Introduction to PCBs and Why Custom PCBs Matter
Printed Circuit Boards (PCBs) are the foundation of nearly all modern electronic devices. These flat boards, made from insulating materials like fiberglass, have conductive pathways etched or printed on them to create electrical connections between components. PCBs allow for the miniaturization and mass production of complex electronic circuits.
While off-the-shelf PCBs are readily available for many applications, custom PCBs offer several key advantages:
- Tailored Design: Custom PCBs are designed specifically for your project’s requirements, ensuring optimal performance and compatibility.
- Cost Efficiency: For larger production runs, custom PCBs can be more cost-effective than generic boards.
- Intellectual Property Protection: Custom designs help safeguard your proprietary technology from competitors.
- Flexibility: Custom PCBs allow for unique shapes, sizes, and features that may not be available in standard boards.
In this guide, we’ll walk you through the process of creating custom PCBs, from design to manufacturing, to help you achieve the best results for your project.
Understanding PCB Layers and Materials
PCB Layers
PCBs can be categorized by the number of conductive layers they contain:
Layers | Description |
---|---|
1 | Single-sided boards with components on one side and traces on the other |
2 | Double-sided boards with components and traces on both sides |
4+ | Multi-layer boards with inner layers for more complex routing |
The choice of layers depends on the complexity of your circuit and the space available for the board.
PCB Materials
The most common PCB materials are:
Material | Description | Applications |
---|---|---|
FR-4 | Flame-retardant fiberglass, affordable and widely used | General-purpose electronics |
High Tg FR-4 | Improved thermal stability for high-temperature environments | Automotive, aerospace |
Polyimide | Flexible and resistant to heat and chemicals | Wearables, medical devices |
Aluminum | Excellent heat dissipation properties | High-power LED lighting, RF/MW |
Consider your project’s specific requirements, such as temperature range, flexibility, and thermal management, when selecting a PCB material.
Designing Your Custom PCB
Schematic Capture
The first step in creating a custom PCB is to create a schematic diagram of your circuit. This can be done using Electronic Design Automation (EDA) software like KiCad, Eagle, or Altium Designer. The schematic captures the electrical connections between components and serves as a blueprint for the PCB layout.
PCB Layout
Once your schematic is complete, you can move on to the PCB layout. This involves arranging the components and routing the traces on the board. Key considerations during PCB layout include:
- Component Placement: Arrange components logically, minimizing trace lengths and considering heat dissipation and signal integrity.
- Trace Routing: Ensure traces are sized appropriately for current, and avoid sharp angles or close proximity to reduce electromagnetic interference (EMI).
- Ground Planes: Use ground planes to provide a low-impedance return path for currents and shield against EMI.
- Design Rule Check (DRC): Perform a DRC to ensure your layout meets manufacturing constraints and design best practices.
File Generation
After finalizing your PCB layout, generate the necessary files for manufacturing. The most common file formats are:
File Format | Description |
---|---|
Gerber | Industry-standard format containing information for each PCB layer |
Drill | Specifies hole sizes and locations for through-hole components |
Pick and Place | Defines component placement for automated assembly |
Bill of Materials (BOM) | Lists all components used in the design |
Ensure your files adhere to your chosen manufacturer’s specifications to avoid issues during production.
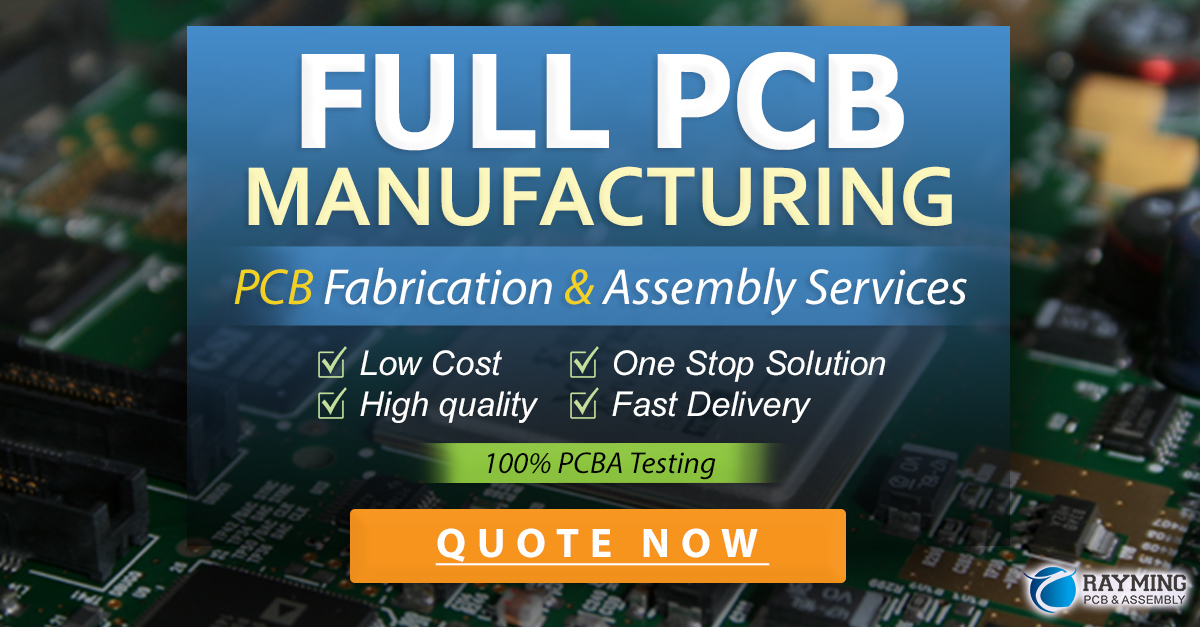
Manufacturing Your Custom PCB
Choosing a PCB Manufacturer
When selecting a PCB manufacturer, consider the following factors:
- Capabilities: Ensure the manufacturer can accommodate your PCB’s size, layercount, material, and special requirements (e.g., impedance control, fine-pitch BGA).
- Quality: Look for manufacturers with relevant certifications (e.g., ISO 9001, UL, IPC) and a proven track record of quality.
- Lead Time: Consider the manufacturer’s typical lead times and whether they offer expedited services if needed.
- Cost: Compare prices across manufacturers, but don’t sacrifice quality for cost.
PCB Fabrication Process
The PCB fabrication process typically involves the following steps:
- Copper Cladding: The base PCB material is coated with a thin layer of copper on one or both sides.
- Etching: Unwanted copper is removed using a chemical etching process, leaving only the desired traces and pads.
- Lamination: For multi-layer boards, the individual layers are aligned and bonded together under high pressure and temperature.
- Drilling: Holes are drilled for through-hole components and vias.
- Plating: Copper is electroplated onto the drilled holes to create electrical connections between layers.
- Solder Mask Application: A protective solder mask is applied to the board, exposing only the pads and other areas where components will be soldered.
- Silkscreen: Text and symbols are printed onto the board for component identification and assembly guidance.
- Surface Finish: A surface finish, such as HASL or ENIG, is applied to protect the copper and enhance solderability.
PCB Assembly
After fabrication, the PCB is ready for assembly. This can be done in-house or outsourced to a specialized assembly service. The assembly process typically includes:
- Solder Paste Application: Solder paste is applied to the pads using a stencil.
- Component Placement: Components are placed on the board, either manually or using automated pick-and-place machines.
- Reflow Soldering: The board is heated in a reflow oven, melting the solder paste and creating electrical connections.
- Inspection: The assembled board is inspected for defects, such as bridged connections or misaligned components.
Testing and Validation
Before putting your custom PCB into production, it’s essential to thoroughly test and validate its functionality and reliability.
Functional Testing
Functional testing verifies that your PCB performs as intended. This can include:
- Power-On Test: Ensuring the board powers on and all voltages are within expected ranges.
- Connectivity Test: Verifying that all connections are intact and there are no shorts or open circuits.
- Signal Integrity Test: Checking that signals are clean and free from excessive noise or distortion.
Environmental Testing
Environmental testing ensures your PCB can withstand the conditions it will face in its intended application. Common environmental tests include:
Test | Description |
---|---|
Thermal Cycling | Exposing the PCB to alternating high and low temperatures |
Vibration | Subjecting the PCB to vibration to check for mechanical stability |
Humidity | Exposing the PCB to high humidity to check for corrosion or degradation |
Reliability Testing
Reliability testing assesses the long-term durability of your PCB. This can involve:
- Accelerated Life Testing: Subjecting the PCB to increased stress (e.g., higher temperature, voltage) to estimate its lifespan under normal conditions.
- Burn-In Testing: Operating the PCB for an extended period to identify early failures.
By thoroughly testing your custom PCB, you can identify and address any issues before mass production, saving time and resources in the long run.
FAQ
What software do I need to design a custom PCB?
To design a custom PCB, you’ll need Electronic Design Automation (EDA) software. Popular options include KiCad (free and open-source), Autodesk Eagle (subscription-based), and Altium Designer (high-end, subscription-based).
How much does it cost to manufacture a custom PCB?
The cost of manufacturing a custom PCB depends on several factors, including the board’s size, layercount, material, quantity, and the manufacturer you choose. Generally, expect to pay more for smaller quantities, higher layercounts, and specialized materials. It’s best to request quotes from multiple manufacturers to compare prices.
What are the most common PCB assembly methods?
The two most common PCB assembly methods are through-hole and surface-mount.
- Through-Hole: Components have long leads that are inserted into holes drilled in the PCB and soldered on the opposite side. This method is easier for manual assembly but less space-efficient.
- Surface-Mount: Components are placed directly on the PCB’s surface and soldered in place. This method allows for smaller components and higher density but requires more precise placement.
How long does it take to manufacture a custom PCB?
Lead times for custom PCB manufacturing vary depending on the manufacturer and the complexity of your design. Typical lead times range from a few days to several weeks. Rush services may be available for an additional cost.
What certifications should I look for in a PCB manufacturer?
When choosing a PCB manufacturer, look for relevant certifications such as:
- ISO 9001: Quality management system certification
- UL: Safety certification for the United States
- IPC: Industry association certifications for PCB manufacturing and assembly standards (e.g., IPC-A-600, IPC-A-610)
These certifications demonstrate a manufacturer’s commitment to quality and adherence to industry best practices.
Conclusion
Creating a custom PCB involves multiple steps, from design to manufacturing and testing. By understanding the process and best practices, you can ensure your custom PCB meets your project’s requirements and performs reliably.
When designing your PCB, consider factors such as the number of layers, material choice, component placement, and trace routing. Generate the necessary manufacturing files and choose a reputable manufacturer with the capabilities and certifications to produce high-quality boards.
Finally, don’t overlook the importance of thorough testing and validation. By identifying and addressing issues early, you can save time and resources in the long run and ensure your custom PCB is ready for mass production and integration into your final product.
With careful planning and execution, custom PCBs can provide tailored, cost-effective solutions for your electronic projects, giving you a competitive edge in today’s rapidly evolving technology landscape.
Leave a Reply