Introduction to PCB Cutting
Printed Circuit Boards (PCBs) are the backbone of modern electronics. They provide the electrical connections and mechanical support for various components in electronic devices. PCBs come in different shapes and sizes, and often need to be cut to fit specific design requirements. PCB cutting is an essential skill for electronics hobbyists, engineers, and technicians.
In this comprehensive guide, we will cover everything you need to know about PCB cutting. From the tools and techniques to safety precautions and best practices, we’ll provide you with the knowledge and skills to cut PCBs like a pro.
Why Cut PCBs?
There are several reasons why you might need to cut a PCB:
-
Prototyping: When designing a new electronic device, you may need to create custom-shaped PCBs to fit the enclosure or optimize the layout.
-
Modification: Sometimes, you may need to modify an existing PCB by removing unwanted sections or reshaping it to accommodate new components.
-
Repair: If a PCB is damaged, cutting out the affected area and replacing it with a new piece can be a cost-effective repair solution.
-
Salvaging: When recycling old electronic devices, you may want to cut out useful sections of the PCB to reuse in other projects.
Tools for PCB Cutting
To cut PCBs effectively, you’ll need the right tools. Here are some essential tools for PCB cutting:
PCB Cutting Shears
PCB cutting shears are specialized scissors designed for cutting PCBs. They have strong, sharp blades that can easily cut through the fiberglass substrate and copper traces. PCB cutting shears are ideal for making straight cuts and trimming the edges of PCBs.
Rotary Tools
Rotary tools, such as Dremel or similar brands, are versatile tools that can be used for PCB cutting. With the right attachments, such as cutting wheels or router bits, rotary tools can make precise cuts, holes, and shapes in PCBs.
Nibbling Tools
Nibbling tools, also known as nibbler punches, are hand-operated tools that can cut small, precise shapes in PCBs. They work by punching out small bits of the PCB material with each squeeze of the handle. Nibbling tools are great for making intricate cuts and shapes.
Saws
For thicker PCBs or larger cutting jobs, you may need to use a saw. There are several types of saws suitable for PCB cutting:
- Hacksaw: A fine-toothed hacksaw can be used to make straight cuts in PCBs.
- Bandsaw: A bandsaw with a fine-toothed blade can make precise, curved cuts in PCBs.
- Scroll saw: A scroll saw with a fine-toothed blade is ideal for making intricate, curved cuts in PCBs.
Tool | Pros | Cons |
---|---|---|
PCB Cutting Shears | Easy to use, makes straight cuts | Limited to straight cuts and edge trimming |
Rotary Tools | Versatile, can make precise cuts and shapes | Requires skill and practice to use effectively |
Nibbling Tools | Makes intricate cuts and shapes | Slow process, limited to small cuts |
Saws | Can cut thicker PCBs and make larger cuts | Requires careful setup and skill to use safely |
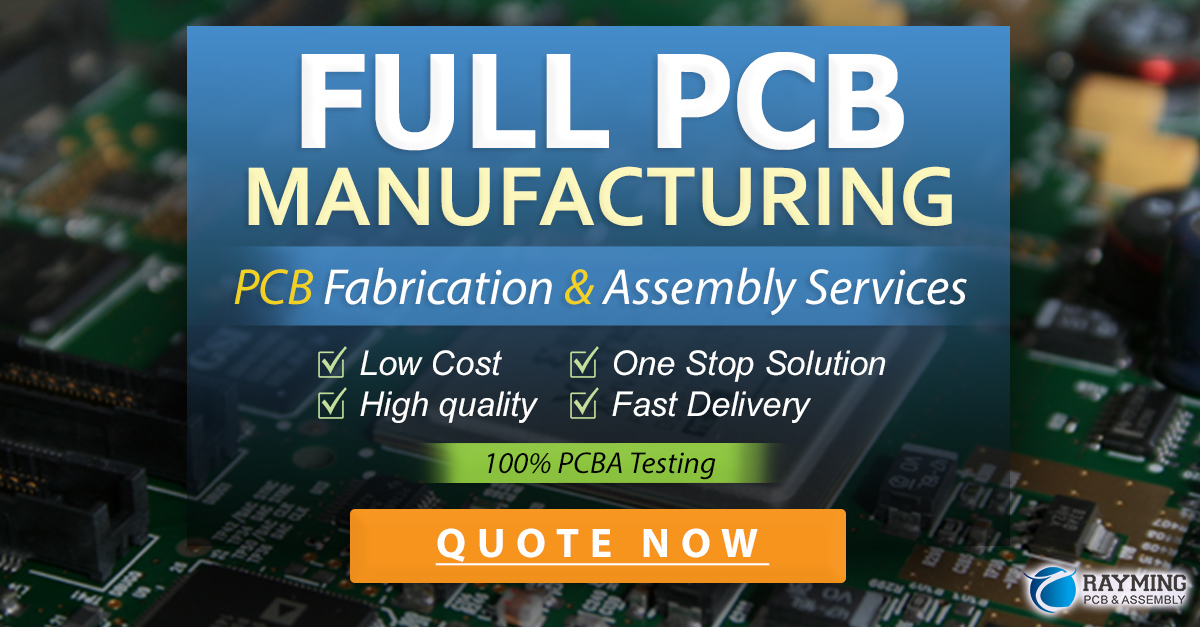
Safety Precautions
Before you start cutting PCBs, it’s crucial to take proper safety precautions. PCBs contain fiberglass and other materials that can produce harmful dust when cut. Always follow these safety guidelines:
- Wear protective eyewear to prevent dust and debris from entering your eyes.
- Use a dust mask or respirator to avoid inhaling PCB dust.
- Work in a well-ventilated area to minimize dust exposure.
- Wear gloves to protect your hands from sharp edges and potential cuts.
- Properly dispose of PCB dust and debris, as it may contain hazardous substances.
PCB Cutting Techniques
Now that you have the tools and safety equipment, let’s explore some PCB cutting techniques.
Straight Cuts
For making straight cuts, PCB cutting shears or a hacksaw are the best tools. Here’s how to make a straight cut:
- Measure and mark the desired cut line on the PCB using a ruler and a permanent marker.
- Align the PCB cutting shears or hacksaw blade with the cut line.
- Apply steady pressure and cut along the line, keeping the blade perpendicular to the PCB surface.
- Smooth any rough edges with a file or sandpaper.
Curved Cuts
To make curved cuts, a rotary tool with a cutting wheel or a scroll saw with a fine-toothed blade are the preferred tools. Here’s the process:
- Mark the desired cut line on the PCB.
- For a rotary tool, secure the PCB in a vise or clamp, and carefully guide the cutting wheel along the line. For a scroll saw, place the PCB on the saw table and follow the cut line.
- Make several passes, gradually deepening the cut with each pass.
- Smooth the edges with a file or sandpaper.
Holes and Cutouts
To make holes and cutouts in PCBs, a rotary tool with a router bit or a nibbling tool can be used. Here’s how:
- Mark the location and size of the hole or cutout on the PCB.
- For a rotary tool, secure the PCB and carefully plunge the router bit into the PCB at the marked location. Follow the outline of the cutout.
- For a nibbling tool, align the punch with the marked location and squeeze the handle to remove small bits of the PCB. Continue punching around the outline of the cutout.
- Smooth the edges of the hole or cutout with a file or sandpaper.
Best Practices for PCB Cutting
To achieve the best results when cutting PCBs, follow these best practices:
- Always use sharp, well-maintained tools to ensure clean, precise cuts.
- Secure the PCB properly to prevent it from moving or vibrating during cutting.
- Take your time and make multiple, shallow passes rather than trying to cut through the PCB in one go.
- Keep the cutting tools perpendicular to the PCB surface to avoid angled or uneven cuts.
- Clean the PCB thoroughly after cutting to remove any dust or debris.
FAQ
Can I use regular scissors to cut PCBs?
No, regular scissors are not suitable for cutting PCBs. The fiberglass substrate and copper traces are too hard and dense for regular scissors to cut through effectively. Using regular scissors may damage the PCB and the scissors. Always use dedicated PCB cutting shears or other specialized tools.
How do I prevent the copper traces from tearing when cutting PCBs?
To prevent copper traces from tearing, use sharp, well-maintained tools and make clean, perpendicular cuts. Avoid twisting or bending the PCB while cutting, as this can cause the traces to tear. If you’re using a rotary tool or saw, make sure to use a fine-toothed blade and take shallow, gradual passes to minimize stress on the traces.
Can I cut PCBs with a laser cutter?
Yes, laser cutters can be used to cut PCBs, especially for intricate designs or high-volume production. However, laser cutting requires specialized equipment and may not be practical for hobbyists or small-scale projects. Laser cutting can also produce harmful fumes, so proper ventilation and safety precautions are essential.
How do I dispose of PCB dust and debris?
PCB dust and debris may contain hazardous substances, so it’s important to dispose of them properly. Collect the dust and debris in a sealed container, such as a plastic bag, and label it clearly. Contact your local waste management authority for guidelines on disposing of electronic waste in your area. Do not throw PCB dust in the regular trash or down the drain.
Can I reuse the cut-off pieces of PCBs?
Yes, you can reuse cut-off pieces of PCBs in other projects, as long as they are in good condition and have the required features. Before reusing PCB pieces, clean them thoroughly to remove any dust or debris. Inspect the pieces for any damage or defects that may affect their functionality. If the pieces are suitable, you can incorporate them into your new projects, saving materials and reducing electronic waste.
Conclusion
PCB cutting is a valuable skill for anyone involved in electronics projects. With the right tools, techniques, and safety precautions, you can create custom-shaped PCBs, modify existing designs, and salvage useful components. By following the guidelines in this comprehensive guide, you’ll be well-equipped to tackle any PCB cutting task with confidence and precision.
Remember to always prioritize safety, use the appropriate tools for the job, and take your time to ensure clean, accurate cuts. With practice and patience, you’ll be cutting PCBs like a pro in no time.
Happy PCB cutting!
Leave a Reply