Introduction to Brushless Motors
Brushless motors, also known as brushless DC motors (BLDC) or electronically commutated motors (ECM), have gained significant popularity in various applications due to their high efficiency, low maintenance, and precise control capabilities. Unlike traditional brushed motors, brushless motors rely on electronic commutation to control the rotation of the rotor. This article will provide a comprehensive guide to Brushless Motor Wiring, including its specifications and best practices.
Understanding Brushless Motor Construction
To grasp the concept of brushless motor wiring, it is essential to understand the basic construction of a brushless motor. A brushless motor consists of three main components:
- Stator: The stationary part of the motor that houses the windings.
- Rotor: The rotating part of the motor that contains permanent magnets.
- Electronic Speed Controller (ESC): The electronic device responsible for controlling the motor’s speed and direction.
The stator typically has three phases, each connected to a set of windings. These windings are energized in a specific sequence to create a rotating magnetic field, which interacts with the permanent magnets on the rotor, causing it to rotate.
Brushless Motor Wiring Specifications
Phase Wires
Brushless motors typically have three phase wires, often labeled as A, B, and C, or U, V, and W. These wires are connected to the corresponding terminals on the ESC. The order of connection determines the direction of rotation of the motor. Swapping any two phase wires will reverse the motor’s direction.
Hall Sensor Wires
Most brushless motors are equipped with Hall Effect Sensors, which provide feedback to the ESC about the rotor’s position. Hall sensor wires are usually labeled as H1, H2, and H3, or S1, S2, and S3. These wires must be connected to the corresponding ports on the ESC for proper commutation and speed control.
Power Wires
Brushless motors require a power source to operate. The power wires, typically labeled as positive (+) and negative (-), should be connected to the appropriate terminals on the ESC. It is crucial to ensure that the voltage and current ratings of the power source match the specifications of the motor and ESC.
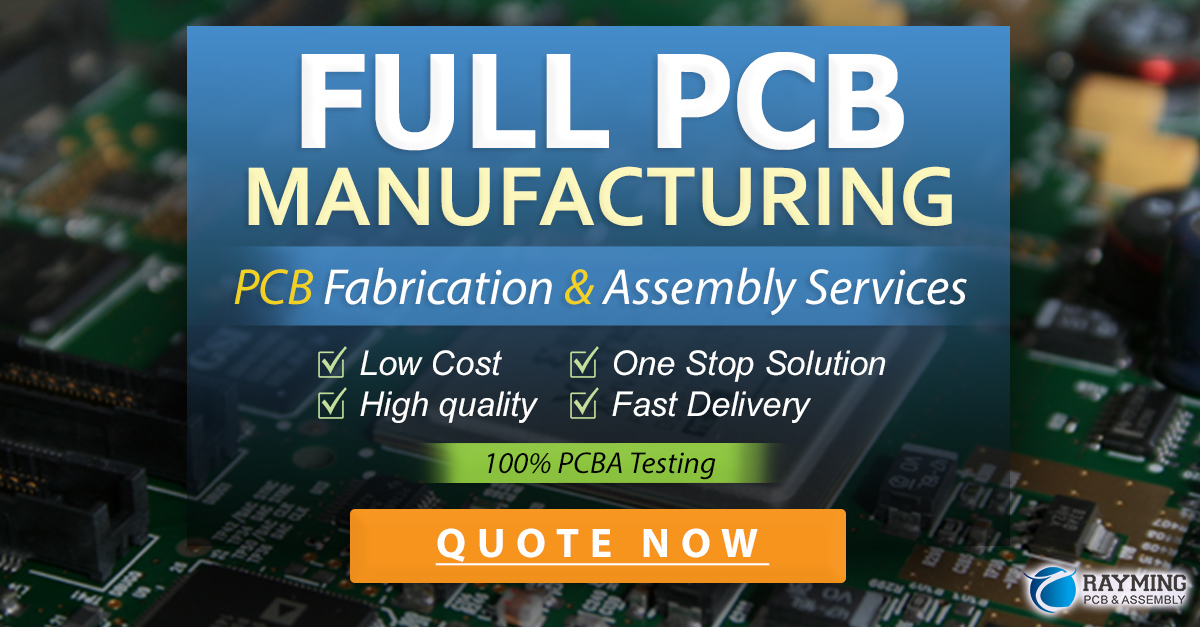
Brushless Motor Wiring Diagram
To better understand the wiring connections, let’s consider a typical brushless motor wiring diagram:
+---------+
| |
| ESC |
| |
+----+----+
|
| Phase Wires
| +---+---+---+
| | | | |
| A B C |
| | | | |
| +---+---+---+
|
| Hall Sensor Wires
| +---+---+---+
| | | | |
| H1 H2 H3 |
| | | | |
| +---+---+---+
|
| Power Wires
| +---+---+
| | | |
| + - |
| | | |
| +---+---+
|
+----+----+
| |
| Motor |
| |
+---------+
In this diagram, the ESC is connected to the brushless motor using three sets of wires: phase wires (A, B, C), Hall sensor wires (H1, H2, H3), and power wires (positive and negative).
Brushless Motor Wiring Steps
To properly wire a brushless motor, follow these steps:
- Identify the phase wires, Hall sensor wires, and power wires on both the motor and ESC.
- Connect the phase wires from the motor to the corresponding terminals on the ESC (A to A, B to B, C to C).
- Connect the Hall sensor wires from the motor to the corresponding ports on the ESC (H1 to H1, H2 to H2, H3 to H3).
- Connect the power wires from the ESC to the power source, ensuring the correct polarity (positive to positive, negative to negative).
- Double-check all connections to ensure they are secure and properly insulated.
Brushless Motor Wiring Best Practices
To ensure optimal performance and longevity of your brushless motor and ESC, consider the following best practices:
- Use high-quality, properly gauged wires for all connections.
- Ensure that all wire connections are secure and properly insulated to prevent short circuits.
- Keep the wiring as short as possible to minimize voltage drop and signal interference.
- Use a suitable capacitor across the power wires to reduce electrical noise and protect the ESC.
- Regularly inspect the wiring for any signs of damage or wear, and replace as necessary.
- Follow the manufacturer’s guidelines for the specific motor and ESC being used.
Common Brushless Motor Wiring Issues and Troubleshooting
Despite following the proper wiring procedures, issues may arise. Here are some common brushless motor wiring issues and their potential solutions:
Issue | Possible Cause | Solution |
---|---|---|
Motor not responding | Incorrect wiring connections | Double-check and correct the wiring connections |
Motor rotating in wrong direction | Phase wires connected incorrectly | Swap any two phase wires |
Erratic or inconsistent rotation | Loose or damaged wiring | Inspect and secure or replace the wiring |
Overheating | Insufficient current rating of wires or power source | Use appropriately gauged wires and a suitable power source |
Excessive vibration or noise | Imbalanced rotor or damaged bearings | Balance the rotor or replace the bearings |
If the issue persists after troubleshooting, consult the manufacturer’s support or seek assistance from a qualified technician.
Frequently Asked Questions (FAQ)
-
Q: Can I connect a brushless motor directly to a battery without an ESC?
A: No, brushless motors require an ESC to control the commutation and speed. Connecting a brushless motor directly to a battery may damage the motor or cause it to operate erratically. -
Q: How do I determine the correct wire gauge for my brushless motor?
A: The wire gauge depends on the current draw of the motor and the length of the wires. Refer to the motor’s specifications and a wire gauge chart to select the appropriate gauge. Generally, thicker wires (lower gauge numbers) are used for higher current applications. -
Q: Can I use any ESC with my brushless motor?
A: No, the ESC must be compatible with the specific brushless motor being used. Ensure that the ESC’s voltage and current ratings match the motor’s requirements, and that the ESC supports the same number of poles as the motor. -
Q: What happens if I connect the Hall sensor wires incorrectly?
A: Incorrect connection of the Hall sensor wires may result in erratic motor behavior or failure to start. Double-check the wiring diagram and ensure that the Hall sensor wires are connected to the corresponding ports on the ESC. -
Q: Can I extend the length of the brushless motor wires?
A: Yes, you can extend the brushless motor wires using appropriate wire gauge and connectors. However, keep the extension as short as possible to minimize voltage drop and signal interference. If long wire runs are necessary, consider using shielded cables to reduce electromagnetic interference (EMI).
Conclusion
Proper brushless motor wiring is essential for optimal performance, efficiency, and longevity. By understanding the motor’s construction, wiring specifications, and best practices, you can ensure a successful installation and troubleshoot common issues. Always refer to the manufacturer’s guidelines and seek professional assistance if unsure about any aspect of the wiring process. With the knowledge gained from this comprehensive guide, you are well-equipped to tackle your brushless motor wiring projects with confidence.
Leave a Reply