What are Bendable Circuit Boards?
Bendable circuit boards, also known as flexible printed circuits (FPCs), are made from flexible materials that allow the board to bend and flex without damage to the components or conductive tracks. This allows them to be used in applications where a rigid printed circuit board (PCB) would not be suitable.
Some key properties and advantages of FPCs:
- Can be bent and folded repeatedly without cracking or breaking conductive copper tracks
- Thin and lightweight
- Can conform to different shapes and spaces
- Vibration and impact resistant
- Allow for flexible design and packaging of electronics
- Often used in small consumer electronics, wearables, medical devices, aerospace, automotive and robotics
FPCs use flexible insulating substrates like polyimide or polyester instead of traditional rigid substrates like FR-4. Conductive tracks are photolithographically printed on the substrate using copper foil bonding. Components can be soldered onto the FPC and integrated flex-rigid boards combine both flexible and rigid sections.
FPC Construction
The basic construction of a flexible PCB comprises:
- Flexible Substrate Material – Usually polyimide or polyester sheets around 25-100 microns thick
- Conductive Layer – Photolithographically etched copper tracks, around 12-35 microns thick
- Coverlay – A soldermask overlayer that protects the copper from oxidation and prevents shorts
- Adhesive – Acrylic or epoxy resin that bonds the layers together
FPCs can be single sided with circuits on one side only, double sided with circuits on both sides, or multilayer with sandwiched internal circuit layers laminated together. Shielding layers can also be added for EMI/RFI protection.
Applications of Flex Circuits
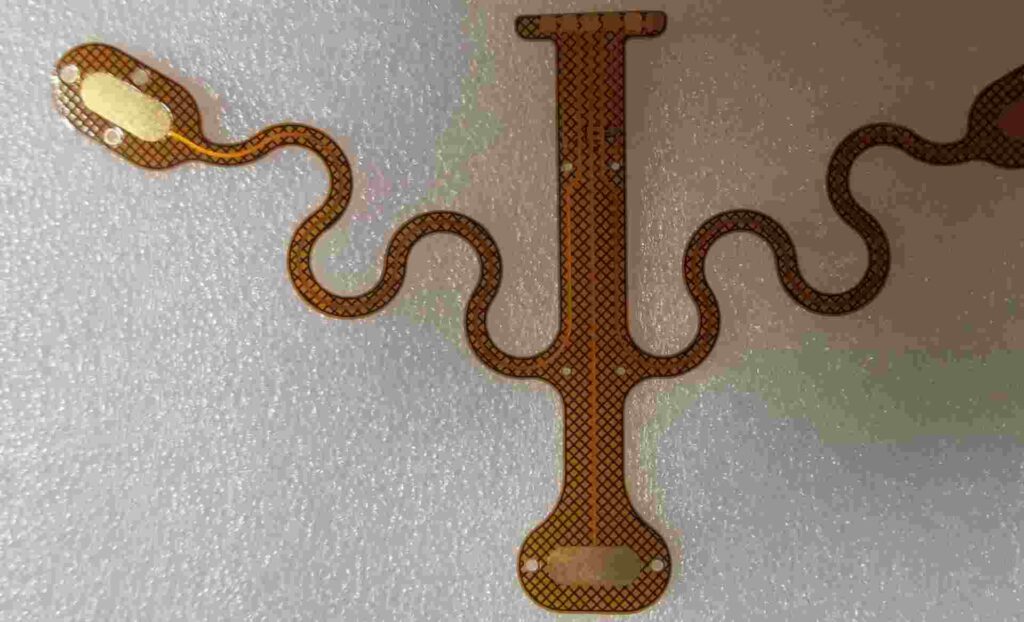
Some of the main applications of bendable circuit boards include:
Consumer Electronics
FPCs are commonly used to connect LCD/OLED displays to motherboards in smartphones, tablets and TVs. Flex circuits allow the screen to fold over onto the device body. They are also used for wearable tech like smart watches and fitness bands, allowing the circuitry to conform to the wrist.
Automotive
Flex circuits are used in brake lights, engine systems, sensors, dashboard electronics, switches and other automotive applications. Their flexibility allows installation in tight spaces and the ability to withstand vibration.
Medical Devices
In medical devices like hearing aids and heart monitors, flexible circuits can follow complex contours and bends of the human body. This allows optimization of device comfort and safety.
Aerospace and Defense
Avionics systems, radars and other electronic systems in aircraft and spacecraft use flexible circuits. Their lightweight nature and vibration resistance Suit the aerospace environment.
Robotics
FPCs allow movement of robotic arms, improving range of motion. Circuitry in robot joints can flex repeatedly without breakage.
Benefits of Flexible Printed Circuits
Some of the main benefits that make flexible PCBs advantageous for many applications include:
- Light weight – Flex circuits are much thinner and lighter than rigid PCBs. This allows for smaller, more compact product designs. Weight savings are particularly beneficial in aerospace, automotive and portable consumer electronics applications.
- Flexibility – The ability to bend, fold and flex to non rigid shapes allows installation of circuits where rigid boards just wouldn’t work. They can adapt to moving configurations and mechanisms.
- Reliability – FPCs are extremely durable and withstand repeated bending stress much better than rigid boards. The polyimide base material provides temperature resistance and chemical resistance.
- Space savings – Complex wiring can be condensed down onto a thin, flexible circuit that takes up less space. This allows for miniaturization and integration of tight spaces.
- Cost savings – The fabrication process can lower costs compared to rigid PCBs for short production runs and prototype builds. Less wiring and connectors also increase cost efficiency.
Trends and Future Outlook
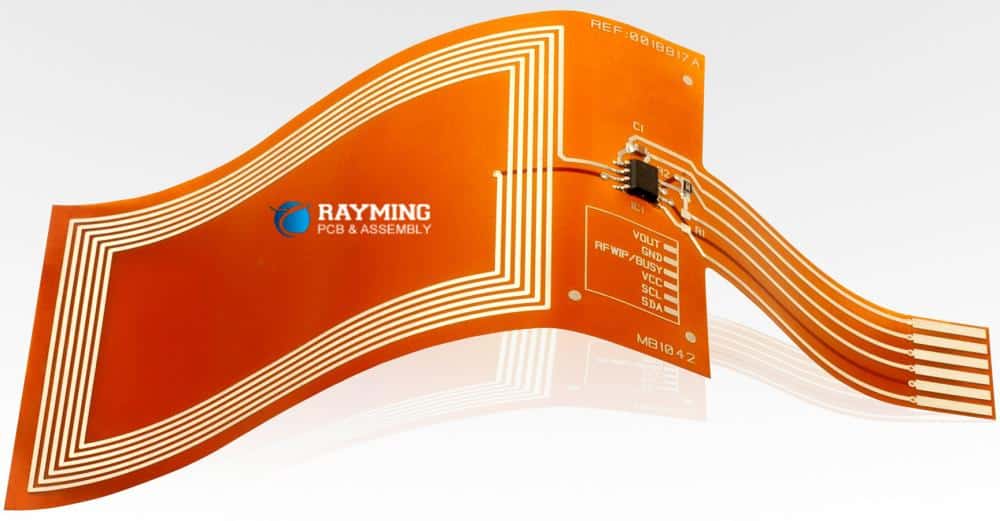
Flex circuits represent an important enabling technology for the miniaturization and integration of modern electronic devices and systems across industries. Some key trends to watch for include:
- Wearable technology – Flex circuits will become even more vital as wearable devices like health and fitness trackers become more sophisticated. Comfort and reliability with flexible human movement is paramount.
- Flexible displays – Foldable and rollable displays will drive demand for flex circuit innovation to accommodate frequent display contour changes. Applications include foldable smartphones, tablets and TVs.
- Flexible batteries – As battery technology evolves to incorporate flexibility, they will pair well with flexible circuits to power tomorrow’s devices.
- Smart fabric – Electronic textiles will integrate flex circuits to bring connectivity, sensors and computing power into clothing and fabric materials.
- Medical – Flexible thin circuitry with biosensors will be key to next generation implantables, prosthetics and medical monitoring devices.
- IoT devices – The Internet of Things market will look to FPCs for embedding streamlined circuitry into a variety of products like appliances, sensors, controllers and more.
As electronic devices continue getting smaller, lighter and more sophisticated, demand for flex circuit technology is projected to steadily grow over the next decade across a wide array of markets and applications.
Benefits vs Limitations
Benefits
- Can conform to a wide variety of shapes
- Highly durable and flexible – thousands of bends are possible
- Good high frequency characteristics
- Lightweight and space saving
- Allows optimized industrial design and packaging
- Vibration and impact resistance
- Easier installation in tight spaces
- Lower fabrication costs at lower volumes
Limitations
- More expensive at higher volumes compared to rigid PCBs
- Not suitable for very high density interconnection circuits
- Requires special design considerations for flexing areas
- Often requires additional stiffeners and encapsulation for structure
- Thermal management can be challenging
- Repair and rework is more difficult compared to rigid PCBs
FQA
What materials are used in flexible printed circuits?
The most common materials are polyimide or polyester films for the flexible dielectric substrate. Copper foil is used to form the conductive tracks and traces. Epoxy acrylic polymers are used for the adhesive layers. Coverlays made of soldermask or liquid photoimagable coatings are used.
Can components be mounted directly onto flexible circuits?
Yes, components like resistors, capacitors, diodes, LEDs and ICs can be surface mounted onto flexible circuits using conductive epoxy or soldering. Smaller components are preferable for flexibility. Rigid sections can also be incorporated onto flex-rigid boards.
How many times can FPCs be flexed before failing?
Properly designed FPCs using robust materials like polyimide substrates can withstand flexing hundreds of thousands of times. Dynamic flexing endurance depends on several factors like substrate thickness, conductor thickness, bend radius etc.
Are flexible PCBs suited for high frequency, high speed signals?
Yes, FPCs can be engineered to work well with high frequency signals up to several GHz, due to the smooth copper conductors and solid dielectric properties. Controlled impedance flex circuits with proper signal integrity design are important.
Are there limitations to the minimum bend radius of flex circuits?
Yes, overly tight bending can damage flex circuits. The minimum bend radius is usually defined as 10X the total thickness for dynamic flexing or 5X for static bends. The bend radius must be considered carefully in the design.
Leave a Reply