What is a PCB?
Definition and Purpose
A Printed Circuit Board (PCB) is a flat board made of insulating material, such as fiberglass or composite epoxy, with conductive copper traces printed onto its surface. PCBs serve as the foundation for electronic circuits, providing mechanical support and electrical connections for various components like resistors, capacitors, and integrated circuits (ICs).
Advantages of Using PCBs
PCBs offer several advantages over traditional point-to-point wiring:
- Compact size: PCBs allow for the miniaturization of electronic devices by placing components close together.
- Reliability: The rigid structure and precise layout of PCBs ensure consistent performance and reduce the risk of loose connections.
- Mass production: PCBs can be easily manufactured in large quantities, reducing costs and production time.
- Standardization: PCBs follow industry standards, making it easier to design and troubleshoot circuits.
PCB Components and Materials
Substrate
The substrate is the base material of the PCB, providing a stable and insulating foundation for the copper traces and components. Common substrate materials include:
- FR-4: A fiberglass-reinforced epoxy laminate, widely used for its excellent mechanical and electrical properties.
- Polyimide: A flexible and heat-resistant material used in flexible PCBs (FPCBs) for applications requiring bendability.
- Ceramic: Used in high-frequency and high-temperature applications due to its low dielectric loss and thermal stability.
Copper Traces
Copper traces are thin, conductive paths printed onto the PCB substrate, connecting the various components. The thickness and width of the traces depend on the current-carrying requirements and signal integrity considerations.
Solder Mask
A solder mask is a protective coating applied to the PCB surface, covering the copper traces while exposing the component pads and other areas that require soldering. Solder masks prevent short circuits and improve the PCB’s appearance.
Silkscreen
The silkscreen is a layer of text and symbols printed onto the PCB surface, providing information such as component designators, logos, and assembly instructions. Silkscreen is typically white but can be any color contrasting with the solder mask.
Types of PCBs
PCBs can be categorized based on the number of conductive layers and their flexibility:
Single-Layer PCBs
Single-layer PCBs have conductive traces on only one side of the substrate. They are the simplest and most cost-effective option for low-complexity circuits.
Double-Layer PCBs
Double-layer PCBs have conductive traces on both sides of the substrate, connected through plated holes called vias. They offer more routing options and higher component density than single-layer PCBs.
Multi-Layer PCBs
Multi-layer PCBs consist of three or more conductive layers sandwiched between insulating layers. They are used for complex circuits that require high component density and extensive interconnections.
PCB Type | Layers | Complexity | Cost |
---|---|---|---|
Single-Layer | 1 | Low | Low |
Double-Layer | 2 | Medium | Medium |
Multi-Layer | 3+ | High | High |
Rigid PCBs
Rigid PCBs are the most common type, made with a solid substrate that maintains its shape. They are suitable for most electronic applications.
Flexible PCBs (FPCBs)
FPCBs use flexible substrate materials, allowing them to bend and conform to various shapes. They are often used in wearable electronics, medical devices, and applications requiring movable parts.
Rigid-Flex PCBs
Rigid-flex PCBs combine rigid and flexible sections, offering the benefits of both types. They are ideal for applications that require both stability and flexibility, such as folding smartphones or aerospace electronics.
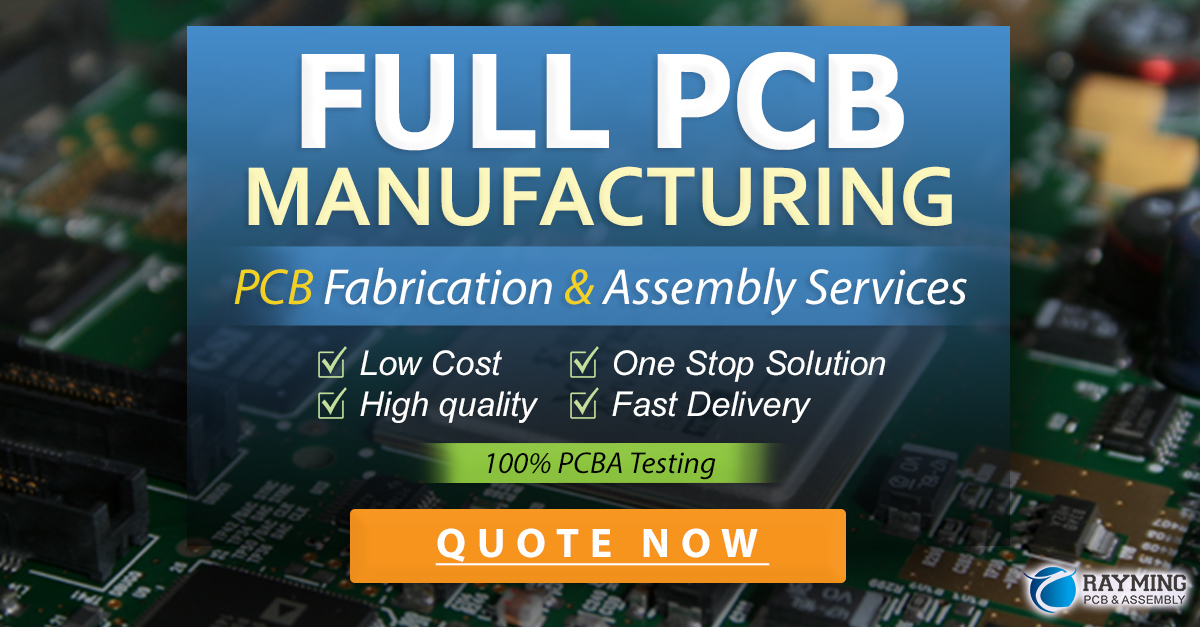
PCB Design and Layout
Schematic Capture
The first step in PCB design is creating a schematic diagram that represents the circuit’s electrical connections and components. Schematic capture software, such as KiCad or Eagle, is used to create the schematic.
PCB Layout
Once the schematic is complete, the next step is to create the PCB layout. PCB layout software is used to arrange the components and route the copper traces according to the schematic. Key considerations during PCB layout include:
- Component placement: Components should be placed logically and efficiently to minimize trace lengths and optimize signal integrity.
- Trace routing: Traces should be routed with appropriate width and spacing to minimize crosstalk and electromagnetic interference (EMI).
- Power and ground planes: Dedicated power and ground planes help distribute power evenly and reduce noise.
- Design rule checks (DRC): DRC ensures that the PCB layout adheres to manufacturing constraints and industry standards.
PCB Manufacturing Process
The PCB manufacturing process involves several steps:
- PCB design: The PCB layout is finalized using CAD software.
- Gerber file generation: The PCB design is exported as Gerber files, which contain the necessary information for manufacturing.
- Fabrication: The PCB substrate is laminated, and the copper traces are etched based on the Gerber files.
- Drilling: Holes are drilled for through-hole components and vias.
- Plating: The holes are plated with copper to establish electrical connections between layers.
- Solder mask application: The solder mask is applied to protect the copper traces and prevent short circuits.
- Silkscreen printing: The silkscreen layer is printed onto the PCB surface.
- Surface finish: A surface finish, such as HASL or ENIG, is applied to the exposed copper pads to prevent oxidation and enhance solderability.
- Electrical testing: The PCB undergoes electrical testing to ensure proper functionality and connectivity.
Frequently Asked Questions (FAQ)
- What is the difference between a breadboard and a PCB?
-
A breadboard is a prototyping tool used for temporarily building and testing circuits, while a PCB is a permanent, manufactured board that provides a reliable and compact solution for electronic circuits.
-
Can I make my own PCB at home?
-
Yes, it is possible to make simple PCBs at home using methods like toner transfer or chemical etching. However, for complex designs and professional-quality PCBs, it is recommended to use a professional PCB manufacturing service.
-
What software can I use to design PCBs?
-
There are several PCB design software options available, both free and paid. Some popular choices include KiCad, Eagle, Altium Designer, and Autodesk Fusion 360.
-
How do I choose the right PCB thickness for my project?
-
The choice of PCB thickness depends on factors such as the number of layers, component size, and mechanical requirements. Common PCB thicknesses range from 0.8mm to 1.6mm, with 1.6mm being the most widely used for standard applications.
-
What is the lead time for PCB manufacturing?
- The lead time for PCB manufacturing varies depending on the complexity of the design, the manufacturer’s workload, and shipping options. Typical lead times range from a few days to several weeks. Some PCB manufacturers offer expedited services for faster turnaround times.
Conclusion
In this comprehensive guide, we’ve covered the fundamentals of PCB boards, from their basic components and materials to the manufacturing process. Understanding PCBs is crucial for anyone involved in electronics, whether you’re a hobbyist working on DIY projects or an engineer designing complex systems.
As you dive deeper into the world of PCBs, keep in mind the importance of proper design, layout, and manufacturing considerations. With the right knowledge and tools, you’ll be well on your way to creating reliable and efficient electronic devices.
Happy PCB designing!
Leave a Reply