Copper Thickness and Its Impact on PCB Performance
One of the primary concerns that users have when working with copper PCBs is the thickness of the copper layer. The thickness of the copper layer can have a significant impact on the performance of the PCB, including its electrical conductivity, thermal management, and mechanical strength.
Understanding Copper Thickness
Copper thickness is typically measured in ounces per square foot (oz/ft²) or microns (μm). The most common copper thicknesses used in PCBs are:
Copper Thickness (oz/ft²) | Copper Thickness (μm) |
---|---|
0.5 oz/ft² | 17 μm |
1 oz/ft² | 35 μm |
2 oz/ft² | 70 μm |
3 oz/ft² | 105 μm |
Impact on Electrical Conductivity
The thickness of the copper layer directly affects the electrical conductivity of the PCB. Thicker copper layers provide lower resistance and higher current-carrying capacity, which is essential for high-power applications. However, thicker copper layers also increase the weight and cost of the PCB.
Thermal Management Considerations
Copper thickness also plays a role in the thermal management of the PCB. Thicker copper layers can help dissipate heat more effectively, which is crucial for applications that generate significant amounts of heat, such as power electronics.
Mechanical Strength and Durability
The thickness of the copper layer can also impact the mechanical strength and durability of the PCB. Thicker copper layers provide better resistance to mechanical stress and vibration, which is important for applications that are exposed to harsh environments.
Copper Trace Width and Spacing
Another important concern for users when working with copper PCBs is the width and spacing of the copper traces. The trace width and spacing can affect the signal integrity, crosstalk, and electromagnetic compatibility (EMC) of the PCB.
Factors Affecting Trace Width and Spacing
Several factors can influence the choice of trace width and spacing, including:
- Signal frequency and rise time
- Current-carrying requirements
- Manufacturing capabilities
- PCB layer count and density
Signal Integrity Considerations
Trace width and spacing can have a significant impact on signal integrity, particularly for high-speed signals. Narrower traces and smaller spacing can lead to increased crosstalk and signal reflections, which can degrade signal quality and cause errors in data transmission.
Crosstalk and EMC
Crosstalk occurs when signals from one trace couple onto adjacent traces, causing interference and signal distortion. Proper trace spacing and the use of ground planes can help minimize crosstalk and improve EMC performance.
Copper Surface Finish Options
The surface finish of the copper layer is another important consideration for users when working with copper PCBs. The surface finish protects the copper from oxidation and corrosion, enhances solderability, and improves the overall reliability of the PCB.
Common Copper Surface Finishes
Some of the most common copper surface finishes used in PCBs include:
- Hot Air Solder Leveling (HASL)
- Electroless Nickel Immersion Gold (ENIG)
- Immersion Silver (IAg)
- Immersion Tin (ISn)
- Organic Solderability Preservative (OSP)
Choosing the Right Surface Finish
The choice of surface finish depends on several factors, such as the intended application, environmental conditions, shelf life requirements, and cost. Each surface finish has its own advantages and disadvantages, and users should carefully consider their specific needs when selecting a surface finish.
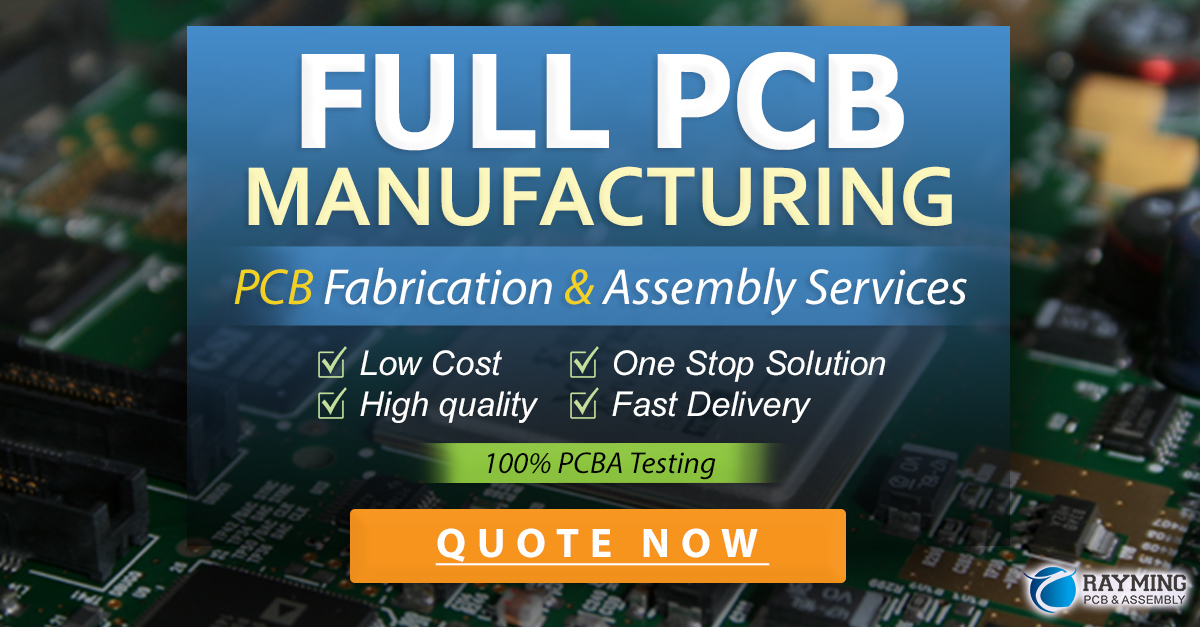
Copper Etching and Manufacturing Challenges
The process of etching copper to create the desired circuit patterns on a PCB can present several manufacturing challenges that users should be aware of.
Etching Precision and Accuracy
Achieving high precision and accuracy during the etching process is crucial for ensuring the proper functioning of the PCB. Factors such as etchant concentration, temperature, and agitation can affect the etching rate and the resulting trace dimensions.
Undercut and Overetch
Undercut occurs when the etchant removes more copper from the sides of the traces than the top, resulting in traces that are narrower at the base than at the top. Overetch, on the other hand, occurs when the etchant removes too much copper, leading to traces that are thinner than intended.
Copper Thickness Variation
Variations in copper thickness across the PCB can lead to inconsistencies in trace impedance and current-carrying capacity. Proper process control and monitoring are essential for minimizing copper thickness variations.
Copper Plating and Via Filling
Copper plating is often used to increase the thickness of the copper layer in specific areas of the PCB, such as in vias and through-holes. Via filling is another process that involves filling the vias with copper to create a solid connection between layers.
Importance of Copper Plating and Via Filling
Copper plating and via filling are important for several reasons:
- Improving electrical conductivity and current-carrying capacity
- Enhancing thermal management
- Providing better mechanical support and durability
Challenges in Copper Plating and Via Filling
Some of the challenges associated with copper plating and via filling include:
- Ensuring uniform plating thickness
- Achieving complete via fill without voids or defects
- Maintaining proper adhesion between the plated copper and the base material
Copper Grain Structure and Annealing
The grain structure of the copper layer can have a significant impact on the mechanical and electrical properties of the PCB. Annealing is a process that involves heating the copper to a specific temperature and then cooling it slowly to improve its grain structure and reduce internal stresses.
Impact of Grain Structure on PCB Performance
The grain structure of the copper layer can affect several aspects of PCB performance, including:
- Mechanical strength and flexibility
- Electrical conductivity and resistance
- Thermal conductivity and heat dissipation
Benefits of Annealing
Annealing can provide several benefits for copper PCBs, such as:
- Improving the ductility and formability of the copper
- Reducing internal stresses and the risk of cracking or fracturing
- Enhancing the electrical and thermal conductivity of the copper
Copper Recycling and Environmental Concerns
As with any manufacturing process, the production of copper PCBs can have environmental impacts that users should be aware of. Copper recycling is an important consideration for minimizing the environmental footprint of PCB manufacturing.
Environmental Impact of Copper Mining and Processing
Copper mining and processing can have significant environmental impacts, including:
- Habitat destruction and deforestation
- Water and air pollution
- Greenhouse gas emissions
Importance of Copper Recycling
Recycling copper from old PCBs can help reduce the environmental impact of PCB manufacturing by:
- Conserving natural resources and reducing the need for new copper mining
- Saving energy and reducing greenhouse gas emissions associated with copper production
- Minimizing waste and landfill disposal of old PCBs
Challenges in Copper Recycling
Some of the challenges associated with copper recycling from PCBs include:
- Separating the copper from other materials, such as solder mask and laminate
- Ensuring the purity and quality of the recycled copper
- Establishing efficient and cost-effective recycling processes
Frequently Asked Questions (FAQ)
-
Q: What is the most common copper thickness used in PCBs?
A: The most common copper thickness used in PCBs is 1 oz/ft² (35 μm). -
Q: How does copper thickness affect the performance of a PCB?
A: Copper thickness can affect the electrical conductivity, thermal management, and mechanical strength of a PCB. Thicker copper layers provide better performance in these areas but also increase the weight and cost of the PCB. -
Q: What factors should be considered when choosing a copper surface finish?
A: Factors to consider when choosing a copper surface finish include the intended application, environmental conditions, shelf life requirements, and cost. Each surface finish has its own advantages and disadvantages. -
Q: What is the difference between undercut and overetch in copper etching?
A: Undercut occurs when the etchant removes more copper from the sides of the traces than the top, resulting in traces that are narrower at the base. Overetch occurs when the etchant removes too much copper, leading to traces that are thinner than intended. -
Q: Why is copper recycling important for the environment?
A: Copper recycling helps reduce the environmental impact of PCB manufacturing by conserving natural resources, saving energy, reducing greenhouse gas emissions, and minimizing waste and landfill disposal of old PCBs.
In conclusion, copper PCBs are widely used in various applications due to their excellent electrical conductivity and affordability. However, users should be aware of the important issues and concerns associated with copper PCBs, such as copper thickness, trace width and spacing, surface finish options, manufacturing challenges, copper plating and via filling, grain structure and annealing, and environmental considerations. By understanding these issues and making informed decisions, users can ensure the optimal performance and reliability of their copper PCBs while minimizing their environmental impact.
Leave a Reply