What is Electronics Environmental Testing?
Electronics Environmental Testing, also known as environmental stress screening or ESS, refers to the process of subjecting electronic devices, components, and systems to controlled environmental conditions to assess their performance, reliability, and durability. The primary objective of environmental testing is to identify potential failures or weaknesses in the design, manufacturing, or materials used in electronic products before they are released to the market.
Environmental testing simulates the various environmental factors that an electronic device may encounter during its lifecycle, such as temperature, humidity, vibration, shock, altitude, and electromagnetic interference. By exposing the device to these stresses in a controlled laboratory setting, manufacturers can ensure that their products meet the required standards and specifications, and can withstand the rigors of real-world use.
Categories of Electronics Environmental Testing
Electronics Environmental Testing can be broadly categorized into two main types:
-
Qualification Testing: This type of testing is performed to verify that a product meets the specified requirements and standards. Qualification testing is usually done on a sample of products before mass production begins. The purpose is to ensure that the design and manufacturing processes are capable of producing products that meet the desired quality and reliability levels.
-
Reliability Testing: This type of testing is conducted to determine the expected lifetime and failure rates of a product under normal operating conditions. Reliability testing involves subjecting the product to various environmental stresses over an extended period to simulate real-world usage. The data collected from these tests can be used to estimate the product’s mean time between failures (MTBF) and other reliability metrics.
Different Types of Electronics Environmental Tests
There are several types of environmental tests that electronic products may undergo, depending on their intended application and the environmental conditions they are expected to encounter. Some of the most common types of tests include:
Temperature Testing
Temperature testing involves subjecting the device to extreme high and low temperatures to evaluate its performance and reliability. The tests can be conducted in a temperature-controlled chamber, where the device is exposed to a range of temperatures for a specified duration. The purpose of temperature testing is to ensure that the device can function correctly and safely within its specified temperature range.
Test Type | Temperature Range | Duration |
---|---|---|
High Temperature Operating Life (HTOL) | +85°C to +150°C | 500 to 1000 hours |
Low Temperature Operating Life (LTOL) | -40°C to -65°C | 500 to 1000 hours |
Thermal Cycling | -65°C to +150°C | 500 to 1000 cycles |
Thermal Shock | -65°C to +150°C | 10 to 100 cycles |
Humidity Testing
Humidity testing evaluates the device’s ability to withstand exposure to high levels of humidity without experiencing corrosion, electrical shorts, or other failures. The tests are typically conducted in a humidity chamber, where the device is subjected to a controlled level of humidity for a specified duration.
Test Type | Humidity Range | Temperature Range | Duration |
---|---|---|---|
Steady State Humidity | 85% to 95% RH | +30°C to +85°C | 500 to 1000 hours |
Cyclic Humidity | 65% to 95% RH | +25°C to +65°C | 500 to 1000 cycles |
Vibration Testing
Vibration testing assesses the device’s ability to withstand mechanical vibrations during transportation, handling, and use. The tests are conducted on a vibration table, where the device is subjected to controlled levels of vibration at various frequencies and amplitudes.
Test Type | Frequency Range | Amplitude | Duration |
---|---|---|---|
Sinusoidal Vibration | 10 Hz to 2000 Hz | 1 to 50 g | 1 to 24 hours |
Random Vibration | 20 Hz to 2000 Hz | 0.01 to 0.1 g²/Hz | 1 to 24 hours |
Shock Testing
Shock testing evaluates the device’s ability to withstand sudden, high-level mechanical shocks, such as those experienced during drops or impacts. The tests are conducted using a drop tester or shock machine, where the device is subjected to controlled levels of acceleration for a short duration.
Test Type | Peak Acceleration | Duration | Number of Shocks |
---|---|---|---|
Half Sine Shock | 50 to 5000 g | 0.5 to 20 ms | 1 to 10 |
Trapezoidal Shock | 20 to 100 g | 6 to 11 ms | 1 to 10 |
Altitude Testing
Altitude testing assesses the device’s ability to operate correctly at high altitudes, where the air pressure and density are lower than at sea level. The tests are conducted in a vacuum chamber, where the device is subjected to controlled levels of low pressure for a specified duration.
Test Type | Altitude Range | Duration |
---|---|---|
Operating Altitude | 0 to 30,000 ft | 1 to 24 hours |
Non-operating Altitude | 0 to 50,000 ft | 1 to 24 hours |
Electromagnetic Compatibility (EMC) Testing
EMC testing evaluates the device’s ability to operate correctly in the presence of electromagnetic interference (EMI) and to not generate EMI that could affect other devices. The tests are conducted in an EMC chamber, where the device is subjected to controlled levels of electromagnetic fields at various frequencies.
Test Type | Frequency Range | Field Strength |
---|---|---|
Radiated Emissions | 30 MHz to 1 GHz | 30 to 1000 V/m |
Conducted Emissions | 150 kHz to 30 MHz | 66 to 56 dBμV |
Radiated Immunity | 80 MHz to 6 GHz | 1 to 30 V/m |
Conducted Immunity | 150 kHz to 80 MHz | 1 to 30 V |
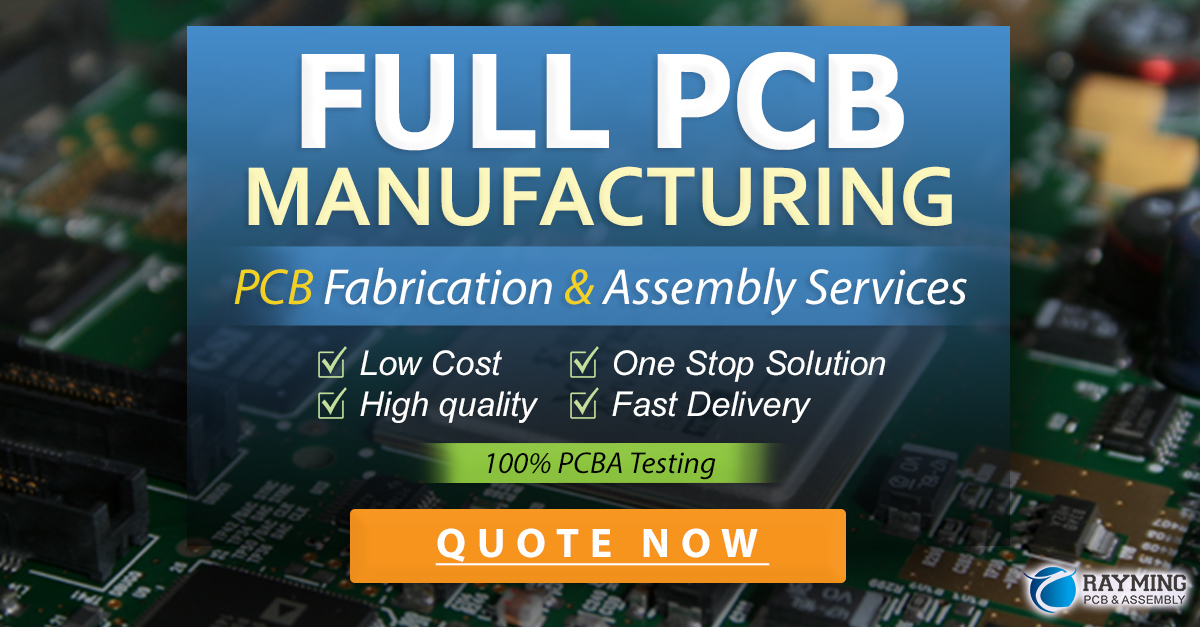
FAQ
-
Q: Why is electronics environmental testing important?
A: Electronics environmental testing is crucial to ensure that electronic devices and systems can function reliably and safely under the environmental conditions they are expected to encounter during their lifecycle. By identifying potential issues early in the development process, manufacturers can avoid costly failures and recalls after the product is released to the market. -
Q: What are the benefits of conducting environmental testing?
A: The benefits of conducting environmental testing include improved product reliability, reduced warranty claims and field failures, increased customer satisfaction, and compliance with industry standards and regulations. Environmental testing also helps manufacturers optimize their designs and manufacturing processes, leading to cost savings and faster time-to-market. -
Q: How long does an environmental test typically take?
A: The duration of an environmental test varies depending on the type of test, the product being tested, and the specific requirements of the manufacturer or customer. Some tests, such as temperature and humidity testing, can take several weeks or months to complete, while others, such as shock and vibration testing, may only take a few hours or days. -
Q: Can environmental testing guarantee that a product will never fail?
A: While environmental testing can significantly reduce the risk of product failures, it cannot guarantee that a product will never fail. There are always inherent uncertainties and variabilities in the manufacturing process, material properties, and user behavior that can lead to unexpected failures. However, by conducting thorough environmental testing and following best practices in design and manufacturing, manufacturers can minimize the likelihood of failures and ensure that their products meet the required quality and reliability standards. -
Q: What are the industry standards for electronics environmental testing?
A: There are several industry standards that specify the requirements and methods for electronics environmental testing, depending on the application and market. Some of the most common standards include: - MIL-STD-810: Environmental Engineering Considerations and Laboratory Tests (U.S. Military)
- IEC 60068: Environmental Testing (International Electrotechnical Commission)
- JEDEC JESD22: Reliability Test Methods for Packaged Devices (Joint Electron Device Engineering Council)
- RTCA DO-160: Environmental Conditions and Test Procedures for Airborne Equipment (Radio Technical Commission for Aeronautics)
- SAE J1455: Recommended Environmental Practices for Electronic Equipment Design in Heavy-Duty Vehicle Applications (Society of Automotive Engineers)
Manufacturers should consult the relevant standards and regulations for their specific industry and market to ensure compliance and optimal product performance.
Leave a Reply