Introduction to Lithium Battery PCBs in Electric Vehicles
The rise of electric vehicles (EVs) has revolutionized the automotive industry, and at the heart of this revolution lies the lithium battery. Lithium batteries have become the preferred choice for EVs due to their high energy density, long life span, and relatively low cost. However, to ensure optimal performance and safety, these batteries require a well-designed printed circuit board (PCB) that can effectively manage and monitor the battery’s operation. In this comprehensive guide, we will dive deep into the world of lithium battery PCBs for electric cars, exploring their design, manufacturing, and key considerations.
The Role of PCBs in Lithium Batteries
Lithium battery PCBs play a crucial role in the overall functioning of the battery pack. These PCBs are responsible for:
-
Battery Management System (BMS): The PCB houses the BMS, which monitors and controls the battery’s charging and discharging processes, ensuring optimal performance and safety.
-
Cell Balancing: The PCB helps to balance the voltage levels across individual battery cells, preventing overcharging or undercharging, which can lead to reduced battery life or even safety hazards.
-
Temperature Monitoring: The PCB includes temperature sensors that continuously monitor the battery’s temperature to prevent overheating and ensure safe operation.
-
Communication: The PCB facilitates communication between the battery pack and the vehicle’s main control unit, exchanging vital information such as battery state of charge (SOC), state of health (SOH), and fault status.
Lithium Battery PCB Design Considerations
Battery Configuration and Voltage
The first step in designing a lithium battery PCB is to determine the battery configuration and voltage requirements. Electric vehicles typically use high-voltage battery packs, ranging from 48V to 800V, depending on the vehicle’s size and performance requirements. The PCB design must accommodate the specific voltage and current ratings of the battery pack.
Component Selection
Selecting the right components for the lithium battery PCB is crucial for ensuring reliable and efficient operation. Key components include:
-
Microcontroller: The microcontroller is the brain of the BMS, responsible for executing the battery management algorithms and communicating with other vehicle systems.
-
Voltage and Current Sensors: These sensors monitor the battery’s voltage and current levels, providing accurate data to the BMS for optimal control.
-
Temperature Sensors: Temperature sensors, such as thermistors or thermocouples, are used to monitor the battery’s temperature and prevent thermal runaway.
-
Power MOSFETs: Power MOSFETs are used for cell balancing and for controlling the charging and discharging processes.
-
Passive Components: Resistors, capacitors, and inductors are used for signal conditioning, filtering, and power management.
PCB Layout and Routing
The PCB layout and routing are critical aspects of lithium battery PCB design. Proper layout and routing help to minimize electromagnetic interference (EMI), reduce signal integrity issues, and ensure optimal thermal management. Key considerations include:
-
Power and Ground Planes: Dedicated power and ground planes help to distribute power evenly across the PCB and reduce voltage drops.
-
Signal Integrity: High-speed signals, such as communication interfaces, require careful routing to minimize crosstalk and signal reflections.
-
Thermal Management: The PCB layout should facilitate efficient heat dissipation, with adequate spacing between components and the use of thermal vias where necessary.
-
EMI Reduction: Proper grounding, shielding, and filtering techniques should be employed to minimize EMI and ensure compliance with automotive electromagnetic compatibility (EMC) standards.
Manufacturing and Assembly
PCB Fabrication
Lithium battery PCBs for electric vehicles are typically manufactured using high-quality, automotive-grade materials to ensure reliability and longevity. The PCB fabrication process involves the following steps:
-
Material Selection: FR-4 is the most common PCB substrate material, but other high-performance materials, such as polyimide or ceramic, may be used for more demanding applications.
-
Copper Etching: The desired circuit pattern is etched onto the copper layers using photolithography and chemical etching processes.
-
Drilling and Plating: Holes are drilled for through-hole components and vias, and the holes are plated with copper to establish electrical connections between layers.
-
Solder Mask and Silkscreen: A solder mask is applied to protect the copper traces from oxidation and prevent short circuits, while a silkscreen layer is added for component labeling and identification.
Component Assembly
Once the PCB fabrication is complete, the components are assembled onto the board using either through-hole or surface-mount technology (SMT). SMT is the more common choice for lithium battery PCBs due to its higher component density and better mechanical stability. The assembly process involves:
-
Solder Paste Application: Solder paste is applied to the PCB pads using a stencil or screen printing process.
-
Component Placement: The components are placed onto the PCB using automated pick-and-place machines or manual placement for larger components.
-
Reflow Soldering: The PCB is heated in a reflow oven, melting the solder paste and forming electrical and mechanical connections between the components and the PCB.
-
Inspection and Testing: The assembLED PCB undergoes visual inspection and electrical testing to ensure proper functionality and adherence to quality standards.
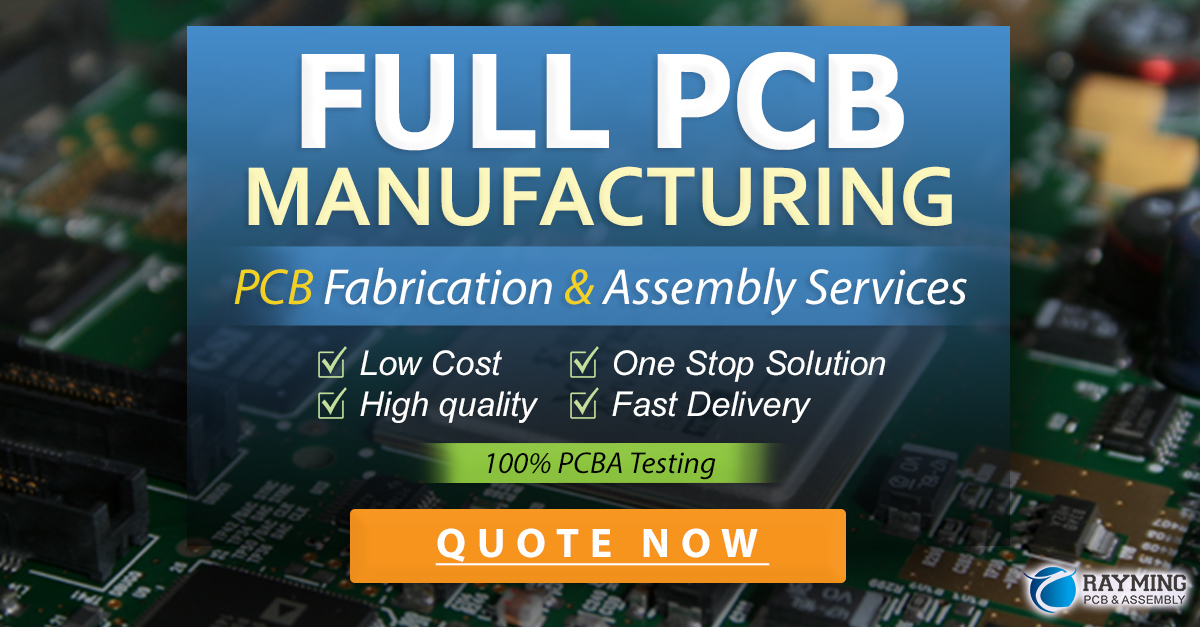
Testing and Validation
Functional Testing
Functional testing is performed to verify that the lithium battery PCB operates as intended. This includes testing the BMS functionality, cell balancing, temperature monitoring, and communication interfaces. Functional testing is typically performed at the PCB level and then again at the battery pack level to ensure seamless integration.
Environmental Testing
Lithium battery PCBs for electric vehicles must be able to withstand harsh environmental conditions, including temperature extremes, vibration, and shock. Environmental testing is conducted to validate the PCB’s performance and reliability under these conditions. Common environmental tests include:
-
Temperature Cycling: The PCB is subjected to alternating high and low-temperature cycles to simulate real-world operating conditions.
-
Vibration and Shock: The PCB is subjected to vibration and shock tests to ensure it can withstand the mechanical stresses encountered in an electric vehicle.
-
Humidity Testing: The PCB is exposed to high humidity levels to assess its resistance to moisture and corrosion.
Safety and Compliance Testing
Safety is paramount in the design and manufacturing of lithium battery PCBs for electric vehicles. The PCBs must comply with various safety standards and regulations, such as:
-
ISO 26262: This standard addresses functional safety in road vehicles and defines the requirements for electrical and electronic systems, including lithium battery PCBs.
-
UN 38.3: This UN standard specifies the testing requirements for lithium batteries to ensure their safety during transport.
-
UL 2580: This standard covers the safety requirements for batteries used in electric vehicles, including the PCBs used in the battery management system.
Safety and compliance testing are conducted to ensure that the lithium battery PCBs meet these standards and do not pose any safety risks during operation.
Future Trends and Developments
As electric vehicles continue to evolve, so too will the lithium battery PCBs that power them. Some of the future trends and developments in this field include:
-
Higher Voltage Systems: The industry is moving towards higher voltage battery packs, such as 800V systems, to increase vehicle range and reduce charging times. This will require PCBs designed to handle higher voltages and currents.
-
Wireless BMS: Wireless battery management systems are being developed to reduce the weight and complexity of wiring harnesses in battery packs. This will require PCBs with integrated wireless communication capabilities.
-
Advanced Materials: New PCB materials, such as ceramic or metal-core substrates, are being explored to improve thermal management and high-voltage performance.
-
Integration with Other Vehicle Systems: Lithium battery PCBs will become more integrated with other vehicle systems, such as the powertrain and thermal management systems, requiring more sophisticated communication and control capabilities.
Frequently Asked Questions (FAQ)
-
Q: What is the difference between a lithium battery PCB and a standard PCB?
A: Lithium battery PCBs are specifically designed for use in battery management systems for lithium batteries. They include specialized components and features, such as voltage and temperature sensors, cell balancing circuits, and high-voltage protection, that are not typically found on standard PCBs. -
Q: Why are lithium battery PCBs important for electric vehicles?
A: Lithium battery PCBs are crucial for ensuring the safe and efficient operation of the high-voltage battery packs used in electric vehicles. They monitor and control the charging and discharging processes, balance the voltage levels across individual cells, and protect the battery from overheating or other hazardous conditions. -
Q: What are the key design considerations for lithium battery PCBs?
A: Key design considerations include selecting the appropriate battery configuration and voltage, choosing the right components for reliable and efficient operation, optimizing the PCB layout and routing for signal integrity and thermal management, and ensuring compliance with automotive safety and EMC standards. -
Q: What are the manufacturing and assembly processes for lithium battery PCBs?
A: Lithium battery PCBs are typically manufactured using high-quality, automotive-grade materials and processes, such as FR-4 substrate, copper etching, and solder mask application. The components are then assembled onto the PCB using surface-mount technology (SMT) and reflow soldering, followed by inspection and testing. -
Q: What are some of the future trends and developments in lithium battery PCBs for electric vehicles?
A: Future trends and developments include higher voltage systems (e.g., 800V), wireless battery management systems, advanced materials for improved thermal management and high-voltage performance, and greater integration with other vehicle systems.
Conclusion
Lithium battery PCBs are a critical component in the development and advancement of electric vehicles. By providing reliable and efficient battery management, these PCBs ensure the safe and optimal performance of high-voltage lithium battery packs. As the demand for electric vehicles continues to grow, so too will the need for well-designed and manufactured lithium battery PCBs.
This comprehensive guide has covered the key aspects of lithium battery PCBs for electric cars, including their role in the battery system, design considerations, manufacturing and assembly processes, testing and validation, and future trends and developments. By understanding these factors, engineers and manufacturers can develop lithium battery PCBs that meet the stringent requirements of the automotive industry and contribute to the ongoing revolution in electric mobility.
Leave a Reply