Introduction to Computer-Aided Manufacturing (CAM)
Computer-Aided Manufacturing (CAM) is a modern manufacturing process that utilizes computer software and hardware to automate and optimize the production of various products. CAM systems are designed to increase efficiency, reduce costs, and improve the quality of manufactured goods by integrating computer technology with traditional manufacturing processes. This technology has revolutionized the manufacturing industry, enabling companies to produce complex parts and components with high precision and speed.
Key Components of CAM Systems
- Computer Numerical Control (CNC) Machines
- CAM Software
- Post-Processing Software
- Simulation and Verification Tools
Automated High-Speed Machining
Automated high-speed machining is a crucial aspect of computer-aided manufacturing that focuses on the rapid and precise production of parts using CNC machines. This process involves the use of advanced cutting tools, high-speed spindles, and sophisticated CAM software to achieve optimal machining performance.
Benefits of Automated High-Speed Machining
- Increased Productivity
- Improved Part Quality
- Reduced Lead Times
- Lower Production Costs
- Enhanced Flexibility
Challenges in Implementing Automated High-Speed Machining
- Initial Investment Costs
- Skilled Workforce Requirements
- Process Planning and Optimization
- Tool and Machine Maintenance
CNC Machines for High-Speed Machining
CNC machines are the backbone of automated high-speed machining processes. These machines are designed to handle the demanding requirements of high-speed cutting operations, such as high spindle speeds, rapid tool changes, and advanced motion control.
Types of CNC Machines for High-Speed Machining
- High-Speed Vertical Machining Centers
- High-Speed Horizontal Machining Centers
- Multi-Axis CNC Machines
- Swiss-Type CNC Lathes
Key Features of High-Speed CNC Machines
- High Spindle Speeds (up to 100,000 RPM)
- Linear Motor Technology for Fast Axis Movements
- Advanced Cooling Systems
- Rigid Machine Structure
- High-Precision Spindles and Bearings
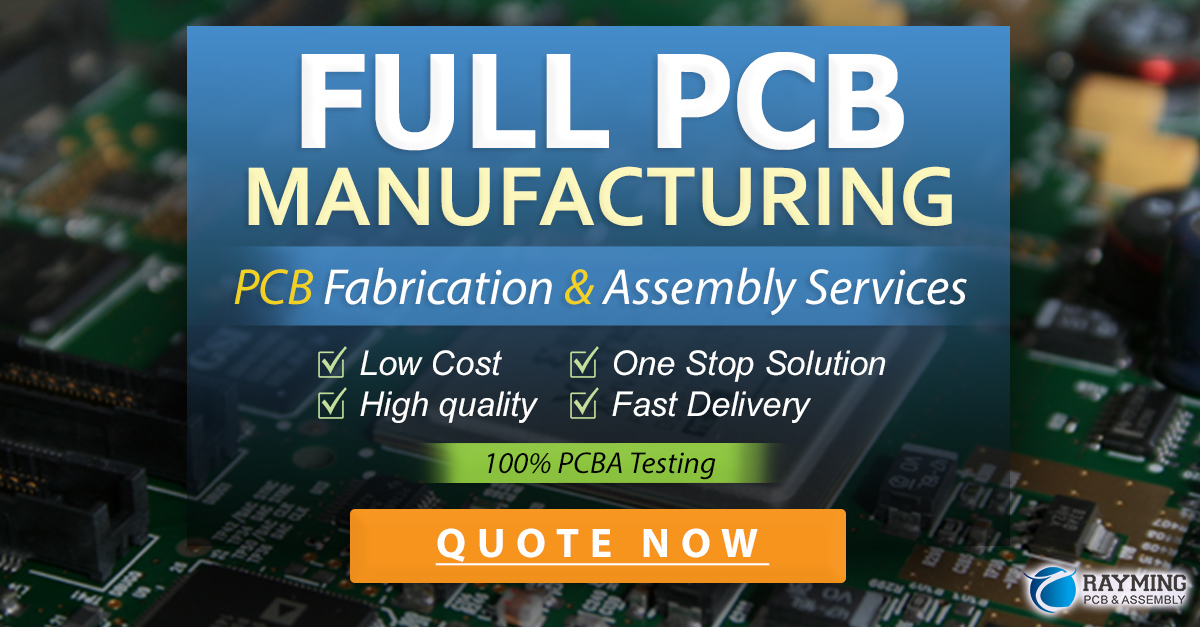
CAM Software for High-Speed Machining
CAM software plays a crucial role in automated high-speed machining by generating efficient toolpaths and optimizing the machining process. These software packages offer advanced features specifically designed for high-speed machining applications.
Popular CAM Software for High-Speed Machining
Software | Manufacturer | Key Features |
---|---|---|
Mastercam | CNC Software, Inc. | Dynamic Motion Technology, High-Speed Toolpaths |
Siemens NX | Siemens PLM Software | Adaptive Milling, High-Speed Machining Templates |
Autodesk PowerMill | Autodesk, Inc. | Vortex High-Efficiency Toolpaths, Collision Avoidance |
ESPRIT | DP Technology Corp. | ProfitMilling, High-Speed Machining Cycles |
Key Features of CAM Software for High-Speed Machining
- High-Speed Toolpath Strategies
- Adaptive Roughing and Finishing
- Trochoidal Milling
- Volumetric Compensation
- Simulation and Verification
Tooling and Workholding for High-Speed Machining
Proper tooling and workholding are essential for successful high-speed machining operations. The selection of cutting tools and workholding devices should be based on the specific requirements of the machining process, such as material properties, part geometry, and desired surface finish.
Cutting Tools for High-Speed Machining
- Solid Carbide End Mills
- Ceramic Cutting Tools
- Polycrystalline Diamond (PCD) Tools
- High-Feed Milling Cutters
- Thread Mills
Workholding Techniques for High-Speed Machining
- Vacuum Chucks
- Hydraulic Clamping Systems
- Magnetic Chucks
- Shrink-Fit Tool Holders
- Collet Chucks
Process Optimization for High-Speed Machining
To achieve the best results in automated high-speed machining, it is essential to optimize the machining process. This involves selecting the appropriate cutting parameters, toolpath strategies, and machine settings based on the specific requirements of the job.
Factors Affecting High-Speed Machining Performance
- Spindle Speed and Feedrate
- Depth of Cut and Width of Cut
- Toolpath Strategy
- Tool Geometry and Coating
- Coolant Application
Optimization Techniques for High-Speed Machining
- Tool Wear Monitoring and Compensation
- Chatter Reduction Strategies
- Thermal Error Compensation
- Vibration Analysis and Control
- Process Simulation and Verification
Applications of Automated High-Speed Machining
Automated high-speed machining is used in various industries to produce a wide range of parts and components. Some of the most common applications include:
- Aerospace Components
- Automotive Parts
- Medical Devices
- Mold and Die Making
- Electronic Components
Case Studies
Case Study 1: Aerospace Component Manufacturing
An aerospace company implemented automated high-speed machining to produce complex titanium parts for jet engines. By utilizing advanced CAM software and high-speed CNC machines, the company achieved:
- 50% reduction in machining time
- 30% reduction in tool wear
- Improved surface finish and part quality
Case Study 2: Automotive Transmission Component Production
An automotive supplier adopted automated high-speed machining to manufacture transmission components. The company invested in multi-axis CNC machines and optimized the machining process using CAM software, resulting in:
- 40% increase in production capacity
- 25% reduction in cycle time
- Reduced scrap rates and improved part consistency
Future Trends in Automated High-Speed Machining
As technology continues to advance, the future of automated high-speed machining looks promising. Some of the emerging trends in this field include:
- Integration of Artificial Intelligence (AI) and Machine Learning (ML)
- Development of Hybrid Manufacturing Processes
- Increased Adoption of Additive Manufacturing Techniques
- Implementation of Industry 4.0 Technologies
- Focus on Sustainable and Eco-Friendly Machining Practices
Conclusion
Automated high-speed machining is a critical component of computer-aided manufacturing that enables companies to produce complex parts with high precision and efficiency. By leveraging advanced CNC machines, CAM software, and process optimization techniques, manufacturers can achieve significant benefits, such as increased productivity, improved part quality, and reduced production costs. As technology continues to evolve, the future of automated high-speed machining looks bright, with the potential for further advancements and innovations in this field.
Frequently Asked Questions (FAQ)
-
What is the difference between conventional machining and high-speed machining?
High-speed machining involves higher spindle speeds, faster feedrates, and more advanced cutting tools compared to conventional machining. This enables faster material removal rates and improved surface finishes. -
What are the key benefits of using CAM software for high-speed machining?
CAM software for high-speed machining offers advanced toolpath strategies, adaptive roughing and finishing techniques, and simulation capabilities that optimize the machining process, reduce cycle times, and improve part quality. -
How does workholding impact high-speed machining performance?
Proper workholding is crucial for high-speed machining to ensure part stability, minimize vibrations, and maintain precision. Advanced workholding techniques, such as vacuum chucks and hydraulic clamping systems, are often used in high-speed machining applications. -
What are some common challenges in implementing automated high-speed machining?
Some of the challenges include high initial investment costs, the need for skilled operators and programmers, process planning and optimization complexities, and increased tool and machine maintenance requirements. -
How can manufacturers optimize the high-speed machining process?
Manufacturers can optimize high-speed machining by selecting appropriate cutting parameters, toolpath strategies, and machine settings based on the specific requirements of the job. Techniques such as tool wear monitoring, chatter reduction, thermal error compensation, and process simulation can further enhance machining performance.
Leave a Reply