Introduction to PCB Electrical Testing
Printed Circuit Boards (PCBs) are the backbone of modern electronics. They are used in almost every electronic device, from smartphones and computers to industrial equipment and aerospace systems. PCBs are designed to interconnect electronic components and provide a stable platform for their operation. To ensure that PCBs function as intended, they must undergo rigorous testing, including electrical testing.
PCB electrical testing is a critical step in the manufacturing process that verifies the electrical integrity of the board. It involves measuring various electrical parameters such as continuity, resistance, capacitance, and inductance to ensure that the PCB meets the required specifications. Electrical testing also helps to identify any defects or issues that may affect the performance or reliability of the PCB.
In this article, we will provide a comprehensive understanding of PCB electrical testing, including its importance, types of tests, equipment used, and best practices.
Why is PCB Electrical Testing Important?
PCB electrical testing is essential for several reasons:
-
Quality Assurance: Electrical testing ensures that the PCB meets the required quality standards and specifications. It helps to identify any defects or issues that may affect the performance or reliability of the PCB.
-
Reliability: PCBs are often used in critical applications where failure can have serious consequences. Electrical testing helps to ensure that the PCB is reliable and will perform as intended under various operating conditions.
-
Cost Savings: Identifying and fixing defects early in the manufacturing process can save significant costs associated with rework, scrap, and warranty claims.
-
Regulatory Compliance: Many industries have specific regulatory requirements for PCBs, including electrical safety and electromagnetic compatibility (EMC). Electrical testing helps to ensure that the PCB meets these requirements.
Types of PCB Electrical Tests
There are several types of electrical tests that can be performed on PCBs, depending on the specific requirements and standards. Some of the most common tests include:
Continuity Test
A continuity test is used to verify that there is a continuous electrical path between two points on the PCB. This test is typically performed using a multimeter or a dedicated continuity tester. The test is performed by measuring the resistance between two points, and if the resistance is below a certain threshold, the path is considered continuous.
Resistance Test
A resistance test is used to measure the resistance between two points on the PCB. This test is typically performed using a multimeter or a dedicated resistance tester. The resistance value is compared to the expected value to ensure that it is within the acceptable range.
Capacitance Test
A capacitance test is used to measure the capacitance between two points on the PCB. This test is typically performed using a dedicated capacitance tester or an LCR meter. The capacitance value is compared to the expected value to ensure that it is within the acceptable range.
Inductance Test
An inductance test is used to measure the inductance between two points on the PCB. This test is typically performed using a dedicated inductance tester or an LCR meter. The inductance value is compared to the expected value to ensure that it is within the acceptable range.
Dielectric Withstanding Voltage (DWV) Test
A DWV test is used to verify that the PCB can withstand a specified voltage without breaking down or arcing. This test is typically performed using a high-voltage tester, and the voltage is applied between the PCB and a ground plane. The test is performed at a specified voltage and duration, and the leakage current is measured to ensure that it is below a certain threshold.
Insulation Resistance (IR) Test
An IR test is used to measure the resistance between two points on the PCB that are separated by an insulating material. This test is typically performed using a high-resistance meter or a megohmmeter. The resistance value is compared to the expected value to ensure that it is above a certain threshold.
Electromagnetic Compatibility (EMC) Test
An EMC test is used to verify that the PCB does not emit electromagnetic interference (EMI) that can affect other electronic devices, and that it is not susceptible to EMI from other devices. This test is typically performed in a specialized EMC test chamber, and the PCB is subjected to various electromagnetic fields and transients to ensure that it meets the required standards.
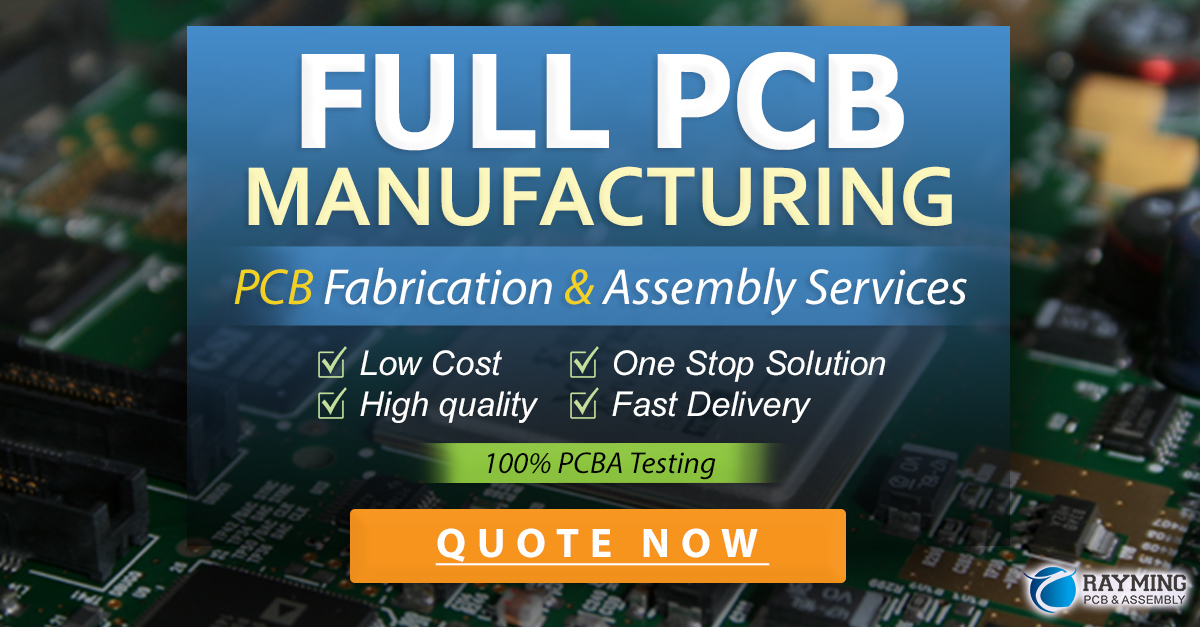
PCB Electrical Testing Equipment
To perform PCB electrical testing, various types of equipment are used, depending on the specific test and requirements. Some of the most common equipment includes:
Multimeter
A multimeter is a versatile instrument that can measure voltage, current, resistance, and continuity. It is commonly used for continuity and resistance tests.
Oscilloscope
An oscilloscope is used to visualize and measure electrical signals over time. It is commonly used for signal integrity testing and debugging.
LCR Meter
An LCR meter is used to measure inductance, capacitance, and resistance. It is commonly used for capacitance and inductance tests.
High-Voltage Tester
A high-voltage tester is used to apply high voltages to the PCB for DWV testing. It typically includes safety features such as interlocks and current limiting.
High-Resistance Meter
A high-resistance meter, also known as a megohmmeter, is used to measure high resistances for IR testing. It typically includes a high-voltage source and a sensitive current meter.
Automated Test Equipment (ATE)
ATE is a specialized system that can perform various electrical tests on PCBs automatically. It typically includes a test fixture that holds the PCB, a switching matrix to connect the test points, and software to control the tests and analyze the results.
Best Practices for PCB Electrical Testing
To ensure accurate and reliable PCB electrical testing, several best practices should be followed:
-
Develop a comprehensive test plan: The test plan should include all the required tests, acceptance criteria, and equipment to be used. It should be reviewed and approved by all stakeholders.
-
Use appropriate test equipment: The test equipment should be selected based on the specific requirements and standards. It should be calibrated and maintained regularly to ensure accuracy and reliability.
-
Follow proper safety procedures: Electrical testing can be hazardous, especially when working with high voltages. Proper safety procedures, such as wearing personal protective equipment (PPE) and using interlocks, should be followed.
-
Use appropriate test fixtures: Test fixtures should be designed to provide reliable and repeatable connections to the PCB. They should be properly maintained and cleaned to prevent contamination.
-
Document test results: Test results should be documented and stored for traceability and analysis. Any issues or defects should be identified and corrected before the PCB is released for production.
FAQs
-
What is the difference between a continuity test and a resistance test?
A continuity test verifies that there is a continuous electrical path between two points, while a resistance test measures the actual resistance value between two points. -
What is the purpose of a dielectric withstanding voltage (DWV) test?
A DWV test verifies that the PCB can withstand a specified voltage without breaking down or arcing. It helps to ensure the electrical safety of the PCB. -
What is the difference between an oscilloscope and a multimeter?
An oscilloscope is used to visualize and measure electrical signals over time, while a multimeter is used to measure voltage, current, resistance, and continuity. -
What is automated test equipment (ATE) used for?
ATE is used to perform various electrical tests on PCBs automatically. It helps to increase the efficiency and reliability of the testing process. -
What safety precautions should be taken during PCB electrical testing?
Proper safety procedures, such as wearing personal protective equipment (PPE) and using interlocks, should be followed. High-voltage testing should only be performed by qualified personnel in a controlled environment.
Conclusion
PCB electrical testing is a critical step in the manufacturing process that ensures the electrical integrity and reliability of the board. It involves various types of tests, equipment, and best practices to verify that the PCB meets the required specifications and standards.
By understanding the importance of PCB electrical testing, the types of tests involved, and the equipment used, manufacturers can ensure that their PCBs are of high quality and will perform as intended in the field. Following best practices such as developing a comprehensive test plan, using appropriate equipment and fixtures, and documenting test results can help to streamline the testing process and catch defects early in the manufacturing process.
As PCBs continue to become more complex and are used in increasingly critical applications, the importance of PCB electrical testing will only continue to grow. By staying up to date with the latest testing methods and technologies, manufacturers can ensure that their PCBs meet the highest standards of quality and reliability.
Leave a Reply