Introduction to DC Motors
A DC motor is an electrical machine that converts direct current (DC) electrical energy into mechanical energy. DC motors are widely used in various applications, from small household appliances to large industrial machines. In this comprehensive guide, we will dive deep into the world of DC motors, exploring their types, working principles, applications, and more.
How Does a DC Motor Work?
Basic Principles
A DC motor operates on the principle of electromagnetic induction. It consists of two main components: a stator (stationary part) and a rotor (rotating part). The stator includes permanent magnets or field windings that create a magnetic field, while the rotor has armature windings connected to a commutator.
When a DC current is applied to the armature windings, it generates a magnetic field that interacts with the field produced by the stator. This interaction creates a torque, causing the rotor to spin. The commutator and brushes ensure that the current in the armature windings is reversed at the appropriate time, maintaining the rotation of the motor.
Back EMF
As the rotor spins, it also generates a voltage called back electromotive force (back EMF). This voltage opposes the applied voltage and increases with the speed of the motor. The back EMF helps regulate the motor’s speed and prevents it from drawing excessive current.
Types of DC Motors
There are several types of DC motors, each with its own characteristics and applications. Let’s explore the most common types:
Brushed DC Motors
Brushed DC motors are the most basic and widely used type. They have a simple construction with brushes and a commutator that mechanically switch the direction of the current in the armature windings. Brushed DC motors are affordable and easy to control but require regular maintenance due to brush wear.
Permanent Magnet DC Motors
Permanent magnet DC (PMDC) motors use permanent magnets in the stator to create the magnetic field. They offer high starting torque and good speed regulation. PMDC motors are commonly used in automotive applications, toys, and small appliances.
Series Wound DC Motors
In series wound DC motors, the field windings are connected in series with the armature windings. This configuration provides high starting torque but poor speed regulation. Series wound motors are suitable for applications that require high starting torque, such as cranes and hoists.
Shunt Wound DC Motors
Shunt wound DC motors have the field windings connected in parallel with the armature windings. They offer good speed regulation and controllability but have lower starting torque compared to series wound motors. Shunt wound motors are used in applications that require constant speed, such as conveyor belts and machine tools.
Compound Wound DC Motors
Compound wound DC motors combine the characteristics of series and shunt wound motors. They have both series and shunt field windings, providing a balance between starting torque and speed regulation. Compound wound motors are used in applications that require a compromise between the two, such as elevators and printing presses.
Brushless DC Motors
Brushless DC (BLDC) motors eliminate the need for brushes and a commutator. Instead, they use electronic commutation to control the current in the armature windings. BLDC motors offer several advantages over brushed motors, including higher efficiency, longer lifespan, and reduced maintenance.
Outrunner BLDC Motors
Outrunner BLDC motors have the permanent magnets mounted on the outer rotor, while the armature windings are stationary. They provide high torque and are commonly used in drones, electric vehicles, and robotics.
Inrunner BLDC Motors
Inrunner BLDC motors have the armature windings on the rotor, while the permanent magnets are stationary. They offer high speed and efficiency and are used in applications such as computer fans, hard disk drives, and small pumps.
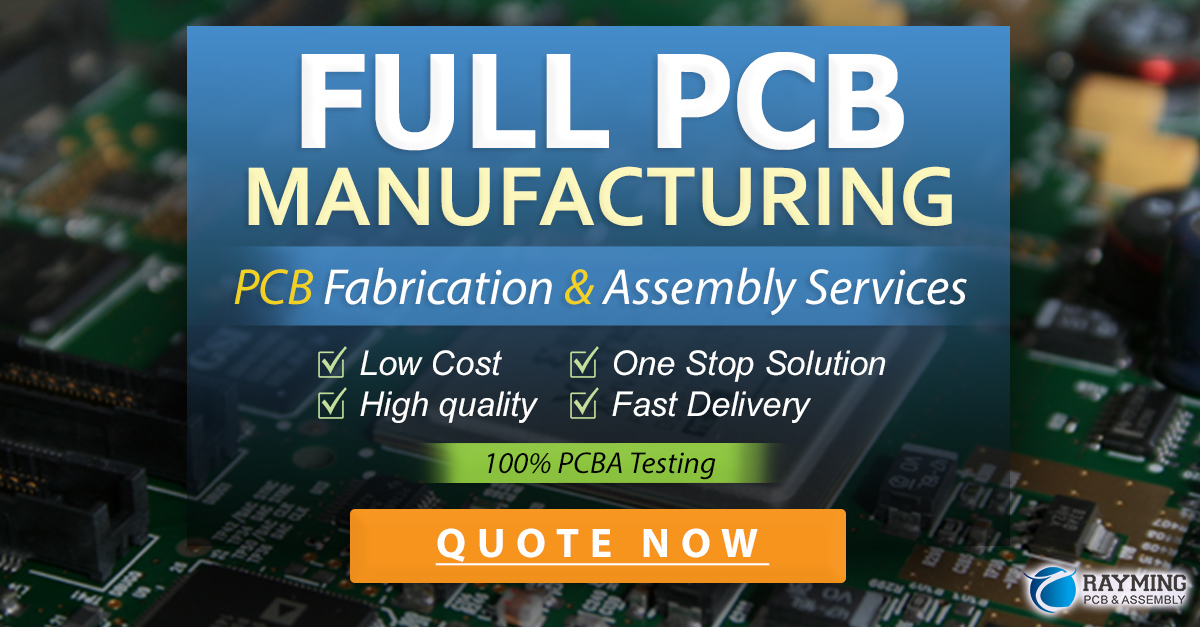
DC Motor Specifications
When selecting a DC motor for a specific application, it’s essential to understand its specifications. Here are some key specifications to consider:
Voltage Rating
The voltage rating indicates the nominal voltage at which the motor is designed to operate. DC motors are available in various voltage ratings, such as 12V, 24V, and 48V.
Current Rating
The current rating specifies the maximum continuous current that the motor can draw without overheating or damage. It’s important to ensure that the power supply can provide sufficient current to meet the motor’s requirements.
Power Rating
The power rating represents the mechanical output power of the motor, typically expressed in watts (W) or horsepower (HP). It indicates the motor’s ability to perform work.
Speed Rating
The speed rating refers to the nominal speed of the motor at its rated voltage and load. It’s usually expressed in revolutions per minute (RPM).
Torque Rating
The torque rating indicates the maximum continuous torque that the motor can produce. It’s a measure of the motor’s ability to overcome resistance and is typically expressed in Newton-meters (N·m) or pound-force-feet (lbf·ft).
DC Motor Applications
DC motors find applications in a wide range of industries and devices. Some common applications include:
Automotive
DC motors are used in automotive applications such as windshield wipers, power windows, seat adjustments, and engine cooling fans.
Robotics
DC motors are essential components in robotics, providing precise motion control for robotic arms, grippers, and mobility systems.
Industrial Machinery
DC motors are used in various industrial machines, such as conveyors, pumps, compressors, and machine tools.
Consumer Electronics
DC motors are found in numerous consumer electronic devices, including electric toothbrushes, hair dryers, portable fans, and toys.
Aerospace
DC motors are used in aerospace applications for actuators, control surfaces, and positioning systems.
DC Motor Control Methods
Controlling the speed and torque of DC motors is crucial for precise and efficient operation. Several control methods are commonly used:
Voltage Control
Voltage control involves varying the voltage applied to the motor to control its speed. Higher voltages result in higher speeds, while lower voltages reduce the speed.
PWM Control
Pulse Width Modulation (PWM) control is a technique that varies the average voltage supplied to the motor by rapidly switching the power on and off. By adjusting the duty cycle of the PWM signal, the motor’s speed can be precisely controlled.
Current Control
Current control regulates the current flowing through the motor to control its torque output. This method is often used in applications that require precise torque control, such as robotics and servo systems.
DC Motor Selection Considerations
When choosing a DC motor for a specific application, several factors should be considered:
Load Requirements
Consider the torque, speed, and power requirements of the load that the motor needs to drive. Ensure that the selected motor can meet or exceed these requirements.
Operating Environment
Take into account the environmental conditions in which the motor will operate, such as temperature, humidity, and dust. Choose a motor that can withstand these conditions and has appropriate ratings.
Size and Weight
Consider the size and weight constraints of the application. Select a motor that fits within the available space and meets the weight requirements.
Efficiency
Evaluate the efficiency of the motor, especially if energy consumption is a concern. Higher efficiency motors can lead to reduced operating costs and improved system performance.
Cost
Consider the initial cost of the motor as well as the long-term operating and maintenance costs. Find a balance between performance and cost that aligns with the project’s budget.
DC Motor Maintenance
Proper maintenance is essential to ensure the longevity and optimal performance of DC motors. Here are some maintenance tips:
Regular Inspection
Regularly inspect the motor for any signs of wear, damage, or contamination. Check for unusual noises, vibrations, or overheating.
Lubrication
Lubricate the motor bearings according to the manufacturer’s recommendations. Use the appropriate type and amount of lubricant to prevent premature wear.
Brush Replacement
For brushed DC motors, regularly check the condition of the brushes and replace them when necessary. Worn or damaged brushes can lead to reduced performance and motor failure.
Cleaning
Keep the motor clean and free from dust, debris, and moisture. Use compressed air or a soft brush to remove any accumulation of contaminants.
Proper Storage
When storing DC motors, ensure that they are kept in a clean, dry, and temperature-controlled environment. Protect them from moisture, dust, and other harmful elements.
Frequently Asked Questions (FAQ)
1. What is the difference between brushed and brushless DC motors?
Brushed DC motors have physical brushes and a commutator that mechanically switch the direction of the current in the armature windings. Brushless DC motors, on the other hand, use electronic commutation and have no brushes or commutator.
2. Can DC motors be used for high-precision applications?
Yes, DC motors can be used for high-precision applications when paired with appropriate control systems and feedback mechanisms. Techniques such as PWM control and closed-loop feedback enable precise speed and position control.
3. How do I determine the power rating of a DC motor for my application?
To determine the power rating, you need to consider the torque and speed requirements of your application. Calculate the required power using the formula: Power (W) = Torque (N·m) × Angular Speed (rad/s).
4. What are the advantages of using DC motors over AC motors?
DC motors offer several advantages, including easy speed control, high starting torque, compact size, and the ability to operate directly from DC power sources like batteries.
5. How can I extend the lifespan of my DC motor?
To extend the lifespan of your DC motor, ensure proper maintenance, including regular inspections, lubrication, and cleaning. Operate the motor within its rated specifications and avoid overloading or overheating. Additionally, use appropriate power supply and protection circuitry to prevent electrical damage.
Conclusion
DC motors are versatile and widely used in various applications, offering reliable and efficient conversion of electrical energy into mechanical energy. Understanding the types, working principles, specifications, and control methods of DC motors is crucial for selecting the right motor for a specific application.
By considering factors such as load requirements, operating environment, size, weight, efficiency, and cost, you can make an informed decision when choosing a DC motor. Regular maintenance and proper care can help extend the lifespan and ensure optimal performance of your DC motor.
With this comprehensive guide, you now have a solid foundation of knowledge about DC motors. Whether you’re an engineer, hobbyist, or student, this information will help you navigate the world of DC motors and make informed decisions for your projects.
Leave a Reply