Introduction
Couplings are used to connect two shafts together while allowing for shaft misalignment and end movement or vibration. There are two main types of couplings: rigid couplings and flexible couplings. Rigid couplings like sleeve or clamp couplings provide a very stiff connection between the shafts but do not allow for any misalignment. Flexible couplings on the other hand can accommodate some degree of misalignment through the flexibility or elasticity in their design.
Flexible couplings have several advantages over rigid couplings which makes them more commonly used in many industrial applications. This article will examine these advantages in detail.
Advantages of Flexible Couplings
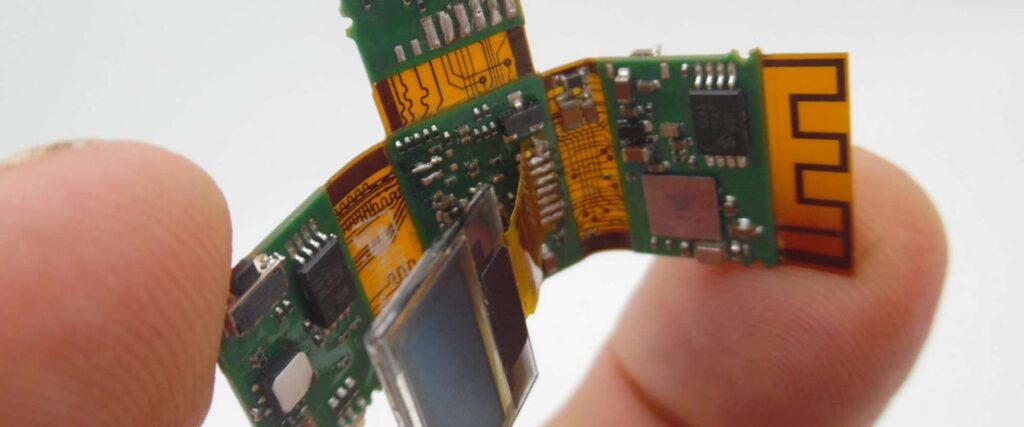
Allows for Shaft Misalignment
One of the main advantages of flexible couplings is their ability to accommodate misalignment between the connected shafts. There are several types of misalignment – parallel offset, angular misalignment and axial displacement.
Flexible couplings can compensate for these through flexing of their elastic components. Common flexible coupling designs like gear couplings, grid couplings and disc couplings allow for both parallel and angular misalignment. Bellows type flexible couplings can also accommodate axial displacement between shafts.
This ability to accommodate misalignment reduces loads and stresses on the coupling and connected machinery. It also reduces bearing wear in the equipment compared to rigid couplings.
Absorbs Shock Loads and Vibration
Another major advantage of flexible couplings is their ability to dampen shock loads and vibration from the driving or driven equipment.
The flexible components in the coupling act as shock absorbers and isolate the vibration of one shaft from the other. This protects the equipment from damage due to sudden shock loads.
Common applications where shock absorption is important include reciprocating pumps, compressors, punch presses, shredders etc. Flexible couplings in these applications allow for smoother operation.
Low Reaction Forces on Bearings
With rigid couplings, any shaft misalignment produces very high reaction forces which act on the shaft and their support bearings. This can lead to reduced bearing life.
Flexible couplings on the other hand produce very low reaction forces for the same misalignment due to the flexing in their components. This results in lower loads on bearings so that their life is increased.
Allows for End Movement
Some flexible couplings like bellows type or tyre type flexible couplings allow for small end movements or displacements between the shafts.
This enables their use in applications where thermal expansion or contraction of the shafts occurs during operations. The coupling can accommodate the changes in shaft length without creating high stresses.
Easy Installation
Flexible couplings offer greater tolerance to imperfect alignment while installing coupled machinery. Special foundations, precision alignment etc. are not required as the coupling can accommodate minor alignment errors. This reduces the installation time and cost.
Less Maintenance
The flexible coupling components generally have no lubrication needs and require very little maintenance over their service life. Only occasional inspection of the flexible elements is required to check for wear or fatigue. This reduces maintenance costs.
Rigid couplings on the other hand may require more frequent lubrication and inspections. There is also greater potential for damage if they are overloaded due to vibration or shock loads.
Disadvantages of Flexible Couplings
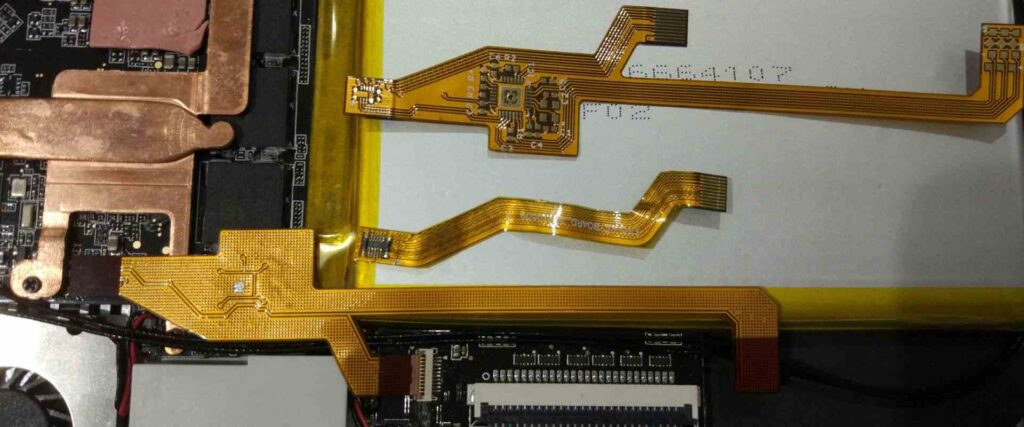
While flexible couplings have numerous advantages, they also have some disadvantages compared to rigid couplings:
- Have lower torque ratings than rigid couplings of the same size.
- Generate more heat than rigid couplings under the same operating conditions due to internal friction and flexing actions. Additional cooling may be required.
- More expensive than rigid couplings in most cases.
- May need to be replaced more often than rigid couplings due to wearing out of flexible components.
- Not suitable for applications requiring very precise shaft alignment.
Types of Flexible Couplings
Some common types of flexible couplings include:
Gear Couplings
- Consist of two hubs with exterior teeth that mesh with a gear or spline.
- Allow angular and parallel shaft offset.
- Well-suited for high speeds and loads.
Grid Couplings
- Have two disengaged sleeves connected by an elastic grid of rubber or metal.
- Accommodate angular, parallel and axial shaft misalignment.
- Offer vibration damping.
Bellows Couplings
- Have bellows as the flexible member.
- Absorb high levels of misalignment and end thrust.
- Used in applications with large temperature variations.
Disc Couplings
- Designed as sets of thin circular discs layered between driving and driven hubs.
- Allow for angular misalignment and parallel offset.
- Well suited for high speed applications.
Tyre Couplings
- Use rubber tyres as the flexible component.
- Permit small end movements and shock absorption.
- Ideal for applications with extreme misalignment.
Applications of Flexible Couplings
Flexible couplings are used in a wide range of shaft coupling applications across all industries. Some typical applications include:
- Connecting motor shaft to pump shafts
- Coupling gearbox shafts to conveyor shafts
- Connecting drive shafts to agitator shafts in mixers
- Coupling shafts in large generators and turbines
- Linking drive shafts to fan shafts in HVAC applications
- Connecting shafts in machine tools, paper mills, rolling mills etc.
- Coupling shafts in marine propulsion systems
In most rotating machinery applications, flexible couplings are preferred over rigid couplings due to their ability to accommodate misalignment and absorb shock loads. They protect the equipment, allow smoother operation and require less maintenance.
Frequently Asked Questions
What is the main difference between rigid and flexible couplings?
The main difference is that rigid couplings do not allow for any shaft misalignment whereas flexible couplings can accommodate angular, parallel and axial misalignment through flexing of their elastic components.
When should rigid couplings be used instead of flexible ones?
Rigid couplings would be preferred in applications requiring very precise shaft alignment or positioning. They can also safely transmit higher torques than flexible couplings of the same size.
How are flexible couplings maintained?
Flexible couplings require little maintenance – usually just routine inspection of the flexible elements for signs of fatigue or damage. Lubrication is generally not required. Alignment should be checked periodically if misalignment is suspected.
What causes a flexible coupling to fail?
Common failure causes are excessive misalignment beyond the coupling’s ratings, high vibration, overload conditions, heat buildup, corroded fasteners, and exceeding service life of the flexible components.
Can flexible couplings be used at very high speeds?
Yes, many flexible coupling designs are suitable for high speed applications above 10,000 rpm. Gear, grid and disc couplings are commonly used at high speeds. Care must be taken to select a coupling rated for the speed and service conditions.
Leave a Reply