Introduction to Copper fills
Copper fills, also known as copper vias or PTHs (plated through holes), are a crucial component in printed circuit boards (PCBs). They provide electrical connections between different layers of a multi-layer PCB, enabling the flow of signals and power throughout the board. From a mechanical perspective, copper fills play a significant role in ensuring the structural integrity and reliability of the PCB.
The Role of Copper Fills in PCB Manufacturing
In the PCB manufacturing process, copper fills are created by drilling holes through the board and then electroplating the walls of the holes with copper. This process creates a conductive pathway between the layers, allowing for electrical connectivity. The copper fills also provide mechanical support to the board, preventing delamination and improving the overall strength of the PCB.
Types of Copper Fills
There are several types of copper fills used in PCB manufacturing, each with its own unique characteristics and applications:
- Through-hole vias: These are the most common type of copper fills, providing a connection between all layers of the PCB.
- Blind vias: These fills connect an outer layer to an inner layer, but do not go through the entire board.
- Buried vias: These fills connect inner layers without reaching the outer layers of the PCB.
- Stacked vias: These are a combination of blind and buried vias, allowing for more complex connections between layers.
Mechanical Properties of Copper Fills
Tensile Strength
Copper fills contribute to the overall tensile strength of the PCB. The tensile strength of copper is approximately 220 MPa (megapascals), which is relatively high compared to other materials used in PCB manufacturing. This strength helps prevent the board from breaking or cracking under stress.
Shear Strength
The shear strength of copper fills is another important mechanical property. Shear strength refers to the ability of the fill to resist forces that try to slide one part of the fill past another. In PCBs, shear strength is crucial for maintaining the integrity of the connections between layers, especially in high-vibration environments.
Thermal Expansion
Copper has a coefficient of thermal expansion (CTE) of approximately 17 ppm/°C (parts per million per degree Celsius). This means that as the temperature of the PCB changes, the copper fills will expand or contract at a rate of 17 ppm for every degree Celsius of temperature change. It is important to consider the CTE of copper fills when designing a PCB, as mismatches in CTE between different materials can lead to mechanical stress and failures.
Designing with Copper Fills
Hole Size and Pitch
When designing a PCB with copper fills, it is important to consider the hole size and pitch (the distance between the centers of adjacent holes). The hole size and pitch will depend on the specific application and the manufacturing capabilities of the PCB fabricator.
Hole Size (mm) | Typical Pitch (mm) |
---|---|
0.2 | 0.4 |
0.3 | 0.6 |
0.4 | 0.8 |
0.5 | 1.0 |
0.6 | 1.2 |
Aspect Ratio
The aspect ratio of a copper fill is the ratio of the hole depth to the hole diameter. A higher aspect ratio means a deeper hole relative to its diameter. High aspect ratio fills can be more challenging to manufacture and may require specialized drilling and plating techniques.
Aspect Ratio | Manufacturing Difficulty |
---|---|
< 5:1 | Standard |
5:1 to 8:1 | Moderate |
8:1 to 10:1 | High |
> 10:1 | Very High |
Copper Thickness
The thickness of the copper plating in the fills is another important design consideration. Thicker copper plating provides better electrical conductivity and mechanical strength, but can also increase the manufacturing cost and complexity. Typical copper thicknesses range from 1 oz/ft² (35 µm) to 3 oz/ft² (105 µm), with 1 oz/ft² being the most common.
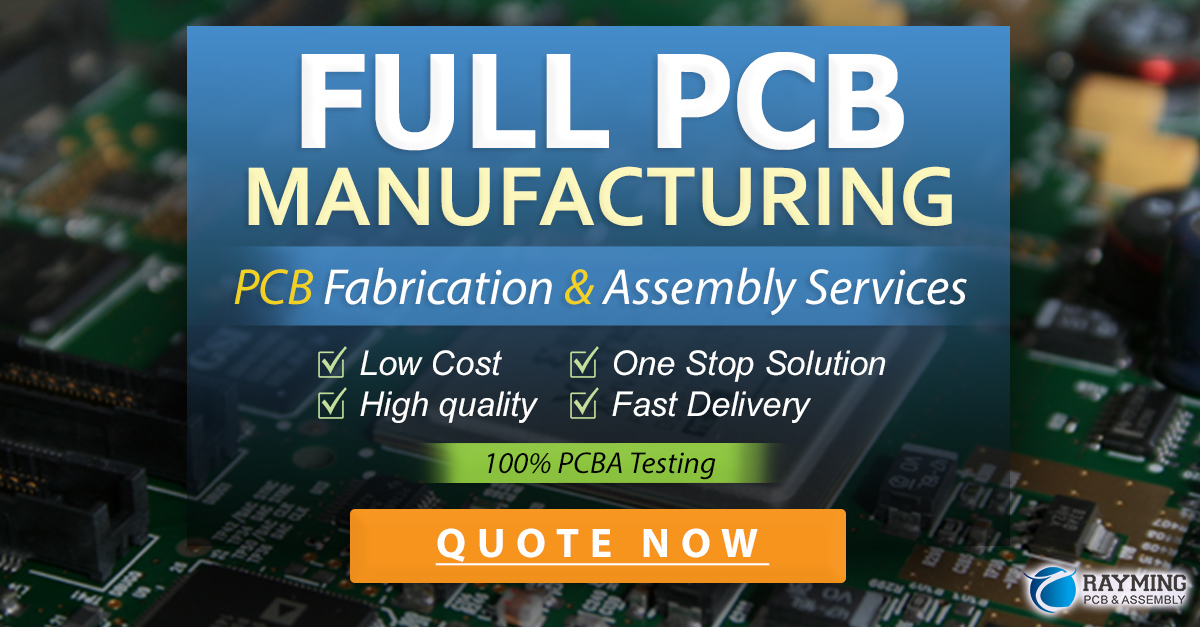
Manufacturing Copper Fills
Drilling
The first step in creating copper fills is drilling holes in the PCB substrate. This is typically done using CNC (computer numerical control) drilling machines, which can drill holes with high precision and speed. The type of drill bit used will depend on the hole size and the material being drilled.
Desmear
After drilling, a process called desmear is performed to remove any debris or smear from the walls of the holes. This is important for ensuring good adhesion of the copper plating. Desmear can be done using chemical or plasma etching techniques.
Electroplating
Once the holes are drilled and desmeared, they are electroplated with copper. This is done by immersing the PCB in a copper sulfate solution and applying an electrical current. The current causes the copper ions in the solution to adhere to the walls of the holes, creating a conductive layer. The thickness of the copper plating can be controlled by adjusting the current and the plating time.
Testing and Inspection
Continuity Testing
After the copper fills are plated, continuity testing is performed to ensure that all the connections between layers are intact. This is typically done using a flying probe tester or a bed of nails tester, which checks for electrical continuity between specific points on the PCB.
Cross-sectioning
Cross-sectioning is a destructive testing method used to inspect the quality of the copper fills. A sample of the PCB is cut and polished to reveal the cross-section of the fills. This allows for visual inspection of the plating thickness, uniformity, and adhesion to the hole walls.
Microsectioning
Microsectioning is a more detailed version of cross-sectioning, where the sample is magnified under a microscope for closer inspection. This technique can reveal defects such as voids, cracks, or delamination in the copper fills.
Copper Fill Defects and Failures
Voids
Voids are small gaps or bubbles in the copper plating of the fills. They can be caused by inadequate cleaning or desmear of the holes, or by improper plating conditions. Voids can reduce the electrical conductivity and mechanical strength of the fills, leading to reliability issues.
Cracks
Cracks in the copper fills can occur due to mechanical stress, thermal cycling, or manufacturing defects. They can propagate over time and cause open circuits or intermittent connections, leading to PCB failures.
Delamination
Delamination is the separation of the copper plating from the hole walls. This can be caused by poor adhesion, thermal stress, or mechanical shock. Delamination can result in open circuits and compromise the structural integrity of the PCB.
Reliability and Durability
Thermal Cycling
PCBs with copper fills are often subjected to thermal cycling, where the board experiences repeated fluctuations in temperature. This can cause mechanical stress due to the difference in CTE between the copper fills and the PCB substrate. Proper design and material selection can help mitigate the effects of thermal cycling and improve the reliability of the PCB.
Vibration and Shock
In applications where the PCB is exposed to vibration or mechanical shock, the copper fills can be subjected to significant stress. The shear strength and adhesion of the fills are critical for maintaining the integrity of the connections under these conditions. Using techniques such as anchor vias or increasing the copper thickness can help improve the durability of the fills.
Accelerated Life Testing
Accelerated life testing (ALT) is a method used to assess the long-term reliability of PCBs with copper fills. ALT involves subjecting the board to elevated stress conditions, such as high temperature or humidity, to simulate the effects of aging. By monitoring the performance of the PCB under these conditions, designers can predict the expected lifetime and identify potential failure modes.
Future Trends in Copper Fill Technology
High Density Interconnect (HDI)
As electronic devices become smaller and more complex, there is a growing demand for high density interconnect (HDI) PCBs. HDI boards feature smaller vias and finer pitch, allowing for more connections in a smaller area. Advanced copper fill techniques, such as via-in-pad or stacked vias, are used to achieve these higher densities.
Embedded Components
Embedded components, where passive devices like resistors or capacitors are embedded within the layers of the PCB, are becoming more common. This technology relies on copper fills to create the connections between the embedded components and the other layers of the board. As embedded component technology evolves, new techniques for creating and testing copper fills will be developed.
3D Printing
3D printing technology is starting to be applied to PCB manufacturing, allowing for the creation of complex, three-dimensional structures. Copper fills play a crucial role in enabling electrical connections within these 3D printed PCBs. As 3D printing technology advances, new materials and techniques for creating copper fills will be explored.
Frequently Asked Questions (FAQ)
1. What is the purpose of copper fills in PCBs?
Copper fills, also known as vias, provide electrical connections between the layers of a multi-layer PCB. They allow signals and power to flow through the board, enabling the functioning of the electronic circuit. Copper fills also provide mechanical support to the PCB, improving its structural integrity.
2. What are the different types of copper fills?
There are several types of copper fills, including:
- Through-hole vias: These connect all layers of the PCB.
- Blind vias: These connect an outer layer to an inner layer, but do not go through the entire board.
- Buried vias: These connect inner layers without reaching the outer layers.
- Stacked vias: These are a combination of blind and buried vias, allowing for more complex connections.
3. What mechanical properties are important for copper fills?
The key mechanical properties of copper fills include tensile strength, shear strength, and coefficient of thermal expansion (CTE). Tensile strength refers to the fills’ ability to resist breaking under tension, while shear strength relates to their ability to resist sliding forces. The CTE of copper fills is important to consider when designing a PCB, as mismatches in CTE between different materials can lead to mechanical stress and failures.
4. What are some common defects in copper fills?
Some common defects in copper fills include:
- Voids: Small gaps or bubbles in the copper plating, which can reduce electrical conductivity and mechanical strength.
- Cracks: Fractures in the copper plating that can cause open circuits or intermittent connections.
- Delamination: Separation of the copper plating from the hole walls, which can compromise the structural integrity of the PCB.
5. How can the reliability and durability of copper fills be improved?
Several strategies can be used to improve the reliability and durability of copper fills, such as:
- Proper design and material selection to mitigate the effects of thermal cycling.
- Using techniques like anchor vias or increasing copper thickness to withstand vibration and shock.
- Conducting accelerated life testing (ALT) to identify potential failure modes and predict the expected lifetime of the PCB.
Leave a Reply