What is a Blank PCB Board?
A blank PCB (Printed Circuit Board) is a bare board without any components soldered onto it. It consists of a substrate, usually made of fiberglass or other composite materials, with copper traces etched on one or both sides to form the electrical connections between components. The copper traces are typically coated with a layer of solder mask, which protects the traces and prevents accidental short circuits.
Blank PCBs come in various sizes, shapes, and thicknesses, depending on the specific application and design requirements. They can be single-sided (copper traces on one side), double-sided (copper traces on both sides), or multi-layered (multiple layers of copper traces sandwiched between insulating layers).
Types of Blank PCB Boards
There are several types of blank PCB boards, each with its own characteristics and applications:
Type | Description | Applications |
---|---|---|
FR-4 | Made of fiberglass reinforced epoxy laminate, excellent mechanical and electrical properties | High-frequency circuits, industrial electronics, medical devices |
Aluminum | Uses aluminum as the substrate, provides excellent heat dissipation | Power electronics, LED lighting, automotive electronics |
Flexible | Made of flexible materials like polyimide, can bend and conform to various shapes | Wearable electronics, aerospace, medical implants |
Rigid-Flex | Combines rigid and flexible sections, allows for 3D packaging and space savings | Aerospace, military, high-density electronics |
High Tg | Uses high glass transition temperature materials, withstands higher temperatures | Automotive, aerospace, high-power applications |
Manufacturing Process of Blank PCB Boards
The manufacturing process of blank PCB boards involves several steps:
-
Design: The PCB layout is designed using specialized software, following the schematic and component placement requirements.
-
Printing: The design is printed onto a photosensitive film or directly onto the copper-clad laminate using a laser printer or plotter.
-
Exposure: The photosensitive layer on the copper-clad laminate is exposed to UV light through the printed film, hardening the exposed areas.
-
Developing: The unexposed areas of the photosensitive layer are removed using a chemical developer, leaving the desired copper traces protected.
-
Etching: The exposed copper is removed using an etching solution, typically ferric chloride or ammonium persulfate, leaving only the desired copper traces.
-
Stripping: The remaining photosensitive layer is stripped away, revealing the bare copper traces.
-
Solder Mask Application: A layer of solder mask is applied to the board, protecting the copper traces and preventing accidental short circuits.
-
Silkscreen: A silkscreen layer is added to the board, providing text and symbols for component placement and identification.
-
Surface Finish: A surface finish, such as HASL (Hot Air Solder Leveling), ENIG (Electroless Nickel Immersion Gold), or OSP (Organic Solderability Preservative), is applied to the exposed copper to improve solderability and protect against oxidation.
What Are the Advantages of Using Blank PCB Boards?
Using blank PCB boards offers several advantages over other methods of creating electronic circuits:
-
Consistency: PCBs provide a consistent and reliable platform for building electronic circuits, ensuring that all connections are made accurately and consistently every time.
-
Compact Size: PCBs allow for the miniaturization of electronic devices by enabling the dense packing of components and the use of multi-layer designs.
-
Improved Performance: The copper traces on a PCB provide low-resistance pathways for electrical signals, reducing noise and improving overall circuit performance.
-
Increased Reliability: PCBs are designed to withstand the stresses of manufacturing and use, resulting in more reliable and durable electronic devices.
-
Cost-Effective: Mass production of PCBs is cost-effective compared to other methods of creating electronic circuits, such as point-to-point wiring or wire wrapping.
-
Simplified Assembly: PCBs simplify the assembly process by providing a clear layout for component placement and soldering, reducing the likelihood of errors and improving production efficiency.
What Are the Different PCB Board Materials?
PCB board materials play a crucial role in determining the performance, reliability, and cost of the final product. The choice of material depends on factors such as the intended application, operating environment, frequency, and budget. Some common PCB board materials include:
FR-4
FR-4 is the most widely used PCB material, consisting of a fiberglass reinforced epoxy laminate. It offers excellent mechanical and electrical properties, making it suitable for a wide range of applications, including:
- Consumer electronics
- Industrial control systems
- Telecommunications equipment
- Medical devices
Aluminum
Aluminum PCBs use aluminum as the substrate material, providing excellent thermal conductivity and heat dissipation. This makes them ideal for applications that generate significant amounts of heat, such as:
- Power electronics
- LED lighting
- Automotive electronics
- High-power amplifiers
Flexible PCBs
Flexible PCBs are made using flexible materials, such as polyimide or polyester, allowing them to bend and conform to various shapes. They are commonly used in applications that require flexibility or space savings, such as:
- Wearable electronics
- Aerospace and military equipment
- Medical implants
- Portable devices
Rigid-Flex PCBs
Rigid-flex PCBs combine rigid and flexible sections, offering the benefits of both types of materials. They allow for 3D packaging and space savings, making them suitable for applications such as:
- Aerospace and military equipment
- High-density electronics
- Medical devices
- Automotive electronics
High Tg Materials
High Tg (glass transition temperature) materials are designed to withstand higher temperatures compared to standard PCB materials. They are used in applications that expose the PCB to elevated temperatures, such as:
- Automotive electronics
- Aerospace and military equipment
- High-power applications
- Industrial control systems
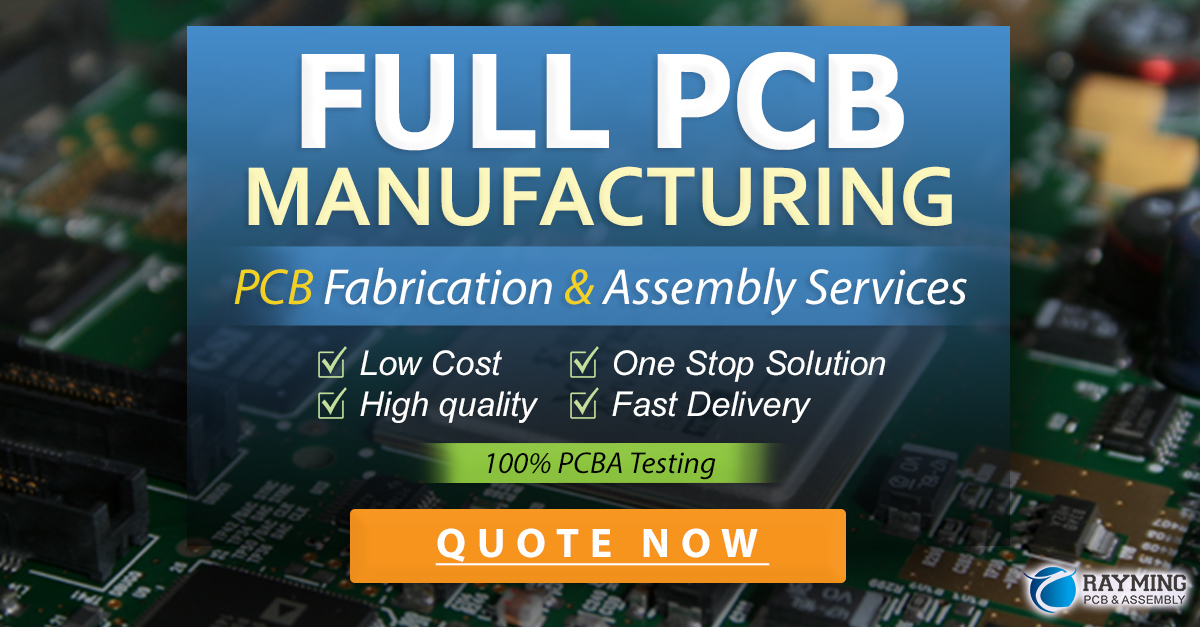
What Are the Different Types of PCB Board Finishes?
PCB board finishes are applied to the exposed copper surfaces of a PCB to improve solderability, protect against oxidation, and enhance the appearance of the board. The choice of finish depends on factors such as the intended application, environmental requirements, and cost. Some common PCB board finishes include:
HASL (Hot Air Solder Leveling)
HASL is a widely used and cost-effective finish that involves dipping the PCB in molten solder and then using hot air to remove excess solder, creating a smooth, level surface. It offers good solderability and is suitable for most general-purpose applications.
ENIG (Electroless Nickel Immersion Gold)
ENIG is a high-quality finish that consists of a layer of nickel followed by a thin layer of gold. It provides excellent solderability, corrosion resistance, and a flat surface finish, making it suitable for fine-pitch components and high-reliability applications.
OSP (Organic Solderability Preservative)
OSP is a thin, organic coating applied to the copper surfaces of a PCB. It provides temporary protection against oxidation and improves solderability. OSP is a cost-effective option for applications with short storage times and minimal environmental exposure.
Immersion Silver
Immersion silver is a thin layer of silver applied to the copper surfaces of a PCB. It offers excellent solderability and conductivity, making it suitable for high-frequency applications. However, it can tarnish over time and may not be suitable for some environments.
Immersion Tin
Immersion tin is a thin layer of tin applied to the copper surfaces of a PCB. It provides good solderability and is a cost-effective alternative to HASL. However, it can be prone to tin whiskers, which can cause short circuits in some applications.
What Are the Design Considerations for Blank PCB Boards?
When designing a blank PCB board, several factors must be considered to ensure optimal performance, reliability, and manufacturability. Some key design considerations include:
-
Material Selection: Choose the appropriate PCB material based on the intended application, operating environment, frequency, and budget.
-
Thickness: Select the appropriate board thickness based on the mechanical and electrical requirements of the design. Thicker boards provide better mechanical stability but may be more challenging to manufacture.
-
Copper Weight: Specify the appropriate copper weight for the traces based on the current-carrying requirements and the desired trace width and spacing.
-
Trace Width and Spacing: Design traces with appropriate width and spacing to ensure signal integrity, minimize crosstalk, and meet the current-carrying requirements of the circuit.
-
Via Size and Placement: Choose the appropriate via size and placement to ensure reliable electrical connections between layers while minimizing the impact on signal integrity.
-
Component Placement: Place components in a way that minimizes the length of critical signal paths, reduces electromagnetic interference, and facilitates efficient assembly.
-
Thermal Management: Consider the thermal requirements of the design and incorporate features such as thermal vias, heat sinks, or metal-core PCBs to dissipate heat effectively.
-
Manufacturing Constraints: Ensure that the design is compatible with the manufacturing capabilities of the chosen PCB fabricator, including minimum feature sizes, layer count, and drilling capabilities.
-
Testing and Inspection: Incorporate features that facilitate testing and inspection, such as test points, fiducial markers, and clear silkscreen labeling.
-
Cost Optimization: Balance the design requirements with the cost constraints of the project, considering factors such as material choice, layer count, and manufacturing volume.
By carefully considering these design factors and working closely with the PCB fabricator, designers can create blank PCB boards that meet the specific requirements of their applications while ensuring optimal performance, reliability, and cost-effectiveness.
Frequently Asked Questions (FAQ)
1. What is the difference between a single-sided and double-sided blank PCB board?
A single-sided blank PCB board has copper traces on only one side of the substrate, while a double-sided board has copper traces on both sides. Double-sided boards offer more design flexibility and higher component density but are more complex and expensive to manufacture.
2. Can I use a blank PCB board for high-frequency applications?
Yes, blank PCB boards can be used for high-frequency applications, but the choice of material and design considerations become more critical. Materials with low dielectric constants and dissipation factors, such as Rogers or Teflon, are often used for high-frequency PCBs. Proper trace routing, impedance control, and shielding techniques must also be employed to ensure signal integrity.
3. What is the minimum feature size achievable on a blank PCB board?
The minimum feature size depends on the capabilities of the PCB fabricator and the chosen manufacturing process. For standard PCB manufacturing, minimum trace widths and spacings of around 0.1 mm (4 mil) are achievable. Advanced processes, such as HDI (High-Density Interconnect) or mSAP (modified Semi-Additive Process), can achieve even smaller feature sizes, down to 0.05 mm (2 mil) or less.
4. How do I choose the right surface finish for my blank PCB board?
The choice of surface finish depends on factors such as the intended application, environmental requirements, solderability, and cost. HASL is a cost-effective option for general-purpose applications, while ENIG provides excellent solderability and corrosion resistance for high-reliability applications. OSP is suitable for applications with short storage times, while immersion silver and tin offer good solderability but may have limitations in certain environments.
5. Can I design and manufacture a blank PCB board myself?
Designing and manufacturing a blank PCB board requires specialized knowledge, software, and equipment. While it is possible to design a PCB using CAD software and manufacture it using a small-scale etching process, it is generally more practical and cost-effective to work with a professional PCB fabricator for most applications. PCB fabricators have the expertise, equipment, and quality control processes in place to produce high-quality, reliable PCBs in volume.
Leave a Reply