Introduction
Capacitive touch sensing has become ubiquitous in consumer electronics and industrial controls. Embedded touch buttons and touchscreens based on capacitive sensing allow for sleek, durable and intuitive human-machine interfaces. Flexible printed circuit boards (flex PCBs) have emerged as the ideal substrate for implementing capacitive touch sensors and interfaces due to their thin, lightweight and conformal nature.
This article provides an overview of capacitive touch flex PCB technology. We will cover the operating principles, design considerations, manufacturing processes and applications of capacitive touch flex PCBs. By the end of this article, you should have a solid understanding of this fascinating and enabling technology.
How Do Capacitive Touch Flex PCBs Work?
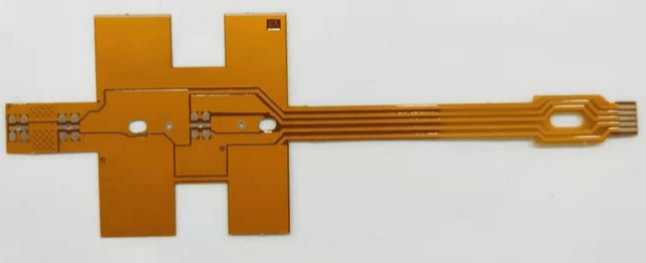
Capacitive touch sensing relies on measuring changes in capacitance caused by a user’s finger. The finger acts as a virtual ground, increasing the capacitance between the touch pad and finger. This change in capacitance is measured by the touch controller to detect touch events.
On a capacitive touch flex PCB, conductive touch pads are printed on the flex circuit substrate. The touch pads form one plate of the capacitor, while the finger forms the second plate. An electric field develops between the finger and pad. More electric field lines appear when a finger touches the pad, increasing its capacitance.
The flex PCB tracks route the touch signals to a capacitive touch controller chip. The touch controller scans the touch pads, measuring their capacitance. It generates a digital activation signal when it detects a threshold increase in capacitance. The controller chip communicates the touch data to a host microcontroller over an interface like I2C or SPI.
Capacitive Touch Flex PCB Design Considerations
Several factors must be considered when designing a capacitive touch interface on a flex PCB:
Sensor Patterning
The size, shape and spacing of the capacitive touch pads impacts sensitivity and accuracy. Larger pads offer higher sensitivity but lower touch point resolution. A fine pitch array offers high resolution but may miss narrow touches. Inter-pad spacing must exceed 2-3mm to prevent false touches. Individual optimization is needed based on touch accuracy requirements.
Flex Circuit Layout
The flex PCB conductive layers are patterned to create the touch pads and interconnect traces. Minimizing trace length improves touch signal integrity. Vias can connect top and bottom layer traces. The flex circuit layout must avoid overlap between touch pads and traces to prevent reduced sensitivity and crosstalk.
Grounding
A system ground plane helps shield the capacitive touch signals from external noise. Individual touch pads can be surrounded by ground traces for localized shielding. Proper grounding is key for reliable capacitive touch performance.
Touch Controller Selection
The touch controller scans the touch pads, sets detection thresholds and handles touch data processing. Important parameters are number of sensing channels, sensitivity, response time and interface compatibility with the host processor. High performance controllers allow advanced features like water rejection, gloved touch sensing and multi-touch detection.
Capacitive Touch Flex PCB Manufacturing Process
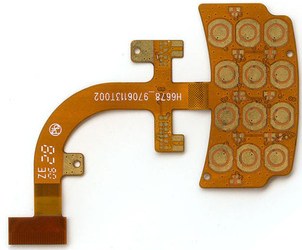
Capacitive touch flex PCBs are manufactured using the following standard processes:
Flex PCB Fabrication
The base flex circuit substrate is a thin, flexible polyimide film. The Cu conductive layers are deposited on the polyimide film using sputtering or plating. Photolithography patterns the conductive layers into circuit traces and touch pads. Flex circuit fabrication allows very fine trace widths and spacing down to 50 microns.
Touch Controller Embedding
The capacitive touch controller IC is mounted onto the flex PCB using surface mount technology (SMT). High precision pick-and-place machines position the tiny controller chip onto PCB pads. Reflow soldering bonds the chip to the pads. The chip is encapsulated with epoxy for protection.
Lamination
The fabricated flex circuit is often laminated with a transparent polyester or PET film overlay. The overlay protects the circuitry and provides a durable touch surface. Lamination uses adhesive films to bond the overlay to the flex circuit.
Testing
Electrical testing validates the continuity and functioning of the touch pads, traces and connections. Optical inspection checks for defects. Parameter testing confirms the sensitivity, accuracy and speed of the capacitive touch interface. End-of-line testing ensures reliable performance.
Assembly
The completed capacitive touch flex PCB assemblies are installed into devices using mechanical mounting or Z-axis tape. Electrical interfaces connect the touch controller to the main PCB. The thin, flexible circuits can fit into tight spaces and fold into complex shapes.
Capacitive Touch Flex PCB Applications
With their versatility and reliability, capacitive touch flex PCBs are found in many cutting-edge applications:
Consumer Electronics
Button overlays, touchpads and touchscreens on smartphones, tablets, wearables and home appliances use capacitive sensing flex circuits for their sleek and compact form factors. Flex circuits conform to curved surfaces and small spaces.
Industrial Control Panels
Rugged human-machine interfaces based on flexible capacitive touch PCBs withstand harsh industrial environments. Flex circuits integrate well into machines and cabinets due to their thin profile.
Medical Devices
Medical monitors, imaging systems and assistive devices employ contamination-resistant capacitive touchscreens on flex circuits. Smooth, wipeable surfaces enable sanitization between patients.
Automotive Interiors
Cars integrate dashboards, center consoles and seat controls built using flexible capacitive touch PCBs. The automotive-grade circuits withstand vibration, temperature extremes and wear over long service lives.
Consumer Appliances
White goods like washing machines, microwaves and coffee makers use ultra-thin capacitive touch flex PCBs on their control panels. Sleek exterior designs and easy-to-clean surfaces are enabled by flexible circuits.
Future Outlook
Several technology and market trends point toward expanded applications for capacitive touch flex PCBs:
- Increasing adoption of touch interfaces across all devices due to their intuitive, natural feel
- More consumer products with curved and irregular surfaces needing thin, conformal touch sensors
- High-resolution flexible touch displays and touchpads for next-generation wearables and mobiles
- Industrial automation requiring thinner, more reliable and customized touch interfaces
- Medical devices calling for antimicrobial, washable yet sensitive touch surfaces
Advances in conductive inks, substrates and controllers will also enhance performance and capabilities. The unique benefits of flexible printed circuits provide a robust foundation for capacitive touch interfaces to become more ubiquitous moving forward.
Frequently Asked Questions
Here are some common FAQs about capacitive touch flex PCB technology:
What are the main advantages of capacitive touch flex PCBs versus rigid PCBs?
Flex PCBs offer thin, lightweight and bendable circuits that conform to challenging mechanical requirements. This allows integration into tight, curved spaces and devices with irregular shapes or surfaces. The flexible circuits are also more durable to vibration, impacts and flexing stresses.
How do capacitive touchscreens work?
Capacitive touchscreens consist of a matrix of transparent conductive rectangles or diamonds printed on an insulating substrate forming a grid-like sensor overlay. Circuits connected to each node measure capacitance to detect touch location. No overlay can be used for projected capacitive sensing.
What touch controllers are typically used on flex PCBs?
Leading capacitive touch controller chips from suppliers like Microchip, Cypress, Synaptics and STMicroelectronics are commonly used. Key factors are number of inputs, sensitivity, response time, package size and interface options.
How small can the traces be on a capacitive touch flex PCB?
Using photolithographic patterning, trace widths down to 50 microns are standard for capacitive touch flex PCBs, with spacing of similar dimensions. This enables high-density sensor arrays for maximum resolution and minimal form factor.
How many simultaneous touches can be detected?
Most standard controllers support 1-2 simultaneous touches. However, specialized multi-touch controllers can support 5, 10 or more touch points for advanced gesture recognition and multi-user interfaces.
Summary
Capacitive sensing implemented using flexible printed circuit boards provides an ideal solution for modern touch interfaces. The conformal, durable and sensitive flex circuits can be designed into a wide range of consumer, industrial, medical and automotive applications. With technology improvements, capacitive touch flex PCBs will continue gaining adoption across markets.
Leave a Reply