Understanding the Importance of High TG PCBs
In today’s fast-paced world of electronics, devices are becoming increasingly complex and are expected to perform under a wide range of environmental conditions. One of the most critical factors that can impact the performance and longevity of electronic devices is temperature. Extreme temperatures can cause standard PCBs to warp, delaminate, or even fail, leading to device malfunctions and shortened lifespans.
High TG PCBs are designed to address these challenges by utilizing specialized materials and manufacturing processes that enable them to maintain their structural integrity and electrical properties at elevated temperatures. This makes them an essential component in various industries, including:
- Automotive electronics
- Aerospace and defense systems
- Industrial automation and control
- High-power LED lighting
- Medical devices
- Telecommunications equipment
By understanding the importance of High TG PCBs and their unique properties, engineers and designers can make informed decisions when selecting the most suitable PCB materials for their projects.
Properties and Benefits of High TG PCBs
Thermal Stability
The primary advantage of High TG PCBs is their enhanced thermal stability. These PCBs are made using substrate materials with higher glass transition temperatures, such as polyimide or high-performance epoxy resins. The higher TG values enable the PCBs to maintain their mechanical and electrical properties at elevated temperatures, typically ranging from 170°C to 260°C, depending on the specific material used.
Material | Glass Transition Temperature (TG) |
---|---|
FR-4 | 130°C – 140°C |
High TG FR-4 | 170°C – 180°C |
Polyimide | 250°C – 260°C |
The thermal stability of High TG PCBs offers several benefits, including:
- Reduced thermal expansion and warping
- Improved solder joint reliability
- Enhanced durability in high-temperature environments
- Increased product lifespan and reliability
Electrical Performance
In addition to their thermal stability, High TG PCBs also exhibit excellent electrical performance. The specialized substrate materials used in these PCBs often have lower dielectric constants and dissipation factors compared to standard FR-4 materials. This results in improved signal integrity, reduced signal loss, and better high-frequency performance.
Material | Dielectric Constant (at 1 GHz) | Dissipation Factor (at 1 GHz) |
---|---|---|
FR-4 | 4.2 – 4.5 | 0.02 – 0.03 |
High TG FR-4 | 3.8 – 4.2 | 0.01 – 0.02 |
Polyimide | 3.4 – 3.6 | 0.006 – 0.008 |
The enhanced electrical properties of High TG PCBs make them well-suited for applications that require high-speed data transmission, such as telecommunications equipment and high-frequency circuits.
Mechanical Strength
High TG PCBs also demonstrate superior mechanical strength and durability compared to standard PCBs. The high-performance substrate materials used in these PCBs offer better resistance to mechanical stress, vibration, and impact. This makes High TG PCBs an ideal choice for applications that require rugged and reliable performance, such as automotive electronics and aerospace systems.
Manufacturing Process of High TG PCBs
The manufacturing process of High TG PCBs is similar to that of standard PCBs, with a few key differences in material selection and processing parameters. The basic steps involved in the production of High TG PCBs include:
-
Material Selection: High TG substrate materials, such as polyimide or high-performance epoxy resins, are chosen based on the specific requirements of the application.
-
Circuit Design: The circuit layout is designed using CAD software, taking into account the unique properties and characteristics of the High TG substrate material.
-
Lamination: The substrate layers are laminated together using high-temperature and high-pressure processes to ensure proper bonding and dimensional stability.
-
Drilling: Holes are drilled through the laminated board to accommodate component leads and vias.
-
Plating: The drilled holes are plated with copper to establish electrical connections between layers.
-
Etching: The unwanted copper is removed from the board using a chemical etching process, leaving only the desired circuit traces.
-
Solder Mask Application: A protective solder mask is applied to the board to prevent short circuits and improve solderability.
-
Surface Finishing: The exposed copper areas are coated with a surface finish, such as ENIG (Electroless Nickel Immersion Gold) or OSP (Organic Solderability Preservative), to enhance solderability and protect against oxidation.
-
Silkscreen Printing: Labels, logos, and component identifiers are printed on the board using a silkscreen printing process.
-
Quality Control: The finished High TG PCBs undergo rigorous quality control inspections to ensure they meet the required specifications and performance standards.
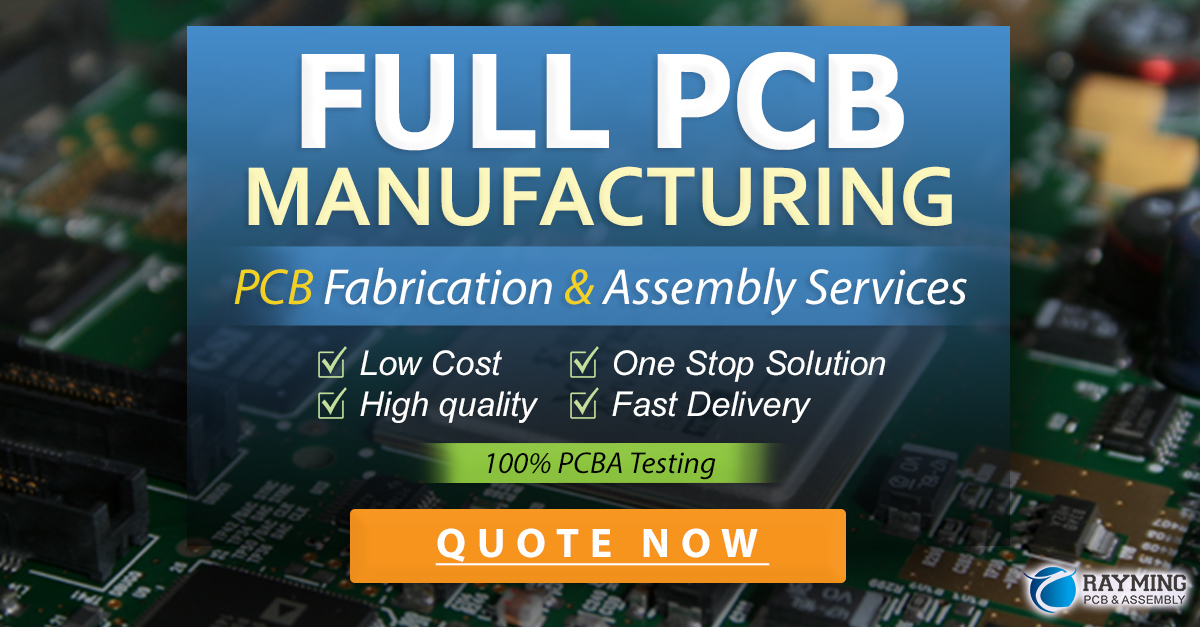
Applications of High TG PCBs
High TG PCBs find applications in a wide range of industries and products where thermal stability, reliability, and high-performance are critical. Some of the most common applications include:
Automotive Electronics
The automotive industry has seen a significant increase in the use of electronic systems, such as engine control units, infotainment systems, and advanced driver assistance systems (ADAS). These electronic components are often exposed to harsh environmental conditions, including high temperatures under the hood and extreme temperature fluctuations. High TG PCBs are well-suited for automotive applications, as they can withstand the demanding thermal requirements and ensure reliable operation over the vehicle’s lifespan.
Aerospace and Defense Systems
Aerospace and defense applications require PCBs that can operate reliably in extreme conditions, including high altitudes, wide temperature ranges, and exposure to vibration and shock. High TG PCBs are commonly used in avionics systems, satellite communications equipment, and military electronics due to their excellent thermal stability, mechanical strength, and electrical performance.
Industrial Automation and Control
Industrial automation and control systems, such as programmable logic controllers (PLCs), motor drives, and power inverters, often operate in harsh industrial environments with elevated temperatures and exposure to dust, moisture, and vibration. High TG PCBs are ideal for these applications, as they can maintain their performance and reliability under challenging conditions, ensuring the smooth operation of industrial processes.
High-Power LED Lighting
High-power LED lighting systems generate significant amounts of heat, which can impact the performance and lifespan of the electronic components. High TG PCBs are used in LED lighting applications to provide a stable and reliable platform for mounting and interconnecting LEDs, drivers, and control circuitry. The enhanced thermal stability of High TG PCBs helps to dissipate heat effectively and prevent thermal damage to the components.
Medical Devices
Medical devices, such as imaging equipment, patient monitors, and surgical instruments, require PCBs that can operate reliably and maintain their performance over extended periods. High TG PCBs are used in medical applications to ensure the devices’ longevity and accuracy, even when exposed to sterilization processes and harsh disinfectants.
Telecommunications Equipment
Telecommunications equipment, including routers, switches, and base stations, requires PCBs that can handle high-speed data transmission and maintain signal integrity in high-temperature environments. High TG PCBs are used in these applications to provide a stable and reliable platform for high-frequency circuits and to ensure optimal performance in demanding operating conditions.
Frequently Asked Questions (FAQ)
-
What is the difference between High TG PCBs and standard PCBs?
High TG PCBs are made using substrate materials with higher glass transition temperatures, such as polyimide or high-performance epoxy resins, which offer enhanced thermal stability and performance compared to standard FR-4 PCBs. This allows High TG PCBs to maintain their mechanical and electrical properties at elevated temperatures, making them suitable for demanding applications. -
What are the typical glass transition temperatures for High TG PCB materials?
The glass transition temperatures for High TG PCB materials can vary depending on the specific material used. High TG FR-4 materials typically have a TG range of 170°C to 180°C, while polyimide materials can have a TG range of 250°C to 260°C. -
Can High TG PCBs be used for multilayer designs?
Yes, High TG PCBs can be manufactured in multilayer configurations, just like standard PCBs. The high-temperature lamination process used in the production of High TG PCBs ensures proper bonding and dimensional stability between the layers. -
Are High TG PCBs more expensive than standard PCBs?
Yes, High TG PCBs are generally more expensive than standard PCBs due to the specialized materials and manufacturing processes involved. However, the added cost is often justified by the enhanced performance, reliability, and longevity that High TG PCBs offer in demanding applications. -
How do I select the right High TG PCB material for my application?
When selecting a High TG PCB material for your application, consider factors such as the expected operating temperature range, electrical requirements, mechanical stress, and environmental conditions. Consult with your PCB manufacturer or material supplier to determine the most suitable High TG material that meets your specific needs.
Conclusion
High TG PCBs, or PCB-TG, are a specialized type of printed circuit board designed to offer superior performance and reliability in high-temperature environments. By utilizing substrate materials with higher glass transition temperatures, such as polyimide or high-performance epoxy resins, High TG PCBs can maintain their mechanical and electrical properties at elevated temperatures, making them ideal for demanding applications in various industries.
The enhanced thermal stability, electrical performance, and mechanical strength of High TG PCBs make them essential components in automotive electronics, aerospace and defense systems, industrial automation and control, high-power LED lighting, medical devices, and telecommunications equipment. By understanding the unique properties and benefits of High TG PCBs, engineers and designers can make informed decisions when selecting the most suitable PCB materials for their projects, ensuring optimal performance and reliability in challenging operating conditions.
As technology continues to advance and the demand for high-performance electronics grows, the importance of High TG PCBs will only continue to increase. By staying informed about the latest developments in PCB materials and manufacturing processes, engineers and designers can stay ahead of the curve and create innovative solutions that push the boundaries of what is possible in the world of electronics.
Leave a Reply