Introduction
Flexible printed circuits, also known as flex circuits, are made from flexible polymer substrates that allow them to bend and flex. They are commonly used in electronics applications where flexibility is required, like wearables, medical devices, automotive electronics, and consumer electronics. The materials and layer stack-up used in a flex circuit design determine its electrical, mechanical, and thermal performance characteristics. This article provides an overview of common flex circuit substrate materials, cover layers, adhesives, and layer stack configurations.
Flex Circuit Substrate Materials
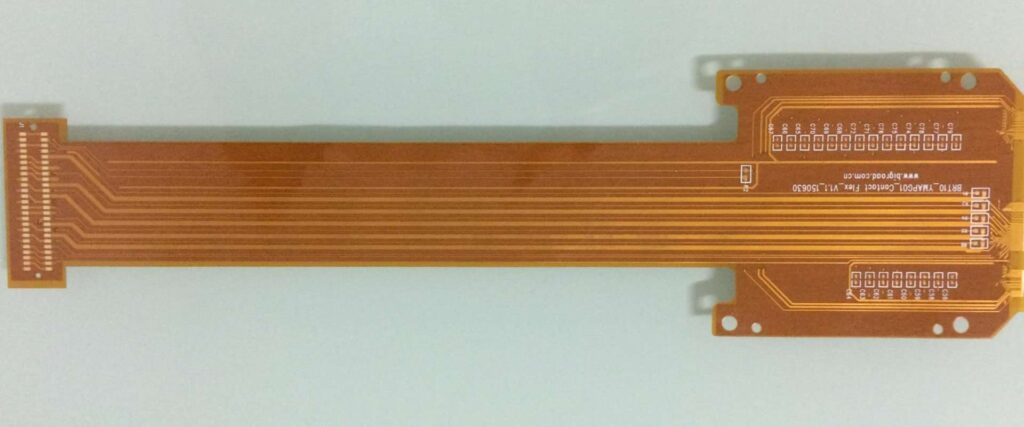
The main substrate that forms the base of the flex circuit is typically a flexible polymer film. Common materials used include:
Polyimide
Polyimide films like Kapton from DuPont are most widely used as flex circuit substrates. Polyimide offers excellent thermal stability, chemical resistance, and mechanical toughness. It has good dielectric properties and is capable of functioning across a wide temperature range. Polyimide films are available in various thicknesses down to 12 microns.
Polyester
PET (Polyethylene Terephthalate) and PEN (Polyethylene Naphthalate) are two common polyester films used for flex circuit substrates when high temperatures are not required. Polyester films provide good dielectric strength and are low-cost options, but have lower maximum operating temperatures than polyimide. Typical thicknesses range from 13-250 microns.
LCP
Liquid crystal polymer (LCP) films like Zenite offer improved thermal and chemical resistance over other polymer substrates. LCP retains its mechanical and electrical properties through 260°C. It is suitable for high-frequency and miniaturized flex circuit applications.
Fluoropolymers
PTFE (Polytetrafluoroethylene) substrates provide thermal stability up to nearly 300°C. Common trade names are Teflon and Fluon. PFA (Perfluoroalkoxy) and FEP (Fluorinated ethylene propylene) are related fluoropolymer films with slightly lower maximum temperatures but better optical clarity than PTFE.
Cover Layers
Cover layers are thin laminated sheets that provide protection and insulation to the flex circuit. Common cover layer materials include polyimide, PET, acrylic, and epoxy. Adhesives are used to bond the cover layer to the flex circuit substrate. Cover layers typically range from 12-75 microns thick. Key considerations when selecting cover layers are flexibility, bond strength, chemical resistance, thermal rating, flammability rating, and dielectric strength.
Adhesives
Adhesives play an important role in the construction of multi-layer flex circuits. Adhesives permanently bond the layers together. Key properties considered when selecting adhesives are flexibility, bond strength, thermal rating, shear strength, and viscosity.
Common adhesive types used in flex circuits include:
- Acrylic: Offer good flexibility and low temperature processing but moderate bond strength.
- Epoxy: Provide very high bond strength and good chemical resistance, but require higher curing temperatures.
- Urethane: Offer a good balance of flexibility, strength, and thermal resistance.
- Silicone: Maintain flexibility and adhesion at very high and low temperatures but have lower shear strength.
Layer Stack Configurations
The design of the layer stack, including the material thicknesses and order of layers, allows flex circuits to be tailored for specific applications. Here are some typical layer stack configurations:
Single Sided Flex Circuits
Consist of a single conductive layer bonded to a flexible substrate. The simplest and lowest cost flex circuit design.
Double Sided Flex Circuits
Have conductive layers on both sides of the substrate to allow for more connection points in a small space. Vias or plated through holes electrically connect the two side.
Multi-layer Flex Circuits
Contain three or more conductive layers separated by adhesive. Allows for high-density interconnections. Signals can pass between layers through plated through holes. Shielding layers can also be incorporated.
Rigid-Flex Circuits
Consist of flexible circuits integrated with rigid FR-4 circuit board sections to provide structural support. Allows conformal mounting to surfaces and compact 3D arrangements.
Flex Circuit Materials Summary
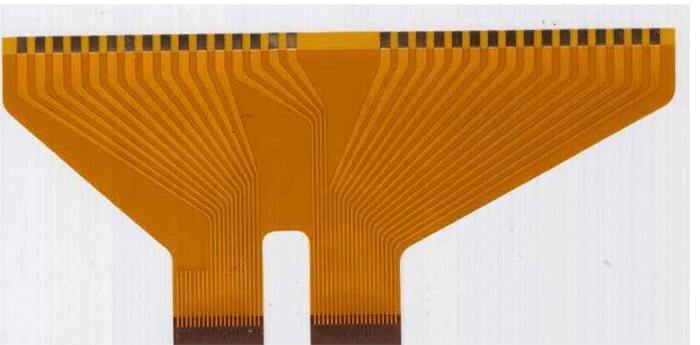
- Polymer substrates like polyimide, polyester, and LCP provide the flexible foundation.
- Cover layers add insulation and protection.
- Adhesives from acrylic to epoxy permanently laminate the layers.
- Layer stack arrangements like single sided, double sided, multilayer, and rigid-flex support functionality.
Careful selection of materials and construction is key to achieving the optimal flex circuit design for an application.
Flex Circuit Design Considerations
There are many important design factors to consider when developing a flex circuit:
Circuit Layout – The arrangement of conductors and components needs to accommodate flexibility and dynamic bending. Generally, conductors should follow directions of high flexibility and avoid areas with tight radii.
Conductor Width and Spacing – Narrower tracks allow for better flexibility and bend radii. Typical widths range from 0.07mm to 0.15mm. Adequate spacing prevents shorts during flexing.
Cover Coat Relief Cuts – Slits in the cover coat over conductors improve dynamic flex life by preventing conductor cracking.
Bond Pad Size – Large bond pads improve reliability by absorbing stress and providing more adhesion area. Typical sizes range from 0.4mm x 0.4mm to 1mm x 1mm.
Flexible Solder Mask – Solder mask coatings like LPI prevent solder bridging between pads while maintaining flexibility.
Stiffener Integration – Strategic placement of stiffeners prevents flexing in sensitive areas while allowing flexibility where needed.
Layer Stack Arrangement – Stacking order, material selection, and thickness should balance flexibility, performance, and manufacturability.
Paying attention to these design considerations will result in a flex circuit that meets the mechanical, electrical, and reliability requirements of the application.
Flex Circuit Applications
Due to their thin, lightweight, and high reliability characteristics, flex circuits are used in many advanced industries and applications:
- Consumer Electronics – Mobile phones, cameras, laptops, VR headsets
- Automotive – Sensors, lighting, engine control modules, infotainment
- Medical – Hearing aids, implants, patient monitoring devices
- Aerospace and Defense – Guidance systems, engine controls, radar
- Industrial – Robotics, automation and control systems
- Wearable Devices – Fitness trackers, smart watches, health monitors
For these and many other uses, flex circuits provide the ideal interconnect solution. Their flexibility allows reliable interconnections for dynamic and space-constrained applications.
Conclusion
Designing and constructing the optimal flex circuit requires careful selection of substrate materials, cover layers, and adhesives to match the mechanical, electrical, and thermal demands. The layer stack configuration, conductor layout, and integration of stiffeners also require engineering attention to flexibility, reliability, and manufacturability. When engineered properly, flex circuits enable miniaturized and robust interconnects for the latest electronics devices and systems.
Flex Circuit Materials and Layer Stacks – FAQ
What are the most common substrate materials used in flex circuits?
The most common flexible substrate materials are polyimide films like Kapton, polyethylene terephthalate (PET), polyethylene naphthalate (PEN), liquid crystal polymer (LCP), and fluoropolymers like PTFE and PFA. Polyimide is the most widely used due to its excellent thermal stability and mechanical properties.
What is the function of a cover layer in a flex circuit?
Cover layers provide electrical insulation, environmental protection, and mechanical support to the flex circuit. Common cover layer materials are polyimide, PET, acrylic, and epoxy. Cover layers are laminated using adhesives and are typically 12-75 microns thick.
How are layers bonded together in multi-layer flex circuits?
Adhesives permanently bond the layers together in multi-layer flex circuits. Typical adhesives used are acrylic, epoxy, urethane, and silicone. The adhesive must maintain flexibility, bond strength, and other mechanical, electrical, and thermal properties.
What are some key flex circuit design considerations?
Important design considerations include conductor layout, conductor width and spacing, cover coat relief cuts, bond pad size, flexible solder mask, stiffener integration, and layer stack arrangement. These factors need to be optimized for flexibility, durability, and manufacturability.
What industries commonly use flex circuits?
Flex circuits are widely used in consumer electronics, automotive, aerospace, medical devices, industrial, and wearable products. Their thin, lightweight, and flexible nature allows reliable interconnections in space-constrained and dynamic applications.
Leave a Reply