Introduction to Ceramic PCBs
Ceramic printed circuit boards (PCBs) are a specialized type of PCB that offer unique properties and benefits compared to traditional FR-4 fiberGlass PCBs. Made from ceramic materials like alumina or aluminum nitride, ceramic PCBs provide excellent thermal conductivity, electrical insulation, and mechanical stability. In 2023, ceramic PCBs are becoming increasingly popular for applications that demand high performance, reliability, and customization.
In this ultimate guide, we’ll dive deep into the world of ceramic PCBs. We’ll explore their advantages, applications, manufacturing process, design considerations, and more. Whether you’re an electrical engineer, PCB designer, or technology enthusiast, this article will provide you with valuable insights into the exciting realm of ceramic PCBs.
Advantages of Ceramic PCBs
1. Excellent Thermal Conductivity
One of the key advantages of ceramic PCBs is their outstanding thermal conductivity. Ceramic materials like alumina have a thermal conductivity of around 20-30 W/mK, which is significantly higher than FR-4 (0.3 W/mK). This means that ceramic PCBs can efficiently dissipate heat generated by electronic components, preventing overheating and thermal stress.
2. High Electrical Insulation
Ceramic PCBs offer excellent electrical insulation properties. With a dielectric strength of over 20 kV/mm, ceramic materials provide superior insulation compared to FR-4 (20-50 kV/mm). This makes ceramic PCBs ideal for high-voltage applications where electrical isolation is critical.
3. Dimensional Stability
Ceramic materials have a low coefficient of thermal expansion (CTE), which means they maintain their dimensions even under extreme temperature changes. This dimensional stability is crucial for applications that require precise component placement and alignment, such as high-frequency circuits and optoelectronics.
4. Mechanical Strength
Ceramic PCBs exhibit excellent mechanical strength and rigidity. They can withstand high levels of stress and vibration without cracking or breaking. This robustness makes them suitable for harsh environments and applications that demand long-term reliability.
5. Customization Options
Ceramic PCBs offer a wide range of customization options. They can be manufactured in various shapes, sizes, and thicknesses to meet specific design requirements. Additionally, ceramic PCBs can incorporate embedded components, cavities, and 3D structures, enabling highly integrated and compact designs.
Applications of Ceramic PCBs
1. High-Power Electronics
Ceramic PCBs are widely used in high-power electronic applications, such as power converters, motor drives, and renewable energy systems. Their excellent thermal conductivity allows for efficient heat dissipation, enabling higher power densities and improved system performance.
2. RF and Microwave Circuits
Ceramic PCBs are well-suited for high-frequency applications, such as RF and microwave circuits. The low dielectric constant and low loss tangent of ceramic materials minimize signal distortion and attenuation, ensuring high signal integrity and low noise.
3. Optoelectronics
Ceramic PCBs find applications in optoelectronic devices, such as laser diodes, photodetectors, and fiber optic modules. The dimensional stability and thermal conductivity of ceramic PCBs enable precise alignment and efficient heat management, which are crucial for optical performance.
4. Automotive Electronics
Ceramic PCBs are used in automotive electronics, especially in high-temperature and high-reliability applications. They can withstand the harsh operating conditions found in automotive environments, such as extreme temperatures, vibrations, and chemical exposure.
5. Aerospace and Defense
Ceramic PCBs are employed in aerospace and defense systems that require high reliability and performance under extreme conditions. They are used in radar systems, satellite communications, avionics, and military electronics.
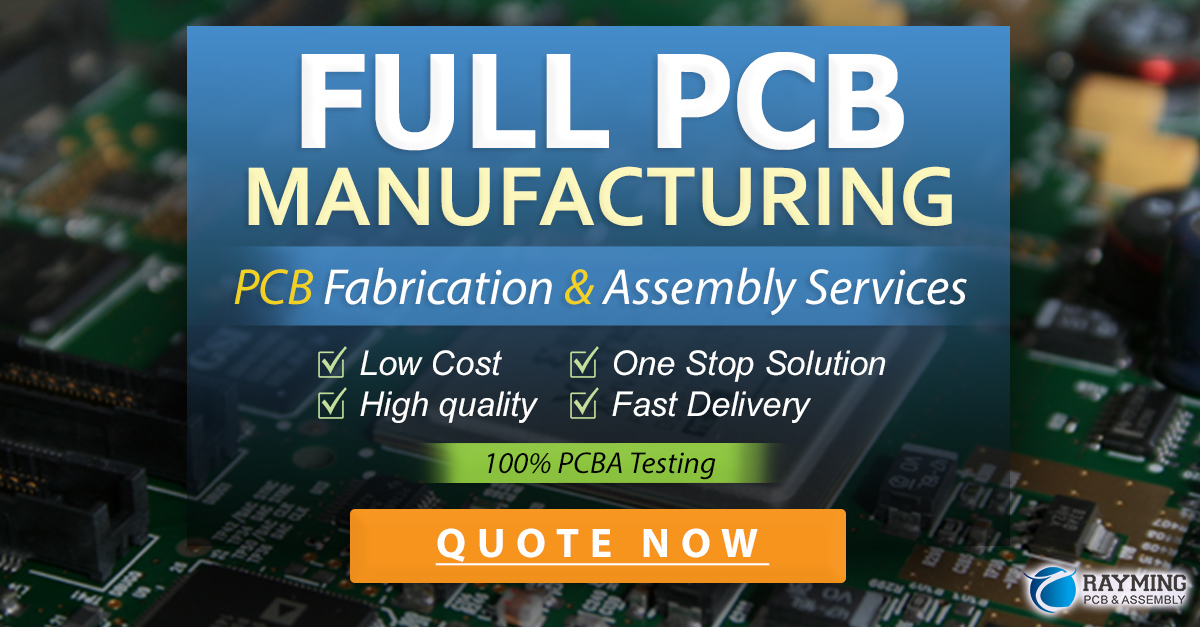
Manufacturing Process of Ceramic PCBs
The manufacturing process of ceramic PCBs differs from that of traditional FR-4 PCBs. Here’s an overview of the key steps involved:
1. Ceramic Substrate Preparation
The ceramic substrate, typically alumina or aluminum nitride, is prepared by mixing ceramic powders with binders and additives. The mixture is then formed into the desired shape using techniques like pressing, casting, or tape casting.
2. Via Formation
Vias, which are conductive pathways that connect different layers of the PCB, are formed in the ceramic substrate. This can be done through mechanical drilling, laser drilling, or co-firing techniques.
3. Metallization
The ceramic substrate is metallized to create conductive traces and pads. Common metallization techniques include screen printing, sputtering, and electroplating. Conductive materials like copper, gold, or silver are used for metallization.
4. Patterning
The metallized layers are patterned to create the desired circuit layout. This is typically done using photolithography, where a photoresist is applied, exposed to light through a mask, and developed to create the desired pattern.
5. Multilayer Lamination
For multilayer ceramic PCBs, multiple ceramic layers with patterned metallization are stacked and laminated together under high pressure and temperature. This process creates a solid, monolithic structure.
6. Firing
The laminated ceramic PCB undergoes a high-temperature firing process, typically above 1500°C. During firing, the ceramic substrate densifies, and the metal layers form strong bonds with the ceramic.
7. Surface Finishing
After firing, the ceramic PCB undergoes surface finishing processes to improve solderability, corrosion resistance, and aesthetics. Common surface finishes include nickel/gold plating, silver plating, and solder mask application.
8. Singulation
Finally, the ceramic PCB panel is singulated into individual boards using techniques like dicing or lasering. The boards are then inspected for quality and packaged for shipment.
Manufacturing Step | Description |
---|---|
Ceramic Substrate Preparation | Mixing ceramic powders, forming into desired shape |
Via Formation | Creating conductive pathways through drilling or co-firing |
Metallization | Applying conductive materials (copper, gold, silver) |
Patterning | Creating circuit layout using photolithography |
Multilayer Lamination | Stacking and laminating multiple ceramic layers |
Firing | High-temperature densification and metal bonding |
Surface Finishing | Improving solderability, corrosion resistance, aesthetics |
Singulation | Cutting the panel into individual boards |
Design Considerations for Ceramic PCBs
When designing ceramic PCBs, several key considerations should be taken into account:
1. Material Selection
Choosing the appropriate ceramic material is crucial based on the application requirements. Alumina is commonly used for its good thermal conductivity and mechanical strength, while aluminum nitride offers even higher thermal conductivity but at a higher cost.
2. Via Formation
The via formation technique should be selected based on the desired via size, aspect ratio, and manufacturing constraints. Mechanical drilling, laser drilling, and co-firing are common options, each with their own advantages and limitations.
3. Metallization Compatibility
The metallization process should be compatible with the chosen ceramic material and the desired circuit performance. Factors like adhesion strength, conductivity, and thermal stability should be considered when selecting the metallization technique and materials.
4. Thermal Management
Proper thermal management is essential for ceramic PCBs to ensure reliable operation and long-term performance. This includes optimizing the layout for heat dissipation, using thermal vias, and incorporating heat sinks or cooling solutions when necessary.
5. Coefficient of Thermal Expansion (CTE) Mismatch
The CTE mismatch between the ceramic substrate and the mounted components should be carefully managed to avoid thermal stresses and reliability issues. Techniques like using compliant interconnects or underfilling can help mitigate CTE mismatch.
6. High-Frequency Considerations
For high-frequency applications, the dielectric properties of the ceramic material should be carefully selected to minimize signal loss and distortion. The layout should also be optimized for impedance control and signal integrity.
7. Manufacturing Tolerances
Ceramic PCBs have tighter manufacturing tolerances compared to FR-4 PCBs due to the high-temperature firing process. Designers should work closely with the manufacturer to ensure that the design is manufacturable and meets the required tolerances.
Frequently Asked Questions (FAQ)
1. What are the main advantages of ceramic PCBs over traditional FR-4 PCBs?
Ceramic PCBs offer several advantages over FR-4 PCBs, including excellent thermal conductivity, high electrical insulation, dimensional stability, mechanical strength, and customization options. These properties make ceramic PCBs suitable for high-performance applications that demand reliability and performance.
2. What are the common applications of ceramic PCBs?
Ceramic PCBs find applications in various industries, including high-power electronics, RF and microwave circuits, optoelectronics, automotive electronics, aerospace, and defense. They are particularly well-suited for applications that require efficient heat dissipation, high-frequency performance, and reliability in harsh environments.
3. How does the manufacturing process of ceramic PCBs differ from traditional PCBs?
The manufacturing process of ceramic PCBs involves additional steps compared to traditional PCBs. Key differences include the preparation of the ceramic substrate, via formation techniques, high-temperature firing, and the need for tighter manufacturing tolerances. The process also requires specialized equipment and expertise.
4. What are the key design considerations for ceramic PCBs?
When designing ceramic PCBs, important considerations include material selection, via formation technique, metallization compatibility, thermal management, CTE mismatch, high-frequency performance, and manufacturing tolerances. Designers should work closely with the manufacturer to ensure a robust and manufacturable design.
5. Are ceramic PCBs more expensive than traditional PCBs?
Yes, ceramic PCBs are generally more expensive than traditional FR-4 PCBs due to the specialized materials, manufacturing processes, and expertise required. However, the higher cost is often justified for applications that demand the unique properties and performance advantages offered by ceramic PCBs.
Conclusion
Ceramic PCBs are a game-changer in the world of printed circuit boards, offering unparalleled performance, reliability, and customization options. With their excellent thermal conductivity, electrical insulation, dimensional stability, and mechanical strength, ceramic PCBs are becoming increasingly popular in 2023 for demanding applications across various industries.
As technology continues to advance, the demand for high-performance electronics will only grow. Ceramic PCBs are well-positioned to meet these challenges, enabling the development of cutting-edge products that push the boundaries of innovation.
By understanding the advantages, applications, manufacturing process, and design considerations of ceramic PCBs, engineers and designers can leverage this technology to create truly remarkable electronic devices. Whether it’s in power electronics, RF circuits, optoelectronics, or aerospace systems, ceramic PCBs offer a platform for unmatched performance and reliability.
As we look ahead to the future of electronics, ceramic PCBs will undoubtedly play a crucial role in shaping the landscape. With their unique properties and customization options, they offer a path towards more compact, efficient, and robust electronic systems.
So, if you’re looking to take your electronic designs to the next level in 2023 and beyond, consider the power and potential of ceramic PCBs. With the right knowledge, tools, and collaboration with experienced manufacturers, you can unlock a world of possibilities and create electronic marvels that stand the test of time.
Leave a Reply