Introduction
A printed circuit board (PCB) is the core component of most electronic devices. It provides the mechanical structure and electrical connections between components. The way the layers in a PCB are stacked up is referred to as the PCB stackup. For simple and cost-effective boards, a 2 layer stackup is commonly used. This article will provide an overview of the common 2 layer PCB stackup, its composition, and design considerations.
Common 2 Layer PCB Stackup
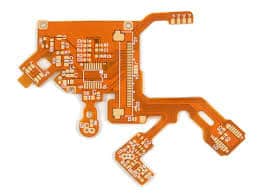
The most basic and common 2 layer PCB stackup consists of:
- Top copper layer
- Bottom copper layer
- Core dielectric substrate
This is the minimal required stackup for a functioning PCB. Here are the key characteristics of each layer:
Top and Bottom Copper Layers
The top and bottom copper layers are thin sheets of copper foil, usually around 1oz thickness (35μm). This copper foil is laminated onto the core dielectric substrate. These layers are etched to form the copper traces, pads, vias and other conductive features needed to route signals and connect components.
The top layer is also often referred to as the “component side” as this is where most components are mounted. The bottom layer may be referred to as the “solder side”.
Core Dielectric Substrate
The core substrate is an insulating dielectric material that separates the top and bottom copper layers. Some common materials used include:
- FR-4 Glass epoxy – Most common, low cost
- CEM-1 Cotton paper
- Rogers RO4003/4005 – High frequency boards
- Polyimide – Flexible boards
The core material determines important parameters like dielectric constant (Dk) which affects signal propagation and impedance, thermal conductivity, CTE (coefficient of thermal expansion) and moisture absorption. FR-4 glass epoxy is the most popular choice for its good balance of electrical and mechanical properties, availability and low cost.
The thickness of the core is typically between 0.4mm to 1.6mm for a 2 layer board. The selected thickness depends on layer count, copper weight, board stiffness and electrical considerations.
Typical Construction and Materials
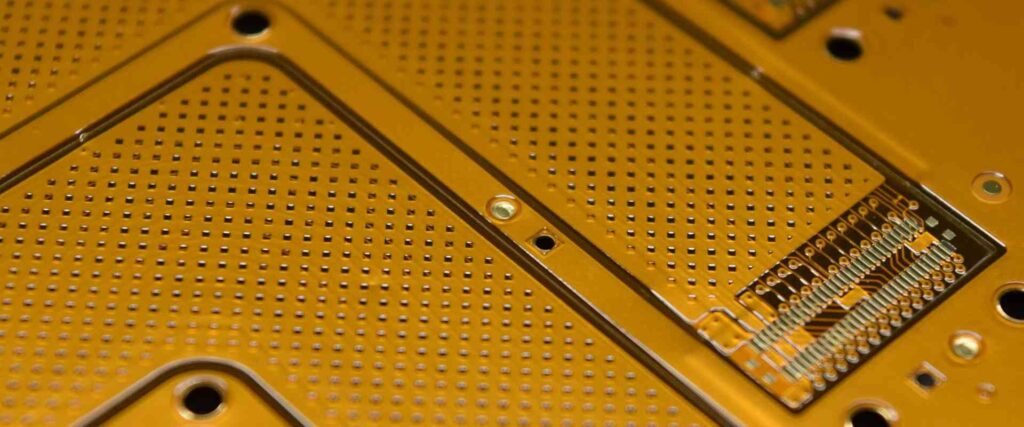
Here is a summary of the typical construction and materials used in a common 2 layer PCB stackup:
Layer | Typical Material | Thickness |
---|---|---|
Top Copper | Electrodeposited Copper Foil | 1oz (35μm) |
Core Dielectric | FR-4 Glass Epoxy | 0.8mm |
Bottom Copper | Electrodeposited Copper Foil | 1oz (35μm) |
- 1oz copper foil equals around 35μm thickness
- FR-4 glass epoxy is the most common low cost core dielectric material
- 0.8mm is a typical core thickness for a simple 2 layer board
This construction provides a robust, low cost and widely manufacturable PCB stackup. The total thickness is around 1.07mm. Other materials and thicknesses can be used depending on design requirements.
PCB Fabrication Process
The generic fabrication process for a 2 layer PCB stackup is:
- Start with a copper clad laminate – this is the dielectric core substrate with copper foil bonded to one or both sides.
- Clean and apply photoresist – The copper surfaces are prepared and a photosensitive resist coating is applied.
- Expose and develop – The resist is exposed to UV light through a mask with the circuit pattern. The resist is developed, leaving exposed copper.
- Etch – The exposed copper is etched away, leaving the desired copper pattern.
- Strip resist – The remaining photoresist is stripped away.
- Apply soldermask – A soldermask layer is applied over the entire board, leaving copper pads exposed.
- Apply legend – Silkscreen legend printing is applied for component outlines, markings, etc.
- Route/V-score – The board perimeter is routed and V-grooves added for easy separation.
- Test and inspect – 100% electrical testing and automated optical inspection.
This sequence of fabrication steps produces the finished 2 layer PCB with the required copper traces, pads, mask and markings as per the design.
Design Considerations
Here are some key considerations when designing a 2 layer PCB:
- Routing complexity – For simpler boards with less dense routing, 2 layers are often sufficient. Complex or high density designs may require more layers.
- Signal layers – With 2 layers, typically 1 layer is used for power and 1 for signals. Careful routing is needed.
- Impedance control – 2 layers makes controlled impedance routing harder. Best suited for low speed signals.
- Shielding – No internal ground or power planes. Additional shielding may be required.
- Thermal management – Only 2 layers are available for heat dissipation. Thermal vias and/or copper fills may be required.
- Board stiffness – 2 layers can result in more board flexure. Thicker cores or stiffeners may be used.
With good design practices, many boards can be implemented with just 2 layers to minimize cost. In some cases, 4 or more layers are required for high density, high speed or RF designs.
Typical Applications
Some typical applications well suited to a 2 layer PCB stackup:
- Low complexity digital boards – Microcontroller boards, sensors etc.
- Analog signal conditioning – Filtering, amplifying etc.
- Power supplies – Low/medium power, non-switching supplies.
- LED lighting drivers – Constant current LED drivers.
- Battery powered devices – Wearables, remote controls etc.
- Mechanical assemblies – Encoders, controllers, indicators etc.
Many cost-sensitive consumer electronics products leverage 2 layer boards to optimize the electronics while minimizing PCB fabrication costs.
Pros and Cons of 2 Layer Stackup
Pros | Cons |
---|---|
Low cost | Limited routing space |
Widely manufacturable | Harder impedance control |
Simpler assembly | Less noise isolation |
Thinner overall | Weaker board, more flex |
Faster design & fabrication | Higher crosstalk |
Summary
A 2 layer PCB stackup is cost effective, simple and widely manufacturable. It is well suited for lower complexity boards that do not require tightly controlled impedances or extensive shielding. With good design practices, optimal component placement and efficient routing, many boards can work well with just 2 copper layers. However, higher density or high frequency designs may require additional layers.
FQA
What are the two copper layers called in a 2 layer PCB?
The two copper layers in a 2 layer PCB stackup are referred to as the top copper layer and bottom copper layer. The top layer is also known as the component side, while the bottom is the solder side.
What is the minimum PCB layer count?
The absolute minimum layer count for a functioning PCB is 2 layers – a top and bottom copper layer separated by a dielectric core substrate. This is the most basic and lowest cost PCB stackup.
What thickness of FR4 is usually used in 2 layer PCB?
For a 2 layer PCB, the FR4 glass epoxy core substrate is typically between 0.4mm to 1.6mm thickness. A common thickness is 0.8mm as it provides a good balance of stiffness and low cost.
Is 2 layer PCB cheaper than 4 layer?
Yes, 2 layer PCBs are cheaper to manufacture than 4 layer boards, owing to fewer layers and simpler processing. However, 4 layers provide more routing space and better signal integrity.
What are some examples of 2 layer PCBs?
Some examples include Arduino boards, TV remotes, LED drivers, power supplies, battery chargers, and various consumer electronics devices. 2 layers work well for cost-sensitive, low complexity designs.
Leave a Reply