Introduction
Printed circuit boards (PCBs) are essential components in most electronic devices. They provide the mechanical support and electrical connections between electronic components. While rigid PCBs are the most common, flexible and semi-flexible PCBs are gaining popularity due to their unique characteristics and advantages in certain applications.
Semi-flexible PCBs, as the name suggests, offer more rigidity than fully flexible PCBs but maintain some degree of flexibility. This makes them suitable for applications that require moderate flexibility, durability, and reliability.
In this article, we will look at what makes semi-flexible PCBs unique, their advantages over rigid PCBs, different types available, and some of their common applications.
What are Semi-Flexible PCBs?
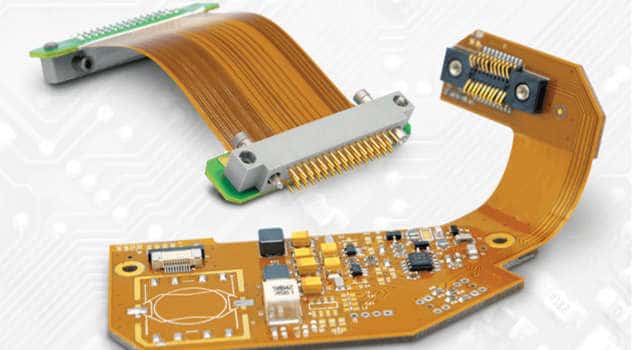
Semi-flexible PCBs consist of flexible dielectric layers laminated onto rigid laminate layers. The dielectric material is typically polyimide or other polymers that can withstand repeated bending. The rigid layers provide mechanical support and stability.
Common rigid layer materials include FR-4, CEM-1, CEM-3 for high temperature applications, and metal core PCBs. The layer stackup and layout are designed to provide the desired degree of flexure for the application.
Compared to rigid PCBs, semi-flex PCBs offer:
- Moderate flexibility and bendability
- Improved durability and dynamic flex performance
- Good heat dissipation if metal-core materials are used
- Reliable performance in high vibration environments
At the same time, they offer better structural rigidity than fully flexible PCBs. This makes them suitable for applications that require dynamic flexing, folding, wrapping, moderate shock/vibration resistance, and installation in tight spaces.
Advantages of Semi-Flexible PCBs
Here are some of the main advantages of semi-flex PCBs compared to rigid boards:
Dynamic Flex Capability
The flexible layers allow semi-flex PCBs to bend repeatedly without damage. This makes them suitable for moveable parts and mechanisms like those found in robotics, automation equipment, printers, and fitness trackers.
Rigid-flex PCBs are better suited for dynamic flexing applications than rigid PCBs which are prone to cracking under repeated bending stresses.
Improved Reliability
Flexible layers in semi-flex PCBs act as a cushion and relieve stresses from vibrations, shocks, and impacts. This improves reliability in high vibration environments like automotive, aerospace, and industrial applications.
Design Flexibility
Semi-flex PCBs allow for flexible portions to route through hinges, joints, and other tight spaces. This enables more compact and space-efficient PCB layouts.
Lightweight Construction
By combining lightweight flexible layers with thin rigid layers, semi-flex PCBs can have lower weight than rigid boards. This is advantageous in weight-sensitive applications.
EMI/RFI Shielding
Metal core materials used in some semi-flex PCB constructions provide good EMI/RFI shielding from unwanted electromagnetic interference.
Types of Semi-Flexible PCBs
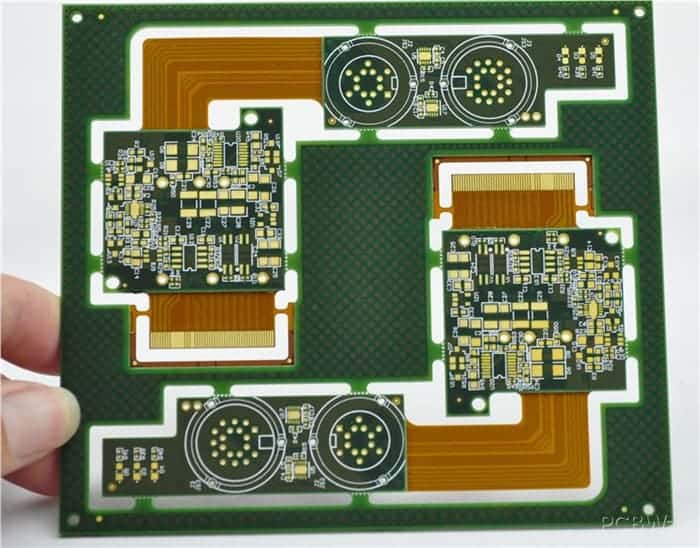
There are two main construction approaches for semi-flex PCBs:
Rigid-Flex
These have alternating flexible and rigid portions in the same board. The rigid sections provide mechanical support while flexible portions enable dynamic flexing.
Flex-Rigid
These have outer flexible layers laminated onto inner rigid layers for support. The entire board can bend thanks to the flexible outer layers.
Other constructions like metal-core flex-rigid provide enhanced thermal performance. The choice depends on mechanical, electrical, and thermal requirements.
Common Applications of Semi-Flexible PCBs
Thanks to their unique advantages, semi-flex PCBs are growing in popularity across many industries:
Wearable Electronics
The flexible portions allow the PCB to contour to the body ergonomically. Semi-flex PCBs are common in fitness bands, smart watches, medical sensors, and other wearables.
Robotics and Automation
Semi-flex PCBs withstand repeated bending in moveable joints and arms. They also withstand vibration in robots and automated equipment.
Medical Devices
Semi-flex circuits can wrap around irregular-shaped medical devices for compact, lightweight designs. The durability also suits the dynamic flexing within medical equipment.
Consumer Electronics
Laptops, mobile phones, headphones, and handheld electronics leverage semi-flex PCBs to interconnect various hinged and jointed assemblies. The dynamic flex capability and reliability are valued in consumer devices.
Automotive Electronics
Semi-flex PCBs withstand mechanical shocks and vibrations in vehicle-mounted electronics. The reliability makes them well-suited for engine control units, dashboards, lighting, and in-car entertainment.
Industrial Electronics
In automation systems and motor drives, semi-flex PCBs endure continuous vibration and mechanical stresses better than rigid boards. They also facilitate assembly and maintenance with flex portions routed into tight spaces.
With their growing adoption across industries, semi-flex PCBs deliver reliable performance where moderate flex, vibration resistance, and compact design are important. Continued advances in flexible PCB technology and materials will expand their capabilities and potential applications in the future.
Frequently Asked Questions
Here are some common questions about semi-flexible PCBs:
What are the typical layer counts for semi-flex PCBs?
Semi-flex PCBs typically have 2 to 12 layers. High layer counts are possible but increase complexity and cost. For most applications, 2 to 6 layers are typical.
Can components be mounted on the flexible portions?
It is generally not recommended to place heavy or bulky components on the flexible areas. Only small, lightweight components like chips and resistors should be placed in flexible regions.
How long do semi-flex PCBs last in dynamic flexing applications?
With proper design, quality materials, and assembly, semi-flex PCBs can withstand over 100,000 dynamic flex cycles. This makes them suitable for moderate flex applications over the lifetime of most products.
What are some good PCB substrates for semi-flex circuits?
Polyimide is the most common flexible dielectric. Rigid layers are often standard FR-4 or high Tg materials like CEM-1, CEM-3 for higher temperature rating. Metal core layers also provide stiffness and heat dissipation.
Are semi-flex PCBs more expensive than rigid PCBs?
Yes, semi-flex PCBs typically cost 20-50% more than rigid boards. Additional processing steps are required to manufacture the flex layers and properly laminate them to the rigid layers. However, the benefits often justify the additional cost.
Conclusion
With their unique combination of moderate flexure, durability, and reliability, semi-flexible PCBs deliver valuable advantages in a wide range of electronics applications. As PCB and flex circuit technology continues advancing, semi-flex PCBs will take on growing importance thanks to their design flexibility, dynamic flex capability, and performance in demanding environments. With a sound understanding of their construction, properties, and applications, design engineers can effectively leverage semi-flex PCBs where rigid boards fall short.
Leave a Reply