What is a Bare Board?
A bare board, also known as a printed circuit board (PCB) without components, is the foundation of any electronic device. It consists of a non-conductive substrate, typically made of fiberglass or other composite materials, with conductive copper traces etched onto its surface. These traces form the electrical connections between the various components that will be mounted on the board later in the manufacturing process.
Bare boards are the starting point for creating complex electronic devices, from smartphones and computers to industrial control systems and medical equipment. The quality and reliability of the bare board directly impact the performance and longevity of the final product.
The Importance of Bare Board Testing
Bare board testing is a critical step in the manufacturing process of electronic devices. It involves thoroughly examining the bare board for defects and ensuring that it meets the required specifications before any components are soldered onto it. This testing process is crucial for several reasons:
-
Early Defect Detection: By identifying defects early in the manufacturing process, bare board testing helps prevent costly rework and delays later on. Catching issues at this stage is much more cost-effective than discovering them after components have been mounted or the device has been assembled.
-
Quality Assurance: Bare board testing ensures that the foundation of the electronic device is of high quality and meets the necessary standards. This, in turn, contributes to the overall reliability and performance of the final product.
-
Compliance with Standards: Many industries, such as automotive, aerospace, and medical, have strict quality standards that electronic devices must meet. Bare board testing helps manufacturers comply with these standards by verifying that the boards are free from defects and meet the required specifications.
-
Cost Savings: By identifying and addressing issues early in the manufacturing process, bare board testing helps reduce the overall cost of production. It minimizes the need for rework, scrap, and delays, which can significantly impact the bottom line.
Common Bare Board Defects
During the manufacturing process, various defects can occur on bare boards. These defects can lead to malfunctions or complete failure of the electronic device if not detected and corrected. Some of the most common bare board defects include:
-
Short Circuits: A short circuit occurs when two or more conductive traces that should not be connected come into contact with each other. This can happen due to manufacturing errors, such as over-etching or incorrect trace spacing.
-
Open Circuits: An open circuit is a break in a conductive trace that prevents electrical current from flowing through it. This can be caused by under-etching, damage to the trace, or incorrect drilling.
-
Incorrect Trace Width or Spacing: If the width or spacing of the conductive traces does not meet the specified requirements, it can lead to signal integrity issues or even short circuits.
-
Hole Defects: Holes drilled in the bare board for component leads or vias must be the correct size and position. Incorrect hole sizes, missing holes, or misaligned holes can cause assembly issues and affect the device’s functionality.
-
Contaminants: Foreign particles, such as dust or dirt, can contaminate the bare board during the manufacturing process. These contaminants can cause short circuits or other defects if not removed.
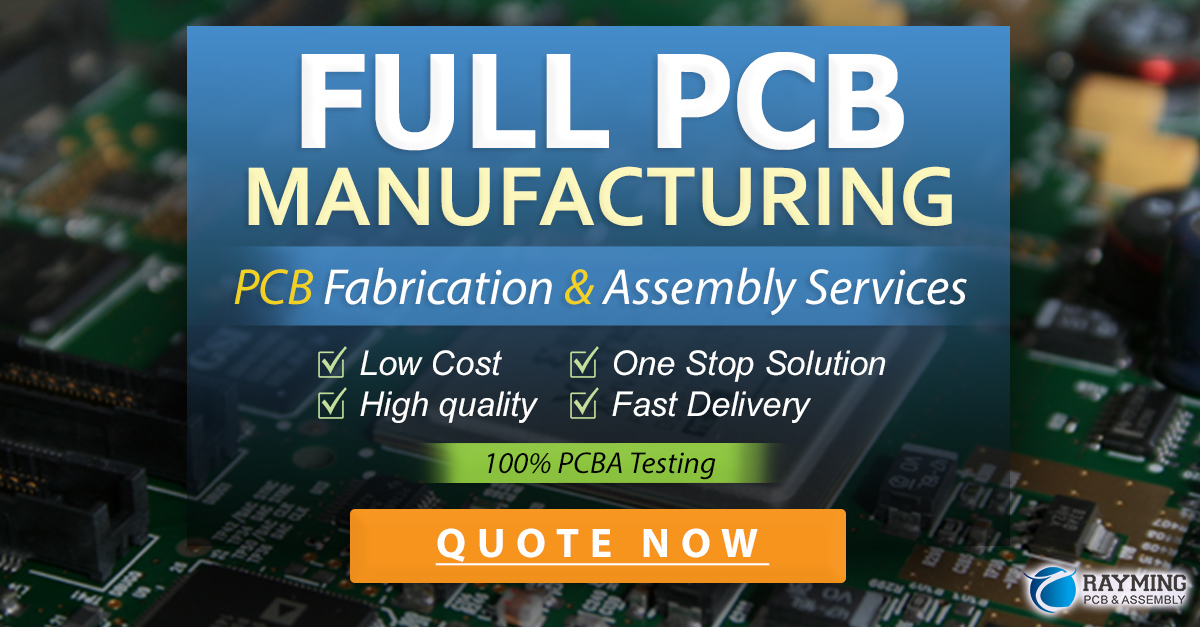
Bare Board Testing Methods
There are several methods used to test bare boards for defects. The choice of method depends on factors such as the complexity of the board, the required level of accuracy, and the available resources. Some of the most common bare board testing methods include:
-
Visual Inspection: This is the most basic form of bare board testing, where the board is visually examined for defects such as scratches, contamination, or incorrect etching. While visual inspection can catch some obvious defects, it is not reliable for detecting more subtle issues.
-
Automated Optical Inspection (AOI): AOI uses high-resolution cameras and advanced image processing software to automatically inspect the bare board for defects. This method is faster and more accurate than manual visual inspection and can detect a wide range of defects, including short circuits, open circuits, and incorrect trace widths.
-
Flying Probe Testing: In this method, a set of movable probes is used to make contact with the conductive traces on the bare board. The probes apply electrical signals to the traces and measure the response to detect defects such as short circuits and open circuits. Flying probe testing is highly accurate but slower than some other methods.
-
Bed of Nails Testing: This method involves using a fixture with a grid of spring-loaded pins (the “nails”) that make contact with specific points on the bare board. Electrical signals are applied to the pins, and the response is measured to detect defects. Bed of nails testing is fast and efficient but requires a custom fixture for each board design.
-
Electrical Impedance Testing: This method measures the electrical impedance of the conductive traces on the bare board. By comparing the measured impedance to the expected values, defects such as short circuits, open circuits, and incorrect trace widths can be detected. Electrical impedance testing is accurate and can be performed quickly.
Choosing the Right Bare Board Testing Method
When selecting a bare board testing method, several factors should be considered:
-
Board Complexity: The complexity of the bare board, including the number of layers, the density of the traces, and the presence of fine-pitch features, will influence the choice of testing method. More complex boards may require more advanced testing methods to ensure accurate defect detection.
-
Required Accuracy: The level of accuracy required for defect detection will also impact the choice of testing method. Some methods, such as flying probe testing, offer higher accuracy than others, such as visual inspection.
-
Testing Speed: The speed at which the testing must be performed is another important consideration. Some methods, such as bed of nails testing, are faster than others, such as flying probe testing. The choice of method should balance the need for speed with the required accuracy.
-
Cost: The cost of the testing equipment and the overall cost per board should also be considered. Some methods, such as AOI, require a higher initial investment but can offer cost savings in the long run due to increased efficiency and reduced rework.
Testing Method | Accuracy | Speed | Cost |
---|---|---|---|
Visual Inspection | Low | Slow | Low |
Automated Optical Inspection (AOI) | High | Fast | High |
Flying Probe Testing | High | Slow | Medium |
Bed of Nails Testing | Medium | Fast | Medium |
Electrical Impedance Testing | High | Fast | Medium |
Best Practices for Bare Board Testing
To ensure the effectiveness and efficiency of bare board testing, consider the following best practices:
-
Establish Clear Specifications: Before beginning the testing process, ensure that the bare board specifications are clearly defined and communicated to all relevant parties. This includes the expected dimensions, tolerances, and electrical properties of the board.
-
Choose the Appropriate Testing Method: Select the bare board testing method that best suits the specific requirements of the project, considering factors such as board complexity, required accuracy, testing speed, and cost.
-
Regularly Calibrate and Maintain Equipment: To ensure accurate and consistent results, regularly calibrate and maintain the testing equipment according to the manufacturer’s recommendations.
-
Document and Analyze Results: Keep detailed records of the testing results, including any defects found and the actions taken to address them. Regularly analyze this data to identify trends and potential areas for improvement in the manufacturing process.
-
Implement a Quality Management System: Establish a robust quality management system that encompasses bare board testing and other aspects of the manufacturing process. This can help ensure consistent quality, reduce defects, and facilitate continuous improvement.
Frequently Asked Questions (FAQ)
-
What is the difference between a bare board and a printed circuit board (PCB)?
A bare board and a PCB are essentially the same things – a non-conductive substrate with conductive traces etched onto its surface. The term “bare board” is used to refer to the board before any components are mounted on it, while “PCB” can refer to the board at any stage of the manufacturing process. -
Why is bare board testing important?
Bare board testing is important because it helps identify defects early in the manufacturing process, ensuring that the foundation of the electronic device is of high quality and meets the necessary standards. This, in turn, contributes to the overall reliability and performance of the final product, reduces the cost of production, and helps manufacturers comply with industry standards. -
What are some common defects found during bare board testing?
Common defects found during bare board testing include short circuits, open circuits, incorrect trace width or spacing, hole defects, and contaminants. These defects can lead to malfunctions or complete failure of the electronic device if not detected and corrected. -
What are the main bare board testing methods?
The main bare board testing methods are visual inspection, automated optical inspection (AOI), flying probe testing, bed of nails testing, and electrical impedance testing. Each method has its own advantages and disadvantages in terms of accuracy, speed, and cost. -
How can I choose the right bare board testing method for my project?
When choosing a bare board testing method, consider factors such as the complexity of the board, the required level of accuracy, the testing speed, and the cost. Evaluate each method based on these factors and select the one that best suits the specific requirements of your project. It may also be helpful to consult with experienced professionals or testing service providers to make an informed decision.
Conclusion
Bare board testing is a critical step in the manufacturing process of electronic devices, ensuring that the foundation of the device is of high quality and free from defects. By identifying issues early on, bare board testing helps reduce costs, improve reliability, and ensure compliance with industry standards.
There are several methods available for bare board testing, each with its own strengths and weaknesses. Choosing the right method depends on factors such as board complexity, required accuracy, testing speed, and cost. Implementing best practices, such as establishing clear specifications, regularly calibrating equipment, and documenting results, can further enhance the effectiveness of bare board testing.
As electronic devices continue to become more complex and miniaturized, the importance of bare board testing will only continue to grow. By investing in the right testing methods and practices, manufacturers can ensure the quality and reliability of their products, ultimately leading to customer satisfaction and business success.
Leave a Reply