What are Blind-Buried-Vias?
Blind and buried vias are two types of interconnects used in printed circuit board (PCB) design. These vias provide electrical connections between different layers of a multi-layer PCB, allowing for more complex and compact designs. Unlike through-hole vias, which span the entire thickness of the board, blind and buried vias are partially or completely hidden within the layers of the PCB.
Blind Vias
Blind vias are interconnects that start from either the top or bottom surface of the PCB and terminate at an inner layer, without reaching the opposite surface. They are called “blind” because they are not visible from one side of the board. Blind vias are typically used to connect the outer layers to the inner layers of a multi-layer PCB, reducing the need for through-hole vias and saving space on the board surface.
Buried Vias
Buried vias, on the other hand, are interconnects that are completely hidden within the inner layers of a multi-layer PCB. They do not extend to either the top or bottom surface of the board. Buried vias are used to create connections between inner layers, allowing for even more complex routing and further space savings on the board surface.
Advantages of Using Blind-Buried-Vias
The use of blind and buried vias in PCB design offers several advantages, including:
-
Space Savings: By utilizing the inner layers of the PCB, blind and buried vias reduce the need for through-hole vias, freeing up valuable space on the board surface for components and routing.
-
Improved Signal Integrity: Blind and buried vias can help minimize the length of signal paths, reducing the risk of signal degradation and electromagnetic interference (EMI).
-
Increased Design Flexibility: With the ability to create connections between inner layers, designers have more freedom to route signals and optimize the placement of components on the board.
-
Enhanced Reliability: Blind and buried vias can improve the overall reliability of the PCB by reducing the number of potential failure points associated with through-hole vias.
Challenges and Considerations
Despite their advantages, using blind and buried vias in PCB design also presents some challenges and considerations:
Manufacturing Complexity
The process of manufacturing PCBs with blind and buried vias is more complex and costly compared to standard through-hole via boards. Special equipment and processes, such as controlled depth drilling and precise layer alignment, are required to create these interconnects.
Design and Layout Considerations
When incorporating blind and buried vias into a PCB design, designers must carefully consider the placement and routing of these interconnects to ensure proper functionality and manufacturability. Factors such as via size, spacing, and layer stackup must be taken into account to avoid potential issues during fabrication and assembly.
Cost Implications
Due to the increased manufacturing complexity, PCBs with blind and buried vias are generally more expensive to produce than standard through-hole via boards. The cost increase is often justified by the space savings, improved performance, and enhanced reliability offered by these advanced interconnect technologies.
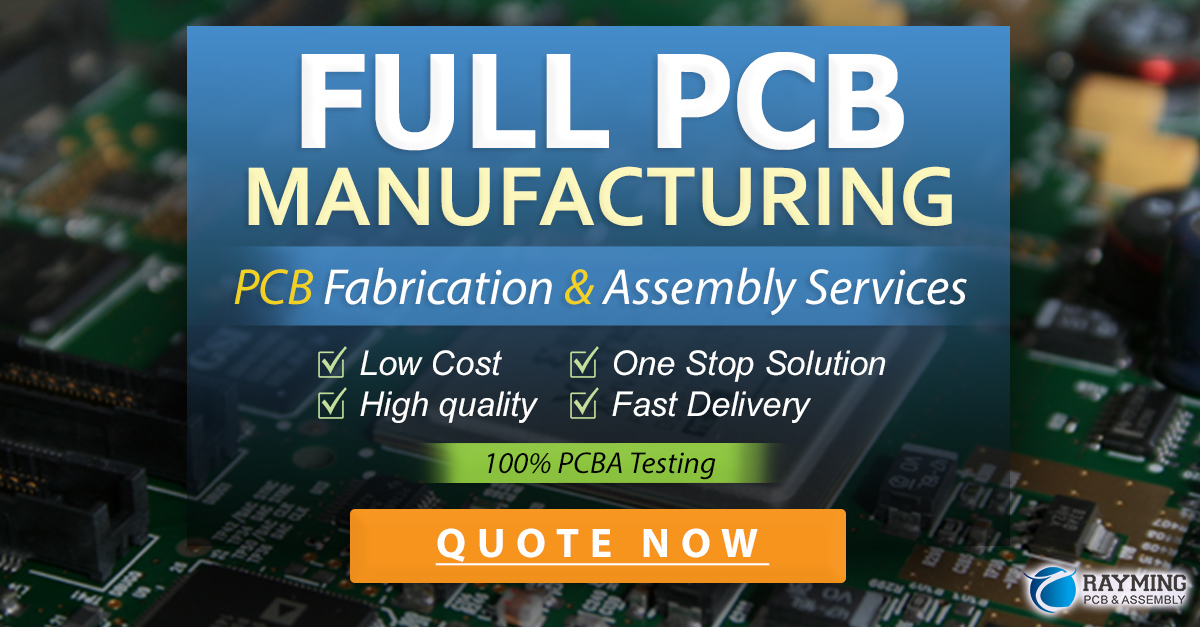
Applications of Blind-Buried-Vias
Blind and buried vias are commonly used in a variety of applications that require high-density interconnects, improved signal integrity, and compact form factors. Some examples include:
-
Smartphones and Tablets: The compact and feature-rich nature of modern mobile devices necessitates the use of blind and buried vias to maximize space utilization and enable the integration of advanced components.
-
Wearable Electronics: Wearable devices, such as smartwatches and fitness trackers, benefit from the space savings and design flexibility provided by blind and buried vias, allowing for smaller and more ergonomic form factors.
-
Aerospace and Defense: In aerospace and defense applications, where reliability and performance are critical, blind and buried vias are used to create robust and high-density interconnects that can withstand harsh environments and demanding operating conditions.
-
Medical Devices: Medical devices, such as implantable sensors and monitoring systems, often require compact and highly integrated PCBs. Blind and buried vias enable the development of miniaturized and reliable medical electronics that can be safely used in patient care.
Design and Manufacturing Process
The design and manufacturing process for PCBs with blind and buried vias involves several key steps:
PCB Design and Layer Stackup
The first step in the process is to design the PCB and define the layer stackup. This involves determining the number of layers required, the placement of components, and the routing of signals. The use of blind and buried vias must be carefully considered during this stage to ensure optimal performance and manufacturability.
Drilling and Plating
Once the PCB design is finalized, the manufacturing process begins with the drilling of via holes. For blind vias, controlled depth drilling is used to create holes that extend from the surface to the desired inner layer. Buried vias are created by drilling holes in the inner layers before the layers are laminated together.
After drilling, the via holes are plated with a conductive material, typically copper, to create the electrical connections between layers.
Lamination and Pressing
The next step is to laminate the individual layers of the PCB together using heat and pressure. This process bonds the layers and creates a solid, multi-layer board. The lamination process must be carefully controlled to ensure proper alignment of the layers and to maintain the integrity of the blind and buried vias.
Etching and Finishing
After lamination, the outer layers of the PCB are etched to create the desired circuit patterns. This process involves applying a photoresist material, exposing it to light through a patterned mask, and then chemically removing the unwanted copper.
Finally, the PCB undergoes various finishing processes, such as solder mask application, silkscreen printing, and surface finishing, to protect the board and improve its aesthetics and solderability.
FAQ
-
Q: What is the difference between blind and buried vias?
A: Blind vias start from either the top or bottom surface of the PCB and terminate at an inner layer, without reaching the opposite surface. Buried vias are completely hidden within the inner layers of the PCB and do not extend to either the top or bottom surface. -
Q: What are the advantages of using blind and buried vias in PCB design?
A: The advantages of using blind and buried vias include space savings on the board surface, improved signal integrity, increased design flexibility, and enhanced reliability. -
Q: Are PCBs with blind and buried vias more expensive to manufacture?
A: Yes, PCBs with blind and buried vias are generally more expensive to manufacture compared to standard through-hole via boards due to the increased complexity of the manufacturing process and the need for specialized equipment. -
Q: In what applications are blind and buried vias commonly used?
A: Blind and buried vias are commonly used in applications that require high-density interconnects, improved signal integrity, and compact form factors, such as smartphones, wearable electronics, aerospace and defense systems, and medical devices. -
Q: What are the key steps in the design and manufacturing process for PCBs with blind and buried vias?
A: The key steps in the design and manufacturing process for PCBs with blind and buried vias include PCB design and layer stackup, drilling and plating of via holes, lamination and pressing of layers, and etching and finishing of the outer layers.
Via Type | Description | Advantages |
---|---|---|
Blind | Starts from the top or bottom surface and terminates at an inner layer | – Space savings on the board surface – Improved signal integrity |
Buried | Completely hidden within the inner layers, does not extend to the top or bottom surface | – Increased design flexibility – Enhanced reliability |
Conclusion
Blind and buried vias are advanced interconnect technologies that offer numerous benefits in PCB design, including space savings, improved signal integrity, increased design flexibility, and enhanced reliability. These types of vias allow for the creation of high-density, compact, and high-performance electronic devices across a wide range of applications, from consumer electronics to aerospace and defense systems.
However, the use of blind and buried vias also presents challenges in terms of manufacturing complexity, design considerations, and cost implications. Designers must carefully balance the benefits and drawbacks of these technologies to ensure the optimal performance and manufacturability of their PCB designs.
As electronic devices continue to advance and become more sophisticated, the demand for innovative interconnect solutions like blind and buried vias will likely continue to grow. By understanding the principles, advantages, and challenges associated with these technologies, PCB designers and manufacturers can leverage blind and buried vias to create cutting-edge electronic products that push the boundaries of performance and functionality.
Leave a Reply