Types of Robot Wheels
Standard Wheels
Standard wheels are the most common type of wheels used in robotics projects. They are simple, affordable, and easy to implement. These wheels are typically made of plastic or rubber and have a cylindrical shape with a flat surface that contacts the ground. Standard wheels provide good traction on smooth surfaces and are suitable for robots that need to move in straight lines or make gentle turns.
Advantages:
– Simple design
– Affordable
– Easy to install and replace
– Suitable for smooth surfaces
Disadvantages:
– Limited maneuverability
– Not suitable for rough or uneven surfaces
– May slip on low-traction surfaces
Omni Wheels
Omni wheels, also known as poly wheels or Swedish wheels, are a type of wheel that features multiple small rollers attached to its circumference. These rollers are positioned at a 90-degree angle to the wheel’s axis of rotation, allowing the wheel to move laterally as well as forward and backward. Omni wheels enable robots to perform complex maneuvers, such as strafing and rotating in place, making them ideal for applications that require high maneuverability.
Advantages:
– High maneuverability
– Ability to move in any direction
– Suitable for tight spaces and complex environments
Disadvantages:
– More complex design compared to standard wheels
– Higher cost
– Reduced traction on uneven surfaces
– May experience slippage under heavy loads
Mecanum Wheels
Mecanum wheels, invented by Bengt Ilon in 1973, are a type of omnidirectional wheel that features a series of rollers attached to its circumference at a 45-degree angle. This unique design allows robots equipped with Mecanum wheels to move in any direction, including forward, backward, sideways, and diagonally, without the need to rotate the wheels themselves. Mecanum wheels are often used in applications that require precise positioning and maneuverability, such as warehouse robots and autonomous guided vehicles (AGVs).
Advantages:
– Omnidirectional movement
– Precise positioning and maneuverability
– Suitable for applications requiring complex motion
Disadvantages:
– Complex design and control system
– Higher cost compared to standard and omni wheels
– Reduced load capacity due to the angled rollers
– May experience slippage on uneven or low-traction surfaces
Pneumatic Wheels
Pneumatic wheels, also known as air-filled wheels, are wheels that feature a rubber tire filled with compressed air. These wheels provide excellent shock absorption and traction, making them suitable for robots that operate on rough or uneven surfaces. Pneumatic wheels are commonly used in outdoor robotics applications, such as agricultural robots and all-terrain vehicles.
Advantages:
– Excellent shock absorption
– High traction on various surfaces
– Suitable for outdoor and rough terrain applications
Disadvantages:
– Larger size compared to other wheel types
– Higher cost
– Risk of punctures and air leaks
– Require maintenance (air pressure checks and refills)
Tank Treads
Tank treads, also known as tracked wheels, are a type of locomotion system that uses a continuous band of treads instead of traditional wheels. Treads provide excellent traction and stability, allowing robots to navigate rough terrain, climb obstacles, and operate in challenging environments. Tank treads are commonly used in military robots, search and rescue robots, and heavy-duty industrial applications.
Advantages:
– Excellent traction and stability
– Ability to navigate rough terrain and climb obstacles
– High load capacity
– Suitable for heavy-duty applications
Disadvantages:
– Complex design and control system
– Higher cost compared to wheeled systems
– Reduced maneuverability in tight spaces
– Higher maintenance requirements
Choosing the Right Robot Wheels
When selecting wheels for your robotics project, consider the following factors:
- Application requirements
- Indoor or outdoor use
- Smooth or rough terrain
- Required maneuverability
- Load capacity
- Robot size and weight
- Ensure the wheels can support the robot’s weight and payload
- Consider the robot’s dimensions and available space for wheels
- Budget
- Determine the available budget for the wheels
- Consider the cost of additional components, such as motors and mounting hardware
- Compatibility with other components
- Ensure the wheels are compatible with the chosen motors and control system
- Consider the ease of integration with the robot’s chassis and other components
Robot Wheel Materials
Robot wheels can be made from various materials, each with its own properties and advantages. Some common materials include:
- Plastic
- Lightweight and affordable
- Suitable for indoor applications and smooth surfaces
- Examples: ABS, PVC, and nylon
- Rubber
- Provides good traction and shock absorption
- Suitable for outdoor applications and uneven surfaces
- Examples: Natural rubber, synthetic rubber (e.g., polyurethane)
- Metal
- High strength and durability
- Suitable for heavy-duty applications and high load capacities
- Examples: Aluminum, steel, and titanium
When choosing wheel materials, consider factors such as the operating environment, required traction, load capacity, and budget.
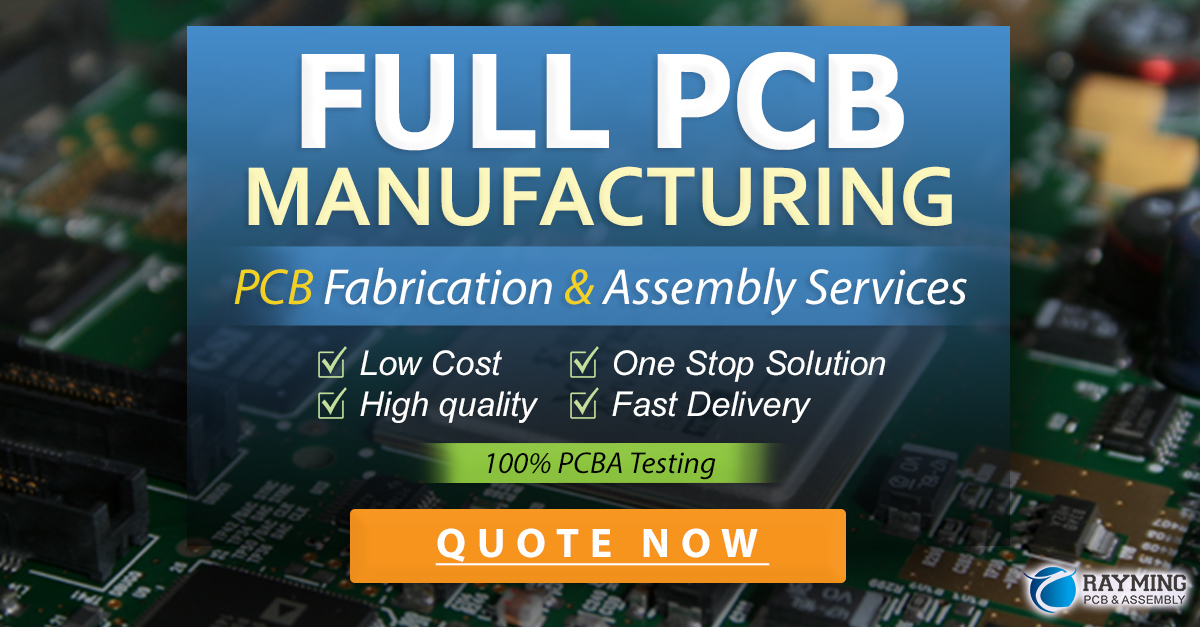
Wheel and Motor Sizing
Properly sizing the wheels and motors is crucial for ensuring optimal robot performance. Consider the following factors when selecting wheel and motor sizes:
- Robot weight and payload
- Determine the total weight of the robot, including its chassis, components, and payload
- Ensure the wheels and motors can support the total weight
- Desired speed and acceleration
- Consider the required speed and acceleration for the robot’s application
- Choose motors with appropriate power ratings and gearboxes
- Wheel diameter and width
- Larger wheels provide better obstacle clearance and stability but may reduce maneuverability
- Wider wheels offer better traction but may increase rolling resistance
- Motor torque and power
- Ensure the motors provide sufficient torque to accelerate and maintain the desired speed
- Consider the motor’s power rating and efficiency
Use online calculators or consult with experienced roboticists to determine the appropriate wheel and motor sizes for your project.
Mounting and Attaching Robot Wheels
Securely mounting and attaching robot wheels is essential for ensuring reliable performance and longevity. Consider the following methods for mounting wheels:
- Hub-mounted wheels
- Wheels with integrated hubs that attach directly to the motor shaft
- Provides a simple and compact mounting solution
- Suitable for small to medium-sized robots
- Shaft-mounted wheels
- Wheels attached to a separate shaft, which is connected to the motor via a coupling or gearbox
- Offers flexibility in positioning the wheels and allows for larger wheel sizes
- Suitable for medium to large-sized robots
- Omni wheel and Mecanum wheel mounts
- Specialized mounting solutions for omni wheels and Mecanum wheels
- Ensures proper alignment and spacing of the rollers
- Provides stable and secure attachment to the robot chassis
When mounting wheels, ensure that they are properly aligned, balanced, and securely fastened to prevent vibrations and uneven wear.
Wheel Encoders and Odometry
Wheel encoders are sensors that measure the rotation of robot wheels, providing valuable data for odometry and localization. Odometry is the process of estimating a robot’s position and orientation based on the motion of its wheels. By combining data from wheel encoders with other sensors, such as gyroscopes and accelerometers, robots can navigate and map their environment more accurately.
There are two main types of wheel encoders:
- Optical encoders
- Use a light source and a photosensor to detect the rotation of a patterned disk attached to the wheel
- Provide high resolution and accuracy
- Suitable for precise positioning and speed control
- Magnetic encoders
- Use a magnetic sensor to detect the rotation of a magnetized ring attached to the wheel
- Offer good resistance to dust and debris
- Suitable for harsh environments and outdoor applications
When implementing wheel encoders, consider factors such as resolution, accuracy, and compatibility with the robot’s control system and software.
Wheel Maintenance and Troubleshooting
Regular maintenance and troubleshooting are essential for ensuring the longevity and reliable performance of robot wheels. Some common maintenance tasks and troubleshooting tips include:
- Cleaning and lubrication
- Regularly clean the wheels and remove any debris or foreign objects
- Lubricate bearings and moving parts to reduce friction and wear
- Tightening and adjustment
- Check and tighten any loose bolts or fasteners
- Adjust wheel alignment and spacing as needed
- Wear and tear inspection
- Inspect wheels for signs of wear, such as cracks, chips, or uneven wear patterns
- Replace wheels when necessary to maintain optimal performance
- Motor and encoder troubleshooting
- Check motor connections and wiring for any loose or damaged contacts
- Verify encoder functionality and calibration
- Consult the manufacturer’s documentation for specific troubleshooting steps
By performing regular maintenance and addressing any issues promptly, you can ensure that your robot’s wheels remain in good condition and provide reliable performance.
Frequently Asked Questions (FAQ)
- What is the difference between omni wheels and Mecanum wheels?
-
Omni wheels have rollers positioned at a 90-degree angle to the wheel’s axis of rotation, allowing for lateral movement. Mecanum wheels have rollers positioned at a 45-degree angle, enabling omnidirectional movement, including diagonal motion.
-
Can I use standard wheels for an outdoor robotics project?
-
While standard wheels can be used for outdoor projects, they may not provide sufficient traction and stability on rough or uneven surfaces. Consider using pneumatic wheels or tank treads for better performance in outdoor environments.
-
How do I determine the appropriate wheel size for my robot?
-
Consider factors such as the robot’s weight, desired speed, and obstacle clearance when selecting wheel size. Larger wheels provide better stability and obstacle clearance but may reduce maneuverability. Consult online calculators or experienced roboticists for guidance.
-
What is the purpose of wheel encoders in robotics?
-
Wheel encoders measure the rotation of robot wheels, providing data for odometry and localization. This information helps robots navigate, estimate their position, and map their environment more accurately.
-
How often should I perform maintenance on my robot’s wheels?
- The frequency of maintenance depends on factors such as the operating environment, usage intensity, and wheel type. As a general guideline, inspect and clean the wheels regularly (e.g., every few operating hours), and lubricate moving parts as needed. Replace wheels when they show signs of excessive wear or damage.
Conclusion
Robot wheels are a crucial component in adding mobility to your robotics projects. By understanding the different types of wheels, their advantages and limitations, and how to choose the right wheels for your application, you can create robots that effectively navigate and perform tasks in various environments. Remember to consider factors such as wheel materials, sizing, mounting, and maintenance to ensure optimal performance and longevity.
As you explore the world of robot wheels and incorporate them into your projects, keep in mind that experimentation and iterative design are key to success. Don’t be afraid to try different wheel configurations and adapt your designs based on the results. With the right knowledge and approach, you can create robots that are mobile, versatile, and capable of tackling a wide range of challenges.
Wheel Type | Advantages | Disadvantages |
---|---|---|
Standard Wheels | Simple design, affordable, easy to install | Limited maneuverability, not suitable for rough surfaces |
Omni Wheels | High maneuverability, moves in any direction | Complex design, higher cost, reduced traction on uneven surfaces |
Mecanum Wheels | Omnidirectional movement, precise positioning | Complex design and control, higher cost, reduced load capacity |
Pneumatic Wheels | Excellent shock absorption, high traction | Larger size, higher cost, risk of punctures, require maintenance |
Tank Treads | Excellent traction and stability, navigates rough terrain | Complex design, higher cost, reduced maneuverability, higher maintenance |
Leave a Reply