Introduction to Controlled Impedance PCB
In the world of high-speed electronics, signal integrity is a crucial aspect that cannot be overlooked. As digital systems continue to push the boundaries of speed and performance, the need for reliable and efficient printed circuit boards (PCBs) becomes increasingly important. One key factor in ensuring optimal signal integrity is the implementation of controlled impedance PCB design techniques, particularly in the realm of PCB copper traces.
Controlled impedance PCB refers to the practice of designing and manufacturing PCBs with precise control over the impedance of the copper traces. By carefully managing the impedance of these traces, designers can minimize signal integrity issues such as reflections, crosstalk, and electromagnetic interference (EMI), which can degrade the performance and reliability of electronic systems.
In this comprehensive article, we will delve into the intricacies of controlled impedance PCB design, focusing on the critical role of PCB copper traces in maintaining signal integrity. We will explore the fundamentals of impedance, the factors that influence trace impedance, and the various techniques used to achieve controlled impedance in PCB design and manufacturing.
Understanding Impedance in PCB Copper Traces
What is Impedance?
Impedance is a measure of the opposition that a circuit presents to the flow of alternating current (AC) or time-varying signals. It is a complex quantity that combines resistance, capacitance, and inductance, and is measured in ohms (Ω). In the context of PCB copper traces, impedance plays a vital role in determining how signals propagate along the traces and how they interact with other components on the board.
Factors Affecting Trace Impedance
Several factors contribute to the impedance of PCB copper traces:
-
Trace Geometry: The physical dimensions of the copper trace, including its width, thickness, and spacing from other traces or planes, significantly influence its impedance. Wider traces generally have lower impedance, while narrower traces have higher impedance.
-
Dielectric Material: The dielectric material surrounding the copper traces, typically the PCB substrate (e.g., FR-4), affects the trace impedance. The dielectric constant (Dk) and dissipation factor (Df) of the material determine its electrical properties and impact the impedance of the traces.
-
Frequency: The impedance of a copper trace varies with the frequency of the signal passing through it. At higher frequencies, the impedance becomes more complex due to the increased influence of capacitive and inductive effects.
-
Trace Routing: The routing of copper traces on a PCB, including their length, bends, and proximity to other traces or components, can affect their impedance. Proper trace routing is essential for maintaining consistent impedance throughout the signal path.
Importance of Controlled Impedance in PCB Design
Controlling the impedance of PCB copper traces is crucial for several reasons:
-
Signal Integrity: Uncontrolled impedance can lead to signal reflections, which occur when a signal encounters a change in impedance along its path. These reflections can cause signal distortion, ringing, and other undesirable effects that degrade the quality and reliability of the transmitted signal.
-
Crosstalk Reduction: When copper traces are in close proximity to each other, they can experience crosstalk, where signals from one trace couple onto adjacent traces. Controlled impedance helps minimize crosstalk by ensuring proper spacing and impedance matching between traces.
-
EMI Mitigation: Uncontrolled impedance can contribute to electromagnetic interference (EMI), where signals radiate unwanted energy that can interfere with nearby electronic devices. By maintaining consistent impedance, designers can reduce EMI and ensure compliance with electromagnetic compatibility (EMC) standards.
-
High-Speed Performance: As digital systems operate at increasingly higher speeds, the need for controlled impedance becomes more critical. At high frequencies, even small variations in impedance can have significant
effects on signal integrity and system performance. Controlled impedance PCBs are essential for achieving reliable high-speed communication and data transfer.
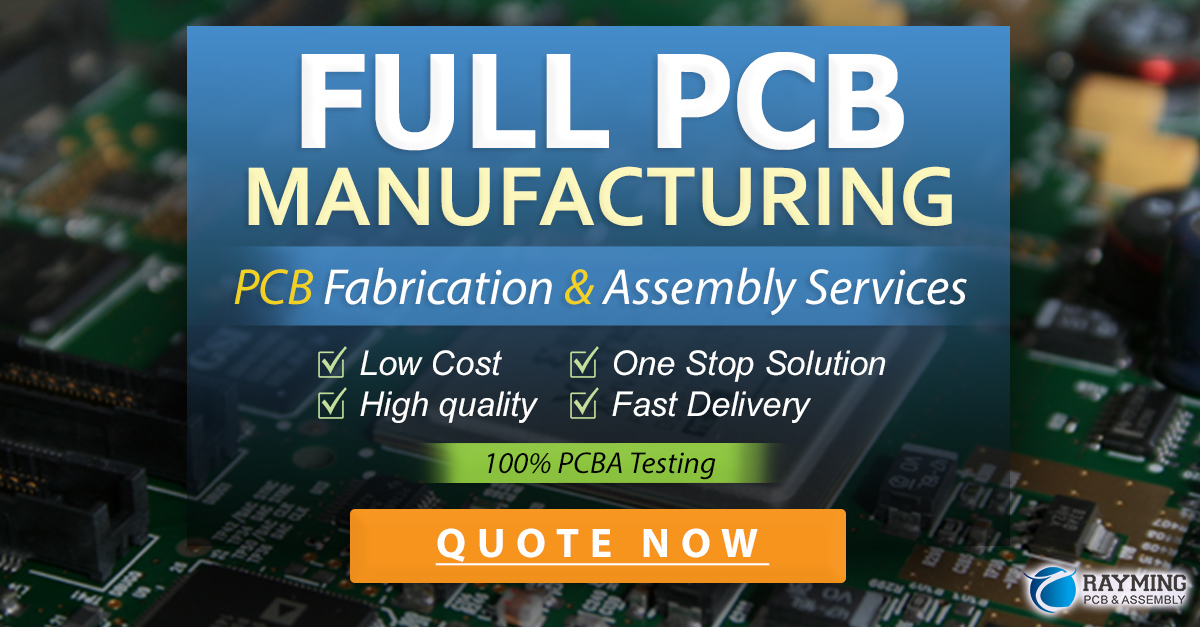
Techniques for Achieving Controlled Impedance
Designing and manufacturing controlled impedance PCBs requires a combination of careful planning, precise calculations, and specialized manufacturing processes. Here are some key techniques used to achieve controlled impedance:
Trace Geometry Calculations
One of the fundamental steps in controlled impedance PCB design is calculating the appropriate trace geometry to achieve the desired impedance. This involves determining the optimal trace width, thickness, and spacing based on factors such as the dielectric material, copper weight, and target impedance.
Several formulas and tools are available to assist in these calculations, including:
- Microstrip Impedance Formula: Used for traces on the outer layers of a PCB, where the trace is separated from a ground plane by the dielectric material.
Z₀ = (87 / √(Ɛᵣ + 1.41)) × ln(5.98 × h / (0.8 × w + t))
Where:
– Z₀ is the characteristic impedance (in ohms)
– Ɛᵣ is the relative dielectric constant of the substrate material
– h is the thickness of the dielectric (in mils)
– w is the width of the trace (in mils)
– t is the thickness of the trace (in mils)
- Stripline Impedance Formula: Used for traces embedded within the inner layers of a PCB, where the trace is sandwiched between two ground planes.
Z₀ = (60 / √Ɛᵣ) × ln(4 × h / (0.67 × (0.8 × w + t)))
Where the variables have the same meanings as in the microstrip formula.
These formulas provide a starting point for designing controlled impedance traces, but designers often use specialized software tools that take into account additional factors and provide more accurate results.
Dielectric Material Selection
The choice of dielectric material is crucial for achieving controlled impedance in PCB design. The dielectric constant (Dk) and dissipation factor (Df) of the material directly influence the impedance of the copper traces.
Common dielectric materials used in PCB manufacturing include:
Material | Dielectric Constant (Dk) | Dissipation Factor (Df) |
---|---|---|
FR-4 | 4.2 – 4.5 | 0.02 |
Rogers | 2.2 – 10.2 | 0.0009 – 0.0035 |
Polyimide | 3.2 – 3.5 | 0.002 – 0.003 |
Teflon | 2.0 – 2.1 | 0.0002 – 0.0007 |
Designers must carefully select the dielectric material based on the specific requirements of their application, considering factors such as the desired impedance, frequency range, and environmental conditions.
Precise Manufacturing Processes
Achieving controlled impedance in PCB manufacturing requires strict adherence to precise manufacturing processes. PCB fabricators use specialized equipment and techniques to ensure that the copper traces are formed with the desired dimensions and spacing.
Some key manufacturing processes for controlled impedance PCBs include:
-
Etching: The process of removing unwanted copper from the PCB substrate to form the desired trace patterns. Precise etching is essential for maintaining consistent trace widths and spacings.
-
Plating: The application of additional copper to the traces to achieve the desired thickness. Careful control of the plating process is necessary to maintain consistent impedance across the board.
-
Lamination: The process of bonding the multiple layers of a PCB together using heat and pressure. Proper lamination is critical for ensuring a uniform dielectric thickness and minimizing variations in impedance.
-
Controlled Depth Drilling: The use of specialized drilling techniques to create vias and through-holes with precise depths and diameters. This helps maintain consistent impedance in the transition between layers.
PCB fabricators often employ automated inspection systems and statistical process control (SPC) techniques to monitor and maintain the quality of controlled impedance PCBs throughout the manufacturing process.
Testing and Verification of Controlled Impedance PCBs
Once a controlled impedance PCB has been designed and manufactured, it is essential to test and verify its performance to ensure that it meets the desired specifications. Several methods are used to measure and characterize the impedance of PCB copper traces:
-
Time Domain Reflectometry (TDR): TDR is a technique that involves sending a fast-rising pulse down a transmission line (i.e., a copper trace) and measuring the reflected signals. By analyzing the timing and amplitude of the reflections, designers can determine the impedance profile of the trace and identify any discontinuities or mismatches.
-
Frequency Domain Analysis: This approach involves measuring the scattering parameters (S-parameters) of a PCB using a vector network analyzer (VNA). S-parameters provide information about the reflection and transmission characteristics of the traces over a range of frequencies, allowing designers to assess the impedance and signal integrity performance of the board.
-
Impedance Test Coupons: PCB manufacturers often include impedance test coupons on the production panel alongside the actual PCBs. These coupons are designed with specific trace geometries and can be measured to verify that the impedance of the manufactured traces matches the designed values.
Regular testing and verification of controlled impedance PCBs help ensure that the boards meet the required specifications and perform reliably in the intended application.
Best Practices for Controlled Impedance PCB Design
Designing controlled impedance PCBs requires a systematic approach and adherence to best practices to achieve optimal results. Some key considerations include:
-
Early Planning: Incorporate controlled impedance requirements into the PCB design process from the outset. This allows for proper allocation of space, layer stackup planning, and material selection.
-
Accurate Modeling: Use accurate PCB modeling tools and techniques to simulate the impedance of copper traces based on the selected materials, trace geometries, and stackup. This helps identify potential issues and optimize the design before manufacturing.
-
Consistent Trace Routing: Maintain consistent trace widths and spacings throughout the signal path to minimize impedance variations. Avoid abrupt changes in trace geometry, such as sharp bends or discontinuities, which can cause reflections.
-
Ground Plane Utilization: Incorporate continuous ground planes adjacent to controlled impedance traces to provide a stable reference and minimize crosstalk. Ensure proper grounding and avoid interruptions in the ground plane, which can affect impedance.
-
Termination Strategies: Use appropriate termination strategies, such as series termination or parallel termination, to match the impedance of the trace to the source or load. This helps minimize reflections and ensure clean signal transitions.
-
Collaborative Design Process: Foster close collaboration between PCB designers, signal integrity engineers, and PCB fabricators. Clear communication and understanding of controlled impedance requirements help ensure that the designed board can be manufactured reliably and cost-effectively.
By following these best practices and carefully considering the various aspects of controlled impedance PCB design, designers can create high-quality boards that deliver optimal signal integrity and performance.
Frequently Asked Questions (FAQ) about Controlled Impedance PCBs
-
Q: What is the difference between single-ended and differential controlled impedance?
A: Single-ended controlled impedance refers to the impedance of a single trace with respect to a reference plane (usually ground). Differential controlled impedance, on the other hand, refers to the impedance between two traces that form a differential pair, where the signals on the traces are equal in magnitude but opposite in polarity. -
Q: How does the choice of dielectric material affect controlled impedance?
A: The dielectric material’s properties, such as its dielectric constant (Dk) and dissipation factor (Df), directly influence the impedance of the copper traces. Materials with higher Dk values result in lower impedance, while materials with lower Dk values lead to higher impedance. The dissipation factor affects the loss and signal attenuation in the traces. -
Q: What are the typical impedance values used in controlled impedance PCB design?
A: Common controlled impedance values include 50 ohms, 75 ohms, and 100 ohms, depending on the application and the specific interface standards being used. For example, 50 ohms is commonly used for high-speed digital interfaces like USB, HDMI, and Ethernet, while 75 ohms is often used for video applications and coaxial cables. -
Q: Can controlled impedance be achieved on multi-layer PCBs?
A: Yes, controlled impedance can be achieved on multi-layer PCBs by carefully designing the layer stackup and utilizing appropriate trace geometries and spacing. Designers must consider the impedance requirements for each signal layer and ensure proper reference planes and grounding throughout the stackup. -
Q: How does controlled impedance affect the cost of PCB manufacturing?
A: Implementing controlled impedance in PCB manufacturing typically increases the cost compared to standard PCBs. This is due to the additional design effort, specialized materials, precise manufacturing processes, and testing required to achieve and verify the desired impedance. However, the cost impact varies depending on factors such as the PCB complexity, volume, and specific impedance requirements.
Conclusion
Controlled impedance PCB design is a critical aspect of modern electronics, particularly in high-speed digital systems where signal integrity is paramount. By carefully managing the impedance of PCB copper traces, designers can minimize signal integrity issues, reduce crosstalk and EMI, and ensure reliable performance across a wide range of frequencies.
Achieving controlled impedance requires a comprehensive understanding of the factors that influence trace impedance, including trace geometry, dielectric materials, and manufacturing processes. Designers must utilize accurate modeling tools, follow best practices, and work closely with PCB fabricators to ensure that the designed impedance is realized in the manufactured board.
As technology continues to advance and the demand for faster, more complex electronic systems grows, the importance of controlled impedance PCB design will only increase. By staying up-to-date with the latest techniques, materials, and design tools, PCB designers can create high-quality, controlled impedance boards that deliver optimal signal integrity and reliable performance in a wide range of applications.
Leave a Reply