Introduction to PCB Stiffeners
A PCB stiffener, also known as a PCB stiffening plate or PCB backbone, is a mechanical support structure used to reinforce and stabilize flexible and rigid-flex printed circuit boards (PCBs). These stiffeners are essential components in various electronic devices, particularly in applications where the PCB is subjected to vibration, shock, or other mechanical stresses. By providing additional rigidity and support, PCB stiffeners help to prevent damage, maintain electrical integrity, and ensure the overall reliability of the electronic assembly.
What are PCB Stiffeners?
PCB stiffeners are flat, rigid plates that are attached to the surface of a flexible or rigid-flex PCB. They are typically made from materials such as aluminum, stainless steel, or FR-4 (a glass-reinforced epoxy laminate). The primary purpose of a PCB stiffener is to provide mechanical support to the PCB, preventing it from bending, twisting, or deforming under stress.
Why are PCB Stiffeners Important?
Flexible and rigid-flex PCBs offer numerous advantages over traditional rigid PCBs, including increased design flexibility, reduced weight, and improved reliability. However, the inherent flexibility of these PCBs can also make them more susceptible to mechanical damage, particularly in applications where the PCB is subjected to frequent movement or vibration.
PCB stiffeners address this issue by providing additional rigidity and support to the flexible or rigid-flex PCB. By reinforcing the PCB, stiffeners help to:
- Prevent bending, twisting, or deformation of the PCB
- Reduce stress on components and solder joints
- Improve the overall mechanical stability of the electronic assembly
- Enhance the reliability and longevity of the PCB
Applications of PCB Stiffeners
PCB stiffeners are used in a wide range of electronic devices and applications, particularly those that require flexible or rigid-flex PCBs. Some common applications include:
Consumer Electronics
Many consumer electronic devices, such as smartphones, tablets, and wearables, utilize flexible or rigid-flex PCBs to achieve compact, lightweight designs. PCB stiffeners are often used in these devices to provide mechanical support and protect the PCB from damage due to everyday use.
Automotive Electronics
In the automotive industry, PCB stiffeners are used to reinforce electronic assemblies that are subjected to harsh environmental conditions, such as extreme temperatures, vibration, and shock. Stiffeners help to ensure the reliability and longevity of critical electronic components, such as engine control units, infotainment systems, and advanced driver assistance systems (ADAS).
Medical Devices
Medical devices, such as patient monitors, diagnostic equipment, and wearable health monitors, often rely on flexible or rigid-flex PCBs to achieve compact, ergonomic designs. PCB stiffeners are used in these devices to provide mechanical support and protect the PCB from damage due to frequent handling or patient movement.
Aerospace and Defense
In aerospace and defense applications, PCB stiffeners are used to reinforce electronic assemblies that are subjected to extreme environmental conditions, such as high altitudes, rapid temperature changes, and intense vibration. Stiffeners help to ensure the reliability and performance of critical electronic systems, such as avionics, communication equipment, and weapon systems.
Designing with PCB Stiffeners
When designing an electronic assembly that incorporates a PCB stiffener, several factors must be considered to ensure optimal performance and reliability.
Material Selection
The choice of material for the PCB stiffener depends on the specific requirements of the application, such as the expected environmental conditions, mechanical stresses, and weight constraints. Common materials used for PCB stiffeners include:
- Aluminum: Lightweight, good thermal conductivity, and relatively low cost
- Stainless steel: High strength, good corrosion resistance, and suitable for harsh environments
- FR-4: Non-conductive, lightweight, and compatible with standard PCB manufacturing processes
Stiffener Thickness
The thickness of the PCB stiffener is another important consideration. Thicker stiffeners provide greater rigidity and support, but also add weight and may increase the overall thickness of the electronic assembly. The optimal stiffener thickness depends on factors such as the size and flexibility of the PCB, the expected mechanical stresses, and the space constraints of the application.
Attachment Methods
PCB stiffeners can be attached to the PCB using various methods, including:
- Adhesives: Epoxy or acrylic adhesives provide a strong, permanent bond between the stiffener and the PCB
- Mechanical fasteners: Screws, rivets, or snap-fit features can be used to secure the stiffener to the PCB
- Soldering: In some cases, the stiffener can be soldered directly to the PCB using a process called reflow soldering
The choice of attachment method depends on factors such as the materials involved, the expected mechanical stresses, and the manufacturing process.
Design Considerations
When designing a PCB with a stiffener, several additional factors should be considered:
- Placement: The stiffener should be positioned to provide optimal support to the PCB, particularly in areas with high component density or where the PCB is most likely to flex
- Cutouts and openings: The stiffener design should accommodate any necessary cutouts or openings for components, connectors, or mounting features
- Thermal management: In some cases, the PCB stiffener can also serve as a heat sink, helping to dissipate heat from high-power components
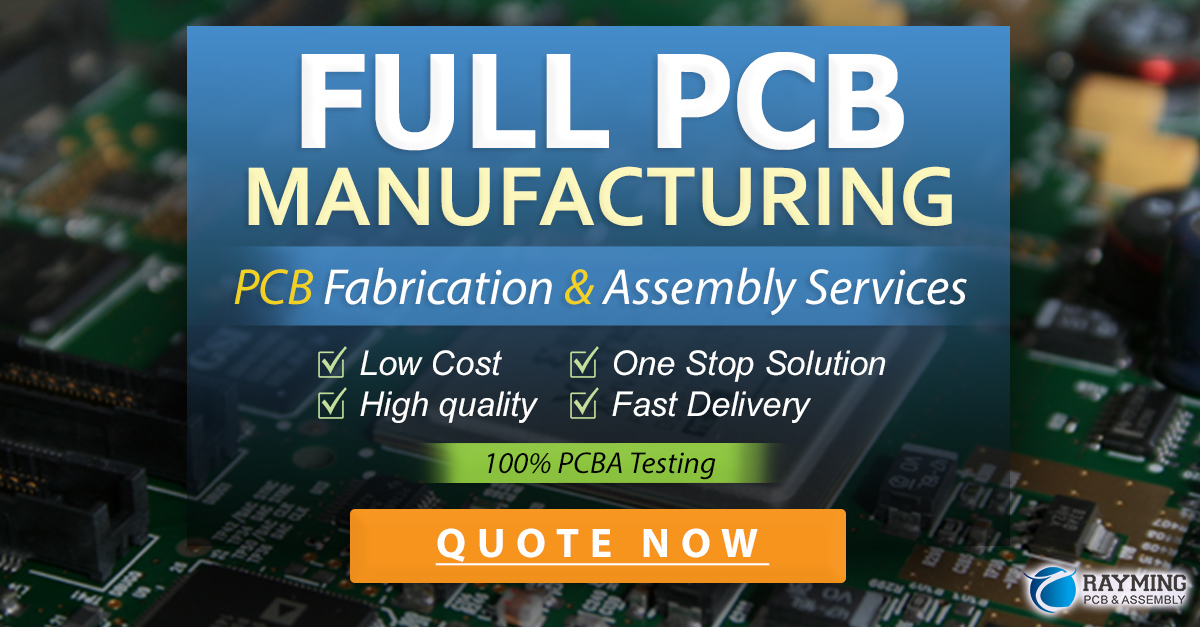
Manufacturing PCBs with Stiffeners
The manufacturing process for PCBs with stiffeners involves several key steps:
-
PCB fabrication: The flexible or rigid-flex PCB is manufactured using standard PCB fabrication techniques, such as photolithography, etching, and lamination.
-
Stiffener fabrication: The PCB stiffener is fabricated using processes such as stamping, machining, or laser cutting, depending on the material and design requirements.
-
Attachment: The stiffener is attached to the PCB using the chosen method (adhesive, mechanical fasteners, or soldering).
-
Assembly: The PCB with the attached stiffener is then populated with components and undergoes final assembly and testing.
Advantages of Using PCB Stiffeners
PCB stiffeners offer several key advantages for flexible and rigid-flex PCBs:
-
Improved mechanical stability: Stiffeners provide additional rigidity and support, preventing bending, twisting, or deformation of the PCB.
-
Enhanced reliability: By reducing stress on components and solder joints, stiffeners help to improve the overall reliability and longevity of the electronic assembly.
-
Design flexibility: PCB stiffeners allow for the use of flexible and rigid-flex PCBs in a wider range of applications, including those with challenging mechanical requirements.
-
Cost-effective: Compared to using thicker or more rigid PCB materials, incorporating a PCB stiffener can be a more cost-effective solution for achieving the desired mechanical properties.
Challenges and Limitations
While PCB stiffeners offer numerous benefits, there are also some challenges and limitations to consider:
-
Added complexity: Incorporating a PCB stiffener adds complexity to the design and manufacturing process, requiring additional steps and considerations.
-
Increased weight: PCB stiffeners can add weight to the electronic assembly, which may be a concern in weight-sensitive applications such as aerospace or portable devices.
-
Limited flexibility: While PCB stiffeners provide necessary support, they can also limit the overall flexibility of the PCB, which may be a drawback in certain applications.
Future Trends and Developments
As electronic devices continue to become more compact, lightweight, and sophisticated, the demand for flexible and rigid-flex PCBs with integrated stiffeners is expected to grow. Some key trends and developments in this area include:
-
Advanced materials: Researchers are exploring new materials for PCB stiffeners, such as carbon fiber composites, which offer high strength-to-weight ratios and excellent mechanical properties.
-
3D printing: Additive manufacturing techniques, such as 3D printing, are being investigated as potential methods for fabricating PCB stiffeners with complex geometries and customized designs.
-
Integrated functionality: PCB stiffeners are being designed to serve additional functions beyond mechanical support, such as acting as heat sinks, electromagnetic shields, or even structural components in the final product.
Conclusion
PCB stiffeners are essential components in the design and manufacture of flexible and rigid-flex PCBs, providing the necessary mechanical support and stability to ensure reliable operation in a wide range of applications. By understanding the key considerations for designing with PCB stiffeners, engineers can create robust, high-performance electronic assemblies that meet the demands of today’s increasingly complex and challenging environments. As technology continues to advance, PCB stiffeners will play an increasingly important role in enabling the next generation of electronic devices and systems.
Frequently Asked Questions (FAQ)
1. What is the primary purpose of a PCB stiffener?
The primary purpose of a PCB stiffener is to provide mechanical support and stability to flexible and rigid-flex PCBs, preventing bending, twisting, or deformation under stress.
2. What materials are commonly used for PCB stiffeners?
Common materials used for PCB stiffeners include aluminum, stainless steel, and FR-4 (a glass-reinforced epoxy laminate).
3. How are PCB stiffeners attached to the PCB?
PCB stiffeners can be attached to the PCB using adhesives (epoxy or acrylic), mechanical fasteners (screws, rivets, or snap-fit features), or through soldering (reflow soldering).
4. Can PCB stiffeners serve additional functions beyond mechanical support?
Yes, PCB stiffeners can be designed to serve additional functions, such as acting as heat sinks to dissipate heat from high-power components or as electromagnetic shields to reduce electromagnetic interference (EMI).
5. Are there any limitations or challenges associated with using PCB stiffeners?
Some limitations and challenges associated with using PCB stiffeners include added complexity to the design and manufacturing process, increased weight of the electronic assembly, and potential limitations on the overall flexibility of the PCB.
Leave a Reply