What is a Blue PCB?
A blue printed circuit board (PCB) is a type of circuit board that has a distinctive blue color. The blue color is not just for aesthetic purposes, but it also serves important functions in the manufacturing and assembly process of electronic devices.
Blue PCBs are made from a substrate material, typically fiberglass, which is coated with a thin layer of copper. The copper layer is then etched to create the desired circuit pattern. After etching, a solder mask is applied to the board to protect the copper traces from oxidation and to prevent short circuits. It is this solder mask that gives the PCB its blue color.
Advantages of Blue PCBs
There are several advantages to using blue PCBs in electronic devices:
-
Improved Visibility: The blue color of the PCB provides a high contrast against the copper traces and other components, making it easier for technicians to inspect the board for defects or errors during the assembly process.
-
Enhanced Durability: The solder mask that gives the PCB its blue color also serves as a protective layer, shielding the copper traces from damage caused by moisture, dust, and other environmental factors.
-
Better Heat Dissipation: The blue solder mask has good thermal conductivity properties, which helps to dissipate heat more efficiently from the components on the board, improving the overall reliability and lifespan of the device.
-
Aesthetic Appeal: While not a functional advantage, the blue color of the PCB can give the finished product a professional and high-quality appearance, which can be important for consumer electronics.
Why are Blue PCBs Used in Certain Applications?
Blue PCBs are commonly used in a variety of electronic devices, from consumer electronics like smartphones and laptops to industrial equipment and aerospace systems. However, there are certain applications where blue PCBs are particularly well-suited:
High-Reliability Electronics
In applications where reliability is critical, such as aerospace, medical devices, and military equipment, blue PCBs are often the preferred choice. The enhanced durability and improved heat dissipation properties of blue PCBs make them less likely to fail under harsh conditions.
High-Density Designs
Blue PCBs are also commonly used in high-density designs where there are many small components and fine pitch traces. The high contrast provided by the blue solder mask makes it easier for technicians to inspect these dense boards for defects and ensure proper assembly.
Cost-Sensitive Applications
While blue PCBs are not the cheapest option, they are often used in cost-sensitive applications where reliability and durability are still important factors. The improved reliability of blue PCBs can help to reduce overall costs by minimizing the need for repairs and replacements over the life of the product.
How are Blue PCBs Manufactured?
The manufacturing process for blue PCBs is similar to that of other types of PCBs, with a few key differences:
-
Substrate Preparation: The fiberglass substrate is cut to the desired size and shape, and any necessary holes are drilled.
-
Copper Deposition: A thin layer of copper is deposited onto the substrate using a process called electroplating.
-
Etching: The copper layer is then etched to create the desired circuit pattern using a photolithographic process.
-
Solder Mask Application: A blue solder mask is applied to the board, typically using a silkscreen printing process. The solder mask is then cured using UV light.
-
Surface Finish: A surface finish, such as HASL (Hot Air Solder Leveling) or ENIG (Electroless Nickel Immersion Gold), is applied to the exposed copper areas to prevent oxidation and improve solderability.
-
Silk Screen: Finally, any necessary text or symbols are printed onto the board using a silkscreen process.
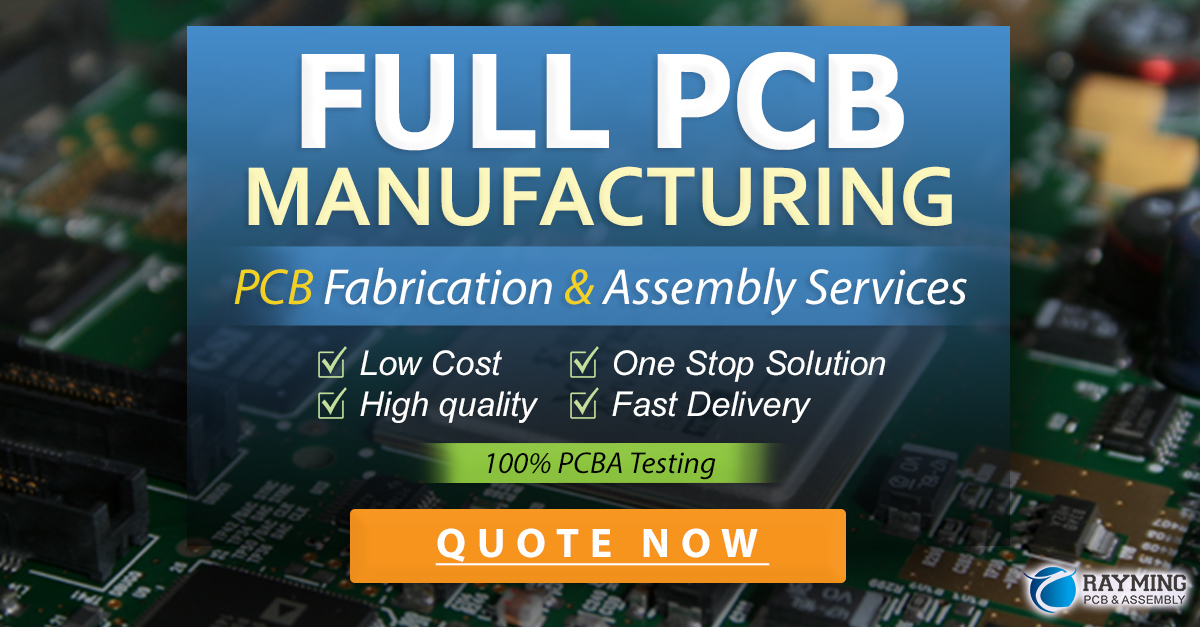
Troubleshooting Blue PCBs
While blue PCBs offer many advantages, they can also present some unique challenges when it comes to troubleshooting and repair. Here are a few tips for working with blue PCBs:
-
Use Proper Lighting: Because of the high contrast provided by the blue solder mask, it is important to use proper lighting when inspecting or working on a blue PCB. A well-lit workspace with a magnifying lamp can help to make defects and errors more visible.
-
Check for Solder Mask Damage: The blue solder mask is an important protective layer, so any damage or cracks in the mask can lead to reliability issues down the line. Be sure to inspect the board carefully for any signs of damage to the solder mask.
-
Use Appropriate Repair Techniques: When repairing a blue PCB, it is important to use techniques that will not damage the solder mask or the underlying copper traces. Avoid using abrasive cleaning methods or excessive heat, which can cause the solder mask to crack or peel.
Frequently Asked Questions
Q: Are blue PCBs more expensive than other types of PCBs?
A: Blue PCBs are typically more expensive than standard green PCBs due to the additional processing steps required to apply the blue solder mask. However, the improved reliability and durability of blue PCBs can offset the higher upfront cost over the life of the product.
Q: Can blue PCBs be used in all types of electronic devices?
A: While blue PCBs are well-suited for many applications, there may be some devices where other types of PCBs are more appropriate. For example, in some high-frequency applications, the dielectric properties of the blue solder mask may not be ideal.
Q: Are there any disadvantages to using blue PCBs?
A: One potential disadvantage of blue PCBs is that the high contrast provided by the blue solder mask can make it more difficult to see certain types of defects, such as hairline cracks in the copper traces. It is important to use proper lighting and inspection techniques to ensure that all defects are caught during the manufacturing process.
Q: How do I specify that I want a blue PCB when ordering from a manufacturer?
A: When placing an order for PCBs, you will typically need to specify the desired solder mask color as part of your design requirements. Most manufacturers will offer a range of standard solder mask colors, including blue, green, red, and yellow. If you have specific color requirements, you may need to provide the manufacturer with a Pantone color code or other color specification.
Q: Can blue PCBs be recycled?
A: Like other types of PCBs, blue PCBs can be recycled to recover valuable materials such as copper and gold. However, the recycling process for PCBs is complex and requires specialized equipment to properly separate the different materials. It is important to work with a reputable recycling company that has experience handling PCBs to ensure that the materials are properly recovered and disposed of in an environmentally responsible manner.
Conclusion
Blue PCBs are a popular choice for many electronic applications due to their improved visibility, enhanced durability, better heat dissipation, and aesthetic appeal. While they may be more expensive than standard green PCBs, the benefits of blue PCBs can make them a cost-effective choice in the long run for applications where reliability and longevity are critical factors.
When working with blue PCBs, it is important to use proper inspection and repair techniques to ensure that the solder mask and underlying copper traces are not damaged. By following best practices for handling and maintenance, blue PCBs can provide reliable performance in a wide range of electronic devices, from consumer electronics to industrial equipment and beyond.
Leave a Reply