Introduction to ICT-PCB Testing
In the world of electronics manufacturing, producing high-quality printed circuit boards (PCBs) is crucial for ensuring the reliability and functionality of the end product. One of the most effective methods for achieving this goal is through the use of in-circuit testing (ICT). ICT is a powerful technique that allows manufacturers to identify and correct defects in PCBs before they are assembled into the final product.
What is ICT?
In-circuit testing is an automated testing method that verifies the functionality of individual components on a PCB by directly probing their pins. This process involves using a specialized test fixture that makes contact with the PCB’s test points, allowing the tester to apply signals and measure responses from each component.
Benefits of ICT-PCB Testing
- Early defect detection
- Improved product quality
- Reduced manufacturing costs
- Faster time-to-market
- Enhanced customer satisfaction
How ICT Works
The ICT Process
- Test Fixture Preparation
- Custom-designed test fixtures are created to match the specific PCB layout
-
Test probes are positioned to make contact with the PCB’s test points
-
Test Program Development
- A test program is created using the PCB’s schematic and bill of materials (BOM)
-
The program defines the test sequence, signal application, and expected responses
-
PCB Loading
- The PCB is placed into the test fixture
-
The fixture is then loaded into the ICT machine
-
Test Execution
- The ICT machine runs the test program
- Signals are applied to the PCB’s components through the test probes
-
Component responses are measured and compared to expected values
-
Result Analysis
- Test results are analyzed to identify any defects or anomalies
- Defective PCBs are marked for repair or rework
Common Tests Performed by ICT
Test Type | Description |
---|---|
Continuity Test | Verifies that all connections on the PCB are intact and free from short circuits |
Resistance Test | Measures the resistance of components and traces to ensure they are within specified tolerances |
Capacitance Test | Checks the capacitance values of capacitors to ensure they are within acceptable ranges |
Inductance Test | Measures the inductance of inductors and transformers |
Diode Test | Verifies the polarity and forward voltage drop of diodes |
Transistor Test | Checks the functionality of transistors by measuring their gain and leakage current |
Implementing ICT in Your Manufacturing Process
Step 1: Design for Testability (DFT)
To effectively implement ICT, it is essential to design your PCBs with testability in mind. This involves:
- Adding test points to the PCB layout
- Ensuring adequate probe access to components
- Minimizing the use of surface-mount devices (SMDs) on the bottom side of the PCB
- Providing clear labeling for test points and components
Step 2: Select an ICT System
When choosing an ICT system for your manufacturing process, consider the following factors:
- Test coverage requirements
- PCB complexity and component density
- Testing speed and throughput
- Ease of programming and maintenance
- Integration with other manufacturing processes
Step 3: Develop Test Fixtures and Programs
- Work with an experienced test fixture provider to design and manufacture custom fixtures for your PCBs
- Collaborate with your ICT vendor to develop comprehensive test programs that cover all critical components and functions
Step 4: Integrate ICT into Your Quality Control Process
- Establish clear testing protocols and acceptance criteria
- Train your production staff on the proper use and maintenance of the ICT system
- Regularly review and analyze test results to identify trends and areas for improvement
- Use ICT data to drive continuous improvement initiatives in your manufacturing process
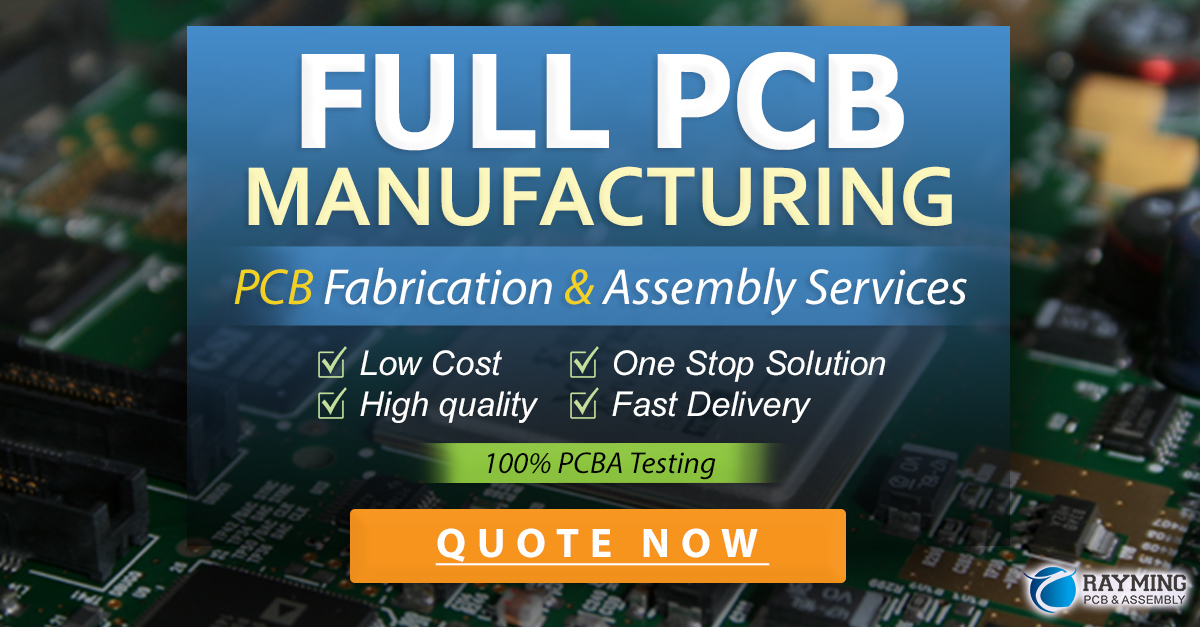
Best Practices for Effective ICT-PCB Testing
- Keep your test fixtures clean and well-maintained to ensure reliable contact with the PCB
- Regularly calibrate your ICT system to maintain accuracy and consistency
- Optimize your test programs to minimize false failures and improve testing efficiency
- Implement version control for your test programs to track changes and maintain traceability
- Foster a culture of continuous improvement by encouraging feedback and suggestions from your production team
Case Studies
Company A: Automotive Electronics Manufacturer
Company A, a leading automotive electronics manufacturer, implemented ICT in their production line to improve the quality and reliability of their PCBs. By investing in a state-of-the-art ICT system and training their staff on its proper use, they were able to:
- Reduce defect rates by 85%
- Improve first-pass yield from 75% to 95%
- Decrease rework costs by 60%
- Shorten their time-to-market by 25%
Company B: Medical Device Manufacturer
Company B, a medical device manufacturer, faced challenges with the reliability of their products due to PCB defects. By implementing ICT and optimizing their test coverage, they achieved:
- A 90% reduction in field failures
- Improved customer satisfaction ratings from 3.5 to 4.8 out of 5
- A 40% reduction in warranty claims
- Compliance with stringent medical device quality standards
Frequently Asked Questions (FAQ)
1. How does ICT differ from other PCB testing methods?
ICT differs from other testing methods, such as functional testing or boundary scan, in that it directly probes the pins of individual components on the PCB. This allows for a more comprehensive and detailed assessment of each component’s functionality.
2. Can ICT detect all types of PCB defects?
While ICT is a powerful tool for identifying many types of defects, it may not detect all issues, such as those related to signal integrity or timing. It is essential to use ICT in conjunction with other testing methods to ensure comprehensive coverage.
3. Is ICT suitable for testing high-volume production runs?
Yes, ICT is well-suited for high-volume production testing due to its automated nature and fast test execution times. However, the initial investment in test fixture development and programming may be higher compared to other methods.
4. How long does it take to develop an ICT test program?
The time required to develop an ICT test program varies depending on the complexity of the PCB and the number of components to be tested. On average, it can take several weeks to create a comprehensive test program.
5. Can ICT be used for testing flexible or rigid-flex PCBs?
Yes, ICT can be used to test flexible and rigid-flex PCBs, but it may require specialized test fixtures and probing techniques to accommodate the unique characteristics of these PCB types.
Conclusion
In-circuit testing is a powerful tool for ensuring the quality and reliability of PCBs in electronics manufacturing. By probing individual components and verifying their functionality, ICT helps identify defects early in the production process, reducing costs and improving overall product quality.
To successfully implement ICT in your manufacturing process, it is crucial to design your PCBs for testability, select the right ICT system, develop comprehensive test programs, and integrate ICT into your quality control process. By following best practices and continuously improving your testing procedures, you can unlock the full potential of ICT and produce high-quality PCBs that meet the demands of your customers.
Leave a Reply