What is PCB strain relief and Why is it Important?
PCB strain relief refers to methods and techniques used to prevent mechanical stress and strain on wires, cables, and connectors attached to a printed circuit board (PCB). When wires or cables are subjected to pulling, bending, or twisting forces, it can cause the connections to loosen or break over time, leading to electrical failures and malfunctions.
Proper strain relief is crucial for ensuring the long-term reliability and durability of electronic devices. It helps to:
- Protect wire and cable connections from mechanical damage
- Prevent intermittent electrical issues caused by loose connections
- Extend the lifespan of the device by minimizing stress on components
- Improve overall product quality and customer satisfaction
Common Causes of Strain on PCB Wires and Cables
There are several factors that can contribute to strain on PCB wires and cables:
-
Vibration and Shock: Electronic devices used in automotive, aerospace, or industrial applications are often subjected to vibration and shock, which can cause wires to rub against each other or the PCB, leading to abrasion and eventual failure.
-
Thermal Expansion and Contraction: Temperature changes can cause materials to expand and contract at different rates, putting stress on wire connections.
-
Improper Handling: Rough handling during assembly, installation, or maintenance can put excessive strain on wires and cables.
-
Poor Design: If the wire gauge is too small for the current load, or if the wire routing is not optimized for strain relief, it can lead to premature failure.
Techniques for Implementing PCB Strain Relief
There are several techniques that can be used to provide strain relief for PCB wires and cables:
1. Strain Relief Connectors
Strain relief connectors are designed to grip the wire or cable insulation and take the strain off the electrical connections. They come in various types, such as:
- Cord grips
- Cable glands
- Bushings
- Clamps
Connector Type | Description | Advantages |
---|---|---|
Cord Grips | Provides a tight fit around the cable jacket | Easy to install, suitable for round cables |
Cable Glands | Offers IP-rated sealing and strain relief | Ideal for harsh environments |
Bushings | Snap-in or threaded designs for panel-mount applications | Quick installation, various sizes available |
Clamps | Secures cables to the PCB or enclosure | Adjustable, can accommodate multiple cables |
2. Strain Relief Brackets
Strain relief brackets are mechanical components that are attached to the PCB and provide an anchor point for wires or cables. They can be made from various materials, such as:
- Metal (e.g., stainless steel, aluminum)
- Plastic (e.g., nylon, polyethylene)
- Rubber (e.g., silicone, thermoplastic elastomer)
Brackets can be designed to suit specific applications and cable sizes, and they can be secured to the PCB using screws, rivets, or adhesives.
3. Cable Ties and Zip Ties
Cable ties and zip ties are simple yet effective solutions for bundling and securing wires and cables. They help to:
- Keep wires organized and tidy
- Prevent wires from rubbing against each other or the PCB
- Provide a strain relief point when anchored to the PCB or enclosure
Cable ties are available in various lengths, widths, and materials to suit different applications. Some common materials include:
- Nylon
- Polypropylene
- Stainless steel
4. Wire Routing and Bend Relief
Proper wire routing and bend relief can help to minimize strain on PCB connections. Some best practices include:
- Keeping wires and cables as short as possible
- Avoiding sharp bends or kinks
- Using smooth, gradual curves when routing wires
- Providing adequate clearance between wires and other components
- Using cable guides or channels to maintain proper routing
5. Adhesives and Potting Compounds
Adhesives and potting compounds can be used to secure wires and provide strain relief. Some common types include:
- Epoxy
- Silicone
- Hot melt adhesives
- UV-curable adhesives
Potting compounds are particularly useful for sealing and protecting wire connections in harsh environments, such as those exposed to moisture, chemicals, or extreme temperatures.
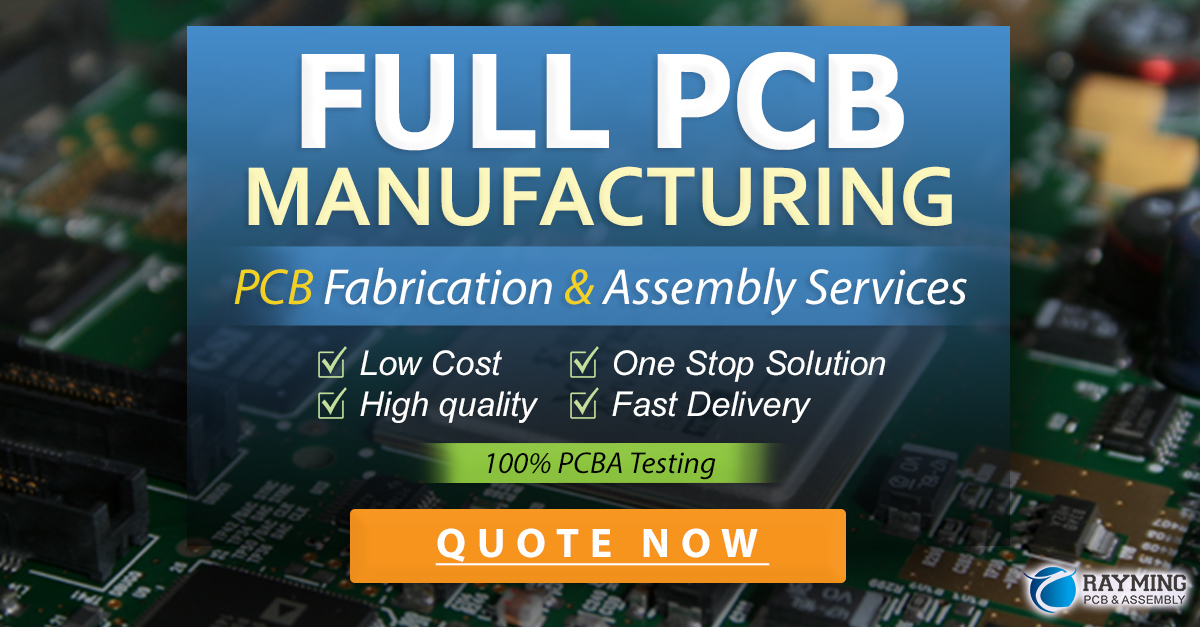
Designing for PCB Strain Relief
When designing a PCB, it’s important to consider strain relief from the outset. Some key factors to keep in mind include:
-
Component Placement: Position connectors and other strain-sensitive components away from the edges of the PCB, and orient them so that the wire or cable exits in a straight line.
-
Hole Size and Shape: Use properly sized holes for wire and cable entry, and consider using rounded or chamfered edges to reduce stress concentrations.
-
Pad Size and Spacing: Ensure that pads are large enough to provide a strong solder joint, and that there is sufficient spacing between pads to prevent bridging or short circuits.
-
Mounting Options: Include provisions for mounting strain relief components, such as brackets or clamps, and ensure that they are easily accessible for assembly and maintenance.
FAQ
1. What is the most common cause of strain on PCB wires?
Vibration and shock are the most common causes of strain on PCB wires, particularly in applications where the device is subjected to constant movement or impact.
2. Can I use cable ties for strain relief on a high-vibration application?
Cable ties can provide some strain relief, but they may not be sufficient for high-vibration environments. In these cases, it’s better to use more robust solutions, such as strain relief brackets or potting compounds.
3. How do I choose the right strain relief connector for my application?
When selecting a strain relief connector, consider factors such as the cable diameter, the level of environmental protection required (e.g., IP rating), and the amount of strain that the connector will need to withstand. Consult the manufacturer’s specifications and recommendations to ensure a proper fit.
4. Can I add strain relief to an existing PCB design?
Yes, it is possible to retrofit strain relief solutions onto an existing PCB, but it may require some modifications to the board or enclosure. It’s always best to incorporate strain relief into the initial design to ensure the best possible performance and reliability.
5. What are some common materials used for strain relief brackets?
Common materials for strain relief brackets include metals (e.g., stainless steel, aluminum), plastics (e.g., nylon, polyethylene), and rubbers (e.g., silicone, thermoplastic elastomer). The choice of material depends on factors such as the required strength, durability, and environmental resistance.
Conclusion
Proper PCB strain relief is essential for ensuring the long-term reliability and performance of electronic devices. By understanding the common causes of strain and implementing appropriate strain relief techniques, designers and engineers can create PCBs that are better equipped to withstand the rigors of real-world use.
Whether through the use of strain relief connectors, brackets, cable ties, or other methods, the goal is to minimize stress on wire and cable connections and prevent failures due to mechanical damage. By considering strain relief throughout the design process and following best practices for wire routing and component placement, it’s possible to create PCBs that are both robust and reliable.
As with any aspect of PCB design, it’s important to consider the specific requirements of the application and to choose strain relief solutions that are well-suited to the environment and conditions in which the device will be used. By taking a thoughtful and proactive approach to strain relief, designers can create PCBs that are built to last and that provide dependable performance over the long haul.
Leave a Reply