Introduction
The Bill of Materials (BOM) is a critical document in PCB manufacturing that lists all the components, materials, and quantities needed to build a printed circuit board. An accurate and well-organized BOM can significantly improve the efficiency of the PCB manufacturing process, reducing lead times, minimizing errors, and ultimately saving costs. In this article, we will explore how the BOM affects PCB Manufacturing Efficiency and provide best practices for creating an effective BOM.
The Importance of an Accurate BOM in PCB Manufacturing
Ensuring Correct Components and Quantities
One of the primary functions of a BOM is to ensure that the correct components and quantities are used in the manufacturing process. An inaccurate BOM can lead to several issues, such as:
- Ordering incorrect or incompatible components
- Shortages or excess inventory of components
- Delays in the manufacturing process due to missing or incorrect parts
By providing a clear and accurate list of components and quantities, the BOM helps avoid these issues and ensures a smooth manufacturing process.
Facilitating Communication Between Teams
The BOM serves as a communication tool between various teams involved in the PCB manufacturing process, including design, procurement, and production. A well-structured BOM helps:
- Design teams to clearly specify the required components
- Procurement teams to order the correct parts from suppliers
- Production teams to assemble the PCB according to the specified components and quantities
By facilitating effective communication, the BOM reduces the risk of misunderstandings and errors, leading to improved efficiency.
Enabling Efficient Inventory Management
An accurate BOM is essential for efficient inventory management. It allows the procurement team to:
- Plan and schedule component purchases based on the required quantities
- Maintain optimal inventory levels to avoid shortages or excess stock
- Negotiate better prices with suppliers by consolidating orders
Efficient inventory management helps reduce costs, minimize waste, and ensure that components are available when needed, contributing to overall manufacturing efficiency.
Best Practices for Creating an Effective BOM
Use a Consistent Format and Structure
Consistency is key when creating a BOM. Use a standard format and structure that includes the following information:
- Item number
- Quantity
- Reference designator
- Manufacturer part number
- Description
- Footprint
- Value (if applicable)
Here’s an example of a consistent BOM structure:
Item | Qty | Ref Des | Mfr Part # | Description | Footprint | Value |
---|---|---|---|---|---|---|
1 | 10 | C1-C10 | ABC123 | Capacitor | 0805 | 10µF |
2 | 5 | R1-R5 | XYZ456 | Resistor | 0603 | 1kΩ |
Using a consistent format and structure makes the BOM easier to read, understand, and maintain, reducing the risk of errors and improving efficiency.
Include Accurate and Complete Information
Ensure that the BOM includes accurate and complete information for each component. This includes:
- Correct manufacturer part numbers
- Detailed descriptions of the components
- Specific values (resistance, capacitance, etc.) when applicable
- Footprint information for proper component placement
Accurate and complete information helps avoid confusion and ensures that the correct components are ordered and used in the manufacturing process.
Use Automated Tools for BOM Management
Consider using automated tools, such as BOM management software or PLM (Product Lifecycle Management) systems, to create, manage, and maintain your BOMs. These tools offer several benefits:
- Centralized storage and version control of BOM data
- Automated validation and error checking
- Integration with other systems, such as EDA (Electronic Design Automation) and ERP (Enterprise Resource Planning)
- Collaboration features for team members to access and update BOM information
Automated tools can help streamline the BOM management process, reduce manual errors, and improve overall efficiency.
Regularly Review and Update the BOM
The BOM is a living document that should be regularly reviewed and updated throughout the product lifecycle. This includes:
- Updating component information when changes occur (e.g., obsolescence, new revisions)
- Incorporating design changes and ECOs (Engineering Change Orders)
- Verifying BOM accuracy before each production run
Regular reviews and updates ensure that the BOM remains accurate and up-to-date, minimizing the risk of manufacturing delays or errors due to outdated information.
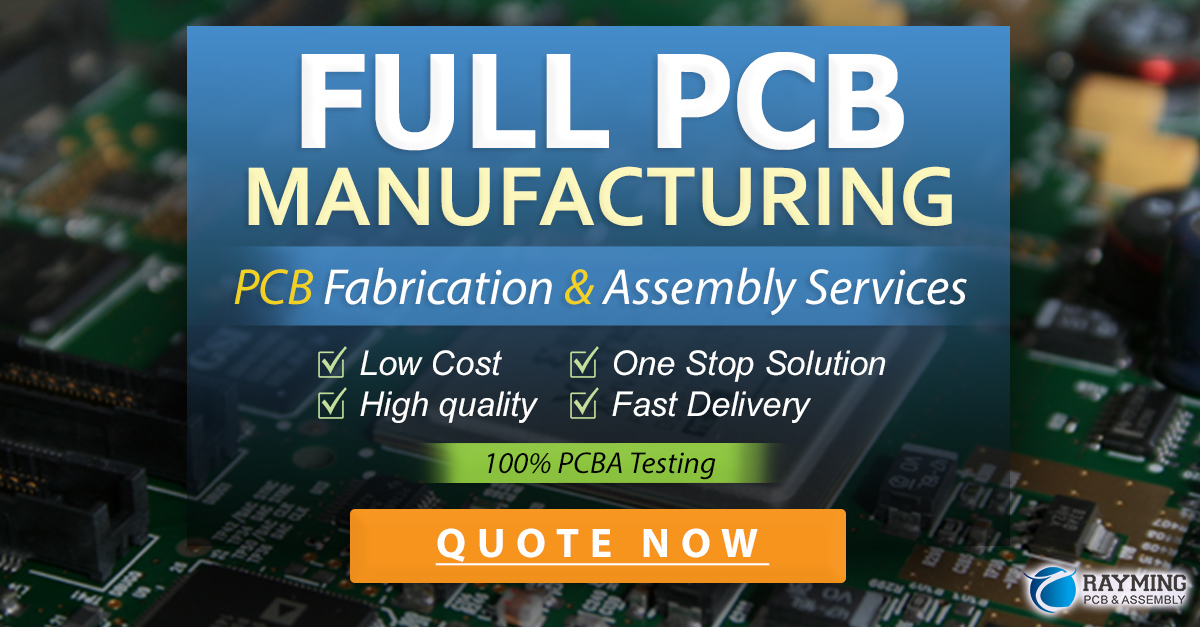
The Impact of BOM Accuracy on PCB Manufacturing Efficiency
Reduced Lead Times
An accurate BOM helps reduce lead times in several ways:
- Faster component ordering and procurement
- Minimized delays due to incorrect or missing parts
- Streamlined assembly process with correct components and quantities
By reducing lead times, an accurate BOM enables faster time-to-market and improves overall manufacturing efficiency.
Minimized Errors and Rework
Inaccuracies in the BOM can lead to various manufacturing errors, such as:
- Using incorrect or incompatible components
- Assembling PCBs with missing or extra components
- Incorrect component placement due to wrong footprint information
These errors often require rework, which can be time-consuming and costly. An accurate BOM minimizes the risk of such errors, reducing the need for rework and improving manufacturing efficiency.
Cost Savings
An accurate BOM contributes to cost savings in several ways:
- Reduced component costs through consolidated ordering and volume discounts
- Minimized waste due to correct quantities and avoided excess inventory
- Lower labor costs associated with rework and troubleshooting
By helping control costs, an accurate BOM improves the overall financial efficiency of the PCB manufacturing process.
FAQ
1. What is a BOM, and why is it important in PCB manufacturing?
A BOM (Bill of Materials) is a comprehensive list of all the components, materials, and quantities required to manufacture a printed circuit board. It is essential in PCB manufacturing because it ensures that the correct components are ordered, used, and assembled, minimizing errors and delays in the production process.
2. What are the key elements that should be included in a BOM?
A BOM should include the following key elements:
- Item number
- Quantity
- Reference designator
- Manufacturer part number
- Description
- Footprint
- Value (if applicable)
Including these elements ensures that the BOM provides accurate and complete information for each component.
3. How can I ensure my BOM is accurate and up-to-date?
To ensure your BOM is accurate and up-to-date, follow these best practices:
- Use a consistent format and structure
- Include accurate and complete information for each component
- Regularly review and update the BOM throughout the product lifecycle
- Use automated tools for BOM management to minimize manual errors
4. What are the consequences of an inaccurate BOM in PCB manufacturing?
An inaccurate BOM can lead to several issues in PCB manufacturing, such as:
- Ordering incorrect or incompatible components
- Shortages or excess inventory of components
- Delays in the manufacturing process due to missing or incorrect parts
- Manufacturing errors and rework due to incorrect component usage or placement
These issues can result in increased lead times, higher costs, and reduced overall manufacturing efficiency.
5. How can an accurate BOM help improve PCB manufacturing efficiency?
An accurate BOM improves PCB manufacturing efficiency by:
- Ensuring correct components and quantities are used
- Facilitating communication between design, procurement, and production teams
- Enabling efficient inventory management
- Reducing lead times
- Minimizing errors and rework
- Contributing to cost savings through consolidated ordering and reduced waste
By addressing these factors, an accurate BOM streamlines the PCB manufacturing process, resulting in improved efficiency and productivity.
Conclusion
The Bill of Materials (BOM) plays a crucial role in determining the efficiency of PCB manufacturing. An accurate and well-organized BOM ensures that the correct components are ordered, used, and assembled, minimizing errors, delays, and costs in the production process. By following best practices such as using a consistent format, including accurate information, regularly updating the BOM, and leveraging automated tools, companies can optimize their BOM management and improve overall PCB manufacturing efficiency. Ultimately, an effective BOM contributes to faster time-to-market, higher quality products, and increased profitability in the competitive world of electronics manufacturing.
Leave a Reply