Introduction to 10-layer PCBs
In today’s world of advanced electronics, printed circuit boards (PCBs) play a crucial role in connecting and supporting various components. As technology progresses, the demand for more complex and high-density PCBs increases. This is where 10-layer PCBs come into the picture. These multilayer boards offer numerous advantages over their simpler counterparts, including improved signal integrity, reduced electromagnetic interference (EMI), and better power distribution.
What is a 10-layer PCB?
A 10-layer PCB is a printed circuit board that consists of ten conductive copper layers laminated together with insulating material. These layers are interconnected through vias, which are small holes drilled through the board and plated with conductive material. The increased number of layers allows for higher component density and more complex routing compared to standard double-sided or four-layer PCBs.
Advantages of using 10-layer PCBs
- Increased routing density
- Better signal integrity
- Reduced electromagnetic interference (EMI)
- Improved power distribution
- Smaller form factor
Designing a 10-layer PCB
Understanding the layer stack-up
The layer stack-up is a critical aspect of 10-layer PCB design. It determines the arrangement of the conductive and insulating layers, as well as the thickness of each layer. A typical 10-layer PCB stack-up may look like this:
Layer | Material | Thickness (mm) |
---|---|---|
1 | Copper | 0.035 |
2 | Prepreg | 0.2 |
3 | Copper | 0.035 |
4 | Prepreg | 0.2 |
5 | Copper | 0.035 |
6 | Core | 0.4 |
7 | Copper | 0.035 |
8 | Prepreg | 0.2 |
9 | Copper | 0.035 |
10 | Prepreg | 0.2 |
11 | Copper | 0.035 |
Signal integrity and power distribution
When designing a 10-layer PCB, it is essential to consider signal integrity and power distribution. Proper signal routing and impedance control help minimize crosstalk and maintain signal quality. Power planes should be strategically placed to provide stable voltage to components while minimizing noise and EMI.
Thermal management
With the increased component density and power requirements of 10-layer PCBs, thermal management becomes a critical concern. Designers must carefully consider the placement of components and the use of thermal vias to dissipate heat effectively. Thermal simulations can help identify potential hot spots and optimize the design for better heat dissipation.
Manufacturing 10-layer PCBs
Choosing the right PCB manufacturer
Selecting a reliable and experienced PCB manufacturer is crucial when it comes to fabricating 10-layer boards. Look for manufacturers with a proven track record of producing high-quality, complex PCBs. Consider factors such as their manufacturing capabilities, quality control processes, and customer support.
Material selection
The choice of materials for a 10-layer PCB can significantly impact its performance and reliability. Common base materials include FR-4, high-Tg FR-4, and polyimide. The choice of material depends on the specific requirements of the application, such as temperature resistance, dielectric constant, and mechanical stability.
Quality control and testing
Rigorous quality control and testing are essential to ensure the reliability and functionality of 10-layer PCBs. Manufacturers should employ advanced inspection techniques, such as automated optical inspection (AOI) and X-ray inspection, to detect any defects or anomalies. Electrical testing, including continuity, insulation resistance, and high-potential (HiPot) tests, help verify the board’s performance and safety.
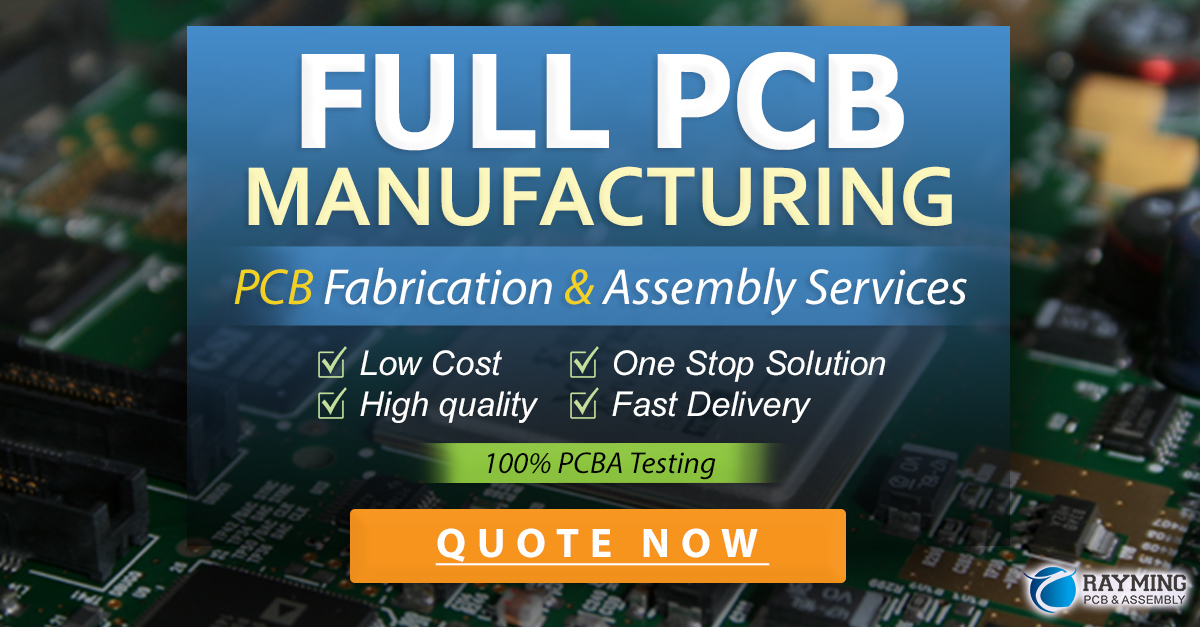
Applications of 10-layer PCBs
High-speed digital systems
10-layer PCBs are commonly used in high-speed digital systems, such as high-performance computing, networking equipment, and telecommunications infrastructure. The increased layer count allows for better signal integrity and reduced crosstalk, which are critical for high-speed data transmission.
Aerospace and defense
The aerospace and defense industries often require highly reliable and compact electronic systems. 10-layer PCBs offer the necessary density and performance to meet these demanding requirements. The use of specialized materials and manufacturing processes ensures that these boards can withstand harsh environmental conditions and extreme temperatures.
Medical devices
Medical devices, such as imaging equipment and patient monitoring systems, rely on complex and reliable electronics. 10-layer PCBs provide the necessary density and signal integrity to support these advanced medical applications. The use of biocompatible materials and strict manufacturing controls ensures that these boards meet the stringent safety and reliability standards required for medical devices.
Conclusion
10-layer PCBs offer numerous advantages over simpler board designs, making them an essential component in today’s advanced electronic systems. By understanding the design considerations, manufacturing processes, and applications of these complex boards, engineers and designers can create high-performance, reliable products that meet the demands of modern technology.
Frequently Asked Questions (FAQ)
1. What is the typical turnaround time for a 10-layer PCB?
The turnaround time for a 10-layer PCB depends on the complexity of the design and the chosen manufacturer. On average, the fabrication process can take between 2-4 weeks, but expedited services may be available for an additional cost.
2. How much does a 10-layer PCB cost compared to a 4-layer PCB?
The cost of a 10-layer PCB is significantly higher than that of a 4-layer PCB due to the increased complexity of the manufacturing process and the additional materials required. The exact price difference depends on factors such as the board size, quantity, and chosen manufacturer, but it can be several times more expensive.
3. Can I use standard FR-4 material for a 10-layer PCB?
While standard FR-4 can be used for 10-layer PCBs, it may not be the optimal choice for high-performance applications. High-Tg FR-4 or other specialized materials may be better suited for designs that require improved thermal stability, lower dielectric constant, or better mechanical properties.
4. What are the minimum trace width and spacing for a 10-layer PCB?
The minimum trace width and spacing for a 10-layer PCB depend on the manufacturing capabilities of the chosen PCB fabricator. Typically, trace widths and spacings can be as small as 0.075-0.1 mm (3-4 mils), but it is essential to consult with the manufacturer to ensure that the design is compatible with their production capabilities.
5. How do I ensure proper signal integrity in a 10-layer PCB?
To ensure proper signal integrity in a 10-layer PCB, designers should follow best practices such as:
- Proper impedance control and matching
- Strategic placement of power and ground planes
- Use of shielding and ground pour to reduce EMI
- Careful consideration of via placement and design
- Simulation and analysis to identify and mitigate potential issues
By adhering to these guidelines and working closely with experienced PCB manufacturers, designers can create high-performance 10-layer PCBs that meet the demanding requirements of today’s advanced electronic systems.
Leave a Reply