What are PCB Castellations?
PCB castellations are plated half-circle cutouts or slots along the edge of a printed circuit board (PCB). The term “castellation” comes from their resemblance to the turrets and battlements on the top of a castle wall.
Castellations serve as a connection point for plugging the PCB perpendicularly into a socket or edge connector, or for soldering the PCB at a right angle to another PCB. This allows PCBs to be connected together to form larger systems.
Types of PCB Castellations
There are two main types of castellations:
Type | Description |
---|---|
Half-circle | Semicircular cutouts along the PCB edge with plated holes |
Rectangular slot | Oblong holes cut into the PCB edge with plating inside |
Half-circle castellations are the traditional and more common type. The slots provide more contact area for a stronger mechanical and electrical connection.
Castellation Dimensions
The size and spacing of castellations is standardized so PCBs can plug into standard sockets and connectors.
Common castellation dimensions for 1.6mm thick boards:
Dimension | Imperial | Metric |
---|---|---|
Drill diameter | 0.040″ | 1.02mm |
Pad diameter | 0.080″ | 2.03mm |
Hole-to-hole spacing | 0.100″ | 2.54mm |
Board edge to hole center | 0.050″ | 1.27mm |
The plating inside the holes is typically 1-2 oz copper with tin-lead or gold finish.
Advantages of Using Castellations
Board-to-Board Connections
The primary use of castellations is for board-to-board connections. By plugging castellated boards perpendicularly into each other, larger systems can be assembled from multiple smaller PCBs.
Some common applications:
- Plugging a module or add-on board into a base board
- Stacking multiple identical PCBs to increase functionality
- Edge connecting boards at right angles to fit in an enclosure
- Connecting boards in a backplane configuration
Compared to other board-to-board connection methods like pin headers or edge connectors, castellations have several advantages:
- No extra parts required – castellations are part of the PCB
- Takes up less board space – castellations are on the PCB edge
- Lower profile – boards can sit flush against each other
- More secure connection – soldered castellations are very robust
Perpendicular Mounting
Another advantage of castellations is they allow a smaller PCB to be soldered perpendicularly onto a larger carrier board, sometimes called a motherboard.
This 90-degree mounting is useful for:
- Reducing the footprint taken up by the daughterboard
- Positioning boards vertically to optimize use of enclosure space
- Orienting displays, indicators or connectors in different directions
- Keeping sensitive circuits away from interference on the main board
Compared to other perpendicular mounting methods like pin headers, castellations provide a lower profile, more stable connection.
How to Design Castellations
PCB Layout
The first step is to lay out the castellation pads along the edge of the PCB in your PCB design software. The pads should be spaced according to the dimensions given earlier.
It’s important to adhere to the standard dimensions to ensure compatibility with standard sockets and connectors. Also pay attention to the number of castellations and the board thickness required by the mating connector.
The pads are typically oval shaped and extend about 2/3 the diameter beyond the board edge:
Soldermask is removed from the pads and the board edge to allow soldering. The board outline is drawn cutting through the center of the pads:
Ensure there is clearance between the castellations and any components, traces or vias on the PCB.
Panelization
Castellated PCBs are usually panelized together for more efficient assembly. Panelization is combining multiple copies of the board into a larger array that can be processed and tested as a single unit.
The castellations are not cut out in the panelized PCB. Instead, the full circles are drilled through at the castellation locations and plating is applied:
V-score lines are added between the boards so the panel can be snapped apart after assembly. When depanelized, the circular holes are cut in half, forming the castellated edges on the individual boards.
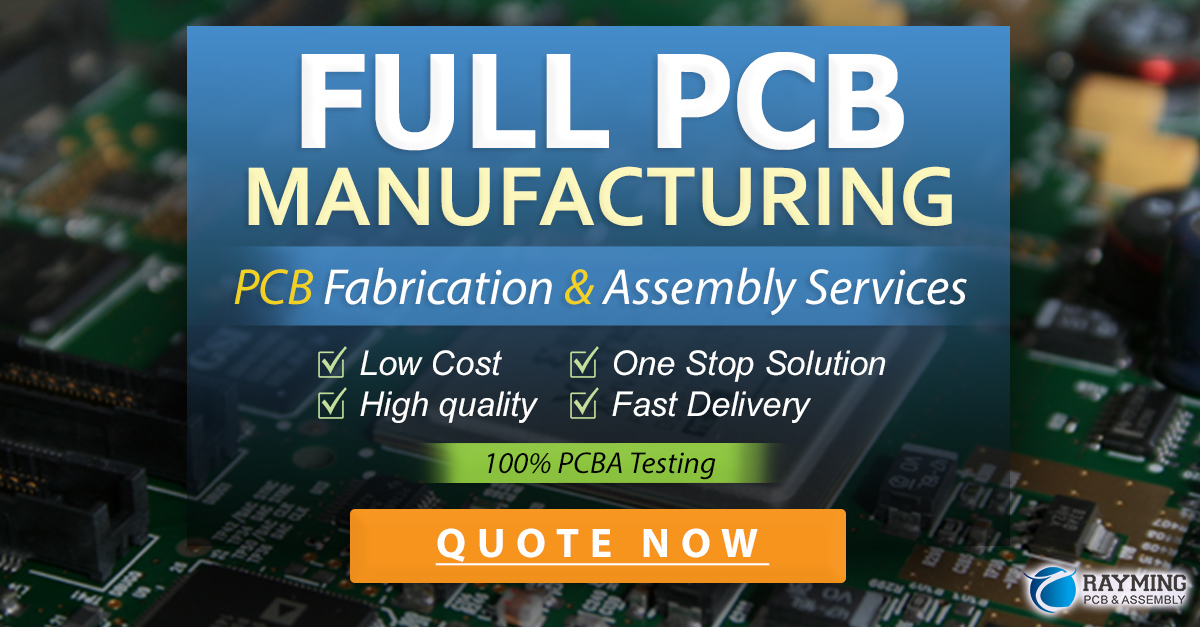
FAQ
What is the difference between castellations and vias?
Castellations and vias are both plated holes in a PCB, but they serve different purposes:
- Vias are used to connect traces between layers within a PCB
- Castellations are used to connect one PCB to another PCB
Vias are fully internal to the PCB while castellations are cut in half to form slots along the board edge. Castellations also have standardized dimensions to mate with sockets.
Can castellations be used for SMT components?
No, surface mount (SMT) components cannot be soldered to castellations. Castellations are plated slots along the edge of the board while SMT pads are on the surface of the board away from the edge.
However, castellations can be used to solder a castellated module perpendicularly to SMT pads on a carrier board. The module’s castellations are inserted through holes in the carrier board and soldered to SMT pads surrounding those holes.
How strong are soldered castellations?
A soldered castellation makes a very strong mechanical connection. The plating in the castellation slots has a relatively large surface area contacting the solder on the mating surface.
For even more strength, a slot castellation can be used instead of half-circles. The extra contact area inside the slots provides an even more robust solder joint.
What materials can be used for castellations?
The core PCB material for castellations is usually standard FR-4 glass-reinforced epoxy. Higher-performance materials like polyimide or ceramic can also be used.
The plating is typically 1-2 oz copper with a tin-lead (HASL) or electroless nickel immersion gold (ENIG) surface finish.
What are the limitations of castellations?
Castellations have a few limitations and drawbacks compared to other connection methods:
- Limited I/O density – a PCB edge has a limited length for castellations
- Large footprint – castellations require perimeter space on the PCB
- No cable connections – castellations are only for board-to-board
- Not repairable – soldered castellations are difficult to rework
- Extra cost – castellations require additional PCB fabrication steps
So castellations are not suitable for every application. High-density, high-flexibility or low-cost designs may be better off using pin headers, card-edge fingers or direct soldering.
Leave a Reply