1. Solder Bridges
Solder bridges are unintended connections between two or more solder joints, causing short circuits and potential component damage. They can occur due to excessive solder paste application, improper component placement, or inadequate solder mask design.
Prevention Methods
Method | Description |
---|---|
Solder Paste Optimization | Ensure the correct solder paste viscosity, particle size, and application technique to prevent excessive solder deposition. |
Proper Component Placement | Use precise pick-and-place machines and vision systems to ensure accurate component placement and alignment. |
Solder Mask Design | Design solder mask openings with adequate spacing and clearance to prevent solder bridging between adjacent pads. |
2. Cold Solder Joints
Cold solder joints are weak, brittle connections that result from insufficient heat during the soldering process. They can cause intermittent electrical connections, reduced mechanical strength, and premature joint failure.
Prevention Methods
Method | Description |
---|---|
Temperature Control | Maintain proper soldering iron temperature and preheat settings to ensure adequate heat transfer to the solder joint. |
Soldering Technique | Use the correct soldering technique, such as proper tip size, dwell time, and solder wire feed rate. |
Flux Selection | Choose the appropriate flux type and activity level to promote solder wetting and minimize oxidation. |
3. Tombstoning
Tombstoning, also known as “drawbridging,” occurs when a surface-mount component stands up on one end due to uneven solder joint formation. This can happen when there is a mismatch in solder paste volume or heating between the component pads.
Prevention Methods
Method | Description |
---|---|
Pad Design | Ensure that component pads are symmetrical and have equal thermal mass to promote even solder joint formation. |
Reflow Profile Optimization | Optimize the reflow oven temperature profile to achieve uniform heating and solder melting across the board. |
Component Placement Accuracy | Use high-precision pick-and-place machines to ensure accurate component placement and alignment. |
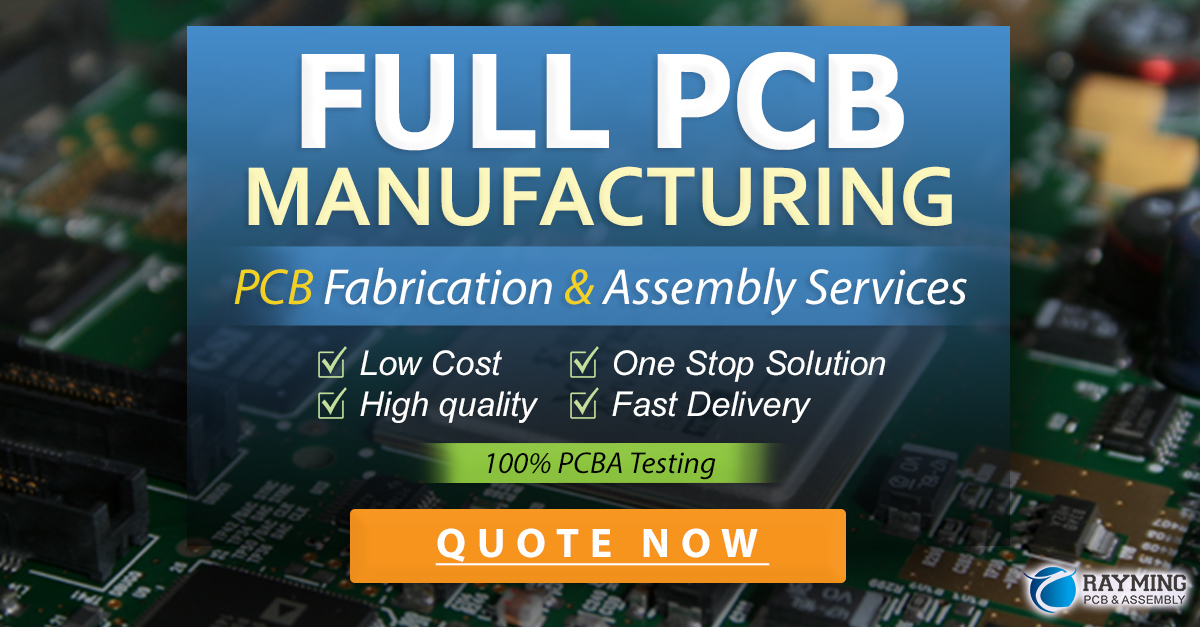
4. Lifted Pads
Lifted pads occur when the copper pad separates from the PCB substrate due to excessive mechanical stress or improper bonding. This can lead to broken connections and component detachment.
Prevention Methods
Method | Description |
---|---|
Laminate Selection | Choose a high-quality PCB laminate with good adhesion properties and thermal stability. |
Controlled Impedance Design | Ensure proper controlled impedance design to minimize mechanical stress on the pads during assembly and operation. |
Gentle Handling | Handle PCBs with care during assembly, avoiding excessive bending, twisting, or impact. |
5. Insufficient Solder
Insufficient solder occurs when there is not enough solder to form a robust and reliable connection between the component and the PCB pad. This can result in weak joints, poor electrical conductivity, and reduced mechanical strength.
Prevention Methods
Method | Description |
---|---|
Solder Paste Stencil Design | Optimize the solder paste stencil aperture size and shape to ensure adequate solder paste deposition on the pads. |
Solder Paste Inspection | Implement solder paste inspection (SPI) to verify the presence, volume, and consistency of solder paste on the pads before component placement. |
Reflow Profile Monitoring | Monitor and control the reflow oven temperature profile to ensure proper solder melting and wetting. |
6. Solder Balls
Solder balls are small, spherical solder particles that can form during the reflow process and cause short circuits or other reliability issues. They can occur due to excessive solder paste, contamination, or improper reflow conditions.
Prevention Methods
Method | Description |
---|---|
Solder Paste Quality Control | Ensure the use of high-quality solder paste with the correct particle size and minimal contamination. |
Reflow Atmosphere Control | Maintain a clean and controlled reflow oven atmosphere to prevent oxidation and solder balling. |
Cleaning and Maintenance | Regularly clean and maintain the stencils, pick-and-place nozzles, and conveyor systems to minimize contamination. |
7. Component Misalignment
Component misalignment refers to the incorrect placement or orientation of components on the PCB, leading to poor connections, reduced functionality, or assembly defects.
Prevention Methods
Method | Description |
---|---|
Vision Systems | Implement advanced vision systems to verify component placement accuracy and alignment before soldering. |
Pick-and-Place Calibration | Regularly calibrate and maintain pick-and-place machines to ensure consistent and precise component placement. |
Fiducial Markers | Use fiducial markers on the PCB to provide reference points for accurate component positioning. |
8. Flux Residue
Flux residue is the remaining non-conductive material left on the PCB after the soldering process. Excessive or corrosive flux residue can cause surface contamination, electrical leakage, or long-term reliability issues.
Prevention Methods
Method | Description |
---|---|
Flux Selection | Choose a no-clean or low-residue flux that is compatible with the solder paste and PCB surface finish. |
Reflow Profile Optimization | Optimize the reflow oven temperature profile to ensure complete flux activation and minimized residue formation. |
Cleaning Processes | Implement appropriate cleaning processes, such as aqueous or solvent cleaning, to remove any remaining flux residue after soldering. |
9. Electrostatic Discharge (ESD) Damage
ESD damage can occur when static electricity discharges through sensitive electronic components, causing permanent damage or latent defects.
Prevention Methods
Method | Description |
---|---|
ESD-Safe Workstations | Establish ESD-safe workstations with grounded surfaces, wrist straps, and dissipative materials. |
Personnel Training | Train personnel on ESD awareness, handling procedures, and the use of ESD-safe equipment. |
Packaging and Handling | Use ESD-safe packaging materials and follow proper handling procedures during storage, transport, and assembly. |
FAQ
-
Q: What are the most common causes of solder bridges?
A: Solder bridges are often caused by excessive solder paste application, improper component placement, or inadequate solder mask design. -
Q: How can cold solder joints be prevented?
A: Cold solder joints can be prevented by maintaining proper soldering iron temperature, using the correct soldering technique, and selecting an appropriate flux. -
Q: What is tombstoning, and how can it be avoided?
A: Tombstoning is when a surface-mount component stands up on one end due to uneven solder joint formation. It can be avoided through proper pad design, reflow profile optimization, and accurate component placement. -
Q: How can lifted pads be prevented during PCB assembly?
A: Lifted pads can be prevented by choosing a high-quality PCB laminate, ensuring proper controlled impedance design, and handling PCBs with care during assembly. -
Q: What are the consequences of insufficient solder in PCB assembly?
A: Insufficient solder can result in weak joints, poor electrical conductivity, and reduced mechanical strength, leading to reliability issues and potential product failures.
By understanding these common PCB Assembly Failures and implementing the appropriate prevention methods, manufacturers can significantly improve the quality, reliability, and efficiency of their PCB assembly processes. Regular process monitoring, equipment maintenance, and personnel training are also essential to minimize the occurrence of these failures and ensure consistent, high-quality PCB assembly output.
Leave a Reply