What is an Air-Core Inductor?
An air-core inductor is a passive electronic component that consists of a coil of wire wound around a non-magnetic core, such as air or plastic. The inductor’s primary function is to store energy in the form of a magnetic field when an electric current passes through it. The stored energy is then released back into the circuit when the current changes.
The inductance of an air-core inductor depends on several factors, including the number of turns, the coil diameter, and the length of the coil. The general formula for calculating the inductance of an air-core inductor is:
L = (µ₀ × N² × A) / l
Where:
– L is the inductance in henries (H)
– µ₀ is the permeability of free space (4π × 10⁻⁷ H/m)
– N is the number of turns
– A is the cross-sectional area of the coil in square meters (m²)
– l is the length of the coil in meters (m)
Advantages and Disadvantages of Air-Core Inductors
Advantages
-
Low losses: Air-core inductors have lower losses compared to inductors with ferromagnetic cores, as they do not suffer from core losses such as eddy current and hysteresis losses.
-
High frequency operation: The absence of a ferromagnetic core allows air-core inductors to operate at higher frequencies without significant performance degradation.
-
No saturation: Air-core inductors do not saturate, as there is no magnetic core material to reach its saturation point.
-
Linearity: The inductance of an air-core inductor remains constant regardless of the current flowing through it, making them suitable for applications requiring linear behavior.
Disadvantages
-
Lower inductance: For a given size, air-core inductors have lower inductance values compared to inductors with ferromagnetic cores.
-
Larger size: To achieve the same inductance value as an inductor with a ferromagnetic core, an air-core inductor requires more turns and a larger size.
-
Susceptibility to external magnetic fields: Air-core inductors are more susceptible to external magnetic fields, which can cause unwanted coupling and interference.
Air-Core Inductor Design Considerations
When designing an air-core inductor, several factors must be considered to ensure optimal performance and meet the desired specifications.
Inductance Value
The first step in designing an air-core inductor is to determine the required inductance value. This value is typically dictated by the application and the desired circuit performance. Once the inductance value is known, the designer can use the inductance formula mentioned earlier to calculate the necessary number of turns, coil diameter, and coil length.
Winding Type
There are several types of windings that can be used for air-core inductors, each with its own advantages and disadvantages.
-
Single-layer solenoid: This is the simplest and most common type of winding, consisting of a single layer of closely spaced turns. Single-layer solenoids offer good performance and are easy to manufacture, but they may have higher parasitic capacitance compared to other winding types.
-
Multi-layer solenoid: Multi-layer solenoids consist of multiple layers of windings, with each layer wound on top of the previous one. This winding type allows for higher inductance values in a smaller package, but it may have higher parasitic capacitance and lower self-resonant frequency (SRF) compared to single-layer solenoids.
-
Toroidal winding: Toroidal windings are wound around a donut-shaped core, providing a more compact design and reduced external magnetic field. However, toroidal windings are more difficult to manufacture and may have higher parasitic capacitance compared to solenoid windings.
-
Planar spiral winding: Planar spiral windings are flat coils etched or printed on a substrate, such as a printed circuit board (PCB). This winding type offers excellent repeatability and low profile, making them suitable for high-frequency applications. However, planar spiral windings have lower inductance values compared to solenoid and toroidal windings.
Wire Gauge and Material
The choice of wire gauge and material is crucial for air-core inductor design, as it affects the inductor’s resistance, current-carrying capacity, and overall performance.
-
Wire gauge: Thicker wire gauges (lower gauge numbers) have lower resistance and higher current-carrying capacity, but they also result in larger inductor sizes. Thinner wire gauges (higher gauge numbers) allow for more compact designs but have higher resistance and lower current-carrying capacity. The designer must balance the trade-offs between size, resistance, and current-carrying capacity when selecting the appropriate wire gauge.
-
Wire material: The most common wire materials for air-core inductors are copper and silver-plated copper. Copper is the most widely used material due to its good conductivity and relatively low cost. Silver-plated copper offers even better conductivity and improved high-frequency performance, but it is more expensive than pure copper.
Quality Factor (Q)
The quality factor (Q) of an air-core inductor is a measure of its efficiency and is defined as the ratio of the inductor’s reactance to its resistance at a given frequency. A higher Q indicates lower losses and better performance. The quality factor can be calculated using the following formula:
Q = (2πfL) / R
Where:
– Q is the quality factor (dimensionless)
– f is the frequency in hertz (Hz)
– L is the inductance in henries (H)
– R is the inductor’s resistance in ohms (Ω)
To optimize the quality factor, designers should minimize the inductor’s resistance by using thicker wire gauges, high-conductivity materials, and minimizing the coil length. However, these measures may result in larger inductor sizes, so a balance must be struck between size and performance.
Self-Resonant Frequency (SRF)
The self-resonant frequency (SRF) of an air-core inductor is the frequency at which the inductor’s parasitic capacitance resonates with its inductance, causing the inductor to behave like a resonant circuit. Above the SRF, the inductor’s performance degrades, and it may even behave like a capacitor.
To maximize the SRF, designers should minimize the inductor’s parasitic capacitance by using single-layer windings, increasing the spacing between turns, and using low-dielectric materials for the coil former and insulation.
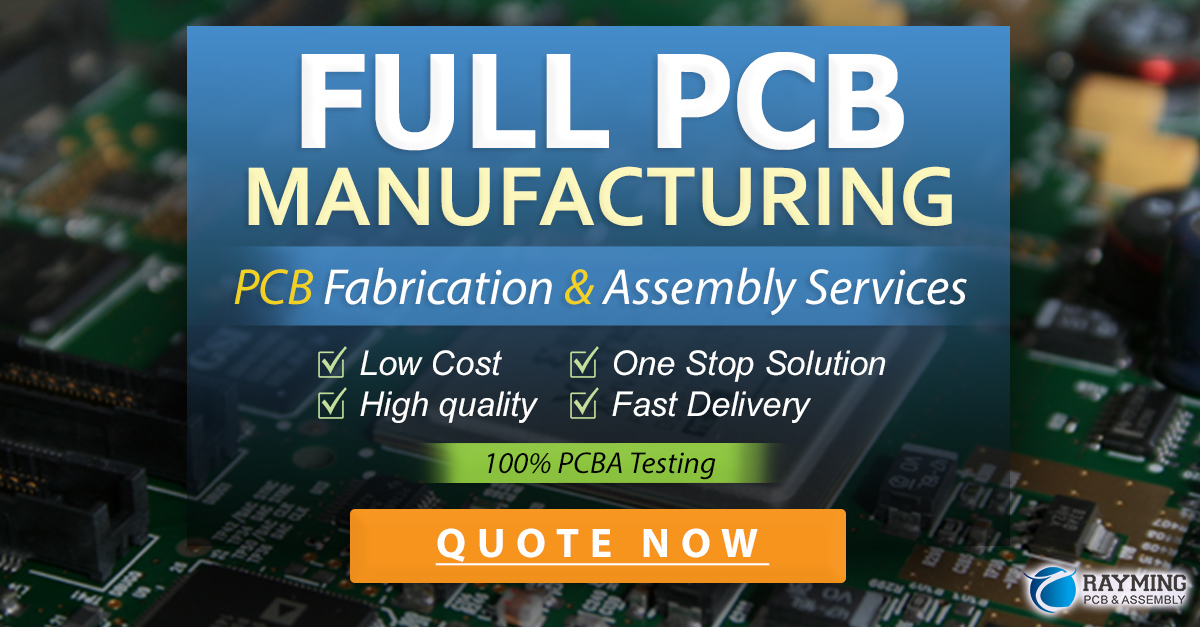
Practical Examples
Example 1: Single-Layer Solenoid Inductor
Design a single-layer solenoid air-core inductor with an inductance of 1 µH, a quality factor of at least 50 at 10 MHz, and a current-carrying capacity of 100 mA.
Given:
– Inductance (L) = 1 µH
– Quality factor (Q) ≥ 50 at 10 MHz
– Current-carrying capacity (I) = 100 mA
Step 1: Determine the maximum allowable resistance.
R = (2πfL) / Q
R = (2π × 10⁷ Hz × 1 × 10⁻⁶ H) / 50
R = 1.257 Ω
Step 2: Choose the wire gauge based on the current-carrying capacity and maximum resistance. In this case, 30 AWG copper wire with a resistance of 0.338 Ω/m is suitable.
Step 3: Calculate the required number of turns using the inductance formula.
L = (µ₀ × N² × A) / l
Assume a coil diameter of 5 mm and a coil length of 10 mm.
A = π × (0.005 m / 2)² = 1.963 × 10⁻⁵ m²
l = 0.01 m
N = √((L × l) / (µ₀ × A))
N = √((1 × 10⁻⁶ H × 0.01 m) / (4π × 10⁻⁷ H/m × 1.963 × 10⁻⁵ m²))
N ≈ 18 turns
Step 4: Calculate the actual coil length and resistance.
Actual coil length = (18 turns × 0.005 m) + (17 spaces × 0.0002 m) = 0.0934 m
Actual resistance = 0.338 Ω/m × 0.0934 m = 0.032 Ω
The resulting single-layer solenoid air-core inductor has an inductance of 1 µH, a quality factor of approximately 394 at 10 MHz, and a current-carrying capacity of 100 mA.
Example 2: Multi-Layer Solenoid Inductor
Design a multi-layer solenoid air-core inductor with an inductance of 10 µH, a quality factor of at least 80 at 5 MHz, and a current-carrying capacity of 50 mA.
Given:
– Inductance (L) = 10 µH
– Quality factor (Q) ≥ 80 at 5 MHz
– Current-carrying capacity (I) = 50 mA
Step 1: Determine the maximum allowable resistance.
R = (2πfL) / Q
R = (2π × 5 × 10⁶ Hz × 10 × 10⁻⁶ H) / 80
R = 3.927 Ω
Step 2: Choose the wire gauge based on the current-carrying capacity and maximum resistance. In this case, 34 AWG copper wire with a resistance of 0.867 Ω/m is suitable.
Step 3: Calculate the required number of turns using the inductance formula.
L = (µ₀ × N² × A) / l
Assume a coil diameter of 4 mm, a coil length of 8 mm, and 4 layers.
A = π × (0.004 m / 2)² = 1.257 × 10⁻⁵ m²
l = 0.008 m
N = √((L × l) / (µ₀ × A))
N = √((10 × 10⁻⁶ H × 0.008 m) / (4π × 10⁻⁷ H/m × 1.257 × 10⁻⁵ m²))
N ≈ 57 turns
Step 4: Calculate the actual coil length and resistance.
Actual coil length = (57 turns × 0.004 m) + (56 spaces × 0.0002 m) = 0.2392 m
Actual resistance = 0.867 Ω/m × 0.2392 m = 0.207 Ω
The resulting multi-layer solenoid air-core inductor has an inductance of 10 µH, a quality factor of approximately 190 at 5 MHz, and a current-carrying capacity of 50 mA.
FAQ
-
Q: What is the difference between air-core inductors and inductors with ferromagnetic cores?
A: Air-core inductors have no magnetic core material, relying solely on the magnetic field generated by the current flowing through the windings. Inductors with ferromagnetic cores use materials such as iron, ferrite, or permalloy to enhance the magnetic field and increase the inductance value for a given size. Air-core inductors have lower losses and can operate at higher frequencies, while inductors with ferromagnetic cores offer higher inductance values in a smaller package. -
Q: How do I choose the right wire gauge for my air-core inductor?
A: The choice of wire gauge depends on the desired current-carrying capacity and the maximum allowable resistance. Thicker wire gauges (lower gauge numbers) have lower resistance and higher current-carrying capacity but result in larger inductor sizes. Thinner wire gauges (higher gauge numbers) allow for more compact designs but have higher resistance and lower current-carrying capacity. Consider the trade-offs between size, resistance, and current-carrying capacity when selecting the appropriate wire gauge. -
Q: What is the self-resonant frequency (SRF) of an air-core inductor, and why is it important?
A: The self-resonant frequency (SRF) is the frequency at which the inductor’s parasitic capacitance resonates with its inductance, causing the inductor to behave like a resonant circuit. Above the SRF, the inductor’s performance degrades, and it may even behave like a capacitor. It is important to design air-core inductors with a high SRF to ensure optimal performance in the desired frequency range. -
Q: How can I increase the quality factor (Q) of my air-core inductor?
A: To increase the quality factor of an air-core inductor, minimize the inductor’s resistance by using thicker wire gauges, high-conductivity materials (such as copper or silver-plated copper), and minimizing the coil length. However, keep in mind that these measures may result in larger inductor sizes, so a balance must be struck between size and performance. -
Q: Can I use an air-core inductor in high-power applications?
A: Air-core inductors can be used in high-power applications, but proper design considerations must be taken to ensure the inductor can handle the required current without overheating or suffering from excessive losses. Using thicker wire gauges, high-conductivity materials, and providing adequate cooling can help improve the inductor’s power-handling capability. However, for very high-power applications, inductors with ferromagnetic cores or other specialized designs may be more suitable.
Conclusion
Air-core inductors are essential components in various electronic applications, offering low losses, high-frequency operation, and linear behavior. When designing air-core inductors, consider factors such as inductance value, winding type, wire gauge and material, quality factor, and self-resonant frequency. By understanding these design considerations and following the provided examples, you can create air-core inductors that meet your specific requirements and optimize performance in your circuits.
Remember to balance the trade-offs between size, resistance, current-carrying capacity, and other design factors to achieve the best possible results. With the knowledge gained from this comprehensive guide, you are now equipped to tackle air-core inductor design challenges and integrate these components into your electronic projects effectively.
Leave a Reply