What is PCB Panelization?
PCB panelization is the process of grouping multiple printed circuit board (PCB) designs onto a single panel for manufacturing. This technique is used to optimize production efficiency, reduce costs, and minimize waste. By placing multiple PCBs on a single panel, manufacturers can process a larger number of boards simultaneously, resulting in faster throughput and lower per-unit costs.
Benefits of PCB Panelization
- Cost reduction: Panelization allows for the production of multiple PCBs in a single manufacturing run, reducing setup time and costs.
- Increased efficiency: By processing multiple boards at once, manufacturers can optimize their production line and increase overall throughput.
- Improved handling: Panelized PCBs are easier to handle during the assembly process, as they can be treated as a single unit until the final depaneling stage.
- Reduced waste: Panelization minimizes the amount of unused space on a manufacturing panel, reducing material waste and environmental impact.
PCB Panelization Techniques
There are several techniques used in PCB panelization, each with its own advantages and disadvantages. The choice of technique depends on factors such as the PCB design, manufacturing requirements, and end-use application.
V-Scoring
V-scoring is a popular panelization technique that involves creating V-shaped grooves along the edges of individual PCBs on the panel. These grooves allow for easy separation of the boards after the manufacturing process is complete. V-scoring is suitable for PCBs with simple shapes and moderate production volumes.
Advantages:
– Cost-effective for moderate production volumes
– Allows for easy separation of individual PCBs
– Suitable for PCBs with simple shapes
Disadvantages:
– Not suitable for complex PCB shapes or designs with components near the edges
– May cause stress on the PCB during the depaneling process
Tab Routing
Tab routing involves creating small tabs that connect individual PCBs on the panel. These tabs are milled away during the depaneling process, leaving behind smooth, clean edges. Tab routing is suitable for PCBs with complex shapes or designs that require components near the edges.
Advantages:
– Suitable for complex PCB shapes and designs
– Allows for components to be placed near the edges of the PCB
– Provides clean, smooth edges after depaneling
Disadvantages:
– More expensive than V-scoring due to additional milling process
– Tabs may cause stress on the PCB during the depaneling process
Perforated Boards
Perforated boards, also known as break-away panels, feature small holes or perforations along the edges of individual PCBs. These perforations allow for easy separation of the boards by applying pressure or bending the panel. Perforated boards are suitable for low-volume production runs and prototyping.
Advantages:
– Cost-effective for low-volume production and prototyping
– Easy to separate individual PCBs without specialized tools
Disadvantages:
– Not suitable for high-volume production
– Perforations may weaken the structural integrity of the PCB
– May leave rough edges after separation
PCB Panelization Design Considerations
When designing a PCB for panelization, several factors must be taken into account to ensure optimal manufacturing results and product quality.
Panel Size and Layout
The size and layout of the panelization panel should be carefully considered to maximize material utilization and minimize waste. Factors to consider include:
- PCB dimensions and shape
- Number of PCBs per panel
- Spacing between individual PCBs
- Placement of tooling holes and Fiducial Markers
Tooling Holes and Fiducial Markers
Tooling holes and fiducial markers are essential features in PCB panelization design. Tooling holes are used to secure the panel during the manufacturing process, while fiducial markers help align the panel for accurate component placement and assembly.
- Tooling holes should be placed in a uniform pattern around the panel edges
- Fiducial markers should be placed near the corners of each individual PCB
Depaneling Methods
The chosen depaneling method should be considered during the PCB design stage to ensure compatibility and minimize potential issues. Designers should take into account:
- The type of panelization technique (V-scoring, tab routing, or perforated boards)
- The location and size of V-grooves, tabs, or perforations
- The required clearance around components and board edges
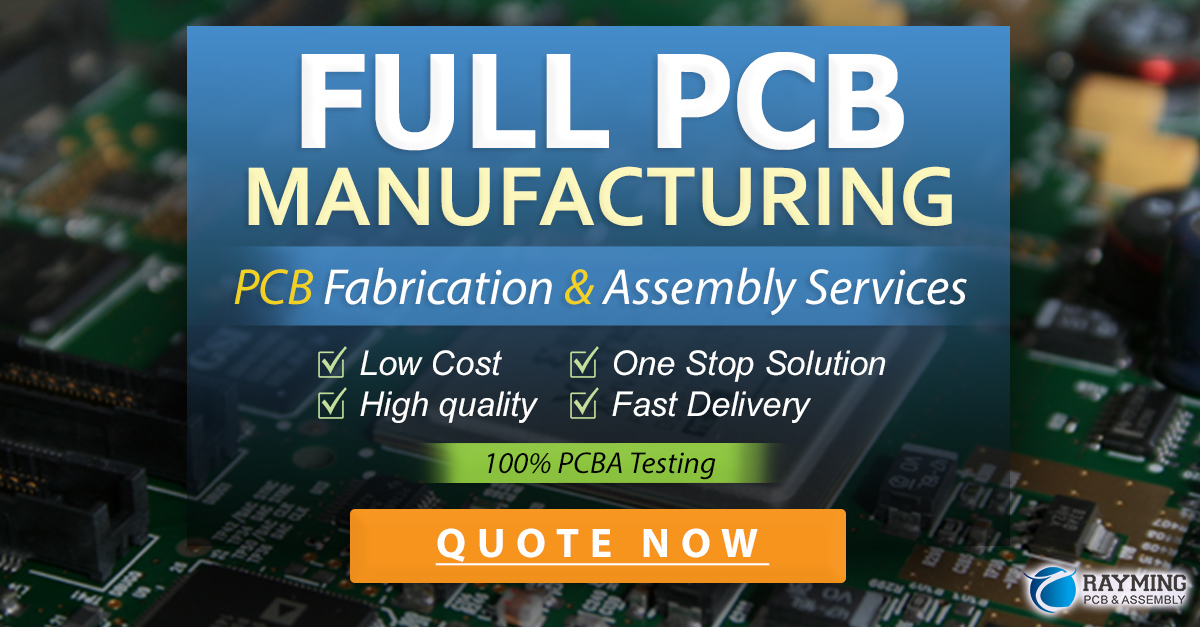
PCB Panelization Manufacturing Process
The PCB panelization manufacturing process involves several key steps to ensure the production of high-quality, reliable circuit boards.
-
Panel preparation: The panelization panel is designed and prepared based on the individual PCB designs and manufacturing requirements.
-
Copper etching: The panel undergoes a copper etching process to create the desired circuit patterns on the PCBs.
-
Drilling: Holes are drilled through the panel for component placement, mounting, and tooling purposes.
-
Solder mask application: A solder mask is applied to the panel to protect the copper traces and prevent short circuits.
-
Silkscreen printing: Text, logos, and component identifiers are printed on the panel using silkscreen printing techniques.
-
Surface finish application: A surface finish, such as HASL, ENIG, or OSP, is applied to the panel to improve solderability and protect the exposed copper.
-
Depaneling: The individual PCBs are separated from the panel using the chosen depaneling method (V-scoring, tab routing, or perforated boards).
Frequently Asked Questions (FAQ)
-
What is the purpose of PCB panelization?
PCB panelization is used to optimize production efficiency, reduce costs, and minimize waste by grouping multiple PCB designs onto a single panel for manufacturing. -
What are the most common PCB panelization techniques?
The most common PCB panelization techniques are V-scoring, tab routing, and perforated boards. Each technique has its own advantages and disadvantages, and the choice depends on factors such as the PCB design, manufacturing requirements, and end-use application. -
What factors should be considered when designing a PCB for panelization?
When designing a PCB for panelization, factors such as panel size and layout, tooling holes and fiducial markers, and depaneling methods should be carefully considered to ensure optimal manufacturing results and product quality. -
How does PCB panelization help reduce manufacturing costs?
PCB panelization helps reduce manufacturing costs by allowing for the production of multiple PCBs in a single manufacturing run, reducing setup time and costs. By processing multiple boards at once, manufacturers can optimize their production line and increase overall throughput. -
What are the benefits of using fiducial markers in PCB panelization?
Fiducial markers help align the panelization panel for accurate component placement and assembly during the manufacturing process. By ensuring precise alignment, fiducial markers contribute to the production of high-quality, reliable PCBs.
Conclusion
PCB panelization is a critical process in the manufacturing of printed circuit boards, offering numerous benefits such as cost reduction, increased efficiency, improved handling, and reduced waste. By understanding the various panelization techniques, design considerations, and manufacturing processes, engineers and manufacturers can optimize their PCB production and ensure the creation of high-quality, reliable products. As the electronics industry continues to evolve, the importance of effective PCB panelization will only continue to grow, driving innovation and shaping the future of PCB manufacturing.
Leave a Reply