What are Battery Separators?
Battery separators are thin, porous membranes placed between the positive and negative electrodes in a battery cell. Their primary purpose is to prevent direct contact between the electrodes while allowing ionic charge transfer through the electrolyte. This physical separation is crucial for preventing short circuits and maintaining the battery’s performance and safety.
Types of Battery Separators
There are several types of battery separators, each with its unique characteristics and applications. Let’s explore some of the most common types:
1. Microporous Separators
Microporous separators are the most widely used type in lithium-ion batteries. They are typically made from polyethylene (PE), polypropylene (PP), or a combination of both (PE/PP). These separators have a porous structure with pore sizes ranging from 0.03 to 0.1 microns, allowing for efficient ion transport while blocking larger particles.
2. Nonwoven Separators
Nonwoven separators are made from a web of randomly oriented fibers, usually polyethylene terephthalate (PET) or glass. They offer excellent mechanical strength, thermal stability, and chemical resistance. Nonwoven separators are commonly used in lead-acid batteries and some lithium-ion batteries.
3. Ceramic-coated Separators
Ceramic-coated separators are microporous separators with an additional ceramic coating, such as alumina (Al2O3) or silica (SiO2). The ceramic coating enhances the separator’s thermal stability, mechanical strength, and resistance to shrinkage at high temperatures. These separators are increasingly used in high-performance lithium-ion batteries for electric vehicles and energy storage systems.
4. Ion-exchange Membranes
Ion-exchange membranes are separators that selectively allow the passage of specific ions while blocking others. They are made from polymers with charged functional groups, such as sulfonic acid or quaternary ammonium. Ion-exchange membranes are used in advanced battery systems, such as redox flow batteries and fuel cells.
Battery Separator Materials
Battery separators can be made from various materials, each with its unique properties and benefits. Here are some of the most common materials used in battery separators:
Material | Characteristics | Applications |
---|---|---|
Polyethylene (PE) | Low cost, good mechanical strength, excellent chemical resistance | Lithium-ion batteries, lead-acid batteries |
Polypropylene (PP) | High mechanical strength, good thermal stability, excellent chemical resistance | Lithium-ion batteries, lead-acid batteries |
PE/PP blend | Combines the benefits of PE and PP, improved shutdown performance | Lithium-ion batteries |
Polyethylene terephthalate (PET) | High mechanical strength, good thermal stability, excellent chemical resistance | Lead-acid batteries, lithium-ion batteries |
Glass fiber | High porosity, excellent thermal stability, good chemical resistance | Lead-acid batteries, high-temperature applications |
Ceramic-coated (Al2O3, SiO2) | Enhanced thermal stability, mechanical strength, and resistance to shrinkage | High-performance lithium-ion batteries |
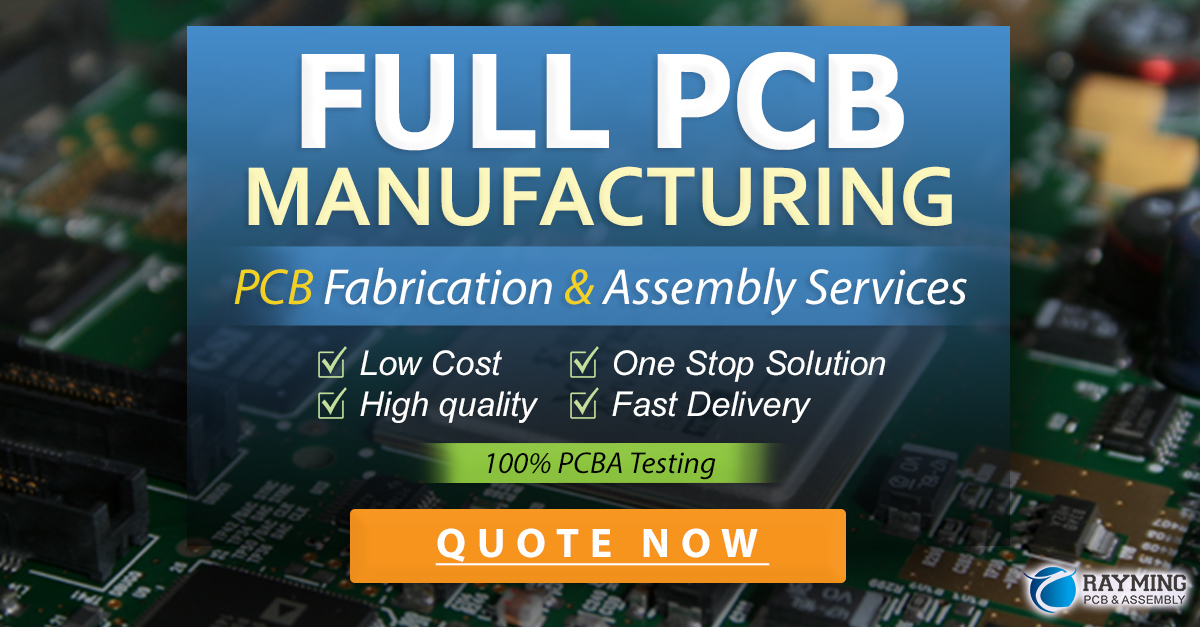
Key Properties of Battery Separators
To ensure optimal battery performance and safety, battery separators must possess several key properties. These include:
1. Porosity and Pore Size Distribution
Porosity refers to the volume fraction of voids within the separator material. A high porosity allows for efficient ion transport through the separator, reducing internal resistance and improving battery performance. Pore size distribution is also crucial, as it determines the separator’s ability to block particles while allowing ions to pass through.
2. Mechanical Strength
Battery separators must have sufficient mechanical strength to withstand the stresses encountered during battery assembly, operation, and potential abuse conditions. Mechanical strength is essential for preventing separator rupture or puncture, which could lead to short circuits and safety issues.
3. Thermal Stability
Thermal stability is a critical property for battery separators, especially in high-temperature applications or abuse conditions. The separator must maintain its dimensional stability and mechanical integrity at elevated temperatures to prevent thermal runaway and ensure safe battery operation.
4. Chemical Resistance
Battery separators are exposed to harsh chemical environments within the battery, including acidic or alkaline electrolytes and oxidizing or reducing species. The separator material must be chemically inert and resistant to degradation to ensure long-term stability and performance.
5. Wettability
Wettability refers to the separator’s ability to absorb and retain the electrolyte solution. Good wettability ensures efficient ion transport and reduces the risk of dry spots, which can lead to increased internal resistance and poor battery performance.
Battery Separator Applications
Battery separators find applications in a wide range of battery systems, from small portable devices to large-scale energy storage systems. Some of the most common applications include:
1. Lithium-ion Batteries
Lithium-ion batteries are the most widely used rechargeable batteries in portable electronics, electric vehicles, and grid-scale energy storage. Microporous PE, PP, or PE/PP separators are the most common choice for lithium-ion batteries, offering good mechanical strength, chemical resistance, and shutdown properties.
2. Lead-acid Batteries
Lead-acid batteries are still widely used in automotive, industrial, and stationary applications. Nonwoven PET or glass fiber separators are commonly used in lead-acid batteries due to their high porosity, mechanical strength, and chemical resistance.
3. Nickel-based Batteries
Nickel-based batteries, such as nickel-cadmium (NiCd) and nickel-metal hydride (NiMH), are used in portable devices and some industrial applications. Nonwoven or microporous separators made from PE, PP, or PET are used in these batteries.
4. Flow Batteries
Flow batteries, such as redox flow batteries and hybrid flow batteries, are emerging technologies for large-scale energy storage. Ion-exchange membranes or microporous separators with high chemical resistance are used in flow batteries to separate the anolyte and catholyte compartments.
Frequently Asked Questions (FAQ)
1. What is the difference between a battery separator and an electrolyte?
A battery separator is a physical barrier that separates the positive and negative electrodes in a battery cell, while an electrolyte is the ionic conductor that allows charge transfer between the electrodes. The separator is a solid material, while the electrolyte is typically a liquid or gel.
2. Can battery separators be reused or recycled?
In most cases, battery separators are not reused or recycled due to the challenges in separating them from other battery components and potential contamination. However, research is ongoing to develop more sustainable and recyclable separator materials.
3. How do battery separators prevent short circuits?
Battery separators prevent short circuits by physically separating the positive and negative electrodes, preventing direct contact between them. The separator’s porous structure allows ions to pass through while blocking larger particles that could cause a short circuit.
4. What is the shutdown function in battery separators?
The shutdown function is a safety feature in some battery separators, particularly in lithium-ion batteries. When the battery temperature reaches a certain threshold, the separator’s pores close, blocking ion transport and shutting down the battery to prevent thermal runaway.
5. How do I choose the right battery separator for my application?
Choosing the right battery separator depends on several factors, including the battery chemistry, operating conditions, safety requirements, and cost. Consult with battery separator manufacturers or experts to determine the most suitable separator material and properties for your specific application.
Conclusion
Battery separators are essential components in rechargeable battery systems, ensuring proper function, safety, and performance. With a wide range of separator types, materials, and properties available, it is crucial to select the most suitable separator for each application. As battery technologies continue to evolve, advances in separator materials and designs will play a key role in enabling higher energy density, longer cycle life, and improved safety in future battery systems.
Leave a Reply