Understanding the Importance of Circuit Board Drilling
Circuit board drilling is a fundamental step in the PCB manufacturing process. It involves creating holes in the PCB substrate to accommodate various components, such as through-hole components, vias, and mounting holes. The accuracy and precision of the drilling process directly impact the overall quality and functionality of the finished PCB.
Key Benefits of Precise Circuit Board Drilling
- Ensures proper component placement
- Facilitates accurate electrical connections
- Enhances mechanical stability of the PCB
- Improves overall reliability and performance
Drill Bit Selection for Circuit Board Drilling
Choosing the right drill bit is essential for achieving optimal results in circuit board drilling. Several factors need to be considered when selecting drill bits, including material compatibility, hole size, and drilling speed.
Common Drill Bit Materials
Material | Characteristics | Applications |
---|---|---|
Carbide | High hardness, wear-resistant | High-volume production, hard materials |
High-Speed Steel (HSS) | Good balance of hardness and toughness | General-purpose drilling, softer materials |
Diamond-Coated | Extreme hardness, long tool life | Abrasive materials, high-precision drilling |
Choosing the Right Drill Bit Size
The drill bit size should be selected based on the desired hole diameter and the tolerance requirements of the PCB design. It is important to consider the following factors:
- Component lead diameter
- Via size
- Plated through-hole (PTH) requirements
- Mounting hole specifications
Drilling Techniques for Circuit Boards
To achieve high-quality holes in circuit boards, proper drilling techniques must be employed. This section will cover the key aspects of drilling techniques, including feed rates, spindle speeds, and drill bit maintenance.
Setting the Optimal Feed Rate
The feed rate, or the speed at which the drill bit advances into the PCB material, plays a crucial role in the drilling process. The optimal feed rate depends on several factors, such as:
- Drill bit material and size
- PCB material and thickness
- Desired hole quality
A general guideline for setting the feed rate is to start with the manufacturer’s recommendations and fine-tune based on the specific application and desired results.
Spindle Speed Considerations
Spindle speed, or the rotational speed of the drill bit, is another critical parameter in circuit board drilling. The appropriate spindle speed depends on the drill bit diameter, material, and the desired hole quality. Higher spindle speeds are generally used for smaller drill bits, while lower speeds are employed for larger bits.
Drill Bit Diameter (mm) | Spindle Speed Range (RPM) |
---|---|
0.2 – 0.5 | 60,000 – 100,000 |
0.5 – 1.0 | 30,000 – 60,000 |
1.0 – 2.0 | 20,000 – 30,000 |
2.0 – 3.0 | 10,000 – 20,000 |
Drill Bit Maintenance and Replacement
Regular maintenance and timely replacement of drill bits are essential for maintaining the quality and efficiency of the circuit board drilling process. Some key practices include:
- Inspecting drill bits for wear and damage
- Cleaning and lubricating drill bits periodically
- Replacing drill bits when they reach the end of their usable life
- Proper storage and handling of drill bits
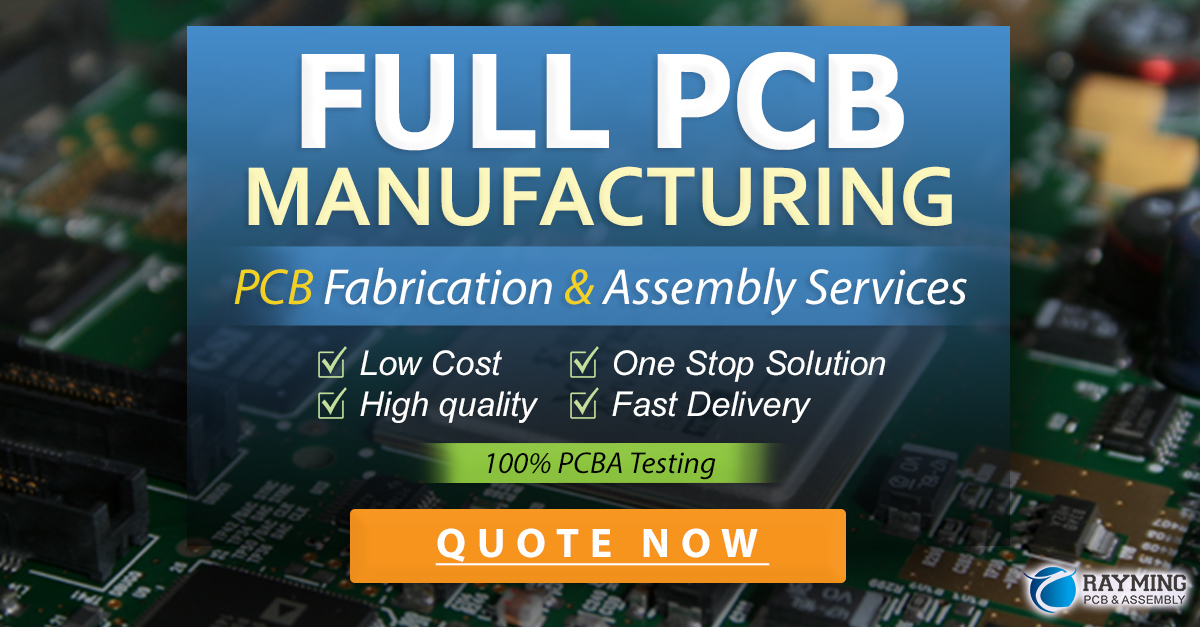
Drilling Accuracy and Precision
Achieving high levels of accuracy and precision is paramount in circuit board drilling. This section will discuss the factors that influence drilling accuracy and precision, as well as techniques for improving these critical aspects.
Factors Affecting Drilling Accuracy and Precision
Several factors can impact the accuracy and precision of circuit board drilling, including:
- Drill bit quality and condition
- Machine spindle runout and vibration
- PCB material properties and thickness variations
- Drill bit alignment and positioning
Techniques for Improving Drilling Accuracy and Precision
To enhance the accuracy and precision of circuit board drilling, consider implementing the following techniques:
- Use high-quality, well-maintained drill bits
- Regularly calibrate and maintain drilling equipment
- Employ precise drill bit alignment and positioning systems
- Implement robust quality control and inspection processes
Troubleshooting Common Circuit Board Drilling Issues
Despite best efforts, issues may arise during the circuit board drilling process. This section will cover common problems encountered and provide troubleshooting tips to resolve them.
Burrs and Rough Hole Edges
Burrs and rough hole edges can occur due to improper drilling parameters or worn drill bits. To minimize these issues:
- Adjust feed rates and spindle speeds
- Replace worn or damaged drill bits
- Implement proper chip evacuation techniques
Hole Misalignment and Positioning Errors
Hole misalignment and positioning errors can lead to component fitting issues and electrical failures. To address these problems:
- Verify drill bit alignment and positioning system accuracy
- Ensure proper PCB fixturing and support
- Implement robust quality control and inspection processes
Drill Bit Breakage and Premature Wear
Drill bit breakage and premature wear can disrupt production and lead to costly downtime. To mitigate these issues:
- Use appropriate drill bit materials and sizes for the application
- Implement proper drilling parameters and techniques
- Perform regular drill bit maintenance and replacement
Best Practices for Efficient Circuit Board Drilling
To optimize the efficiency and quality of the circuit board drilling process, consider adopting the following best practices:
- Standardize drilling parameters and procedures
- Implement a robust preventive maintenance program
- Train operators on proper drilling techniques and troubleshooting
- Continuously monitor and analyze drilling performance metrics
- Invest in high-quality drilling equipment and consumables
Frequently Asked Questions (FAQ)
-
What is the most common drill bit material used for circuit board drilling?
Carbide is the most common drill bit material used for circuit board drilling due to its high hardness and wear resistance, making it suitable for high-volume production and drilling hard materials. -
How often should I replace my drill bits?
The frequency of drill bit replacement depends on several factors, such as the material being drilled, drilling parameters, and the desired hole quality. As a general rule, replace drill bits when they show signs of wear, damage, or when hole quality begins to deteriorate. -
What is the optimal spindle speed for drilling a 1.0 mm hole in a PCB?
For drilling a 1.0 mm hole in a PCB, the recommended spindle speed range is typically between 30,000 and 60,000 RPM. However, the exact spindle speed should be determined based on the specific drill bit material, PCB material, and desired hole quality. -
How can I minimize burrs and rough hole edges in my drilled PCBs?
To minimize burrs and rough hole edges, ensure that you are using sharp, well-maintained drill bits and employing appropriate drilling parameters, such as feed rates and spindle speeds. Additionally, implement proper chip evacuation techniques to prevent the accumulation of debris around the hole edges. -
What are some key factors to consider when selecting drill bits for circuit board drilling?
When selecting drill bits for circuit board drilling, consider the following key factors: - Material compatibility (e.g., carbide for hard materials, HSS for softer materials)
- Hole size and tolerance requirements
- Drilling speed and feed rate capabilities
- Expected tool life and cost-effectiveness
By understanding the importance of circuit board drilling, selecting the right drill bits, employing proper drilling techniques, and implementing best practices, you can ensure the production of high-quality, reliable PCBs. Regular maintenance, troubleshooting, and continuous improvement will help optimize your drilling process and maintain a competitive edge in the PCB manufacturing industry.
Leave a Reply