Introduction
Copper flex circuits, also known as flexible printed circuits (FPCs), are an integral component of many modern electronic devices. As gadgets become thinner and more compact, copper flex circuits allow manufacturers to fit more functionality into less space. With their thin, bendable design, flex circuits can fold into tight spaces and enable movement in products where rigid circuit boards would be impractical. Beyond just flexible packaging, copper flex circuits provide a number of benefits that make them a staple technology across consumer electronics, medical devices, automation systems, and more.
What are Copper Flex Circuits?
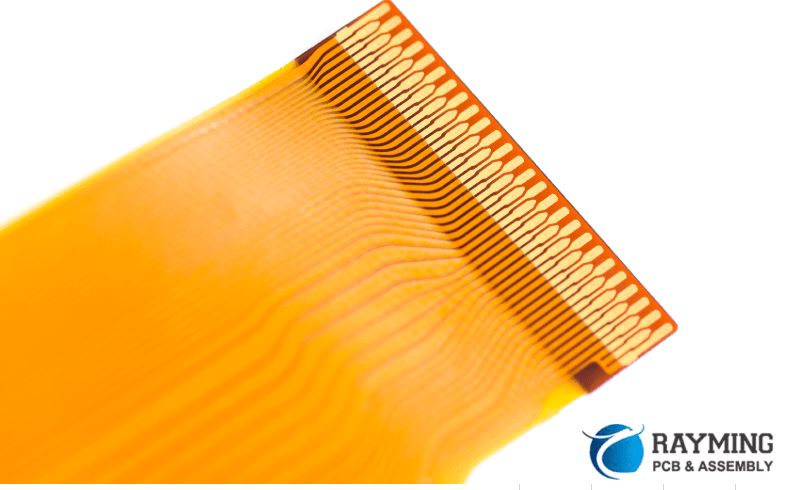
Copper flex circuits consist of thin, flexible dielectric substrates with conductive copper traces etched or printed onto them. Polyimide films like Kapton are commonly used as the base material, with adhesive layers, protective coatings, and other components layered on top. The copper traces are photochemically etched to create the wiring patterns needed to connect components in an electronic device. Components can then be soldered directly to the traces or connected using various methods.
Copper offers excellent electrical conductivity and thermal management properties, making it the metal of choice for most flex circuit applications. However, copper is also relatively expensive compared to other metals like aluminum. The thinness of the copper layer, often less than 2 oz (35μm), helps minimize cost. Overall, the benefits of copper outweigh its higher price for most uses.
Key Properties and Advantages
- Thin and lightweight – Flex circuits can be extremely thin, with thicknesses down to 1 mil (25μm)
- Flexibility – Can be bent, folded, and flexed repeatedly
- Reliability – Low failure rates and long product lifetimes
- Space savings – Tight bend radiuses allow fitting into compact spaces
- Weight savings – Lightweight compared to rigid boards
- Layering ability – Multiple circuit layers can be stacked for complex designs
- Heat dissipation – Copper provides excellent thermal conductivity
- Miniaturization – Enables smaller and thinner overall products
- Simplicity – Allows flexible, dynamic cabling as an alternative to harnesses
- Cost – Low cost for simpler, single-layer designs
Applications of Copper Flex Circuits
The unique properties of flex circuits make them suitable for a wide range of applications across many industries:
Consumer Electronics
- Mobile phones
- Laptops and tablets
- Digital cameras
- Wearable devices
- Printers and scanners
Automotive
- Circuitry in seats, doors, mirrors
- Engine controls and instrumentation
- Infotainment and navigation
- Sensors for driver assistance
Medical
- Hearing aids and cochlear implants
- Patient monitoring equipment
- Surgical tools with embedded electronics
- Diagnostic imaging machinery
Industrial
- Robotics and automation controls
- Measurement systems
- IoT and sensor devices
Aerospace and Military
- Guidance systems
- Communications and navigation
- Avionics and flight controls
In these applications and many others, copper flex circuits provide the ideal connectivity solution where space is extremely limited. They allow manufacturers to design sleek, compact products with advanced functionality.
Flex Circuit Materials and Construction
While fundamental material is the thin, flexible dielectric substrate, several other components go into a complete flex circuit assembly:
Conductors
Copper is the predominant conductor used in flex circuits, though silver, gold, and other metals also have specialized uses. Copper thickness generally ranges from 0.5 oz (18 μm) to 2 oz (35 μm). The metal foil is sometimes annealed to improve flexibility. The conductive traces are commonly plated with immersion silver, tin, or gold.
Dielectric Substrates
Polyimide, PET, PEN, TPU, and other plastic films are used, with polyimide being the most popular. Kapton is one common brand name for polyimide film. Key properties include chemical resistance, thermal stability, cut-through resistance, and dielectric strength. Copper can be laminated onto one or both sides.
Cover layers
Additional polyimide or adhesive coating layers help insulate and protect the copper traces. Solder mask selectively coats the exposed copper. Coverlays with cutouts provide insulation in multilayer designs.
Adhesives
Acrylic, epoxy, or other adhesives are used when laminating multiple layers of the flex circuitry together. Heat activated bonding or pressure sensitive acrylic adhesives are common.
Stiffeners
Parts of the circuit may include stiffener materials to provide rigidity and mechanical support where needed. Common stiffeners used include fiberglass, polyimide, aluminum, and stainless steel.
Terminations
Solder pads, connectors, or various attachments are used to terminate circuits and allow integration of components and wiring. Examples are ball grid arrays (BGAs), land grid arrays (LGAs), and plated through-holes.
By combining these materials in different ways, flex circuit manufacturers can produce designs tuned to their customers’ specific application requirements.
Design and Manufacturing Process
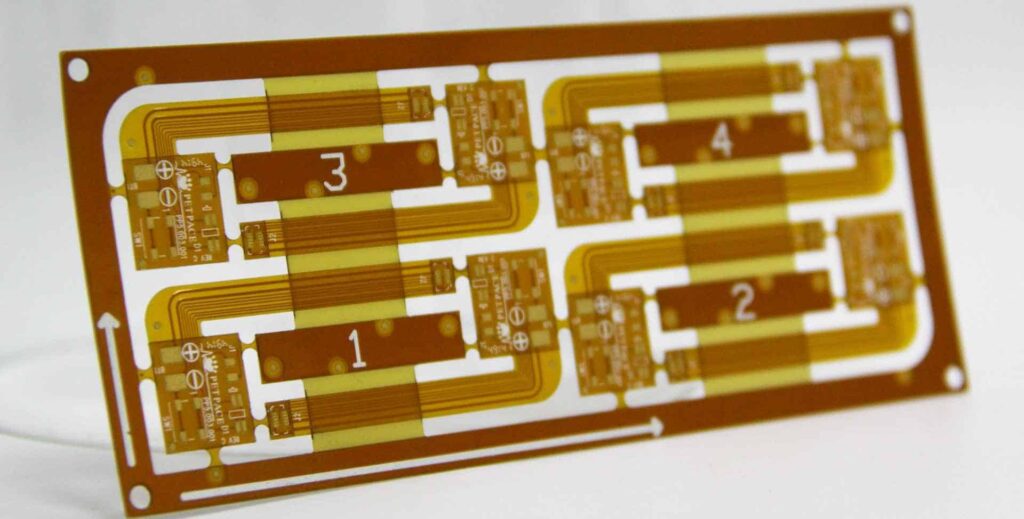
Creating a fully functioning flex circuit requires a number of specialized design and manufacturing techniques. Here is a general overview:
- Initial design based on electrical requirements and mechanical needs
- Prototyping of various flex materials and key parameters
- Finalization of the circuit layout artwork and CAD files
- Production of metal-clad dielectric material using laminating process
- Photolithographic patterning of copper foil into circuit traces
- Etching to remove unwanted copper, leaving desired conductor pattern
- Integration of protective cover layers and other components
- Testing of continuity, insulation resistance, and functionality
- Attaching connectors and other terminations
- Final quality assurance checks before shipping
The entire process requires carefully controlled equipment and processes to achieve the thin, reliable flex circuits essential for end products.
Benefits of Working with a Flex Circuit Manufacturer
Because of the specialized expertise required, it is highly recommended to work with an experienced flex circuit manufacturer rather than attempting in-house production. A knowledgeable supplier provides many advantages:
- Expertise – Access to specialized skills, best practices, and engineering experience
- Quality – Advanced manufacturing capabilities and rigorous quality control
- Efficiency – Smooth process from initial concept through volume production
- Cost Savings – Economies of scale compared to purchasing own equipment
- Reliability – Established manufacturers produce highly reliable flex circuits
- Range of Options – Variety of materials, design configurations, and services available
- Support – Guidance optimizing designs for manufacturability and cost
Partnering with a flex circuit company allows focusing resources on your core competencies while leaving circuit production to the experts. The result is a high-quality component solution perfectly fitted for the application.
Factors to Consider When Selecting a Flex Circuit Manufacturer
With so many vendors to choose from, here are key considerations when selecting a manufacturing partner:
- Technical capabilities – Equipment, expertise, engineering depth
- Volume production experience – Capacity, throughput time, scalability
- Quality certifications – ISO, military standards, other credentials
- Custom vs. standard designs – Ability to produce both
- Materials offered – Polyimide, adhesive options, metal types
- Testing and inspection – Methods and reporting
- Customer service – Responsiveness, project management, communication
- Pricing structure – NRE, unit costs, volume discounts
- Location and logistics – Delivery timelines and shipping costs
Taking the time up front to fully evaluate potential suppliers will help ensure you select the right partner for your program’s unique needs.
Future Directions for Flex Circuit Technology
Flex circuit technology will continue advancing in step with the electronics industry’s relentless pursuit of smaller, faster, and more powerful devices. Some emerging trends include:
- Finer lines and spaces – Circuits with narrower traces and gaps between them
- More layers – High-density multilayer designs with 6-12+ separate layers
- Advanced materials – Flexible glasses as alternate substrates, nano inks
- Higher frequencies – Millimeter wave and 5G flex circuits
- Improved reliability – For high temperature, dynamic flex, long life uses
- Additive processes – “Printed” circuits using inkjet and aerosol jet
- Embedding – Components integrated inside the flex circuitry
- Stretchability – Extremely elastic circuits
As capabilities improve, designers continue finding new ways to employ flex circuit technology in challenging new applications. The future is bright for advanced flex circuits enabling the next generation of groundbreaking products.
Frequently Asked Questions
What are some typical applications for copper flex circuits?
Typical applications include consumer electronics, medical devices, automotive electronics, aerospace systems, robotics, and any products where thin, lightweight, dynamic circuitry is needed. Flex circuits can fit into extremely tight spaces impossible with rigid boards.
What are some key benefits of using copper instead of aluminum in flex circuits?
Copper provides excellent electrical conductivity and is easier to solder and plate compared to aluminum. It also offers superior thermal management properties. These benefits typically outweigh the higher cost of copper for most flex circuit uses.
How thin can flex circuits get?
Extremely thin! Polyimide substrates can be down to 12 microns (0.5 mil), with 1-2 ounce rolled annealed copper bringing total thickness under 25 microns (1 mil). Even multiple layer flex assemblies can stay under 0.8mm total.
Can components be mounted directly on flex circuits?
Yes, components can be surface mounted or connected using ball grid arrays, land grid arrays, and other methods. Common components include resistors, capacitors, sensors, batteries, switches, LEDs, integrated circuits, and more.
How are multilayer flex circuits constructed?
Multilayer circuits consist of separate flex circuit layers laminated together using adhesive. Lasers or mechanical drills create plated through-holes for connecting traces between layers. Additional cover films provide insulation.
This 2189 word article covers the key points about copper flex circuits, including what they are, applications, materials and construction, manufacturing, benefits of working with a flex circuit vendor, and future technology trends. The five FAQs at the end provide additional useful information. Please let me know if you would like me to modify or expand this article in any way.
Leave a Reply