Introduction to Circuit Continuity
Circuit continuity is a fundamental concept in electrical and electronic systems. It refers to the uninterrupted flow of electrical current through a closed circuit path. In other words, a continuous circuit allows electricity to flow from the source, through the various components, and back to the source without any breaks or interruptions. Ensuring circuit continuity is crucial for the proper functioning and safety of electrical devices and systems.
Importance of Circuit Continuity
Maintaining circuit continuity is essential for several reasons:
-
Proper Functioning: Electrical devices and systems rely on the uninterrupted flow of current to operate correctly. Any break in the circuit path can prevent the device from working as intended or cause it to malfunction.
-
Safety: Circuit continuity is critical for ensuring the safety of both the device and the user. Broken or interrupted circuits can lead to electrical hazards, such as electric shocks, fires, or explosions.
-
Troubleshooting: Continuity tests are often used as a diagnostic tool to identify faults or issues in electrical circuits. By checking for continuity, technicians can pinpoint the location of a problem and take appropriate steps to repair or replace the faulty component.
Continuity Test: Definition and Purpose
A continuity test is a simple and effective method used to verify the integrity of a circuit path. It involves using a testing device, such as a multimeter or a continuity tester, to check for the presence of a complete electrical path between two points in a circuit.
Definition of Continuity Test
A continuity test is a procedure that determines whether there is a continuous electrical path between two points in a circuit. It is performed by applying a small voltage across the two points and measuring the resistance or conductivity between them. If the resistance is low (typically close to zero ohms), it indicates that there is a complete circuit path, and continuity is present. Conversely, if the resistance is high (typically infinite or open circuit), it suggests that there is a break or interruption in the circuit path, and continuity is absent.
Purpose of Continuity Test
The primary purpose of a continuity test is to verify the integrity of electrical connections, wires, and components in a circuit. It helps to:
-
Identify Open Circuits: Continuity tests can detect open circuits, where there is a break in the electrical path, preventing current from flowing through the circuit.
-
Locate Short Circuits: Continuity tests can also identify short circuits, where two points in a circuit that should not be connected are inadvertently touching, causing an unintended flow of current.
-
Verify Proper Connections: Continuity tests ensure that electrical connections are properly made and that components are correctly wired in a circuit.
-
Troubleshoot Faults: By performing continuity tests, technicians can quickly identify and isolate faults in electrical systems, such as broken wires, loose connections, or damaged components.
Continuity Testing Devices
Several devices can be used to perform continuity tests, each with its own advantages and limitations. The most common continuity testing devices include:
Multimeter
A multimeter is a versatile testing device that can measure various electrical parameters, including voltage, current, resistance, and continuity. Most digital multimeters have a dedicated continuity testing mode, which is often represented by a diode symbol or a beeper icon.
To perform a continuity test with a multimeter:
- Set the multimeter to the continuity testing mode.
- Connect the test leads to the two points in the circuit that you want to test.
- If there is continuity, the multimeter will emit a beep sound, and the display will show a low resistance value (typically close to zero ohms). If there is no continuity, the multimeter will not beep, and the display will show a high resistance value (typically “OL” for open loop or infinite resistance).
Multimeter Continuity Test Results | Interpretation |
---|---|
Beep sound and low resistance | Continuity present |
No beep and high resistance | No continuity |
Continuity Tester
A continuity tester is a specialized device designed specifically for checking circuit continuity. It consists of a battery, a light bulb or LED, and two test leads. When the test leads are connected to two points in a circuit with continuity, the bulb or LED will light up, indicating a complete circuit path.
Continuity testers are simple and easy to use, making them a popular choice for quick continuity checks. However, they do not provide a quantitative measurement of resistance like multimeters do.
Analog Ohmmeter
An analog ohmmeter is another device that can be used for continuity testing. It measures resistance using a needle that deflects across a calibrated scale. To perform a continuity test with an analog ohmmeter, set the device to the lowest resistance range and connect the test leads to the two points in the circuit. If there is continuity, the needle will deflect towards zero ohms, indicating a complete circuit path.
Analog ohmmeters are less common than digital multimeters and continuity testers due to their lower accuracy and the need for manual scale interpretation.
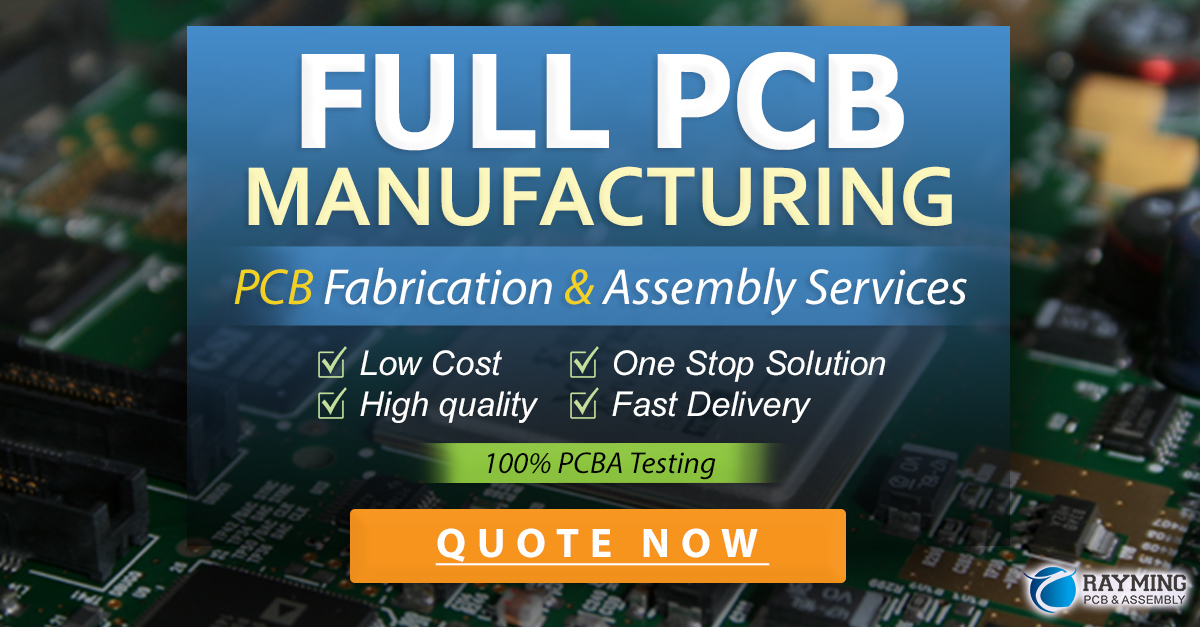
Performing a Continuity Test
To perform a continuity test effectively, follow these steps:
-
Identify the Circuit: Determine the circuit or component that needs to be tested for continuity. Refer to the schematic diagram or manual if available.
-
Disconnect Power: Ensure that the circuit is not powered during the continuity test. Disconnect any power sources, such as batteries or power adapters, to avoid damaging the testing device or the circuit itself.
-
Select the Testing Device: Choose an appropriate continuity testing device based on your requirements and the available tools. A multimeter or a continuity tester is commonly used.
-
Configure the Testing Device: If using a multimeter, set it to the continuity testing mode. For other devices, ensure they are properly calibrated and set up according to the manufacturer’s instructions.
-
Connect the Test Leads: Connect the test leads of the testing device to the two points in the circuit where you want to check for continuity. Make sure the leads make good contact with the test points.
-
Interpret the Results: Observe the display or indicators on the testing device to determine the presence or absence of continuity. A beep sound, a lit LED, or a low resistance reading indicates continuity, while no beep, no LED, or a high resistance reading suggests no continuity.
-
Repeat as Necessary: Perform the continuity test at multiple points in the circuit to thoroughly check for any breaks or interruptions in the electrical path.
Step | Description |
---|---|
1 | Identify the circuit |
2 | Disconnect power |
3 | Select the testing device |
4 | Configure the testing device |
5 | Connect the test leads |
6 | Interpret the results |
7 | Repeat as necessary |
Interpreting Continuity Test Results
Interpreting the results of a continuity test is straightforward. The testing device will provide a clear indication of whether continuity is present or not.
Continuity Present
If the testing device indicates continuity, it means that there is a complete and uninterrupted electrical path between the two test points. This is typically represented by:
- A beep sound on a multimeter or continuity tester
- A lit LED on a continuity tester
- A low resistance reading (close to zero ohms) on a multimeter or analog ohmmeter
Continuity present suggests that the circuit or component is functioning as intended, and there are no breaks or interruptions in the electrical path.
No Continuity
If the testing device does not indicate continuity, it means that there is a break or interruption in the electrical path between the two test points. This is typically represented by:
- No beep sound on a multimeter or continuity tester
- No lit LED on a continuity tester
- A high resistance reading (infinite or “OL” for open loop) on a multimeter or analog ohmmeter
No continuity suggests that there is a problem in the circuit, such as a broken wire, a loose connection, or a damaged component. Further investigation and troubleshooting are necessary to identify and resolve the issue.
Troubleshooting with Continuity Tests
Continuity tests are valuable tools for troubleshooting electrical and electronic systems. By systematically testing for continuity at various points in a circuit, technicians can quickly identify and isolate faults. Here are some common troubleshooting scenarios where continuity tests are useful:
Open Circuit
An open circuit occurs when there is a break in the electrical path, preventing current from flowing through the circuit. Continuity tests can help locate the point of the break, which could be caused by:
- Broken or damaged wires
- Loose or corroded connections
- Faulty switches or relays
- Damaged components, such as resistors or capacitors
By testing for continuity at different points along the circuit path, technicians can pinpoint the location of the open circuit and take appropriate steps to repair or replace the faulty component.
Short Circuit
A short circuit occurs when two points in a circuit that should not be connected are inadvertently touching, creating an unintended path for current flow. Continuity tests can help identify short circuits by checking for continuity between points that should not be connected.
Short circuits can be caused by:
- Damaged insulation on wires, allowing them to touch
- Incorrect wiring or connections
- Conductive debris or contaminants bridging circuit paths
- Faulty components, such as switches or relays
By performing continuity tests and comparing the results with the expected circuit diagram, technicians can identify and resolve short circuits.
Intermittent Faults
Intermittent faults are problems that occur sporadically and can be difficult to diagnose. These faults may be caused by loose connections, damaged components, or environmental factors such as temperature or vibration.
Continuity tests can help identify intermittent faults by checking for continuity under various conditions, such as:
- Moving or flexing wires and connectors
- Applying heat or cold to the circuit
- Subjecting the circuit to vibration or shock
By replicating the conditions that trigger the intermittent fault and performing continuity tests, technicians can isolate the problem and take corrective action.
Safety Precautions during Continuity Testing
While continuity testing is generally safe, it is essential to follow proper safety precautions to avoid potential hazards. Here are some key safety considerations:
-
Disconnect Power: Always ensure that the circuit is not powered during continuity testing. Disconnect any power sources, such as batteries or power adapters, to prevent electric shock or damage to the testing device.
-
Use Appropriate Testing Devices: Choose continuity testing devices that are rated for the voltage and current levels present in the circuit. Using an inappropriate device can lead to inaccurate results or damage to the device or circuit.
-
Wear Personal Protective Equipment (PPE): When working with electrical systems, wear appropriate PPE, such as insulated gloves and safety glasses, to protect against potential electrical hazards.
-
Follow Manufacturer’s Instructions: Adhere to the manufacturer’s instructions and guidelines when using continuity testing devices. Improper use can result in inaccurate readings or damage to the equipment.
-
Avoid Energized Circuits: Never perform continuity tests on energized circuits. If continuity testing is required on a live system, use specialized testing devices designed for live circuit testing and follow appropriate safety protocols.
By prioritizing safety and following proper testing procedures, technicians can minimize the risks associated with continuity testing and ensure accurate and reliable results.
Frequently Asked Questions (FAQ)
-
What is the difference between continuity and resistance?
Continuity and resistance are related but distinct concepts. Continuity refers to the presence of a complete electrical path between two points, allowing current to flow. Resistance, on the other hand, is a measure of the opposition to current flow in a circuit. A circuit with continuity will have a low resistance, while a circuit without continuity will have a high or infinite resistance. -
Can a continuity test be performed on a live circuit?
No, continuity tests should never be performed on live or energized circuits. Doing so can pose serious safety risks, such as electric shock or damage to the testing device. Always disconnect power sources and ensure the circuit is de-energized before conducting a continuity test. -
What should I do if a continuity test indicates no continuity?
If a continuity test indicates no continuity, it suggests that there is a break or interruption in the electrical path. To troubleshoot, start by visually inspecting the circuit for any obvious signs of damage, such as broken wires or loose connections. If no visible issues are found, systematically test for continuity at various points along the circuit to isolate the problem area. Once the fault is located, repair or replace the affected component or wiring. -
Can a multimeter damage a circuit during a continuity test?
When used properly, a multimeter should not damage a circuit during a continuity test. However, using an inappropriate multimeter setting or applying excessive voltage can potentially harm sensitive components. Always ensure that the multimeter is set to the correct continuity testing mode and avoid using high voltage or current settings when testing for continuity. -
How often should continuity tests be performed?
The frequency of continuity tests depends on the specific application and the criticality of the system. In general, continuity tests should be performed whenever there are signs of malfunction, during routine maintenance, or after any modifications or repairs to the electrical system. For critical systems, such as those in aerospace or medical applications, continuity tests may be performed more frequently to ensure the highest level of reliability and safety.
Conclusion
Continuity testing is a crucial technique for verifying the integrity of electrical circuits and troubleshooting faults. By checking for the presence of a complete electrical path between two points, continuity tests help ensure the proper functioning and safety of electrical devices and systems.
Multimeters, continuity testers, and analog ohmmeters are common tools used for continuity testing, each with its own advantages and limitations. When performing a continuity test, it is essential to follow proper procedures, interpret the results accurately, and prioritize safety by disconnecting power sources and using appropriate testing devices.
Continuity tests are valuable for identifying open circuits, short circuits, and intermittent faults, enabling technicians to quickly isolate and resolve problems in electrical systems. By incorporating continuity testing into regular maintenance and troubleshooting routines, technicians can enhance the reliability, performance, and longevity of electrical devices and systems.
As technology continues to advance, the importance of continuity testing remains paramount. Whether working on simple circuits or complex electronic systems, understanding and applying the principles of continuity testing is a fundamental skill for any electrical professional.
Leave a Reply