What Is a Barebone PCB?
A barebone PCB, also known as a bare circuit board or unpopulated PCB, is a printed circuit board that has no components soldered onto it. It is essentially a blank canvas, ready for electronic components to be added according to the specific requirements of the project.
Barebone PCBs are the foundation of any electronic device, providing the necessary interconnections between components. They are made from a non-conductive substrate, typically fiberglass or composite material, with copper traces printed onto the surface to create the desired electrical pathways.
Advantages of Using Barebone PCBs
- Customization: Barebone PCBs allow for complete customization of the electronic device, as the designer has full control over component selection and placement.
- Cost-effective: Purchasing barebone PCBs and components separately can be more cost-effective than buying a pre-assembled PCB, especially for small-scale productions or prototypes.
- Flexibility: With a barebone PCB, designers can easily make changes or updates to the circuit by replacing or adding components as needed.
- Educational value: Working with barebone PCBs is an excellent way to learn about electronic circuits and gain hands-on experience in PCB Assembly.
Types of Barebone PCBs
There are several types of barebone PCBs, each with its own unique characteristics and applications.
Single-sided PCBs
Single-sided PCBs have copper traces on only one side of the substrate. They are the simplest and most cost-effective type of PCB, suitable for basic electronic projects with low component density.
Double-sided PCBs
Double-sided PCBs have copper traces on both sides of the substrate, allowing for more complex circuits and higher component density. The two sides are connected using through-hole vias.
Multi-layer PCBs
Multi-layer PCBs consist of three or more layers of copper traces, separated by insulating layers. They offer the highest component density and are used in advanced electronic devices that require complex interconnections.
Flexible PCBs
Flexible PCBs are made from a flexible substrate, such as polyimide or polyester, allowing them to bend and conform to various shapes. They are often used in wearable electronics, medical devices, and applications where space is limited.
How to Use a Barebone PCB
Using a barebone PCB involves several steps, from designing the circuit to soldering the components onto the board.
Designing the Circuit
- Define the requirements of your electronic device, including its intended function, power requirements, and any specific features.
- Create a schematic diagram of the circuit, showing all the components and their interconnections.
- Use PCB design software, such as KiCad or Eagle, to create a PCB layout based on the schematic. Consider factors such as component placement, trace width, and spacing.
- Generate the necessary files for PCB fabrication, including Gerber files and drill files.
Sourcing Components
- Create a bill of materials (BOM) listing all the components required for your circuit.
- Purchase the components from reliable suppliers, ensuring they meet the specified requirements (e.g., package type, value, and tolerance).
- Consider factors such as lead time, minimum order quantity, and cost when selecting suppliers.
PCB Assembly
- Clean the barebone PCB to remove any dirt or residue that may affect soldering.
- Apply solder paste to the pads where components will be placed, using a stencil or syringe.
- Place the components onto the PCB, ensuring correct orientation and alignment with the pads.
- Use a reflow oven or hot air gun to melt the solder paste and create a strong bond between the components and the PCB.
- Inspect the assembled PCB for any defects, such as bridging, cold joints, or misaligned components.
Testing and Debugging
- Perform a visual inspection of the assembled PCB to identify any obvious issues.
- Use a multimeter to check for continuity and short circuits.
- Power on the device and test its functionality, comparing it to the expected behavior based on the schematic.
- If issues are found, use an oscilloscope or logic analyzer to diagnose the problem and make necessary repairs or modifications.
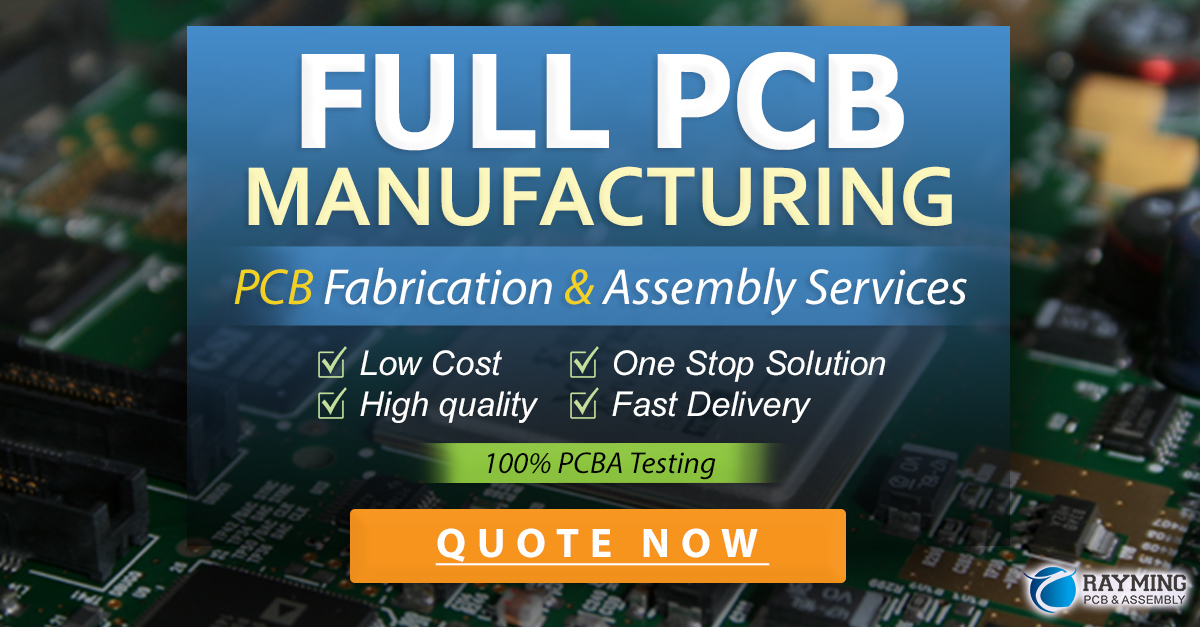
Common Applications of Barebone PCBs
Barebone PCBs are used in a wide range of electronic devices and applications, such as:
- Consumer electronics (e.g., smartphones, tablets, and wearables)
- Industrial control systems
- Medical devices
- Automotive electronics
- Internet of Things (IoT) devices
- Robotics and automation
The versatility of barebone PCBs allows designers to create custom solutions tailored to specific requirements and constraints.
Choosing the Right Barebone PCB
When selecting a barebone PCB for your project, consider the following factors:
- Size and shape: Ensure the PCB fits within the available space and accommodates all the necessary components.
- Layer count: Choose the appropriate number of layers based on the complexity of your circuit and the required component density.
- Material: Select a substrate material that meets your requirements for durability, thermal stability, and electrical properties.
- Copper weight: Specify the appropriate copper weight (thickness) based on the current carrying requirements of your circuit.
- Surface finish: Choose a surface finish that provides adequate solderability, protection against oxidation, and compatibility with your assembly process (e.g., HASL, ENIG, or OSP).
Factor | Consideration |
---|---|
Size and shape | Fit within available space, accommodate components |
Layer count | Based on circuit complexity and component density |
Material | Durability, thermal stability, electrical properties |
Copper weight | Current carrying requirements |
Surface finish | Solderability, oxidation protection, assembly compatibility |
Frequently Asked Questions (FAQ)
1. Can I design a barebone PCB without prior experience?
While it is possible to design a barebone PCB without prior experience, it is recommended to start with simpler projects and gain knowledge through online resources, tutorials, and hands-on practice. PCB design software often includes libraries and templates that can help beginners get started.
2. What is the difference between a barebone PCB and a development board?
A barebone PCB is a blank circuit board without any components soldered onto it, while a development board is a pre-assembled PCB that includes a microcontroller, peripherals, and other components. Development boards are designed for rapid prototyping and learning, while barebone PCBs offer more flexibility and customization.
3. How do I ensure my barebone PCB is manufactured correctly?
To ensure your barebone PCB is manufactured correctly, provide clear and accurate design files (e.g., Gerber and drill files) to the PCB fabrication service. Communicate any special requirements or constraints, and consider using a reputable manufacturer with experience in producing high-quality PCBs.
4. Can barebone PCBs be used for high-volume production?
Yes, barebone PCBs can be used for high-volume production. In fact, using barebone PCBs and sourcing components separately can be more cost-effective for large-scale manufacturing. However, it is essential to consider factors such as supply chain management, lead times, and quality control when scaling up production.
5. What tools and equipment do I need to assemble a barebone PCB?
To assemble a barebone PCB, you will need a soldering iron, solder, flux, tweezers, and a magnifying lens or microscope for inspection. Depending on the complexity of your project, you may also need a reflow oven, hot air gun, or stencil for applying solder paste. ESD-safe equipment and a clean workspace are recommended to prevent damage to sensitive components.
Conclusion
Barebone PCBs offer a flexible and cost-effective solution for creating custom electronic devices. By understanding the different types of barebone PCBs, the design and assembly process, and the factors to consider when selecting a PCB, designers can create innovative and reliable electronic products.
As technology continues to advance, the demand for customized and application-specific electronic devices will only grow. Barebone PCBs will play an increasingly important role in enabling designers to meet these challenges and push the boundaries of what is possible in the world of electronics.
Leave a Reply