Introduction to Flexible PCBs
Flexible printed circuit boards (PCBs) have revolutionized the electronics industry with their unique characteristics and versatile applications. Unlike traditional rigid PCBs, flexible PCBs can bend, twist, and conform to various shapes, making them ideal for compact and complex electronic devices. This article will explore the key characteristics of flexible PCBs that contribute to their growing popularity in various industries.
What is a Flexible PCB?
A flexible PCB, also known as a flex circuit, is a type of printed circuit board that consists of a thin, flexible substrate made of materials such as polyimide or polyester. Conductive traces, typically made of copper, are printed or etched onto the substrate to create the desired circuit pattern. Flexible PCBs can be single-sided, double-sided, or multi-layered, depending on the complexity of the design and the application requirements.
Types of Flexible PCBs
There are several types of flexible PCBs, each with its own unique characteristics and applications:
- Single-sided flexible PCBs
- Double-sided flexible PCBs
- Multi-layer flexible PCBs
- Rigid-flex PCBs
Type | Description |
---|---|
Single-sided flexible PCBs | These PCBs have conductive traces on only one side of the flexible substrate. They are the simplest and most cost-effective type of flexible PCB. |
Double-sided flexible PCBs | These PCBs have conductive traces on both sides of the flexible substrate, allowing for more complex circuit designs and higher component density. |
Multi-layer flexible PCBs | These PCBs consist of multiple layers of flexible substrates with conductive traces, separated by insulating layers. They offer the highest complexity and density. |
Rigid-flex PCBs | These PCBs combine both rigid and flexible sections, allowing for the integration of rigid components with flexible interconnects. |
Characteristics of Flexible PCBs
Flexibility and Bendability
One of the most significant characteristics of flexible PCBs is their ability to bend and flex without damaging the circuit or components. This flexibility allows for the design of compact and space-saving electronic devices, as the PCB can be folded, twisted, or wrapped around components. The degree of flexibility depends on factors such as the substrate material, thickness, and the number of layers.
Bend Radius
The bend radius is a critical parameter in flexible PCB design, as it determines the minimum radius at which the PCB can be bent without causing damage or affecting its performance. The bend radius depends on the thickness of the substrate and the number of layers in the PCB. Typical bend radii for flexible PCBs range from 1-10 times the thickness of the board.
Substrate Thickness (mm) | Single Bend Radius (mm) | Dynamic Bend Radius (mm) |
---|---|---|
0.05 | 0.5 | 1.0 |
0.075 | 0.75 | 1.5 |
0.1 | 1.0 | 2.0 |
0.15 | 1.5 | 3.0 |
0.2 | 2.0 | 4.0 |
Lightweight and Thin Profile
Flexible PCBs are known for their lightweight and thin profile, making them ideal for applications where weight and space are critical factors. The thin substrate materials used in flex circuits, such as polyimide, allow for the fabrication of PCBs as thin as 0.05mm. This characteristic enables the design of compact and portable electronic devices, such as smartphones, wearables, and medical implants.
High Reliability and Durability
Despite their thin and flexible nature, flexible PCBs offer high reliability and durability. The materials used in flex circuits, such as polyimide, have excellent thermal stability, chemical resistance, and mechanical strength. Flexible PCBs can withstand repeated bending and flexing without losing their electrical integrity, making them suitable for applications that require continuous motion or exposure to harsh environments.
Flex Life
Flex life refers to the number of bending cycles a flexible PCB can endure before failing. The flex life of a PCB depends on factors such as the substrate material, copper thickness, and the bend radius. Typical flex life values for flexible PCBs range from 10,000 to over 1,000,000 cycles, depending on the application and design requirements.
Bend Radius (mm) | Copper Thickness (µm) | Flex Life (Cycles) |
---|---|---|
5 | 18 | 100,000 |
5 | 35 | 50,000 |
10 | 18 | 500,000 |
10 | 35 | 200,000 |
High-Density Interconnects
Flexible PCBs allow for high-density interconnects, enabling the integration of a large number of components and circuits in a small space. The thin substrate and fine-pitch traces in flex circuits facilitate the design of complex and compact electronic assemblies. High-density interconnects in flexible PCBs are crucial for applications that require miniaturization, such as implantable medical devices, aerospace systems, and advanced consumer electronics.
Thermal Management
Flexible PCBs offer excellent thermal management properties, as the thin substrate materials have low thermal resistance and can efficiently dissipate heat. The ability to conform to various shapes also allows for better heat distribution and cooling, as the PCB can be placed in close contact with heat sinks or other cooling solutions. Effective thermal management is essential for ensuring the reliability and performance of electronic devices, particularly in high-power or high-density applications.
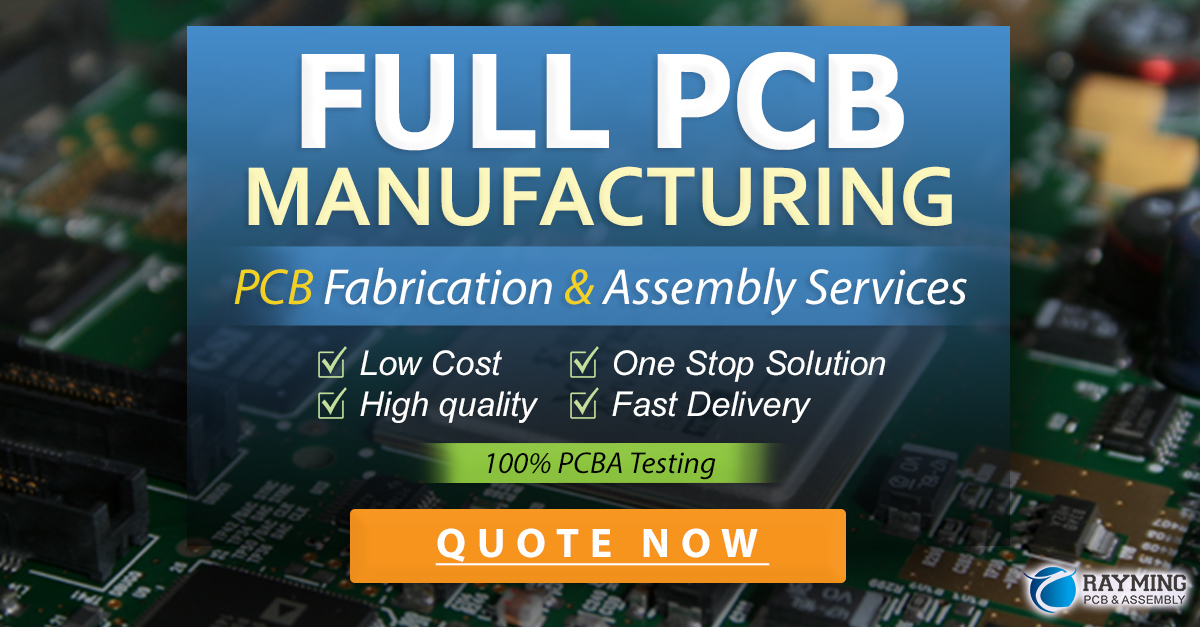
Applications of Flexible PCBs
Consumer Electronics
Flexible PCBs are widely used in consumer electronics, such as smartphones, tablets, laptops, and wearables. The flexibility and thin profile of flex circuits enable the design of slim and compact devices with advanced features and functionality. Flexible PCBs also allow for the integration of various sensors, displays, and input devices, enhancing the user experience and enabling new form factors.
Medical Devices
Flexible PCBs have found extensive applications in medical devices, particularly in implantable and wearable systems. The biocompatibility, flexibility, and high reliability of flex circuits make them suitable for use in pacemakers, cochlear implants, insulin pumps, and other medical implants. Flexible PCBs also enable the development of wearable health monitoring devices, such as smart bandages, ECG sensors, and continuous glucose monitors.
Automotive Electronics
The automotive industry has increasingly adopted flexible PCBs for various applications, such as instrument clusters, infotainment systems, and advanced driver assistance systems (ADAS). Flex circuits offer the ability to integrate complex electronics into confined spaces, such as steering wheels, door panels, and headliners. The high reliability and durability of flexible PCBs also make them suitable for use in harsh automotive environments, where they are exposed to vibration, temperature extremes, and chemical contaminants.
Aerospace and Defense
Flexible PCBs are essential components in aerospace and defense applications, where weight reduction, space savings, and high reliability are critical. Flex circuits are used in avionics systems, satellite communications, radar systems, and military wearables. The ability to conform to complex shapes and withstand extreme environmental conditions makes flexible PCBs ideal for use in aircraft, spacecraft, and military vehicles.
Advantages of Flexible PCBs
- Space savings and miniaturization
- Reduced weight and improved portability
- Enhanced reliability and durability
- Improved electrical performance
- Increased design flexibility and innovation
- Cost-effective for high-volume production
Challenges and Considerations
- Design complexity and layout constraints
- Material selection and compatibility
- Manufacturing process and quality control
- Assembly and interconnection methods
- Testing and inspection techniques
- Environmental factors and reliability testing
Future Trends and Developments
- Advanced materials and substrates
- Increased integration of sensors and electronics
- 3D printing and additive manufacturing techniques
- Flexible hybrid electronics (FHE)
- Wearable and implantable electronics
- IoT and smart connected devices
Frequently Asked Questions (FAQ)
1. What is the difference between a flexible PCB and a rigid PCB?
A flexible PCB is made of a thin, flexible substrate material that allows it to bend and conform to various shapes, while a rigid PCB is made of a solid, non-flexible substrate material, such as FR-4. Flexible PCBs offer advantages in terms of space savings, weight reduction, and design flexibility, while rigid PCBs provide better mechanical stability and are suitable for applications that do not require flexibility.
2. Can flexible PCBs be used in high-temperature environments?
Yes, flexible PCBs can be designed to withstand high-temperature environments. The key is to select the appropriate substrate material, such as polyimide, which has excellent thermal stability and can maintain its mechanical and electrical properties at elevated temperatures. Proper design considerations, such as copper thickness and trace routing, also play a role in ensuring the reliable performance of flexible PCBs in high-temperature applications.
3. How do I choose the right substrate material for my flexible PCB?
The choice of substrate material for a flexible PCB depends on several factors, including the application requirements, operating environment, and budget. Common substrate materials for flexible PCBs include polyimide, polyester, and fluoropolymers. Polyimide is the most widely used substrate material due to its excellent thermal, mechanical, and electrical properties. Polyester is a lower-cost alternative for less demanding applications, while fluoropolymers offer superior chemical resistance and low dielectric constant.
4. What are the common methods for assembling components on flexible PCBs?
The most common methods for assembling components on flexible PCBs are surface mount technology (SMT) and chip-on-flex (COF). SMT involves soldering components directly onto the surface of the flexible PCB, using techniques such as reflow soldering or wave soldering. COF, also known as chip-on-film, is a process where bare die or flip-chip components are directly bonded onto the flexible substrate, eliminating the need for a separate package.
5. How can I ensure the reliability of my flexible PCB design?
To ensure the reliability of your flexible PCB design, consider the following factors:
- Material selection: Choose substrate materials and copper thicknesses that are suitable for your application and operating environment.
- Bend radius: Ensure that the bend radius of your flexible PCB is within the recommended range to prevent damage and maintain electrical integrity.
- Strain relief: Incorporate strain relief features, such as stiffeners or adhesives, to minimize stress on the components and interconnects during bending.
- Layout optimization: Follow best practices for flexible PCB layout, such as avoiding sharp bends, minimizing copper thickness in bend areas, and using tear-drop pads.
- Testing and validation: Perform thorough testing and validation, including environmental testing, flex life testing, and electrical characterization, to ensure the reliability and performance of your flexible PCB design.
Conclusion
Flexible PCBs have become increasingly popular in various industries due to their unique characteristics, such as flexibility, lightweight, thin profile, high reliability, and high-density interconnects. These characteristics enable the design of compact, portable, and innovative electronic devices across a wide range of applications, from consumer electronics to medical devices, automotive systems, and aerospace and defense.
As technology advances and the demand for smaller, smarter, and more connected devices grows, flexible PCBs will continue to play a crucial role in shaping the future of electronics. With ongoing developments in materials, manufacturing processes, and design techniques, flexible PCBs are poised to enable new possibilities and drive innovation in the ever-evolving world of electronics.
Leave a Reply