Introduction to Flexible Printed Circuits
Flexible printed circuits (FPCs) are electrical interconnectors made from flexible materials like polyimide that can be bent, folded or twisted to fit into tight or dynamic spaces. They provide electrical connections between components in flexible and wearable electronics, medical devices, aerospace systems and more. Compared to traditional rigid printed circuit boards (PCBs), FPCs are thinner, lighter and more resilient.
The most common FPC materials are polyimide and polyester. Polyimide offers higher heat resistance, chemical resistance and mechanical strength, making it suitable for more demanding applications. Polyester is cheaper but has lower performance limits.
Advantages of Flexible Printed Circuits
- Thinner and lighter – takes up less space
- Can be bent and twisted – accommodates dynamic or tight spaces
- Vibration and shock resistant – ideal for wearables and vehicles
- High reliability – flexing minimizes solder joint fractures
- Design freedom – can be folded into 3D shapes
- Easier assembly and integration
Applications of Flexible Printed Circuits
- Wearable electronics – smart watches, fitness trackers, VR headsets
- Medical devices – hearing aids, pacemakers, blood glucose monitors
- Aerospace and defense – guidance systems, engine controls, sensors
- Automotive – control panels, engine systems, sensors
- Consumer electronics – laptops, mobile phones, tablets
- Industrial – robotics, instrumentation, control systems
Polyimide as a Flex Circuit Substrate
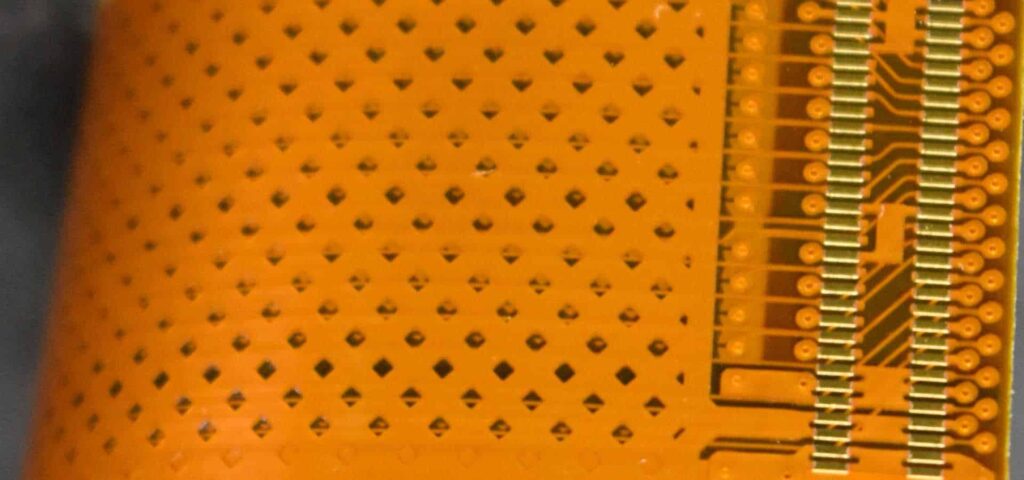
Polyimide film is the most widely used base material (substrate) for flexible printed circuits today. The two most common types of polyimide used are DuPontTM Kapton® and UbeTM Upilex®.
Properties of Polyimide
- High heat resistance – up to 400°C
- Excellent chemical resistance
- High mechanical strength and dimensional stability
- Good dielectric properties
- Flexible even at thin gauges – down to 12.5 microns
- Flame retardant with no halogen added
Benefits of Polyimide Substrates
- Can withstand soldering temperatures
- Resists solvents, acids, bases, oils – ideal for harsh environments
- Withstands repeated flexing without cracking
- Maintains performance over wide temperature range
- Enables very thin, lightweight constructions
- Safer than substrates with halogenated flame retardants
Polyimide vs Other Substrates
Property | Polyimide | Polyester | PEN |
---|---|---|---|
Heat resistance | Excellent | Moderate | Moderate |
Flexibility | Excellent | Good | Good |
Chemical resistance | Excellent | Moderate | Good |
Cost | Moderate | Low | High |
Polyimide has the highest performance but is more expensive than polyester. PEN (polyethylene naphthalate) approaches polyimide’s properties but is the most costly.
Fabrication of Polyimide Flex Circuits
Polyimide flex circuits utilize photolithographic processes similar to rigid PCBs. There are two main methods: additive and subtractive.
Additive Process
- Start with bare polyimide substrate
- Sputter deposit seed layer (e.g. copper)
- Laminate photoresist and expose circuit pattern
- Electroplate copper in openings to desired thickness
- Strip off resist, flash etch seed layer
Subtractive Process
- Start with polyimide substrate clad with copper foil
- Apply photoresist and expose circuit pattern
- Etch away unwanted copper
- Strip off resist
Additive builds up the circuit while subtractive etches away excess copper. Additive achieves finer features but requires sputtering equipment. Subtractive is simpler but limited by copper foil thickness.
Common Fabrication Techniques
Etching:Uses chemical solutions to dissolve away unwanted copper
Plating: Electrolytic process to build up copper thickness
Lamination: Joins layers using adhesive and heat/pressure
Drilling: Creates vias and holes using mechanical or laser drills
Solder mask: Protective coating with openings at pads and vias
Applications of Polyimide Flexible Circuits
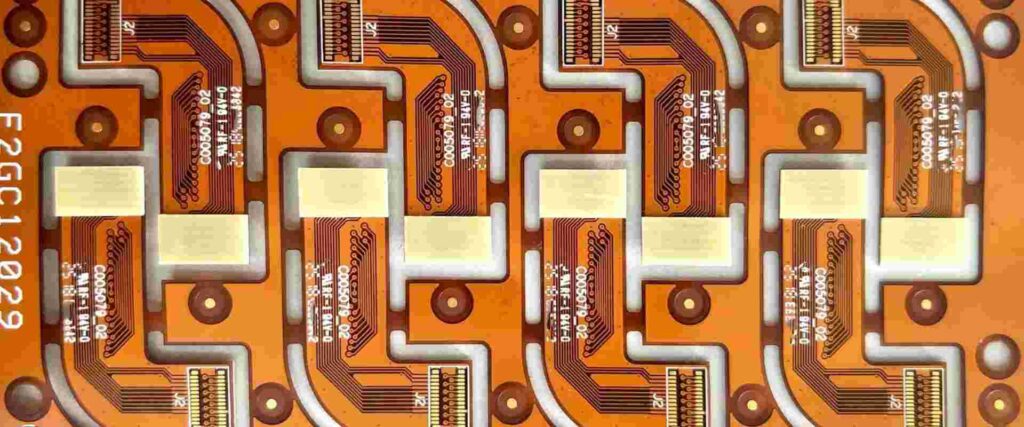
Polyimide’s combination of heat resistance, chemical stability and mechanical flexibility make it ideal for many demanding flex circuit applications.
Aerospace and Defense
- Guidance systems
- Engine controls
- Avionics systems
- Missile systems
- Radar assemblies
Polyimide withstands extreme temps and vibration. Low weight reduces payload.
Medical Electronics
- Hearing aids
- Pacemakers
- Blood analysis instruments
- Patient monitoring devices
- Surgical equipment
Biocompatible and flexible. Can be sterilized. Withstands body environment.
Automotive Electronics
- Instrument panels
- Engine control units
- Sensor interconnects
- Power distribution
- Lighting and safety systems
Vibration resistant. Tolerates under-hood heat. Lightweight.
Consumer Wearables
- Smart watches
- Fitness trackers
- Augmented reality glasses
- Virtual reality headsets
- Media players
Conforms to body. Allows complex compact geometry.
Frequently Asked Questions
What are the key advantages of polyimide flex circuits?
Polyimide provides an unmatched combination of heat resistance, chemical stability, mechanical flexibility and strength. This makes it suitable for applications with extreme temps, harsh environments, tight spaces and dynamic flexing requirements.
How are polyimide flex circuits fabricated?
Photolithographic processes are used, similar to rigid PCBs. The two main approaches are additive, which electrolytically builds up the copper traces, and subtractive, which etches away excess copper foil.
What are some common applications of polyimide flex circuits?
Polyimide flex circuits are widely used in aerospace, medical devices, automotive, and consumer wearables. Example applications include engine controls, pacemakers, VR headsets, and vehicle sensors.
What are the alternatives to polyimide substrates?
The main alternatives are polyester, which is lower cost but has lower performance limits, and polyethylene naphthalate (PEN) which approaches polyimide’s properties but is more expensive.
How thin can polyimide flex circuits be fabricated?
Polyimide can be produced as thin films down to 12.5 microns while maintaining good mechanical properties and flexibility. This allows very thin, lightweight flex circuit constructions.
Leave a Reply