What is a DIY 3D Printer?
A DIY 3D printer is a 3D printer that you build yourself from a kit or from scratch. Unlike pre-assembled 3D printers, DIY 3D printers require you to assemble the components and configure the software yourself. While this may seem daunting at first, building your own 3D printer can be a rewarding and educational experience.
Advantages of Building a DIY 3D Printer
- Cost-effective: Building your own 3D printer can be significantly cheaper than buying a pre-assembled one.
- Customizable: With a DIY 3D printer, you have the freedom to customize and upgrade components to suit your needs.
- Educational: Building a 3D printer from scratch can teach you valuable skills in electronics, mechanics, and programming.
Types of DIY 3D Printers
There are several types of DIY 3D printers available, each with its own advantages and disadvantages. Here are some of the most popular types:
Cartesian 3D Printers
Cartesian 3D printers are the most common type of DIY 3D printer. They use a Cartesian coordinate system (X, Y, and Z axes) to move the print head and build plate. Cartesian 3D printers are known for their simplicity, reliability, and ease of use.
Advantages of Cartesian 3D Printers
- Simple design: Cartesian 3D printers have a straightforward design that is easy to understand and build.
- Reliable: Cartesian 3D printers are known for their reliability and consistent print quality.
- Easy to maintain: Cartesian 3D printers have fewer moving parts, making them easier to maintain and troubleshoot.
Disadvantages of Cartesian 3D Printers
- Limited build volume: Cartesian 3D printers typically have a smaller build volume compared to other types of 3D printers.
- Slower print speed: Cartesian 3D printers may have slower print speeds compared to other types of 3D printers.
Delta 3D Printers
Delta 3D printers use three arms arranged in a triangular configuration to move the print head. Delta 3D printers are known for their fast print speeds and large build volumes.
Advantages of Delta 3D Printers
- Fast print speed: Delta 3D printers can achieve faster print speeds compared to Cartesian 3D printers.
- Large build volume: Delta 3D printers typically have a larger build volume compared to Cartesian 3D printers.
- Unique design: Delta 3D printers have a unique and visually appealing design.
Disadvantages of Delta 3D Printers
- Complex design: Delta 3D printers have a more complex design compared to Cartesian 3D printers, making them more challenging to build and maintain.
- Expensive: Delta 3D printers can be more expensive than Cartesian 3D printers due to their complex design and components.
CoreXY 3D Printers
CoreXY 3D printers use a combination of belts and pulleys to move the print head along the X and Y axes. CoreXY 3D printers are known for their fast print speeds and high precision.
Advantages of CoreXY 3D Printers
- Fast print speed: CoreXY 3D printers can achieve faster print speeds compared to Cartesian 3D printers.
- High precision: CoreXY 3D printers are known for their high precision and accuracy.
- Compact design: CoreXY 3D printers have a compact design that minimizes the footprint of the printer.
Disadvantages of CoreXY 3D Printers
- Complex design: CoreXY 3D printers have a more complex design compared to Cartesian 3D printers, making them more challenging to build and maintain.
- Expensive: CoreXY 3D printers can be more expensive than Cartesian 3D printers due to their complex design and components.
Components of a DIY 3D Printer
Before you start building your DIY 3D printer, it’s important to understand the various components that make up a 3D printer. Here are some of the essential components:
Frame
The frame is the structural backbone of your 3D printer. It provides support for all the other components and ensures that the printer remains stable during operation. The frame can be made from a variety of materials, including aluminum extrusion, wood, or 3D printed parts.
Motors
Motors are used to move the print head and build plate along the X, Y, and Z axes. The most common type of motor used in 3D printers is the stepper motor, which provides precise control over the movement of the printer.
Belts and Pulleys
Belts and pulleys are used to transmit motion from the motors to the print head and build plate. They are typically made from rubber or polyurethane and are designed to be durable and long-lasting.
Extruder
The extruder is responsible for feeding the filament into the hot end and melting it into a liquid state. The extruder consists of a stepper motor, a drive gear, and a hot end.
Hot End
The hot end is responsible for melting the filament and extruding it onto the build plate. It consists of a heating element, a temperature sensor, and a nozzle.
Build Plate
The build plate is the surface on which the 3D printed object is built. It can be made from a variety of materials, including glass, aluminum, or a special adhesive surface.
Electronics
The electronics of a 3D printer consist of a control board, a power supply, and various sensors and switches. The control board is responsible for controlling the motors, extruder, and hot end, while the power supply provides the necessary power to run the printer.
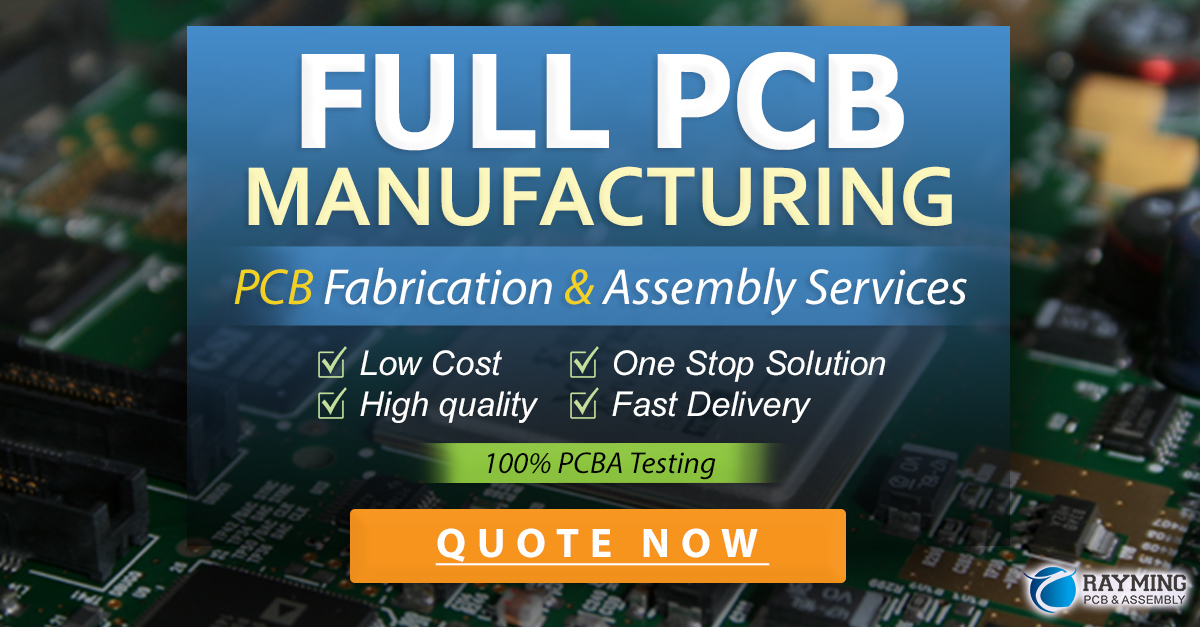
Building Your DIY 3D Printer
Now that you understand the various components of a 3D printer, it’s time to start building your own. Here are the steps you’ll need to follow:
Step 1: Choose a Design
The first step in building your DIY 3D printer is to choose a design. There are many different designs available online, ranging from simple Cartesian printers to more complex Delta or CoreXY printers. Choose a design that matches your skill level and budget.
Step 2: Gather Materials
Once you’ve chosen a design, you’ll need to gather all the necessary materials. This includes the frame, motors, belts, pulleys, extruder, hot end, build plate, and electronics. You can purchase these components individually or as part of a kit.
Step 3: Assemble the Frame
The next step is to assemble the frame of your 3D printer. Follow the instructions provided with your chosen design to ensure that the frame is assembled correctly. Pay close attention to the alignment and squareness of the frame, as this will affect the accuracy of your prints.
Step 4: Install the Motors and Belts
Once the frame is assembled, you can install the motors and belts. Make sure that the motors are securely mounted and that the belts are properly tensioned. This will ensure that the print head and build plate move smoothly and accurately.
Step 5: Install the Extruder and Hot End
Next, you’ll need to install the extruder and hot end. Follow the instructions provided with your chosen design to ensure that these components are installed correctly. Make sure that the hot end is properly aligned with the nozzle and that the extruder is feeding the filament smoothly.
Step 6: Install the Build Plate
The build plate is the surface on which your 3D printed objects will be built. Install the build plate according to the instructions provided with your chosen design. Make sure that the build plate is level and that it is securely attached to the frame.
Step 7: Install the Electronics
The final step in building your DIY 3D printer is to install the electronics. This includes the control board, power supply, and various sensors and switches. Follow the wiring diagram provided with your chosen design to ensure that all the components are connected correctly.
Configuring and Calibrating Your DIY 3D Printer
Once your DIY 3D printer is assembled, you’ll need to configure and calibrate it to ensure that it is printing accurately. Here are the steps you’ll need to follow:
Step 1: Install Firmware
The first step in configuring your 3D printer is to install firmware. Firmware is the software that controls the printer’s hardware and enables communication between the printer and your computer. There are many different firmware options available, including Marlin, Repetier, and Smoothieware. Choose a firmware that is compatible with your control board and follow the installation instructions provided by the firmware developer.
Step 2: Calibrate the Bed
The next step is to calibrate the bed of your 3D printer. This involves ensuring that the bed is level and that the nozzle is at the correct height above the bed. Use a sheet of paper to adjust the bed leveling screws until the nozzle is just touching the paper at all four corners of the bed. This will ensure that the first layer of your print adheres properly to the bed.
Step 3: Calibrate the Extruder
Calibrating the extruder involves ensuring that the correct amount of filament is being extruded for a given distance. This is important because it affects the accuracy and quality of your prints. To calibrate the extruder, you’ll need to measure the distance that the filament travels for a given number of steps and adjust the steps per millimeter setting in your firmware accordingly.
Step 4: Calibrate the Temperature
The temperature of the hot end and bed can have a significant impact on the quality of your prints. Use a temperature tower to calibrate the temperature settings for your specific filament. A temperature tower is a 3D model that is printed at different temperatures, allowing you to determine the optimal temperature for your filament.
Step 5: Fine-Tune Settings
Once you’ve calibrated your 3D printer, you may need to fine-tune some of the settings to achieve optimal print quality. This may involve adjusting the print speed, layer height, or retraction settings. Experiment with different settings and observe the results to determine the best settings for your specific printer and filament.
Troubleshooting Common Issues
Even with proper calibration and configuration, you may encounter issues with your DIY 3D printer from time to time. Here are some common issues and how to troubleshoot them:
Poor Bed Adhesion
If your prints are not sticking to the bed, there are a few things you can try:
- Clean the bed with isopropyl alcohol to remove any dirt or debris.
- Use a glue stick or hairspray to improve adhesion.
- Adjust the bed temperature to ensure that the first layer is sticking properly.
Clogged Nozzle
If your nozzle becomes clogged, you may notice poor print quality or no extrusion at all. Here are a few things you can try:
- Heat up the hot end to the maximum temperature and use a needle or wire to clear the clog.
- Use a cold pull technique to remove any trapped filament from the nozzle.
- Replace the nozzle if it is damaged or worn out.
Layer Shifting
If your prints are shifting or misaligning, there are a few things you can try:
- Check that all the belts and pulleys are properly tensioned and aligned.
- Ensure that the frame is square and that all the components are securely fastened.
- Reduce the print speed to minimize the risk of layer shifting.
FAQ
1. How much does it cost to build a DIY 3D printer?
The cost of building a DIY 3D printer can vary depending on the design and components you choose. A basic Cartesian printer can cost as little as $200, while a more complex Delta or CoreXY printer can cost upwards of $1000.
2. What materials can I print with a DIY 3D printer?
DIY 3D printers can print with a variety of materials, including PLA, ABS, PETG, and TPU. The specific materials you can print with will depend on the type of hot end and extruder you choose.
3. How long does it take to build a DIY 3D printer?
The time it takes to build a DIY 3D printer can vary depending on your skill level and the complexity of the design. A basic Cartesian printer can be built in a weekend, while a more complex Delta or CoreXY printer may take several weeks or months.
4. Do I need any special skills to build a DIY 3D printer?
Building a DIY 3D printer does require some basic mechanical and electrical skills. You should be comfortable working with tools and following instructions. If you have experience with electronics or programming, that can be helpful as well.
5. Can I use a DIY 3D printer for commercial purposes?
While DIY 3D printers can be used for commercial purposes, they may not be as reliable or consistent as commercial-grade printers. If you plan to use your printer for commercial purposes, you may want to invest in a higher-end kit or pre-assembled printer.
Conclusion
Building a DIY 3D printer can be a fun and rewarding experience for beginners and experienced makers alike. By understanding the different types of 3D printers, components, and assembly steps, you can create a custom printer that meets your specific needs and budget. Remember to take your time, follow instructions carefully, and don’t be afraid to ask for help if you get stuck. With a little patience and perseverance, you’ll be printing your own 3D objects in no time!
Leave a Reply