: Custom cable assemblies are designed specifically for the intended application, ensuring optimal electrical and mechanical performance. This can lead to improved system reliability, efficiency, and longevity.
-
Space Savings: By consolidating multiple wires and connectors into a single, compact assembly, custom cable assemblies can help to reduce the overall size and weight of the end product. This is particularly important in applications where space is limited, such as in aerospace or portable devices.
-
Simplified Installation: Custom cable assemblies are delivered ready to install, with all the necessary components and terminations pre-assembled. This simplifies the installation process, reduces the risk of errors, and saves time and labor costs.
-
Enhanced Durability: Custom cable assemblies can be designed to withstand specific environmental conditions, such as extreme temperatures, vibration, or exposure to chemicals. By selecting the appropriate materials and construction methods, the assembly can be made more durable and resistant to damage.
-
Cost Efficiency: While custom cable assemblies may have a higher upfront cost compared to off-the-shelf solutions, they can often provide long-term cost savings by reducing installation time, minimizing maintenance requirements, and extending the product’s lifespan.
Common Applications for Custom Cable Assemblies
Custom cable assemblies are used in a wide range of industries and applications. Some common examples include:
Aerospace and Defense
In aerospace and defense applications, custom cable assemblies are used for:
- Avionics systems
- Radar and communication equipment
- Satellite and spacecraft wiring
- Military vehicles and weapons systems
These assemblies must meet stringent requirements for reliability, durability, and resistance to harsh environmental conditions.
Automotive
Custom cable assemblies are used extensively in the automotive industry for:
- Engine wiring harnesses
- Sensor and actuator connections
- Infotainment and navigation systems
- Electric vehicle battery packs
Automotive cable assemblies must be able to withstand high temperatures, vibration, and exposure to fluids like oil and coolant.
Medical Devices
Medical device applications require custom cable assemblies that are:
- Biocompatible and sterilizable
- Resistant to fluids and chemicals
- Flexible and durable for repeated use
- Compliant with regulatory standards
Examples of medical devices that use custom cable assemblies include:
- Patient monitoring systems
- Surgical instruments
- Diagnostic imaging equipment
- Wearable devices
Industrial Automation
In industrial automation, custom cable assemblies are used for:
- Connecting sensors, actuators, and controllers
- Networking equipment and communication systems
- Power distribution and motor connections
- Robotic and motion control applications
Industrial cable assemblies must be robust, reliable, and resistant to harsh environmental conditions like extreme temperatures, humidity, and chemical exposure.
Telecommunications
Custom cable assemblies are critical components in telecommunications infrastructure, including:
- Fiber optic networks
- Cellular base stations
- Data centers and server racks
- Broadband and cable TV distribution
Telecommunications cable assemblies must provide high-speed data transmission, low signal loss, and resistance to electromagnetic interference.
Quality Control and Testing for Custom Cable Assemblies
Ensuring the quality and reliability of custom cable assemblies is crucial for their intended applications. Manufacturers employ various quality control measures and testing procedures to verify that the assemblies meet the specified requirements.
Visual Inspection
Visual inspection is the first line of defense in identifying potential issues with custom cable assemblies. This process involves examining the assembly for any visible defects, such as:
- Damaged or frayed wires
- Incorrect color coding or labeling
- Poor crimping or soldering of terminals
- Inadequate strain relief or overmolding
Continuity and Resistance Testing
Continuity testing verifies that the electrical connections within the cable assembly are intact and free from opens or shorts. This is typically done using a multimeter or dedicated continuity tester.
Resistance testing measures the resistance of individual wires or the overall assembly to ensure that it meets the specified requirements. This helps to identify any potential issues with the wire gauge, material, or terminations.
Insulation Resistance Testing
Insulation resistance testing measures the resistance between the conductor and the surrounding insulation material. This test helps to verify the integrity of the insulation and identify any potential leakage paths that could lead to electrical failures.
High Voltage Testing
High voltage testing, also known as dielectric withstand testing, involves applying a high voltage between the conductor and the shield or ground. This test verifies that the insulation can withstand the specified voltage without breakdown or arcing.
Mechanical Testing
Mechanical testing evaluates the cable assembly’s ability to withstand physical stresses and maintain its integrity. Some common mechanical tests include:
- Pull testing: Applies a specified tensile force to the assembly to verify the strength of the wire terminations and strain relief.
- Flex testing: Subjects the assembly to repeated bending cycles to assess its flexibility and resistance to fatigue.
- Crush testing: Applies a compressive force to the assembly to verify its ability to withstand external pressure without damage.
Environmental Testing
Environmental testing exposes the custom cable assembly to simulated operating conditions to verify its performance and durability. Some common environmental tests include:
- Temperature cycling: Subjects the assembly to alternating high and low-temperature extremes to assess its ability to withstand thermal stress.
- Humidity testing: Exposes the assembly to high humidity levels to verify its resistance to moisture ingress and corrosion.
- Vibration and shock testing: Evaluates the assembly’s ability to withstand mechanical vibrations and sudden impacts without damage or performance degradation.
By conducting these quality control measures and testing procedures, manufacturers can ensure that custom cable assemblies meet the required specifications and are suitable for their intended applications.
Choosing a Custom Cable Assembly Manufacturer
When selecting a manufacturer for your custom cable assembly needs, consider the following factors:
-
Experience and Expertise: Look for a manufacturer with a proven track record in designing and producing custom cable assemblies for your specific industry or application. They should have the necessary knowledge and skills to guide you through the design process and recommend the best solutions for your requirements.
-
Manufacturing Capabilities: Ensure that the manufacturer has the equipment, facilities, and processes in place to handle your specific cable assembly needs. This includes the ability to work with the required materials, connectors, and termination methods, as well as the capacity to meet your production volume and timeline.
-
Quality Management System: Choose a manufacturer that has a robust quality management system in place, preferably one that is certified to industry standards such as ISO 9001 or AS9100. This demonstrates their commitment to maintaining consistent quality and continuous improvement.
-
Testing and Validation: Verify that the manufacturer has the necessary testing equipment and procedures to validate the performance and reliability of your custom cable assemblies. They should be able to provide test reports and certificates of compliance to ensure that the assemblies meet your specified requirements.
-
Customer Support and Communication: Look for a manufacturer that values clear communication and responsive customer support. They should be willing to collaborate closely with you throughout the design and production process, providing regular updates and addressing any concerns or questions you may have.
-
Cost and Lead Time: While cost is an important consideration, it should not be the sole deciding factor. Balance the cost with the manufacturer’s capabilities, quality, and reputation to ensure that you receive the best value for your investment. Also, consider the manufacturer’s ability to meet your required lead times and delivery schedules.
By carefully evaluating these factors, you can select a custom cable assembly manufacturer that best suits your needs and helps you achieve your project goals.
Frequently Asked Questions (FAQ)
1. What is the minimum order quantity for custom cable assemblies?
The minimum order quantity (MOQ) for custom cable assemblies varies depending on the manufacturer and the specific requirements of the assembly. Some manufacturers may have a relatively low MOQ, while others may require larger quantities to justify the setup costs and ensure cost-effectiveness. It’s best to discuss your specific needs with potential manufacturers to determine their MOQ policies.
2. How long does it take to design and manufacture a custom cable assembly?
The lead time for designing and manufacturing a custom cable assembly depends on several factors, including the complexity of the design, the availability of materials and components, and the manufacturer’s production capacity. A simple assembly may take a few weeks, while a more complex design with specialized components could take several months. To get an accurate estimate of the lead time for your specific project, consult with your chosen manufacturer and provide them with detailed requirements.
3. Can custom cable assemblies be designed to meet specific industry standards?
Yes, custom cable assemblies can be designed to meet a wide range of industry standards, such as:
- UL (Underwriters Laboratories)
- CSA (Canadian Standards Association)
- IPC (Association Connecting Electronics Industries)
- MIL-SPEC (Military Specifications)
- SAE (Society of Automotive Engineers)
When discussing your project with a manufacturer, be sure to specify any industry standards or regulatory requirements that your cable assembly must comply with. The manufacturer should be familiar with these standards and capable of designing and producing assemblies that meet the necessary criteria.
4. How can I ensure the long-term reliability of my custom cable assemblies?
To ensure the long-term reliability of your custom cable assemblies, consider the following:
- Choose a reputable manufacturer with experience in producing high-quality assemblies for your specific industry or application.
- Clearly communicate your requirements and operating conditions to the manufacturer, so they can design and manufacture the assembly accordingly.
- Select appropriate materials, components, and construction methods that are suitable for your application’s environmental and mechanical stresses.
- Verify that the manufacturer conducts thorough testing and quality control measures to validate the performance and reliability of the assemblies.
- Establish a regular maintenance and inspection schedule to identify and address any potential issues before they lead to failures.
By following these guidelines and working closely with your chosen manufacturer, you can help ensure that your custom cable assemblies provide reliable performance over their intended lifespan.
5. Can custom cable assemblies be designed for high-speed data transmission?
Yes, custom cable assemblies can be designed for high-speed data transmission applications, such as:
- USB 3.0/3.1/4.0
- HDMI 2.0/2.1
- DisplayPort
- Thunderbolt
- Ethernet (10G/25G/40G/100G)
When designing cable assemblies for high-speed data transmission, several key factors must be considered, including:
- Impedance matching and control
- Signal integrity and minimizing loss
- Shielding effectiveness against EMI/RFI
- Connector selection and termination methods
- Cable length and routing
An experienced custom cable assembly manufacturer will be able to guide you through the design process and recommend the best solutions for your high-speed data transmission needs. They should also have the necessary expertise and equipment to produce and test these assemblies to ensure optimal performance.
Conclusion
Custom cable assemblies play a critical role in ensuring the performance, reliability, and safety of a wide range of products and systems across various industries. By working with an experienced and reputable manufacturer, you can design and produce cable assemblies that are tailored to your specific requirements and application needs.
When embarking on a custom cable assembly project, it’s essential to clearly communicate your requirements, select appropriate materials and components, and verify that the manufacturer employs rigorous quality control and testing procedures. By following these guidelines and collaborating closely with your chosen manufacturer, you can ensure that your custom cable assemblies provide the optimal solution for your application, leading to improved system performance, reliability, and cost-effectiveness.
Leave a Reply