What are Flexible PCBs?
Flexible PCBs, also known as flex circuits, are a type of printed circuit board that can bend, fold, and twist without losing their electrical functionality. Unlike rigid PCBs, which are made from a solid substrate material, flexible PCBs are constructed using thin, flexible materials such as polyimide or polyester. This flexibility allows them to be used in a wide range of applications, including wearable devices, medical equipment, automotive electronics, and aerospace systems.
Factors Affecting Flexible PCB Cost
Several factors contribute to the overall cost of manufacturing flexible PCBs. Understanding these factors can help you optimize your design and make cost-effective decisions.
1. Material Selection
The choice of material used in the construction of flexible PCBs has a significant impact on the overall cost. The most commonly used materials for flexible PCBs include:
-
Polyimide (PI): Known for its excellent thermal stability and mechanical properties, polyimide is the most popular choice for flexible PCBs. However, it is also one of the more expensive materials.
-
Polyester (PET): Polyester is a lower-cost alternative to polyimide, but it has lower temperature resistance and inferior mechanical properties.
-
Liquid Crystal Polymer (LCP): LCP offers excellent electrical properties and dimensional stability, making it suitable for high-frequency applications. However, it is more expensive than polyimide.
The following table compares the properties and relative costs of these materials:
Material | Temperature Resistance | Mechanical Strength | Relative Cost |
---|---|---|---|
Polyimide | High | High | High |
Polyester | Moderate | Moderate | Low |
LCP | High | High | Very High |
2. Number of Layers
The number of layers in a flexible PCB directly affects its manufacturing cost. Single-sided flexible PCBs, which have conductive traces on only one side of the substrate, are the most affordable option. Double-sided flexible PCBs, with conductive traces on both sides, are more expensive than single-sided boards but offer higher circuit density. Multi-layer flexible PCBs, which consist of three or more conductive layers, provide the highest circuit density but also come with the highest manufacturing costs.
3. Circuit Complexity
The complexity of the circuit design is another factor that influences the cost of flexible PCBs. Designs with intricate patterns, fine pitch traces, and high component density require more advanced manufacturing processes and tighter tolerances, resulting in higher costs. Additionally, features such as blind and buried vias, which are used to interconnect layers in multi-layer flexible PCBs, add to the manufacturing complexity and cost.
4. Board Size and Shape
The size and shape of the flexible PCB also play a role in determining its cost. Larger boards require more material and have higher manufacturing costs compared to smaller boards. Moreover, boards with irregular shapes or cutouts are more challenging to manufacture and may incur additional costs due to the need for specialized tooling and processing.
5. Quantity and Lead Time
The quantity of flexible PCBs ordered and the required lead time also affect the overall cost. Larger order quantities often benefit from economies of scale, resulting in lower per-unit costs. However, smaller quantities may be subject to higher setup costs and minimum order requirements.
Additionally, shorter lead times may incur expedited processing fees, while longer lead times allow for more cost-effective production scheduling.
Cost Reduction Strategies
While flexible PCBs are generally more expensive than their rigid counterparts, there are several strategies you can employ to reduce costs without compromising functionality or reliability.
1. Design Optimization
Optimizing your flexible PCB design can help minimize manufacturing costs. Consider the following tips:
-
Minimize the number of layers: Use the minimum number of layers required to achieve the desired functionality. Fewer layers translate to lower material and processing costs.
-
Simplify the circuit layout: Avoid unnecessary complexity in your circuit design. Straightforward layouts with fewer bends, larger trace widths, and relaxed tolerances are easier and more cost-effective to manufacture.
-
Standardize component sizes: Using standard component sizes and packages can help reduce costs by eliminating the need for custom parts and simplifying the assembly process.
2. Material Selection
Selecting the appropriate material for your flexible PCB can help balance cost and performance. Consider the following guidelines:
-
Choose polyimide for high-reliability applications: If your application demands high temperature resistance and mechanical strength, polyimide is the preferred choice, despite its higher cost.
-
Opt for polyester for cost-sensitive projects: If your application has moderate requirements and cost is a primary concern, polyester can provide a more affordable solution.
-
Consider LCP for high-frequency applications: If your design requires excellent electrical properties and dimensional stability, LCP may be worth the additional cost.
3. Panelization
Panelization is the process of grouping multiple flexible PCBs onto a single panel for manufacturing. By maximizing the utilization of the panel area, you can reduce material waste and lower production costs. However, it’s essential to consider the following factors when panelizing your design:
-
Maintain sufficient spacing between boards: Ensure that there is adequate space between individual boards to allow for clean separation after manufacturing.
-
Incorporate fiducial markers: Include fiducial markers on the panel to aid in alignment and registration during the manufacturing process.
-
Consider the depaneling method: Choose a suitable depaneling method, such as V-scoring or tab routing, based on your design requirements and cost considerations.
4. Vendor Selection
Choosing the right flexible PCB manufacturer can significantly impact your project’s cost and success. Consider the following factors when selecting a vendor:
-
Experience and expertise: Look for a manufacturer with a proven track record in producing flexible PCBs similar to your design.
-
Manufacturing capabilities: Ensure that the vendor has the necessary equipment and processes to accommodate your specific requirements, such as multi-layer fabrication or specialized materials.
-
Quality control: Verify that the manufacturer adheres to strict quality control standards and has the necessary certifications, such as ISO 9001 or IPC-6013.
-
Communication and support: Choose a vendor that provides clear communication channels and responsive support throughout the manufacturing process.
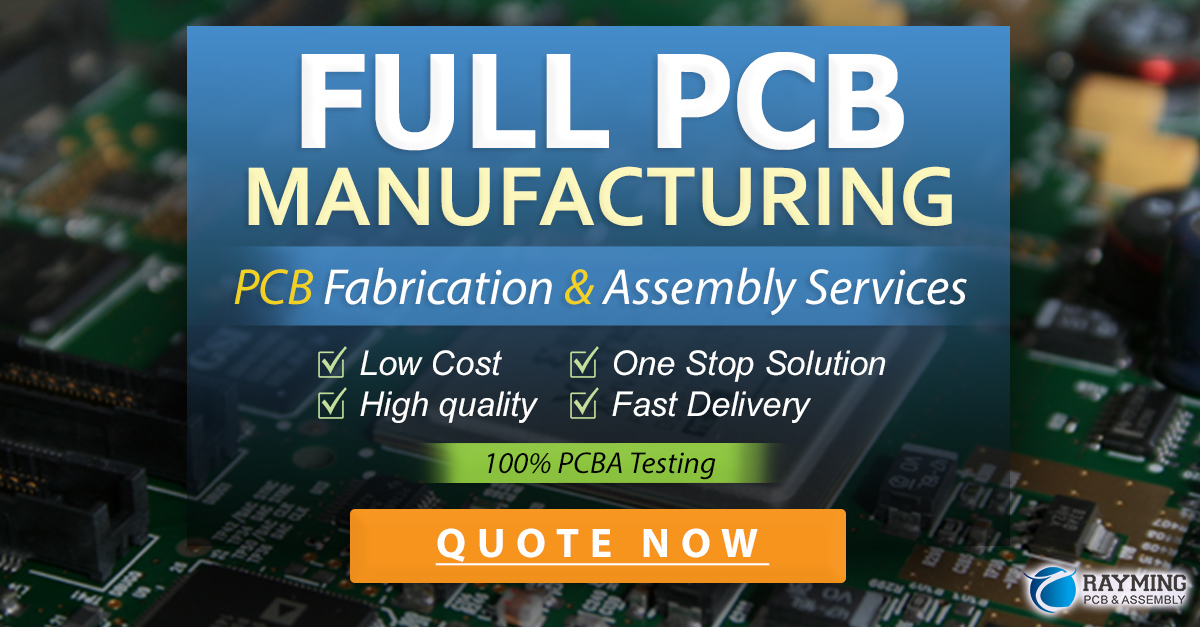
Flexible PCB Cost Estimation
Estimating the cost of a flexible PCB project can be challenging due to the numerous variables involved. However, by considering the following factors, you can develop a rough estimate:
-
Material costs: Determine the cost of the substrate material based on the selected type (polyimide, polyester, or LCP) and the required quantity.
-
Layer count: Multiply the base material cost by the number of layers in your design.
-
Circuit complexity: Add a complexity factor to account for features such as fine pitch traces, blind/buried vias, and high component density.
-
Board size and shape: Adjust the cost estimate based on the board dimensions and any irregular shapes or cutouts.
-
Quantity and lead time: Apply volume discounts for larger quantities and consider any expedited processing fees for short lead times.
To get a more accurate cost estimate, it’s essential to consult with your chosen flexible PCB manufacturer and provide them with your design files and requirements.
Flexible PCB Cost FAQ
Q1. Are flexible PCBs more expensive than rigid PCBs?
A1. Yes, flexible PCBs are generally more expensive than rigid PCBs due to the specialized materials, manufacturing processes, and additional challenges involved in their production.
Q2. What is the most cost-effective material for flexible PCBs?
A2. Polyester (PET) is the most cost-effective material for flexible PCBs, offering moderate performance at a lower cost compared to polyimide (PI) and liquid crystal polymer (LCP).
Q3. How can I reduce the cost of my flexible PCB project?
A3. To reduce the cost of your flexible PCB project, consider optimizing your design by minimizing the number of layers, simplifying the circuit layout, and standardizing component sizes. Additionally, selecting the appropriate material, utilizing panelization, and choosing an experienced and reliable manufacturer can help control costs.
Q4. What factors should I consider when selecting a flexible PCB manufacturer?
A4. When selecting a flexible PCB manufacturer, consider factors such as their experience and expertise in producing flexible PCBs, manufacturing capabilities, quality control standards, certifications, and communication and support throughout the manufacturing process.
Q5. How can I get an accurate cost estimate for my flexible PCB project?
A5. To get an accurate cost estimate for your flexible PCB project, consult with your chosen manufacturer and provide them with your design files and requirements. They will take into account factors such as material selection, layer count, circuit complexity, board size and shape, quantity, and lead time to provide you with a detailed quote.
Conclusion
Understanding the factors that influence flexible PCB cost is crucial for making informed decisions and ensuring the success of your project. By considering material selection, layer count, circuit complexity, board size and shape, quantity, and lead time, you can optimize your design and minimize costs without compromising functionality or reliability.
Remember to employ cost reduction strategies such as design optimization, material selection, panelization, and vendor selection to further control expenses. When estimating the cost of your flexible PCB project, consult with your chosen manufacturer and provide them with your design files and requirements to obtain an accurate quote.
By armed with this knowledge and working closely with a reputable flexible PCB manufacturer, you can successfully navigate the cost considerations associated with your project and achieve the desired outcomes within your budget constraints.
Leave a Reply