What is an SMT Stencil?
An SMT stencil is a thin metal sheet, typically made of stainless steel or nickel, with laser-cut apertures that correspond to the pads on a PCB. The thickness of the stencil can vary depending on the specific application and the size of the components being used. The most common thicknesses range from 0.004 inches (0.1 mm) to 0.008 inches (0.2 mm).
The primary purpose of an SMT stencil is to ensure accurate and consistent solder paste deposition on the PCB pads. By using a stencil, manufacturers can control the amount of solder paste applied to each pad, which is crucial for achieving reliable solder joints and preventing defects such as bridging or insufficient solder.
Types of SMT Stencils
There are two main types of SMT stencils: framed and frameless.
Framed Stencils
Framed stencils are mounted on a rigid frame, typically made of aluminum or stainless steel. The frame provides stability and allows for easy handling and placement on the PCB. Framed stencils are more durable and less prone to damage compared to frameless stencils. They are commonly used in high-volume production environments where the stencil needs to withstand repeated use and cleaning.
Frameless Stencils
Frameless stencils, also known as foil stencils, are not mounted on a frame. Instead, they are placed directly on the PCB and held in place by the solder paste printer’s clamping mechanism. Frameless stencils are thinner and more flexible than framed stencils, making them suitable for applications with fine-pitch components or tight tolerances. They are also less expensive and easier to store than framed stencils.
SMT Stencil Materials
SMT stencils can be made from various materials, each with its own advantages and disadvantages. The most common materials are stainless steel and nickel.
Stainless Steel Stencils
Stainless steel is the most widely used material for SMT stencils due to its durability, stability, and cost-effectiveness. Stainless steel stencils are suitable for a wide range of applications and can withstand repeated use and cleaning without deteriorating. However, they are prone to rust if not properly maintained and may require additional coatings to improve solder paste release.
Nickel Stencils
Nickel stencils are becoming increasingly popular in the SMT industry due to their excellent solder paste release properties and resistance to corrosion. Nickel has a lower surface energy than stainless steel, which means that solder paste is less likely to stick to the stencil apertures, resulting in cleaner and more consistent paste deposits. Nickel stencils are also more durable than stainless steel and can last longer in production. However, they are more expensive than stainless steel stencils.
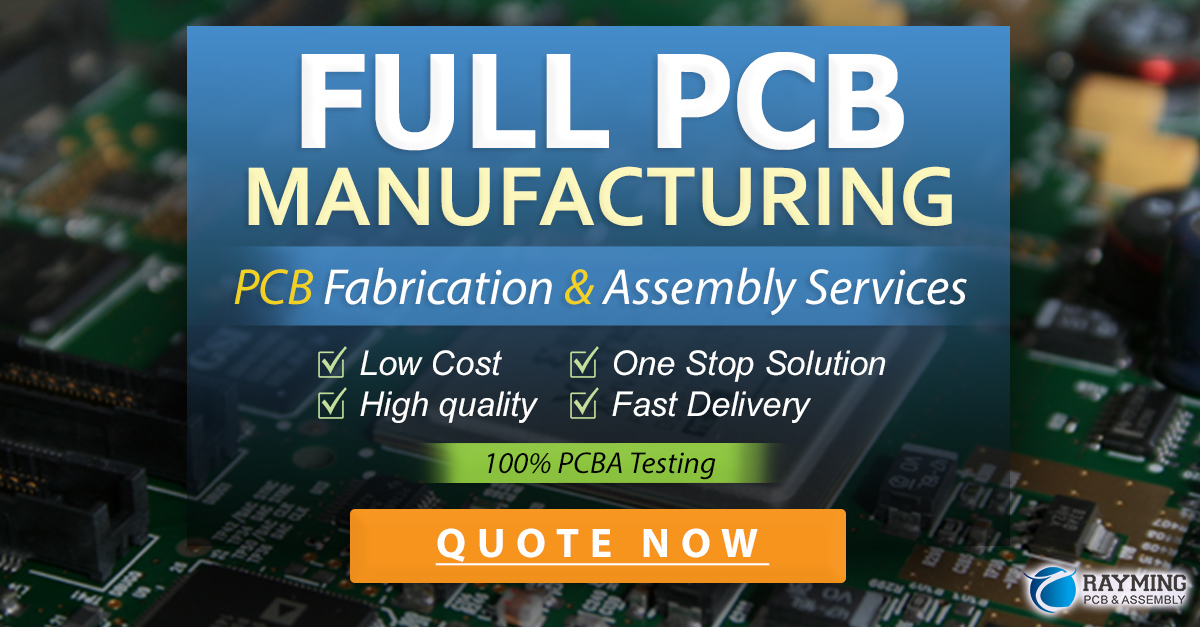
Advantages of Using SMT Stencils
Using SMT stencils in the SMT assembly process offers several key advantages:
-
Precise solder paste deposition: SMT stencils ensure accurate and consistent solder paste deposition on PCB pads, which is essential for achieving reliable solder joints and preventing defects.
-
Increased efficiency: By using a stencil, manufacturers can apply solder paste to multiple PCBs simultaneously, reducing the time and labor required for manual solder paste application.
-
Improved quality: Consistent solder paste deposition leads to higher-quality solder joints, reducing the risk of defects and improving the overall reliability of the assembled PCBs.
-
Cost savings: SMT stencils help minimize solder paste waste and reduce the need for rework and repairs, resulting in cost savings for manufacturers.
Stencil Design Considerations
When designing an SMT stencil, several factors must be considered to ensure optimal performance:
-
Aperture size and shape: The size and shape of the stencil apertures should match the size and shape of the PCB pads. Aperture sizes are typically 1:1 with the pad size, but can be adjusted based on the specific requirements of the application.
-
Stencil thickness: The thickness of the stencil determines the amount of solder paste deposited on the pads. Thicker stencils deposit more paste, while thinner stencils deposit less. The optimal thickness depends on the size of the components and the desired solder joint profile.
-
Aperture wall angle: The angle of the aperture walls affects the release of the solder paste from the stencil. A wall angle of 5 to 7 degrees is typically recommended for optimal paste release.
-
Aperture aspect ratio: The aspect ratio is the relationship between the aperture width and the stencil thickness. A minimum aspect ratio of 1.5 is recommended to ensure proper solder paste release and to prevent bridging.
Stencil Maintenance and Cleaning
Proper maintenance and cleaning of SMT stencils are essential for ensuring consistent performance and longevity. Solder paste residue can accumulate on the stencil over time, clogging apertures and affecting paste release. Regular cleaning using specialized stencil cleaning solutions and equipment is necessary to remove residue and prevent buildup.
Stencils should also be inspected regularly for damage, such as bent or warped areas, and replaced as needed to maintain optimal performance.
Frequently Asked Questions (FAQ)
1. How often should I clean my SMT stencil?
It is recommended to clean your SMT stencil after every shift or every 4-8 hours of continuous use, depending on the volume of production and the type of solder paste being used. Regular cleaning helps prevent solder paste buildup and ensures consistent performance.
2. Can I reuse my SMT stencil for different PCB designs?
While it is possible to reuse an SMT stencil for different PCB designs, it is not recommended. Each stencil is designed specifically for a particular PCB layout, and using it for a different design can result in improper solder paste deposition and defects. It is best to use a new stencil for each unique PCB design.
3. How long does an SMT stencil typically last?
The lifespan of an SMT stencil depends on various factors, such as the material, thickness, and frequency of use. On average, a well-maintained stencil can last for 5,000 to 10,000 prints before needing to be replaced. However, this can vary widely depending on the specific application and maintenance practices.
4. What is the difference between a step stencil and a standard stencil?
A step stencil, also known as a multi-level stencil, has different thicknesses in different areas of the stencil to accommodate components of varying heights on a single PCB. This allows for optimal solder paste deposition on both small and large components. In contrast, a standard stencil has a uniform thickness throughout.
5. Can I use the same SMT stencil for different solder paste types?
It is generally recommended to use a separate stencil for each type of solder paste to avoid cross-contamination and ensure optimal performance. Different solder paste formulations may have different rheological properties, which can affect how they interact with the stencil apertures and release onto the PCB pads.
Conclusion
SMT stencils are a critical component of the SMT assembly process, ensuring precise and consistent solder paste deposition on PCB pads. By understanding the types, materials, and design considerations of SMT stencils, manufacturers can optimize their assembly processes, improve PCB quality, and reduce costs.
Investing in high-quality SMT stencils and implementing proper maintenance and cleaning practices are essential for achieving reliable and efficient SMT assembly. As the electronics industry continues to evolve, with smaller components and more complex PCB designs, the importance of SMT stencils will only continue to grow.
Leave a Reply